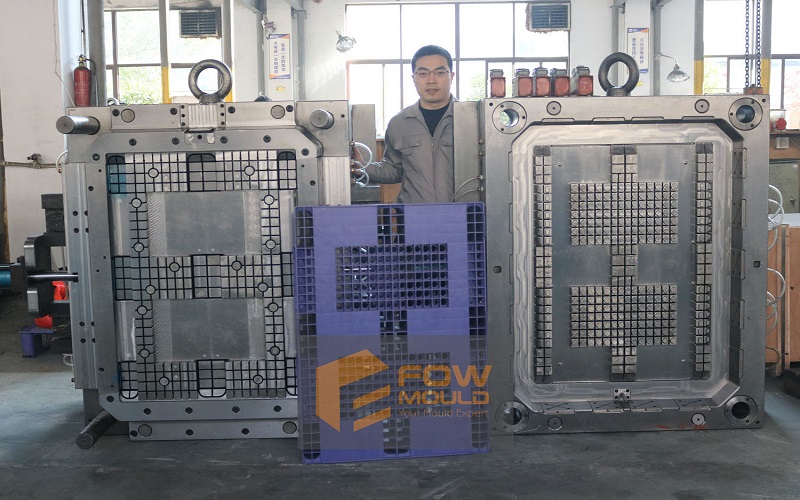
Share :
Share :
Cooling consumes the great majority of clock ticks in every minute of cycle time. As a result, it is a key component in determining a part’s profitability. Mold and component designers are aware of the ramifications, depending on a combination of skill, experience, intuition, prototyping, and CAE analysis to create reliable coolant designs.
This technique allows practical engineers to maximize productivity. In other words, if you build a cooling solution that operates well and reliably for your application, you will be able to spend more time producing high-quality molds as rapidly as feasible.
This article aims to provide a detailed understanding of the injection molding cooling system, as well as its design procedure and molding making technology. All this while getting into the even smaller details known by specialists in the industry. Do read on to find out more.
Source: Pinterest
The purpose of plastic injection mold cooling is to offer heat management throughout the injection molding process. When the hot plastic melt enters the mold chamber, it cools and solidifies due to heat dissipation via the cooling system.
To remove waste heat from an injection molding system, cooling should ideally use either air or liquid. As a result, the system may produce injection mold items that are flawlessly shaped. For it to execute this purpose there are several components required in this injection molding cooling system.
Source: Pinterest
Additional alternatives for increasing injection molding cooling efficiency in difficult-to-reach regions are available in addition to cooling channels internal to the plastic injection mold. Three possibilities for adding to the mold to increase cooling and prevent shrinkage during the cooling step are listed below:
A baffle is a cooling channel that is drilled perpendicular to the main cooling line. It is equipped with a blade that divides the cooling flow into two semi-circular paths. The coolant enters the blade from one side, rotates through the semicircular pathways, later returning to the main cooling line.
The benefit of this alternative is that it expands the surface area that the coolant can cool, and it can also be a cost-effective solution for mold temperature regulation in challenging places.
A Bubbler, which is similar to a Baffle in its capacity to add cooling in challenging regions, is another alternative. The Baffle has a short tube in which the coolant enters at the bottom and bubbles out the top like a fountain. The coolant then flows down the outside of the Bubbler and back to the main coolant line.
This technique is most suited for narrow molding cores that, due to their limited thickness, cannot accommodate a substantial coolant channel.
Thermal pins can be used instead of baffles and bubblers. The pin is a sealed cylinder filled with vaporized fluid that draws heat from the mold. The vapor will condense as it transfers heat to the main coolant, and the process will begin again with the next molding cycle. The thermal pin’s heat transfer efficiency is roughly ten times that of a copper tube, making it an excellent option for increased cooling capacity.
Source: Pinterest
Changes in mold temperature have the greatest impact on cycle time. This is why mold designers place such a high value on temperature uniformity. Pressure within coolant lines, similar to temperature, should be kept as uniform as feasible. Mold designers must ideally aim for a pressure drop of no more than 5 psi across the mold.
Coolant should flow with appropriate disturbance and blockages will also be easier to recognize with uniform pressure throughout all branches of the injection molding cooling system. Efficient cooling systems aid in overcoming these realities, allowing mold designers to manage temperature, pressure, and time tradeoffs to achieve the ultimate goal: shorter cycle time.
A poorly designed injection mold cooling system increases molding time and production costs.
The first step toward achieving uniform temperatures and pressures is to understand the fundamentals. The top three injection molding cycle cooling methods are as follows.
Source: Pinterest
A water cooling system for injection molding, also known as a thermolator, works by circulating chilled water along water lines that run around the outside of a mold’s cavity and runner gates. These water lines will be located closest to outside the manufactured product’s surface to provide even cooling and to eliminate warping of the product’s surfaces. The water in cooling lines is chemically treated to avoid mold and bacterial growth as well as waterline pollution.
Source: Pinterest
An evaporator is used in an air conditioning system to remove heat from the injection system. The heat from the evaporator is subsequently removed using an air-cooled condenser. An air cooling system will consist of an air intake fan that will send cooler air toward the mold and an exhaust fan that will direct hot air away from the mold.
Air injection mold cooling systems transfer heat from an injection molding machine’s running water lines to the ambient air around those lines within a cooler. Because air does not transmit heat as well as water, air-cooled by fans typically requires 10% more electricity.
Source: Pinterest
Ethylene glycol cooling often works with water in a liquid-based injection mold cooling design. Ethylene glycol prevents rust from forming on the internal surface of the mold, and at the same time, cooling and piping maintain a constant temperature within the mold.
When water from within enters the mold, it provides some type of cooling by absorbing heat from the mold. The ethylene glycol then prevents corrosion from accumulating in the mold cooling piping while also assisting you in maintaining a somewhat constant temperature in the mold.
When designing a cooling system for your injection molding, there are a few important issues to consider for cooling and reduced cycle time. Generally, all of the cooling channels in the mold should be close to one of the thickest areas of what you’re producing. Simultaneously, if your cooling channels are larger than the normal 10 millimeters, they must maintain the same diameter throughout the mold.
Source: Pinterest
Even if your mold design is ideally matched to the application, providing the optimal cooling time for part quality, surface smoothness, and total cost, things change when the injection molding machine starts up. Keep these considerations in mind to guarantee that your injection molding cooling design achieves its full potential.
Cooling lines corrode spontaneously over time as the material interacts with its environment and oxidizes. Mineral deposits, which form when cooling lines are exposed to trace minerals in the water supply, are also frequent. Corrosion or scaling in the cooling system can seriously impair thermal diffusivity and drastically diminish efficiency, resulting in longer-than-intended cycle times.
Mapping the surface temperature during setup is a best practice for guaranteeing consistency. Temperatures should be measured at various spots across the mold using a surface temperature gauge. This creates a baseline for subsequent tests, allowing you to discover irregularities immediately.
Efficient cooling isn’t typically the first thing that comes to mind for a mold designer. Even experienced engineers who have created reliable cooling systems can benefit from rethinking a few key design and manufacturing elements. Taking a fresh look at your present cooling system method may generate new ideas that result in faster cycle time—and improved profitability.
If the need arises, replace or improve the system for better results. If you want to learn more information and get professional plastic injection molding service, please check out our website.
Please contact us using the form below or emailing (harry@fowmould.com)