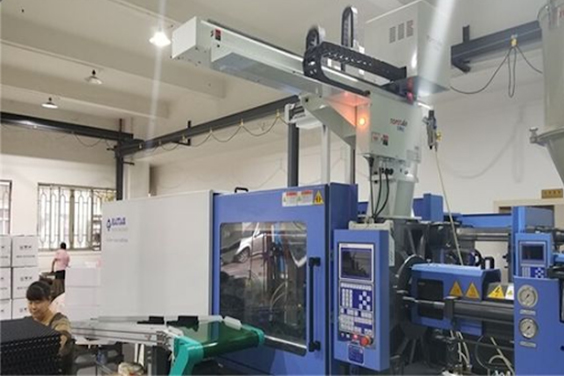
Share :
Share :
Straightforward as it may seem, injection molding has specific steps that have to be followed in order for the process to be a success. One area that manufacturers and mold engineers have to consider deeply is the mold drawing, which is basically the creation of the mould design blueprint.
We are going to look at the things that one has to consider when mold drawing and designing or injection molding process and how each of these considerations affects the final end product. If you have been curious to know more about how things are designed from scratch, then this is where you should be.
There are countless materials that are used for plastic injections, and the ones you will use have to guide the designing of the injection mold. The decision on raw materials is usually the first thing that manufacturers arrive at in the early stages of setting up an injection molding process. This also depends on the type of product that is intended to be made and the availability of the raw material.
Therefore, the size, shape, and other important attributes of the injection mold have to be determined by the type of material that will eventually be used. The chemical and physical resistances are important as they will affect the durability of the injection mold.
The injection molding process undergoes some extreme conditions like high temperatures and pressures which are necessary for the molding of the product to take place. For this to happen successfully, the mold has to possess the ability to withstand all these conditions and even worse for as long as it is being used, or there is a risk that it may contaminate the process or cause defects in the final product. The last thing any mold engineer would want is to have a piece of the mold melting off and becoming part of the molten material.
This is directly tied to the raw materials and any other additional chemicals and instances that will have to be added to make them ideal for the process. By the time you reach a point where you need to design the injection mold, it is assumed that you have already assembled the machinery, and you are now adding the finishing touches. Consider the cost of materials that you will use to make the mold first to avoid having to break your bank in the process. Steel is the recommended material, but you can also use Aluminum and other hardy metals.
The gate forms the entry point of a molten plastic material after being injected by the nozzle. Gates are what control the flow, and once the right amount of material has filled the mold, the gate is closed. When designing the injection mold, consider the location of the gate as it can be placed in varying positions around the whole structure. The location of the molding gate will affect the tolerances, the warpage, the surface finish, the wall thickness, and a host of other factors in the end product. Therefore, think very hard and long about the gate’s location before deciding on the way forward as far as the design of the injection mold is concerned.
The mold should be able to withstand pressure and this will not be possible if the walls are thin. Thicker walls also provide a better cooling area as the temperature dissipates in a uniform manner in a very gradual way rather than the abrupt cooling that could lead to some serious structural issues for the end product. The cooling has to be slow to allow each part of the molten form of the product to solidify evenly and in a more complete way. At the same time, thin walls also have their place in injection molding. There are some certain types of materials that have to be cooled faster, and these are the instances where a thin wall would come in very handy.
Mold flow analysis is the process where certain molding software is used to predict how the final product will look in the end. They are used to make the process less costly and to reduce wastage as the manufacturers are able to know exactly how much they need for each process. Having this in your mold design considerations will help you configure the best mold care that will be able to take advantage of MFA to attain the best possible result at the end of the assembly line.
Injection molds require intricate designs, blueprints and a lot of care when it comes to designing. This is not a process that is completed in a single day. Considering how important they are to the entire process, taking into account the time you need to make the mold is very important. The bottom line is that the process should not be rushed to ensure that the final mold is within the needed parameters as it will be used for multiple batches of manufacturing.
Sometimes you will need additional accessories to make the process complete,, and this has to be reflected in the design just in case. For instance, the ejection process may require lifters, sliders or inserts that will make it safe without inflicting any damage to the final product. All these accessories and additional tools must have their slots designed into the mold well in advance to make it easy for them to be added later on and removed at will, depending on the needs of that particular task.
Are you looking to manufacture small parts like auto molds? Are you looking for plastic injection molding service? Are you going for mass production type of setup, or are you dealing with the manufacture of complex designs that require time? These are some of the questions that you must ask yourself beforehand in order to design a mold that will be able to handle the demand of the task without having to strain too much. This is also tied directly to the old classification, which gives you a clear image of the type of manufacturing you need.
Customization is one of the pillars of injection molding; it is what makes injection molding a very attractive prospect for most manufacturers. The thing that makes customizations easy is the ability to design a mold that will be used for a specific batch of products. Consider the complexity of the dimensions of the product you plan to create as well as the specifications of the client in order to come up with a mold that will be able to produce the exact product that will satisfy the needs of the client.
As it is clearly evident, getting the mold design part right will go a long way in determining the success of the entire production, and this is why manufacturers and mold engineers have to pay extra attention to the design part. For more information on mold making technology and what it entails, check out our website, and all your questions and concerns will be addressed by a team of experts.
Please contact us using the form below or emailing (harry@fowmould.com)