Cold Runner Vs. Hot Runner: What's Their Difference
- Home
- > Blog
Share :
Share :
Cold and hot runners are important in the injection molding process, and each of them serves specific functions that are necessary for the desired results to be achieved. The more injection molding continues to develop, the better it is becoming in the manufacturing space, and that’s why more companies are adopting the process to get perfect mould design.
To better understand what cold runners and hot runners are, we are going to explore each of them, see how they work, compare their advantages and limitations, and look at some of the things that one has to consider when making a choice between the two. This will help you find the most reliable manufacturers who supply professional plastic injection molding service.
Cold Runners
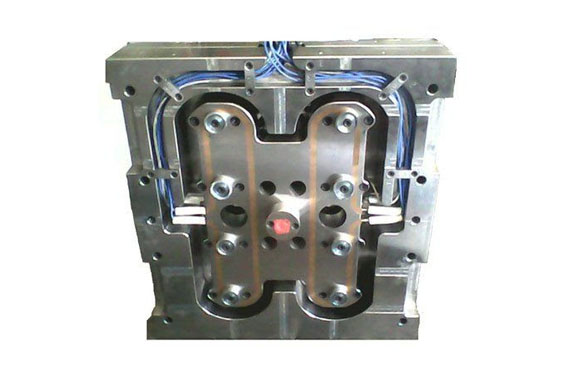
Source: Pinterest
Cold runner molds are constructed using 2 or 3 plates that are joined together inside the mold base. When the injection molding process begins, the molten material is injected into the mold using a nozzle through a sprue. This molten material then fills up a network of runners that are directed towards the empty cavities within the crate to make the final product.
In this system, the runners remain unheated to allow them to act as the delivery system that distributes the molten thermoplastic evenly to the individual molding cavities, hence the name cold runners. In this way, the cold runner also acts as the coolant that makes sprue, the gate, the runner, and the molded part to lose their heat as it cools down to form the end product.
All through the process using the two-mold plate, the runner and the sprue and the two-plate molds remain attached to the product, and they are only separated by the ejector once the cooling has happened. In the three-mold plate, there’s a stripper plate that has the sprue, and this delivers the molten resin to the entire runner network. The final product is then solidified and formed and automatically separated from all the attachments even without the ejector having a hand in it.
Considerations for Choosing Cold Runner Systems
Source: Pinterest
When it comes to choosing a cold runner system over a hot runner one, there are some considerations that you have to pay close attention to increase the level of efficiency and success. These factors include the following.
- Nozzles: Nozzles come in varying sizes, dimensions and they vary from one vendor to another. When selecting a runner, consider the possibility of disposing of the welded assemblies parts and the accessories that some nozzles come with, like removable water jackets that can make cleaning much easier.
- Runner Manifolds: cold runner systems usually come with gin-drilled runner manifolds that usually have some dead spots near the end of the channels. These make it hard for cured materials to be cleaned. Therefore, go for a runner manifold that is not only easy to access but one that makes it easy for disassembly to be done for proper cleaning that will allow the system to work better.
- Piston Assembly: There are certain systems that rely heavily on external barb fittings, airlines, and gun-drilled airways to get rid of the need for air hoses. These additional fittings are what kept the nozzle and other mechanical parts from getting damaged when they were in use.
- Pneumatic Connections: Cold runners usually have two options for disconnections. They can either use an external airline or an air terminal box. However, these two work differently, and each has its own complications that have to be dealt with for the successful disconnections to happen. Consider how far you will go for each before deciding on whether to go for a cold runner or not.
- Nozzle Tips: There are different types of nozzle tips that are being made for injection molding, and finding the right that fits the runner you intend to use is important. Some nozzles come with spring-loaded tips that allow room for thermal expansion. These types come in handy as they keep the injection nozzles in continued contact, and this prevents leakages.
Advantages of Cold Runners
- They are easy to produce and maintain, and the amount of time and effort it takes to repair them when they come apart is also easy.
- Cold runners are best suited for a wide range of polymers as they are flexible enough and they don’t deal with a lot of heat.
- There’s room for modifications to be done to the product while the process is still ongoing; things like color changes can be effected easily.
- The cycle times are much faster, especially when the cold runners are integrated with robotics.
- They are more cost effective considering the faster mold design changes that can be added along the way and the flexibility they bring to the manufacturing process.
Disadvantages of Cold Runners
- The runners have to be manually separated from the end product with each batch, and this is a lot of work, and it increases the chance for damage to take place.
- There are slower production times, and this is due to the fact that the separation of the runners and the product has to be done every time.
- There are part design limitations due to the cooling process. This makes cold runners the worst option to go with if you are looking to create large and complex parts.
- There’s more material waste because there is a lot of manual work involved, and this will automatically lead to product parts being scratched and cut, leading to wastage.
Hot Runners
Source: Pinterest
A hot runner is made up of two plates that are heated via a manifold system and it comes with both external and internal hot runners. This is the system you go for when dealing with materials that are sensitive to heat, as hot runners are able to be controlled through temperature variations. Hot runners are also the best option when you are looking to enhance the flow of molten materials as it maintains that high temperature that keeps the resin in the molten state just enough for the caret to be filled up evenly.
The heated runner system comes housed in a separate plate that remains stationary throughout the molding process. There’s another core plate that opens up to expose the final product without any of the runners attached to it and is ready for ejection.
There are about two types of hot runners that are used in the modern injection molding process. They include the following.
- Insulated Hot Runners: This is an unheated type of runner that comes laden with thick runner channels that keep the molten material hot throughout without any additional heating. They have bigger passages and are inexpensive, effectively eliminating the need for a manifold.
- Heated Hot Runners: This is a type of runner that is heated throughout the entire process, and it comes with thinner walls which ensure the what is able to reach the molten plastic inside to keep it hot until it reaches the crate.
Considerations for Choosing Hot Runner Systems
Source: Pinterest
Just like a cold runner system, there are considerations you have to think of when it comes to selecting a hot runner. These factors include the following.
- Injection Pressure: The plastic that’s found inside a hot runner has to stay hot, and this means that the internal pressure has to drop. This could end badly for the final product. Therefore, check for the internal injection pressure first before making the selection.
- Heating: Heating is the foundation of the hot runner system, and the ability of the components to maintain the neat all through is what makes the system work. You have to pay attention to the heating sources and the external and internal heating plates, and how the runners transport the resin from one point to the other. All these have to work in tandem with each other to ensure that molten material is able to safely reach the rate without dropping temperature.
- Gate Type: Hot runner systems have the advantage of being able to use a wide range of gates. Consider the gate marks, the location, and the materials that are compatible with that particular gate when choosing to go with a hot runner over a cold runner. For instance, crystalline thermoplastics require mold gate designs that are different from what non-crystalline plastics will need.
- Runner Size: The size of the runner will have an impact on the general performance of the hot runner in question. If you miss out on this factor, then you risk having a system that will be plagued with degradation of the plastic components. To find the right runner size, pay attention to the drop in pressure, the temperature, the residence time, among many other factors.
Advantages of Hot Runners
- Hot runners have extremely fast cycle times as they don’t require any manual work to separate the plates from the products. The ejectors can handle that automatically.
- There’s improved quality and consistency in the components of the product being made.
- There’s less waste generated since the heating is maintained all through, and anything that doesn’t get used can always be injected into the next batch.
- It is the best option when it comes to the fabrication of larger parts
- There’s less injection pressure involved.
- The mold engineer has more control over the process
Disadvantages of Hot Runners
- There are higher tooling costs when it comes to hot runners. If you are dealing with high volume production, then a hot runner is what you should avoid at all costs.
- The machining process is very difficult as the hot runner system requires a high accuracy for the desired results to be attained.
- The repairs and maintenance process is very complicated.
Conclusion
The choice to go with hot or cold runners comes down to the nature of work you want to deal with and the resources that you have at your disposal. Each of them is best suited for certain functions and figuring that out is what will help you find the best reasons to make a choice for more information on injection molding and how the runners function, check out our website.