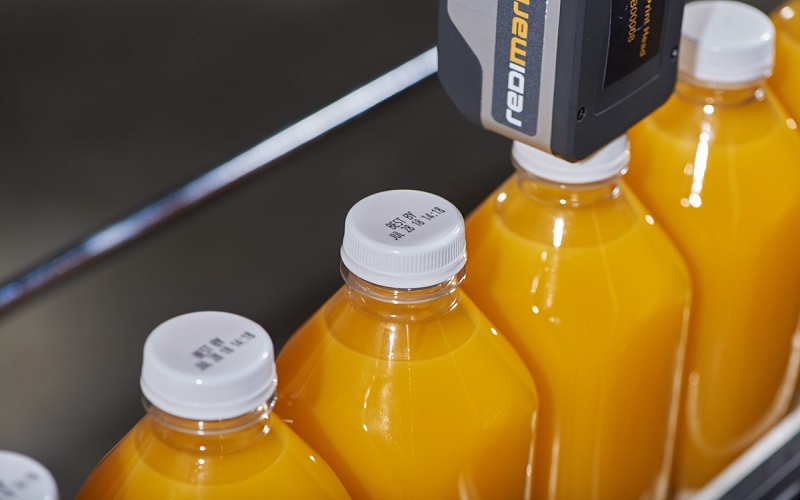
Injection molding companies use a lot of resources to come up with the final product. These resources are quite costly but the results are profitable so it’s always a win-win situation. A mold defines the shape of the final product making it a vital element in the whole process. Injection molding uses some types of plastics like acrylonitrile butadiene styrene (ABS), polyethylene (PE), polystyrene (PS), and polypropylene (PP).
Most plastics manufactured currently are through injection mold making technology since the process permits affordable mass production of products at a lowered period. The whole process is cyclic and whenever shapes need to be changed, the mold is replaced with another mold and the cycle continues.
Source: https://3dinsider.com
A mold is a type of cavity used in the injection molding process where the molten plastic is injected to form a variety of shapes depending on the mold design. They are usually hardened metal examples include; aluminum, beryllium-copper alloy, and steel just to mention a few. Steel molds are usually preferred because of steel properties like durability but are a bit costly compared to the rest.
There are different mold types like hot runner molds, two/three-plate molds, high/low cavitation, unscrewing molds, cold runner molds, family molds, and insulated runner molds. Currently, industries are trying to apply sustainable measures in their manufacturing as it is a global trend and this affects the process since they have to change some aspects to fit this idea. Injection molding companies have to find ways of reducing their carbon footprint.
Source: https://natrajind.files.wordpress.com
Injection molding is a manufacturing process of producing plastic goods. It uses an injection that directs molten plastics into a metal mold under high pressure. The final product’s shape and design depend on the mold’s design. After the plastic has cooled and solidified, the mold is pulled apart to eject the finished item. The process has been in existence for a while now since 1968 and. has diversified and incorporated new technology.
Often, the mold is usually overlooked, but it is the most crucial part of the whole process since it determines the final product’s look. Any defect on the mold results in a defect on the final product, meaning that time, raw materials, and cost has been wasted. Every manufacturer ensures that they have a qualified engineering and design team to facilitate the making of molds according to the right specifications.
Source: https://cdn-bnnjk.nitrocdn.com
An injection mold has different parts divided into two major components; the cavity (stationary) and the core (movable) sides. When the two are closed, space between is the part cavity where the molten plastic fills.
Source: https://encrypted-tbn0.gstatic.com
Consists of;
Source: https://www.researchgate.net
Consists of;
Source: https://3space.com
The mould design determines the product shape and design. Companies should consider hiring experienced designers and engineers to design and build molds. The condition of a mold determines the success of the whole molding process and whether the product will have defects or will be perfectly produced. Before buying or creating a mold, some considerations need to be taken into account.
The gate: they wear out fast and when designing a mold, this needs to be put in mind. The gates need to be made with inserts that are replaceable and durable. The most common materials used in making these inserts are D-2 steel, CPM-10V, and carbide. The gate diameter should be sufficient enough for allowing passage of molten plastic to fill the cavity. The location of the gates should also be considered.
Sprues: the sprue orifice must always be larger than that of the nozzle so that to prevent any leakages during the process.
Mold material: molds are made from steel either hardened or pre-hardened, beryllium-core alloy, and aluminum. Choosing mold materials depends on cost. Steel costs more to build but is long-lasting compared to the others. Over time, steel will be less costly because it needs less replaceability.
Shrinkage: when designing a mold, one should consider the shrinkage allowance of the materials to prevent any defects on the final products.
Wall thickness: the thickness and thinness of the mold wall determine its cooling rate. Designers should have an accurate calculation of the proper thickness of the wall to enable the plastic to cool at the correct rate uniformly.
Cooling system: the holes of the cooling system need to be made on both the cavity and core to minimize the cycle time.
Draft: should be included in the cavity and core to aid in the ejection of the molded parts.
Mold filing: the gate position should be designed to allow the filling of the cavity from thicker to thinner areas.
Polishing: should be done in the direction of material flow in the sprue, runners, cavity, and core.
Source: https://media-exp1.licdn.com
Injection molding engineering core includes ejection system design, gate design, runner design, cooling system design, and wall thickness.
Source: https://mechanicalengblog.com
It is the part responsible for releasing the finished parts from the mold. It is an important system since if it has malfunctioned, it can ruin the molded parts. The ejection system consists of ejector return pins, ejector plates, retainer plates, pins (ejector and stop), and so on. The pins are on the plates and movement on the plate makes the pin move forward ejecting the parts out of the core. The retaining plates ensure the pins are held on the plate. Designing of the system follows some standard rules;
Source: https://www.okmolding.com
The gate is the entry point of the liquid plastic into the cavity. The gate design and condition determine if the molding process will be successful or not since if the gate is clogged or inefficient the molten plastic entry will be delayed resulting in distortion of the whole process. There are four types of gates;
Source: https://lh3.googleusercontent.com
These are smaller passageways for resins from the sprue to the gate. The uniformity of the runner is very important. The thickness determines the pressure by which the plastic is injected. If the wall is thicker, the pressure increases and vise versa. If uniformity cannot be achieved, the change should be gradual and not exceed the previous by a large margin. In terms of shape, trapezoidal runners are preferred because they are easy to design and use.
Round runners are also common and required in some types of materials. Radii should be added in the direction of flow to all runner intersections. Intersections should also have cold slugs.
Source: https://lh3.googleusercontent.com
The cooling system is used to regulate the temperatures of the molten plastic in the cavity in the injection molding process. There are several considerations when designing the cooling system.
Source: http://bp2.blogger.com
Wall thickness affects many aspects of the molding process. The walls should be constant and ensure to avoid thicker or thinner sections. If a variety of thickness is required, ensure there is a gradual transition from thick to thin or vise versa. Uniformity prevents the warping of parts while cooling the molded parts.
Source: https://www.moldex3d.com
The process taken when designing a mold depends on the plastic part to be molded. The process begins with analyzing the plastic part, designing for manufacturing, CAD, mold flow analysis, design confirmation, and mold building.
Source: https://roboticsandautomationnews.com
Before building a mold, one needs to know the part being produced in detail. These are;
Source: https://lh3.googleusercontent.com
The mold design needs to be specified before manufacturing including size, shape, the material to be used, wall thickness, and so on. This is important since the production of molds is quite costly and any mistakes made result in losses financially, time-wise and labor. Proper care needs to be taken in this process to also avoid distortions in the parts to be molded. Considerations include;
Source: https://d12oja0ew7x0i8.cloudfront.net/
The best way to present your design is through computer-aided design ( CAD). A CAD drawing is a digital drawing showing your design in either 2D or 3D format. It provides a detailed way or like a sample of visualizing the mold to be built. This is vital since it provides a way of ensuring there are no defects or issues that may arise on the final mold after manufacturing. Also, alterations can be made to change the design if it is not impressive enough.
Preparing for a CAD drawing requires a couple of things like the best program to be used. There are several CAD programs but the most used are SolidWorks and AutoCAD. These programs have their file type and it is important to contact an expert if you intend to use any. File types are two formats; solid bodies and mesh bodies. For products requiring advanced prototype molding with resins (stereolithography) or prototyping (rapid), mesh files are best. For solid bodies, it is used in large and difficult projects.
CNC machines for mold making use solid bodies to produce quality and cost-effective products. The formats are discussed below.
Source: https://www.midstatemold.com
They are 3D images that demonstrate exactly what the physical product will look like. They are used for the evaluation of manufacturability, designing of injection molds, approximation of weight, designing of packaging materials. Examples of solid bodies format files include;
Source: https://cloudfront.jove.com
They are polygonal 3D images and represent the exterior surface of the model. The polygon shapes are liked to make a hollow interior surface. The files used in mesh bodies are;
Source: https://lh3.googleusercontent.com
It the process of simulating the injection molding cycle using a particular part design and plastic. It analyses if the design is manufacturable before building the actual mold. This process enables manufacturers to identify flaws in their design to prevent building a faulty mold and redoing it. Two elements help designers know if there are any flaws; the fill time and confidence to fill.
Fill time results: as the cavity is filling, the position of the flow front at specific intervals is shown by the fill time results. If it is well balanced, it means that the part has a good fill time and vise versa. It is analyzed via color-coding. Some filling defects are;
Confidence to fill: represents the likelihood of filling the cavity. It is shown by colors.
Source: www.injectionmould.org
Before the final stage of mold building, one needs to confirm the design of the molds from the clients and designers to ensure the correct mold is built. Building a mold is time-consuming and costly hence design needs to be double-checked to make sure everything is in order before commencing the manufacturing. Confirmation of design includes;
Source: www.injectionmould.org
It is the actual manufacturing of the mold. The mold is the foundation of the whole injection molding process hence building it requires high precision. The condition of the mold determines the quality of the products. The mold parts need to be precisely created to meet the product’s specifications and design. There are differenttypes of molds; insert molds, precision molds, multi-cavity molds, unscrewing molds, hot runner molds, thin-wall molds, over molds, family molds, MUD molds, and action molds.
The general classification of mold is two-plate and three-plate. Two-plate molds need only single daylight while tree-plate have two daylight. Mold construction depends on;
The injection molding process is an important manufacturing process since it leads to the production of products ranging from plastic molded chairs to auto plastic parts that are durable, accessible, high-quality, and cost-effective. In the Fow Mold industry, we deliver all your injection needs without hesitation and no project is too big for us. We have a team of experienced experts whose work is reputable across China and the world at large.
We specialize in mold designs, mold making, 3D printing, product design, CNC machining, over-molding, insert molding, and injection molding. Reach out to us for more information on Fow Mold.
Please contact us using the form below or emailing (harry@fowmould.com)