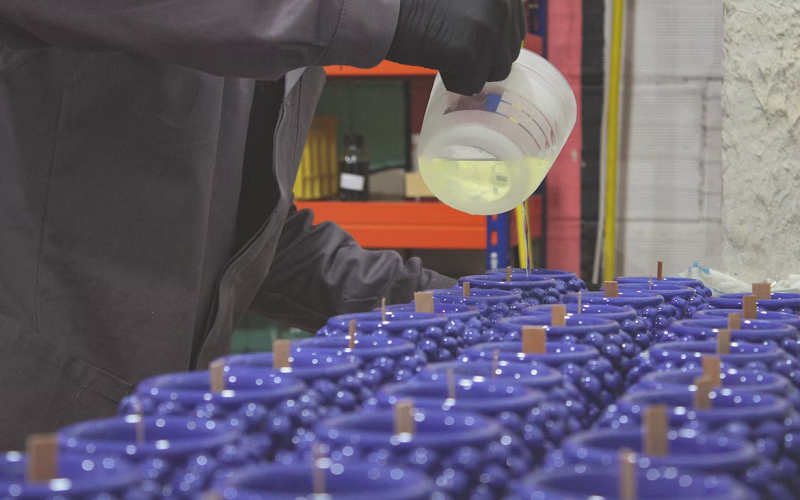
Share :
Share :
Like many other polymers, thermoplastic polyurethane of TPU is a widely used material in injection molding. The polymer is resistant to abrasion and other deterrents and is also famous for its elasticity. For whichever use it is made, the polymer tends to be strong as well as durable. Like any polymer, TPU has its own set of advantages and disadvantages. Thermoplastic polyurethane finds extensive use in the process of overmolding as the elasticity of the material along with its strength is ideal for objects like rubber grips. TPU is more energy-efficient and is also good at retaining colors which helps with its versatility.
Thermoplastic Polyurethane is commonly known as TPU and is a polymer with versatile uses and durable properties. Additives are often added to this polymer to make it less flexible. Everyone from designers to engineers, along with manufacturers, works extensively with this polymer.
During the time of manufacture, thermoplastic polyurethane is made so that it comes up to the industry standards. The surface quality and the elasticity can be managed during manufacture. TPU is also used extensively for advanced prototype molding, which helps with the making of any parts that may require elasticity and flexibility. The flexibility of this polymer allows for better shock absorption and also has greater rebound qualities, 63% rebound resistance, to be specific.
While both the advantages and disadvantages of TPU are mentioned below, the pros of this polymer outweigh the cons it may present. Even though the benefits of thermoplastic polyurethane do not negate the disadvantages, the disadvantages are few and can be tackled to reap the benefits of this polymer.
1.The gate as large as possible, and the mold wall at right angles but not more than the wall thickness of the product, the sprue as short as possible
2.TPU material in the flow direction of the shrinkage rate is usually 1% ~ 3%. Common products mold design reference shrinkage rate of 0.5% ~ 0.6%.
3.TPU moldsurface roughness 25 ~ 35 mm, polishing the mold surface may lead to mold release difficulties
4.Runner cross-section should be rounded.
5.Exhaust slot: 0.015 ~ 0.03 mm.
6.Demolding angle :5°.
7.Use balanced runner system
TPU finds use as automotive instruments as well as floatation devices. The material is also used in castor wheels, belts, gaskets, handbags, medical devices, glass frames, footwear, sporting goods, and also as computer components. It is thermoplastic polyurethane that is found in clear cases of mobile phones. Many keyboard protectors also use this polymer in manufacture. There are multiple common uses of TPU that also include adhesives, textile coating applications, hose and tube, and wire, as well as cable jacketing. Many lamination films also use thermoplastic polyurethane.
3D printing is a very popular usage of this material. TPU is ideal for use in 3D printing because no warping or primer is needed for printing objects that need elasticity and shock absorbance as a property. TPU powders and filaments are both used in the process. TPU pellets are also used in injection molding, which eliminates the necessity of the material being available in filament form.
The physical properties of thermoplastic polyurethane are such that the block of the material has both hard and soft parts. The harder part of the linear segmented block copolymer is usually aromatic and aliphatic. The softer and more flexible portion is a polyether or polyester. The structure of this substance adds to its literal flexibility as well as the flexibility of its applications.
The chemical structure of TPU is such that the substance has a high compression set, is highly resistant to impacts, adverse weather conditions, hydrocarbons, tears, and abrasions. The material is so naturally flexible that it does not need plasticizers to be added during injection molding and mold design. The chemical nature of TPU allows it to be used both as a soft thermoplastic in engineering and as a hard substance likened to rubber in its use.
One of the advantages of this polymer is that it does not require any compounding. TPU is used as an additive to add strength to various materials. Many composites of TPU have better flexural modulus (approximately 150,000 psi) at the end of the additive process. The initial tensile strength of TPU is nearly 5076 psi.
TPU is also manufactured with different base materials leading to the formation of different grades of TPU. These are:
In order to obtain high quality TPU parts, the following relevant conditions need to be followed during the TPU plastic injection molding process:
Injection temperature is one of the key factors affecting the quality of TPU products, the melting point of TPU material is low, the injection temperature is too high will lead to material deterioration, too low will lead to product surface defects and dimensional deviations.
Therefore , TPU injection molding temperature control between 200 ° C ~ 240 ° C is more appropriate.
Mold temperature also has a great influence on the surface quality and dimensional accuracy of TPU products.
A mold temperature that’s too high will lead to excessive melting of the product surface, while too low can lead to surface defects and dimensional discrepancies.
Generally, an appropriate mold temperature for injection molding tpu is between 30°C and 60°C.
Injection pressure is one of the key factors to control the flow of TPU material. Too high injection pressure will lead to poor material flow, bubbles and short shot and other defects, too low will lead to product surface defects and dimensional deviations.
As a result,an appropriate injection pressure for TPU is between 50Mpa and 100Mpa.
Injection speed
Injection speed is one of the key factors to control the flow rate of TPU material.
Too fast injection speed will lead to uneven material flow, short shot and bubbles and other defects, too slow will lead to product surface defects and dimensional deviations.
Thus , TPU injection molding speed control between 5cm / s ~ 20cm / s is more appropriate.
Cooling time is one of the key factors to control the size and surface quality of TPU products.
Cooling time is too short will lead to products not fully cured, visible melt marks and deformation and other defects: too long will lead to process cycle extension and reduced productivity.
Accordingly, the cooling time of TPU products is controlled between 10s~60s.
For specific values, please refer to the following table of TPU processing temperatures in injection molding.
Linear Mold Shrinkage | 0.00040 – 0.0030 cm/cm |
Nozzle Temperature | 221 – 243 °C |
Melt Temperature | 185 – 243 °C |
Mold Temperature | 15.6 – 60.0 °C |
Drying Temperature | 82.2 – 110 °C |
Dew Point | -40.0 – -17.8 °C |
Thermoplastic polyurethane comes under the category of thermoplastic elastomers and has a plethora of applications. The polymer is characterized by its elasticity along with its strength. The specific vary depending upon the grade of the polymer. TPU does not lose any of its properties when it is melted, and the filaments are then used for the 3D printing process. Medical molding is also an application for this polymer. The impact resistance and the durability of this material is the reason why TPU is used in insert molding. Its versatility in injection molding procedures makes it a well sought-after material across many industries.
Please contact us using the form below or emailing (harry@fowmould.com)