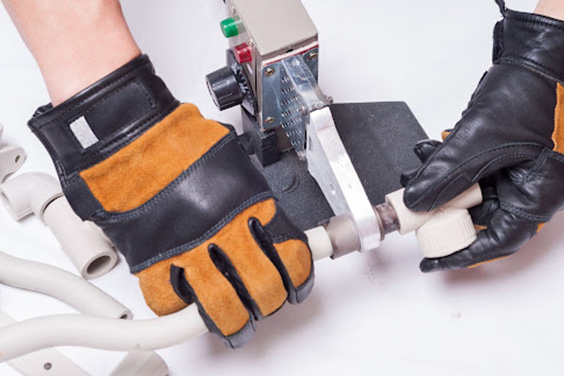
Injection molding may be one of the best plastic molding processes around, but it isn’t without its flaws. Quality issues are always present, and this can affect the safety, function, and performance of the product in question. The issues are never deliberate; they are due to various problems arising from the mold manufacturing process itself, the nature of the material, the tooling design, or a combination of all three factors.
We’ll be exploring some of the most common injection molding problems and solutions to help you deal with the obstacles if they ever arise in your manufacturing establishment. The following are the ten most common injection molding defects.
Source: www.creativemechanisms.com
Flow lines are the wavy patterns that appear on the surface of most flat-based mold products like buckets mould, plastic box mould and other containers. Sometimes they appear in the form of colors that are different from the main color of the product, and at times, they appear as slight grooves that follow well-defined patterns over and over again. They may not affect the integrity of the product, but they are unsightly to the eyes.
Flow lines are caused by the variations in the cooling speed or the difference in thickness.
Raise the injection speed, the temperature of the material, and the pressure to ensure uniform filing before any cooling starts taking place.
Use an even surface for molding to ensure even distribution of the mold.
Increase the diameter of the nozzle.
Source: Google
These are characterized by the rust-colored and black discoloration that can be seen on the edges of plastic products. Although they don’t affect how the product performs, they make the item in question look bad, and this can put people off from buying such items as they tend to assume they are not brand new and have experienced some form of damage.
Burn marks are caused when air is trapped inside the mold or the overheating of the resin itself. When coupled up with fast injection speeds, the overheating causes some burning on the edges.
Lower the mold and melting temperatures.
Bring down the injection speed.
Make the gas vents and gates bigger to give trapped air an avenue of escape.
Reduce the cycle times for molding to stop the resin from overheating.
Source: blog.asaclean.com
Waring happens when different directions of the same mold shrink unevenly. This is due to uneven cooling, and it causes a lot of tension in the structure and can impact the ability of the final product to put in optimum performance. This is noticeable when you place an item that’s supposed to be flat on the ground, and it slants slightly. Rapid cooling is the biggest cause of this effect.
Slow down the cooling process to make it gradual.
Lower the temperature of the material.
Switch to raw materials that don’t shrink too much.
A do-over of Matrix’s mold design to gain some form of symmetry.
Source: www.nexpcb.com
Air pockets and vacuum voids are a big problem in processes that involve injection and blowing. The appearance of air bubbles and spaces inside a finished product is never a good look, and it has the potential to affect the structural integrity of the product.
The main cause of this would be the lack of adequate pressure to squeeze out air from the mold while it is still pliable. This ends up trapping the air as rapid cooling begins taking hold. Another cause would be the material nearest to the mold walls faster than required causing the material to harden and stretch outwards, creating little vacuum pockets.
Raise the pressure of injection to squeeze the air out.
Go with a material that has a lower viscosity to limit the formation of bubbles.
Position the mold gates to the thickest parts of the mold to stop premature cooling from happening.
Source: www.engineersrule.com
Sometimes you may find small depressions and dips on a fairly flat plastic material, and that can be an unsightly appearance. This usually happens when the inside of a molded product shrinks faster then pulls in material from the outside towards the center
The main culprit behind this defect is the slow cooling of the exterior parts that end up creating some form of tension in the structure, leading to slight shrinkages in some areas. This inadvertently pulls the material inwards before it gets enough time to cool down sufficiently.
Raise the holding pressure and the time to allow the surface areas to cool down.
Increase the time needed for the cooling process to reduce shrinkage.
Make the component’s walls thinner to accelerate surface cooling.
Source: www.intouch-quality.com
There are times when you can clearly tell that an item is a combination of two identical parts, thanks to the bonding line that runs from one end to another. This kills the allure and mysticism that surrounds delicately made mold products. This weld line is thin but very discernible, and it can lower the integrity of the item in question.
Weld lines are caused when the two identical parts that need to be joined together have varying temperatures as they come together, casting an unbalanced and partial bonding in some parts.
Increase the temperature of the material to avoid partial hardening.
Raise the speed and pressure of the injection to stop premature cooling.
Use a matrix that doesn’t have partitions.
Use raw materials with lower melting temperatures and viscosity for faster flows.
Source: www.plastictroubleshooter.com
Jetting occurs when solidification starts taking place inside a cavity being filled by molten mold before complete fill-up is finished. This creates an ugly squiggly line on the surface that deforms the final appearance of the product. This can also compromise the ability of the product to function as designed.
Jetting tends to be common when the molten material is injected through a gate that’s way too small, causing the molten material to squirt erratically, cooling faster than intended while the cavity is half empty.
Scale down the injection pressure to stop the squirting.
Increase the temperature to stop early solidification.
Redesign the gate.
Source: www.plastictroubleshooter.com
Discoloration occurs when the melting crucible is not cleaned well, and this allows the mixing of a previous batch of overheated plastic pellets with a new batch. When they mix up, this leads to changes in the color, and you’ll notice some parts getting a little faded compared to others.
Poor thermal stability is the main cause of this, as well as the improper mixing of pellets before the melting process begins.
Clean the molds after every batch.
Invest in a purging compound to get rid of excessive color.
Use colors with good thermal stability.
Ensure the masterbatch is mixed well for consistency.
Source: www.patterson-rothwell.co.uk
This is a condition where you notice an extra layer on the surface of the material due to contamination in the manufacturing process. It resembles a faded out coating that can be peeled off, leaving behind ugly scars.
The main cause of delamination is the presence of foreign materials that happen to find their way in the masterbatch and end up getting rejected by the final mix, forcing them to create an extra layer on the final product.
Pre-dry the plastic before molding.
Watch out for contamination when mixing pellets.
Find good automated ejection mechanisms.
Source: www.laplastic.biz
There are times when some of the molten plastic escapes from the mold crucible through the parting lines or the ejector pin. Once these extrusions cool down, they become part of the final product, but since they were subjected to a different cooling process, they manifest themselves as extended thin patches on the extremities of the product. This is a defect called Flash
Increase the clamp pressure to limit spaces.
Clean the mold properly all the time.
Balance the injection speed, mold temperature, and ventilation for optimum performance.
Injection molding is used in many manufacturing processes in the plastic sector, and it is preferred by many because of the huge volumes of products it is able to churn out per minute. If you are a manufacturer looking to find more ways of dealing with each defect mentioned here, visit our website and get professional plastic injection molding service.
Please contact us using the form below or emailing (harry@fowmould.com)