As one of the lightest thermoplastic materials, Polymethylpentene stands out in numerous high-demand application areas with its exceptional transparency, lightness, and high thermal stability.
Simultaneously, PMP injection molding technology, like a shining new star, demonstrates the limitless possibilities of engineering plastics at the intersection of modern material science and manufacturing technology.
This guide will provide a detailed introduction to the properties of PMP material, delve into the influencing factors in PMP injection molding, and reveal its enormous potential in modern manufacturing.
What Is PMP?
PMP (Polymethylpentene) is a highly crystalline transparent polyolefin, synthesized through the polymerization of 4-methyl-1-pentene (4MP1) monomers obtained from the dimerization of propylene.
With a density of 833 kg/m³, it is the lightest among all plastics.
Polymethylpentene was first synthesized by the Italian scientist Natta using the Ziegler-Natta catalyst he invented. In 1965, semi-industrial production was accomplished by ICI, a British company. Currently, Mitsui Chemicals of Japan is the largest producer and supplier of PMP.
The high transparency of Poly(4-methylpentene) is primarily due to the low optical anisotropy of the molecules in the helical configuration of the crystalline phase, as well as the close match in density and refractive index between the crystalline and amorphous portions.
The close resemblance in refractive index between the crystalline and amorphous parts results in high isotropy of the material.
Therefore, TPX (a common name for Poly(4-methylpentene)) becomes the only crystalline polymer among commercially available high-transparency resins.
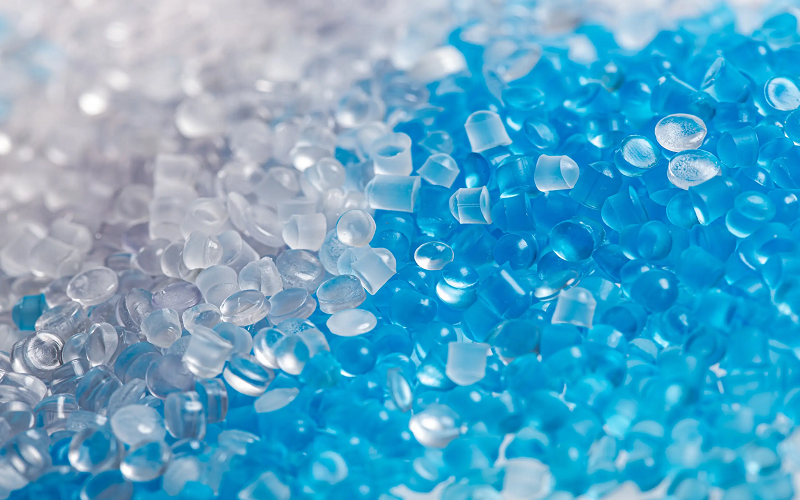
Main Properties of PMP materials
Poly(4-methylpentene-1) is a highly crystalline, here are its main properties:
Density | 0.82-0.83 |
Water Absorption | 0.01% |
Melting Point | 240℃ |
Vicat Softening Point | 160℃-170℃ |
Shrinkage | 1.5%-3.0% |
Light Transmittance | 90%-92% |
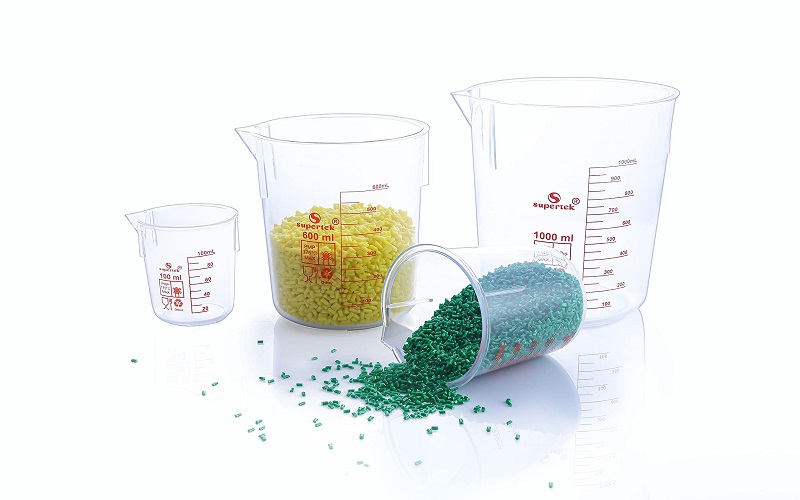
What Are The Advantages Of PMP Plastic?
In addition to the characteristics common to general polyolefin materials, PMP (Polymethylpentene) also exhibits outstanding optical properties, mechanical properties, high-temperature resistance, and electrical properties.
Strong Thermal Stability
PMP plastic has a high melting point of 240°C and a Vicat softening point of 173°C, allowing it to be used at temperatures higher than those suitable for PP (Polypropylene).
Despite its high melting point, PMP has low melt viscosity, good flowability, and excellent thermal stability.
This makes its processing favorable, as it can be molded using general equipment for thermoplastic plastics.
High Degree of Transparency
Although PMP is a crystalline material, its transparency is better than that of Polystyrene (PS) and Polymethyl Methacrylate (PMMA), with a light transmittance rate of 94% for visible light.
Particularly, its UV transmittance is superior to glass and other transparent resins.
Low Electrical Conductivity
Due to its non-polar structure, PMP has a dielectric constant of around 3.12, one of the lowest among synthetic resins, comparable to Polytetrafluoroethylene (PTFE) and Low-Density Polyethylene (LDPE).
Chemical Resistance
Thanks to its stable C-C bonds, PMP demonstrates superior chemical resistance compared to polycarbonate and acrylic resins.
It is particularly resistant to acids, alkalis, alcohols, and can withstand various organic solvents.
PMP remains stable even under high-temperature, high-pressure steam conditions without decomposing.
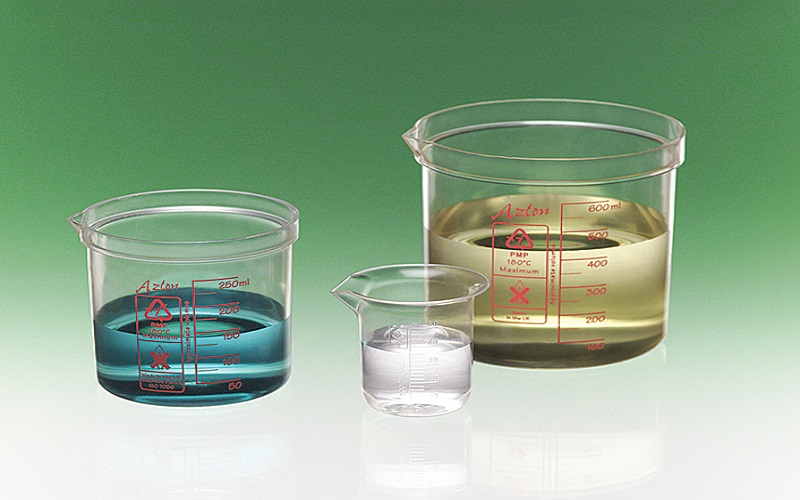
Conditions for PMP Injection Molding Process
To create high-quality injection molded PMP products, mastering the key parameters of PMP injection molding is crucial.
Here are some of the critical parameters:
Melt Temperature
Given that the melting point of PMP is around 240°C, the typical melt temperature range is usually set between 280°C to 310°C.
Mold Temperature
It is recommended to set the mold temperature between 40°C to 60°C.
Lower mold temperatures can help shorten cycle times but may require higher injection pressures.
Injection Pressure
Due to the low melt viscosity of PMP, the injection pressure can be relatively low, typically in the range of 40 to 80 MPa (400 to 800 bar).
Holding Pressure
This is usually set at 50% to 60% of the injection pressure to avoid shrinkage or depressions in the final product.
Back Pressure
Moderate back pressure, generally between 5 to 20 MPa, can improve the quality of the melt, especially when mixing colors.
Cooling Time
The cooling time depends on the thickness of the product and the temperature of the mold.
For standard PMP products, the cooling time might range from 20 seconds to 60 seconds.
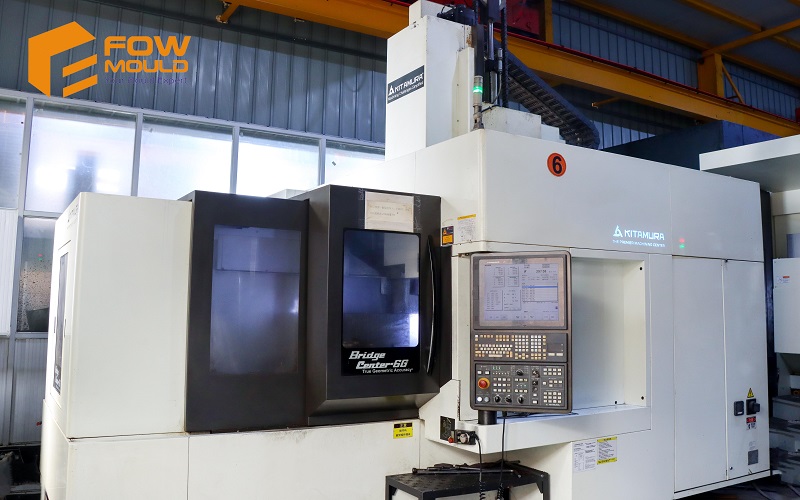
How To Design A PMP Injection Mold?
Designing an injection mold for Polymethylpentene (PMP) involves several critical considerations to ensure high-quality production and efficiency.
Considering the good flowability of PMP, the mold design should support thin-wall construction while maintaining consistent wall thickness to prevent sinking and uneven cooling.
Additionally, to facilitate demolding, the draft angle for PMP parts is typically between 1° to 2°.
For parts with deep cavities or complex geometries, a larger angle, such as 3° to 5°, might be necessary to ensure smooth demolding.
For PMP injection moulding, a cold runner system is generally recommended. The runner diameter usually ranges between 4mm to 8mm.
Cold runners simplify the mold design, reduce manufacturing costs, and minimize material waste.
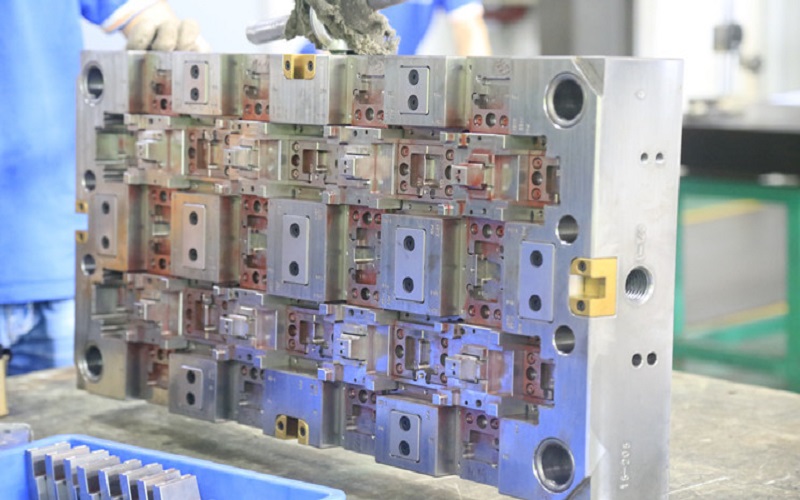
Used Of Injection Molded PMP Parts
In the context of growing demands in ECMO clinical applications and the accelerated construction of 5G base stations, the market for PMP (Polymethylpentene) is expanding significantly.
Here are the main application areas for PMP injection molding products:
Medical Devices
With its high-temperature resistance, non-toxic nature, and good transparency, medical equipment has become one of the primary application areas for PMP injection molding products.
PMP plastic products can be sterilized and reused multiple times.
They are used in medical applications such as syringes, UV blood analysis pools, blood separation troughs, three-way valves, and animal experiment cages.
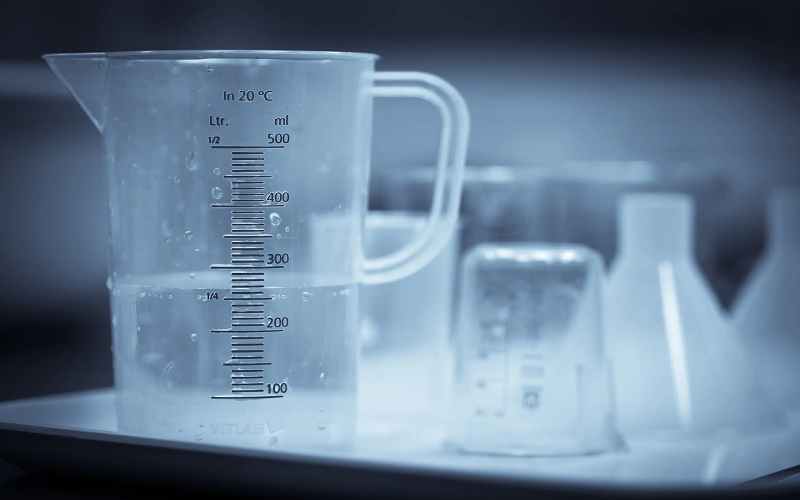
Electronics and Electrical Appliances
Due to its high transparency and heat resistance, PMP can be used in heat-resistant lenses, car lights, cabin lighting equipment, high-frequency electronic components, and printed circuit base plates.
Additionally, PMP is used in various auxiliary devices such as vehicle brakes, clutches, air conditioning units, heaters, and more.
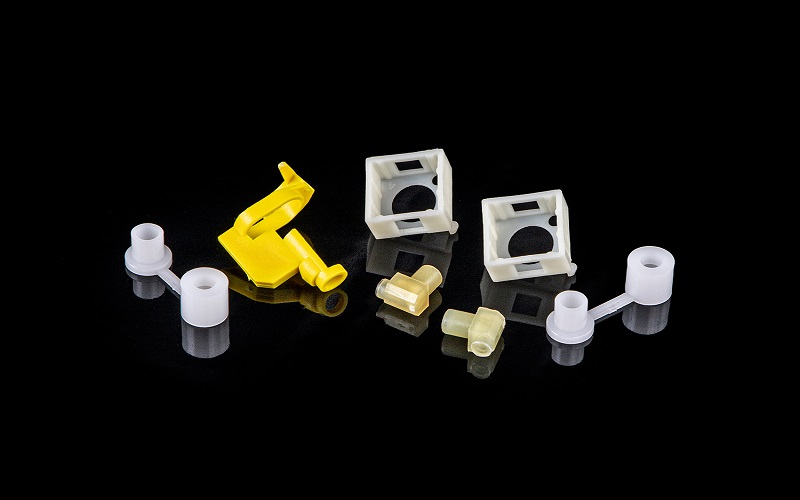
5G Sector
PMP possesses excellent electrical insulation, low dielectric constant, and dielectric loss, offering low dielectric properties comparable to fluoropolymers, making it suitable for use in RF insulators at 5G communication base stations.
Compared to PTFE insulators, PMP has similar electrical properties but at a lower material cost and with a lower density (PTFE density is 2.1-2.3), resulting in lower cost per unit volume.
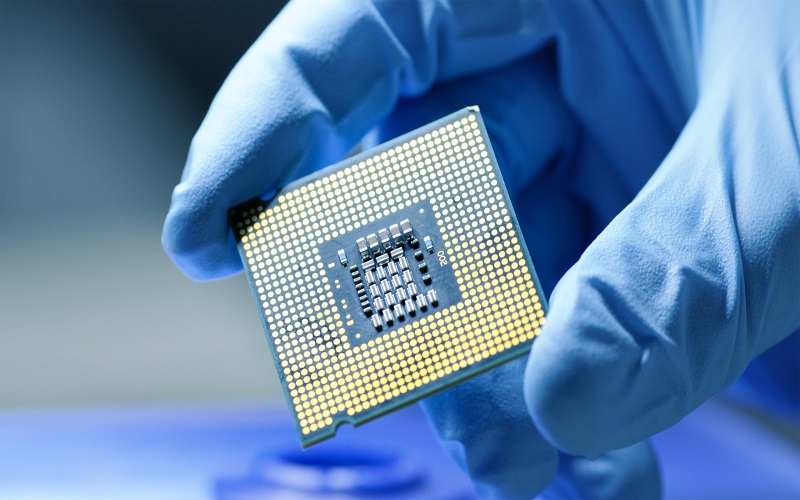
Conclusion
In summary, PMP injection molding is a key player in a wide range of industries due to its unique properties.
From medical devices to emerging 5G technologies, these properties make PMP indispensable in specialized fields.
Its potential for innovation and adaptability makes it a key material for the evolving manufacturing industry.
To learn more about injection molding, choose FOWMOULD as your trusted injection molding partner.