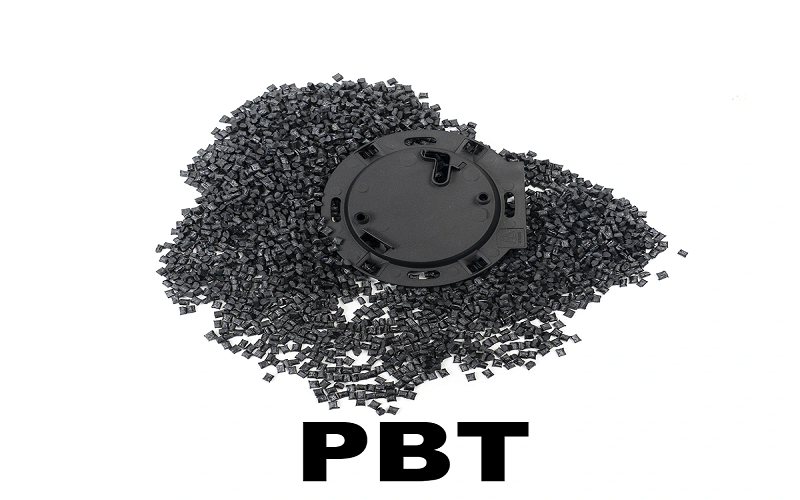
In the manufacturing industry, when it comes to creating different products, there features the use of a variety of processes. These processes help ensure that all the products manufactured are of high quality and offer great performance. One of the most used processes in manufacturing is injection molding.
It is preferred by different manufacturing companies given that it makes large-scale manufacturing easier. For this, working with a quality injection mold manufacturer will be the best option. Additionally, it features the use of different raw materials to achieve different types of products. If you’re getting into injection molding as a beginner, there are a few things you need to keep in mind. These things will help you ensure that you work to provide the best products with this manufacturing process.
Source: www.3erp.com
Injection molding is a manufacturing process that features the use of molten material injected into a mold to produce different parts. This process will feature the use of different molten materials including metal, plastics, and glasses among others. During this process, the materials to be used are fed into a heated barrel to get them into the molten state. Once that is done, they are then injected into the mold cavity and allowed to cool down. After the materials cool down, they harden and take the shape of the mold cavity being used.
With this in mind, the use of mold makers is essential. They’ll ensure that they create different molds designed to take the shape of the different products to be manufactured. The mold cavity usually features the use of a metal material either steel or aluminum. The best thing about this process is that it can be used to produce a variety of products. Regardless of the size or shape in question, this process will enable you to get your desired results. The only catch is to have a well-designed mold cavity that will help you get your end product.
Source: www.process-cooling.com
Plastic injection molding is a process that features the use of different plastic polymers to get desired end plastic products. In this process, the plastic polymers are melted and injected into the mold cavity in use to help get the desired shape. This process can easily be used to produce different plastic products. The products made using this process are designed to be of high quality and are used in different industrial applications.
Some of the industries that work with these plastic components include aerospace, medical, toy, and automotive. This goes to show that the plastic products that are designed using this process offer great performance. This makes plastic injection molding an amazing mold making technology to consider. Additionally, the use of this manufacturing process comes with the advantage of speedy production. You get to produce high quantities of the same high-quality plastic products within a short time frame.
Source: www.cadcrowd.com
The injection mold is the part where the molten material is received and the product created after it has cooled down. The injection mold comes in two parts including the mold core and mold cavity. When these two parts are closed, they create a void or space that is referred to as the part cavity. This part cavity that is created takes on the molten cavity that is injected into the mold.
The injection mold comes in handy when it comes to the production of plastic products in high quantities as earlier discussed. This is made possible by the fact that this machine can accommodate multi-cavity molds designed to create the same products. This can be done simultaneously and continuously depending on your specific requirements. Given the need to produce different sizes, shapes, and designs in the products being manufactured, injection mold design is an essential skill.
Creating the perfect injection mold that features the right dimension and is strong enough for the process requires the right skill and knowledge. When creating a fully functional mold, the use of the right grade of steel is essential. Steel features the ability to ensure that the molten products being used do not run or wear out during the manufacturing process. It is also important to pay attention to the cooling process in the injection mold. Ensure that the water lines are well placed to enhance cooling and reduce warping.
Additionally, when creating the injection mold, you need to pay attention to the gate to ensure that it features the right specifications and dimensions. This is important because these gates control the filling system and the flow of molten material into the mold cavity. They also help with the shut-off once the molten material in the mold cavity is enough. Creating the right injection mold for the products you want to manufacture is essential. When it comes to complex products that feature geometrical shapes and other aspects, you’ll need to work with complex molds. These molds come with additional features like undercuts, hydraulic cylinders, and threads among others.
Source: https://industrytoday.com
During the plastic injection molding process, the most important aspect to consider is the plastic resins to be used in the process. This is important because the choice of plastic material directly affects the molding process and the overall performance of the product manufactured. However, there are a variety of plastic materials available making the selection process harder. To make this easier, you need to consider the product you want to create, its application, and the environment. To get a better understanding, here are a few plastic resin materials that you can consider.
Nylon (Polyamide)
Nylon features a high melting temperature and great chemical resistance. This makes it a strong and adequate material to use in the injection molding process. This material is commonly used to create strong mechanical parts in the automotive industry.
Acrylic
Acrylic is mostly used in creating transparent products. It features high tensile strength and high resistance to scratches and effects by the weather. This material is mostly used in the manufacture of windows and various lighting equipment. It is also featured in refrigerators mainly because it doesn’t have any harmful chemicals like BPA that would affect food
Polycarbonate
Polycarbonate is a thermoplastic material that is strong and offers great performance on products using this material. When it comes to molding, this material is designed to be quite predictable and features a uniform mold shrinkage. It is the perfect option when looking for a material stronger than acrylic.
Polyoxymethylene (POM)
Polyoxymethylene is a strong, tough, and rigid thermoplastic material that is mainly featured in the automotive industry. It is used in the manufacture of gears, fasteners, and ball bearings among others.
Polystyrene (PS)
When it comes to Polystyrene, you’ll be working with two options. You can either go with High Impact Polystyrene (HIPS) or General Purpose Polystyrene (GPPS). The high-impact polystyrene material is opaque and strong. It is mainly featured in the manufacture of hard toolboxes. The general purpose polystyrene material on the other hand is transparent and is used in the manufacture of household products.
Polypropylene (PP)
Polypropylene features great impact strength, elasticity, and toughness that makes it an amazing material to consider. It is mainly featured in products used for food storage and packaging. This goes to show that it doesn’t feature any harmful chemicals.
Source: https://medium.com
With plastic injection molding, you’ll have the ability to create different products that you can use in different applications. Some of the most common products featured in injection molding include:
Source: www.stebro-mold.com
One of the most manufactured products using the injection method is the plastic bottle. Many companies find the use of injection molding and blow molding for their plastic bottles more efficient and cost-effective. Most plastic bottles used in holding water and other drinks for consumers are made using this manufacturing process. In the manufacture of these bottles, you’ll find the use of the polyethylene terephthalate material. This material is preferred mainly because it is light and also strong.
When it comes to the fabrication of electronic housings, the best process to work with is preferably injection molding. The housings manufactured are designed for different electronics including televisions, remote controls, computers, and medical equipment among others. With injection molding, you can typically work on creating any plastic housing you desire for different applications and in different sizes.
Source: https://toolless.com
Source: https://superiorplastics.com
To create different toys in a range of colors, sizes, and shapes, using injection process to get plastic toy mold is an amazing option. It will feature the use of liquefied firm plastic granules that is injected into the mold and cooled to get the perfect and strong toys. For instance, the lego brand of toys is designed and manufactured using the injection molding process. This results in durable toys that kids can play with for a long time.
Some of the items we use at home are fabricated using the injection molding process. This especially applies to different kitchenware items. The use of this process results in strong and long-lasting household items for consumers. Molding in home appluance is quite common and easy, if you are interested, you can even learn how to mold plastic at home by yourself.
Source: https://inhabitat.com
Source: https://advantechplastics.com
Some automotive parts will feature the use of strong and durable plastics for better performance. For instance, dashboard, bumpers, cup holders, and radio controls are some of the parts that will feature the use of plastic. These parts are manufactured and designed using the injection molding process to facilitate accuracy and efficiency.
You may be wondering what plastic products are featured when it comes to the healthcare industry. Well, this industry relies on plastic products a lot and adopts the use of injection molding to easily manufacture them in bulk. This is important because, in the healthcare industry, most of the products will be single-use and will be disposed of after use. Doing this helps prevent the spread of germs and other different infections from one patient to another. Some of the tools featured in injection molding include plastic syringes, test tubes, and beakers among others.
Source: www.injectionmoldingpart.com
The injection molding service process is featured in the one-stop solition for various industries. It features 3 basic steps. These steps include:
Source: www.sz-changhong.com
The product design phase is one of the most important to ensure that you get all the necessary aspects sorted. This part of the process helps you avoid making any extensive mistakes that will render your manufacturing process inefficient. When coming up with the product design, you need to be practical and keep a few things in mind. Consider the product’s application, aesthetics, manufacturability, and assembly among others. Your design should feature these aspects and fulfill your desired requirements to ensure that you’ll be working with the right product design.
In most cases, developing product designs will be done with the aid of computer software. This is referred to as computer-aided design (CAD) and is preferred because it is more convenient and offers a faster prototype translation. This allows you to gauge whether your product design is applicable and realistic for large-scale production. Working with qualified designers and engineers will give you a better advantage and help ensure that you get high-quality designs.
Source: www.ennomotive.com
As earlier discussed, mould design is an important part when it comes to the manufacture of plastic products. It is designed depending on the kind of product you want to achieve. Typically, molds are made using metal material to make them strong and effective during the injection molding process. Some of the metals used include:
Hardened steel
This is a strong metal that comes in handy given that it offers better service and will last longer compared to other options. However, this metal comes with a higher price attached to it when first investing. Given its durability, the price per unit may be reduced significantly. If you’re dealing with the production of the same products in large quantities, this is the best metal to use for your mold design.
Pre Hardened steel
The pre-hardened steel does not feature the durability witnessed with the hardened steel. It however is a good option if you are not dealing with productions in large quantities. This metal option is cheaper compared to the hardened steel.
Aluminum
This is a perfect material when looking for prototypes of the product designs you are working on. It features the use of a single cavity meaning it can only be used to manufacture one product at a time. This is a perfect option to consider before moving to large-scale manufacturing.
Beryllium copper alloy
This metal is typically used in areas of the mold that need fast heat removal or where shear heat is concentrated.
Making sure that you pay attention to mold design will ensure that you prevent unnecessary mistakes from occurring. You’ll have the opportunity to work with an amazing mold design that works for you and that will deliver quality results. This will help make the production and manufacturing process easier.
Source: https://www.seasongroup.com
When it comes to the manufacturing process, thermoplastic and thermoset plastics are fed into the heating barrel. They are heated to a certain predetermined temperature to help get them into a molten state. Once this is done, the molten material is driven by a large screw through the gates into the mold.
When the mold is filled, the molten material will stay in place to facilitate its cooling. Once it is cooled it will have taken the shape and form of the mold being used. After cooling, the screw is then released, the mold opens and the end product is released. This manufacturing process will continue for the duration it will take to manufacture the specified number of products you are working with.
Source: https://www.custompartnet.com
By now, you already have an understanding of what injection molding entails. Learning how the injection molding machine works to facilitate this process will help you have a clearer understanding. When it comes to the injection molding machine, there are 4 aspects to consider that help in ensuring that your process is in order. They include:
Source: https://www.indiamart.com
This part of the machine holds the mold together to ensure that the molten material is allowed to fully form. The mold comes in two halves attached to a base. One-half of the mold that is found on the front is attached to a fixed base that doesn’t move. This half is also designed to align with the nozzle of the cylindrical injection tool. The other part of the mold is attached to a movable plate. This allows it to open and close as required during this process. This mold is known as the mold core. The clamping tool features quality hydraulics that allows it to push the mold cor towards the mold cavity with ease.
Manufacturers prefer to work with plastic pellets that have to be melted down to get the molten state. This is achieved in the injection unit that also ensures the right amount of molten material is introduced into the mold. This unit features the use of a hopper where the raw material is introduced. The hopper comes with an open bottom that then introduces the material into the barrel. Once there, the material is then heated and injected into the mold to facilitate the molding process.
Source: www.ptonline.com
Source: www.dc.engr.scu.edu
Once the molten plastic has been introduced into the mold, it begins the cooling process. This is an automatic process that happens once the material gets into contact with the mold surface. As the plastic begins to cool, it will solidify and immediately take the shape of the mold you are using. During this process, you may expect some shrinkage which you can easily address by ensuring dwelling takes place.
The mold opens only after the injected material has fully cooled and solidified. Once the material is fully cooled, the hydraulic clamp releases and allows the mold to open from one half. After the mold has opened, the cooled material will be released.
Source: Pinterest
Source: www.techbriefs.com
Like any other manufacturing process, injection molding features both advantages and disadvantages that you should consider. Some of the advantages to keep in mind.
Enhanced efficiency and fast production
Injection molding allows manufacturers to produce multiple plastic products without compromising on quality. This enhances its efficiency and makes the use of this manufacturing process a great investment.
Low labor cost
Injection molding is an extension of automation in the manufacturing industry. Most of the process takes place and is run by the machine itself. Having one employee to keep an eye on the processes will suffice. This helps reduce the cost of labor and investing in more employees.
Variety in material choice
As discussed earlier, there are so many materials for you to consider when working on creating plastic products using the injection molding process. This is a great advantage given that you get the convenience of having a variety to choose from.
Design flexibility
When it comes to injection molding, you have unlimited design options to work with. All you need to to ensure that your mold design features the exact design you want. This gives you great flexibility to come up with amazing designs.
Product consistency
Given that you are working with a quality mold design that is not going to change no matter how much you use it, you can be sure that your product consistency will be on point. You won’t have to worry about one product turning out differently compared to others.
Enhanced strength
When working with injection molding, it is possible to add fillers during the process. These fillers come in handy to enhance the strength of your plastic products.
On the other hand, some of the disadvantages that may feature when using this process include:
High tooling cost
When it comes to injection molding as discussed earlier, you’ll need to go through 3 different phases. During the design phase, you’ll need to work with other processes like 3d printing to produce a working prototype. Once you have this, you’ll then need to create a mold and replicate it for large-scale manufacture. This can translate to be a costly process.
Costly on small productions
Injection molding is amazing when it comes to manufacturing plastic products in bulk. However, when it comes to producing the products in small quantities the process will prove to be more costly.
Source: https://www.ien.com
Different injection molding defects may be experienced in this process. These defects will require different actions taken to help prevent such occurrences. Some of the most prevalent defects to keep your eye on and their preventative solutions include:
Flow Lines
When it comes to flow lines they appear as a wavy pattern that may come in a different color compared to its surrounding. It is featured in a narrower section of the plastic mold. This is most likely caused by the inconsistency in speed when it comes to cooling the molten material. This can be prevented by increasing the injection speed, temperature, and round the corners of the mold where wall thickness increases.
Burn Marks
These burn marks usually appear as black discolorations on an edge of the molded plastic part. This is caused by trapped air or when the plastic pellets overheat during the injection. The best way to prevent this is by lowering the melt and mold temperature or reduce the speed of the injection.
Warping
When different parts of the molded product shrink unevenly, this is what is referred to as warping. This is associated with cooling that happens too quickly and can be worsened by prior exposure to very high temperatures. This can be prevented by ensuring the cooling process is gradual and lowering the temperature during the injection.
Sink Marks
Sink marks are small recesses or depressions in an otherwise flat and consistent surface of a molded part. This is caused by the material cooling too slowly. To prevent this, increase holding pressure and increase the cooling time.
Source: Pinterest
When it comes to injection molding, the best way to navigate this is by working with an accomplished and well-known injection mold manufacturer. You’ll get to work with an established R&D department that is well equipped to bring your designs to life. One of the best plastic injection mold manufacturers to consider is FOW Mould. They work to ensure that all their processes are efficient and accurate in the manufacture of plastic products. This makes them a preferred option among different businesses and companies in various industries. If you’re looking for the best manufacturer to work with, consider working with this particular brand.
Injection molding is a great process when working on manufacturing plastic products in bulk. Keep in mind the different aspects that come into play when working on these products. Ensure that you invest in working with the right injection molding manufacturer who will ensure that they provide great quality products.
Please contact us using the form below or emailing (harry@fowmould.com)