In the world of manufacturing, knowing how to make plastic parts efficiently is a critical skill. From small plastic parts to custom plastic components, the process involves a series of steps that require precision, expertise, and a clear understanding of the design and functionality of the part. This article provides a comprehensive step-by-step guide on how to make plastic parts, focusing on the key stages of the process, from the initial design proposal to the final stages of production and quality control.
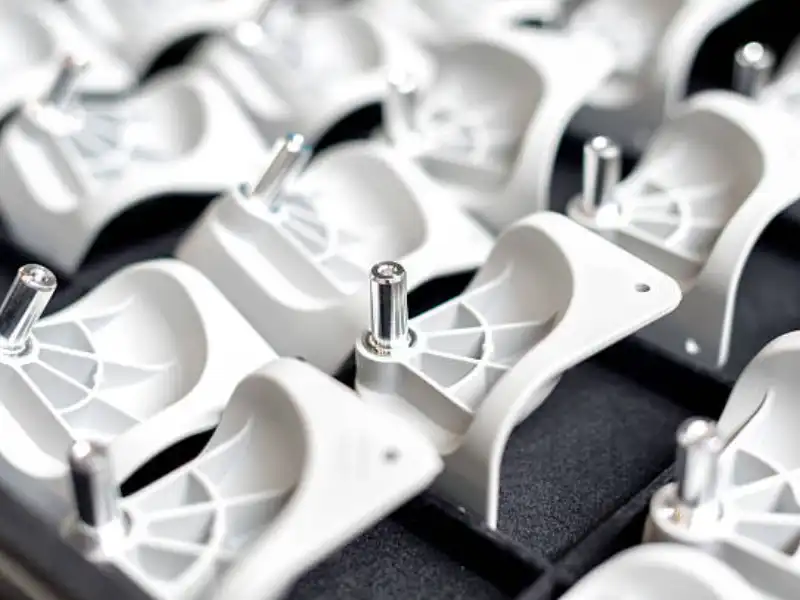
How to Make Plastic Parts?
Creating custom made plastic parts involves a series of steps, each crucial to the overall quality and functionality of the final product. The process begins with a design proposal, followed by consultation with experts, material selection, choosing the manufacturing process, prototyping, refinement, listing specifications, production, quality control, and finally, post-production. Each of these steps plays a critical role in ensuring the efficiency of the entire process and the quality of the custom plastic parts produced.
Design Proposal
The first thing in the process of making plastic parts is the design proposal. This involves sketching your idea for the part, considering factors such as complex geometries, tolerance requirements, and end-use factors that could affect performance. The design process is not just about drawing a sketch; it involves a lot of trial and error, refining the design based on functionality and manufacturability. The design proposal is the foundation upon which the rest of the manufacturing process is built.
Consultation
Once the design proposal is ready, the next step is consultation. This involves engaging with experts in plastic part engineering to review the design. These experts provide valuable feedback on the design’s feasibility and potential improvements. They play a critical role in ensuring that the design is fit for manufacturing and will fulfill its intended function. The consultation phase is crucial in avoiding costly mistakes and ensuring a clear path towards efficient production.
Material Selection (Picking a Resin)
Features: Choosing the right resin is crucial as it determines the final product’s properties, including durability, heat resistance, and other physical characteristics.
Purpose: Always consider the part’s purpose. For high-temperature or corrosive environments, opt for resins with high heat and chemical resistance. For flexible parts, choose resins that can bend or twist without breaking.
Availability and Cost: Resins vary in terms of availability and price. While some are perfect for specific applications, they might be hard to obtain or costly. It’s essential to strike a balance between the resin’s cost and its functionality.
Compatibility with Manufacturing Process: Ensure the chosen resin is compatible with the intended manufacturing method. For instance, while some resins are ideal for injection molding, they might not be suitable for 3D printing. Understanding this relationship is vital for a successful material selection.
Selecting the Manufacturing Process
Selecting the right manufacturing process is another crucial step in making plastic parts. There are several processes you can use, each with its advantages and limitations. The most common methods include CNC machining, injection molding, 3D printing (additive processing), compression molding, and vacuum forming.
Manufacturing Process | Advantages | Disadvantages |
CNC Machining | High precision and accuracy, excellent surface finish, can handle complex geometries, suitable for a wide range of materials | High cost for large-scale production, requires skilled operators, material wastage |
Injection Molding | Ideal for mass production, high-speed, high-volume, cost-effective for large quantities, excellent surface finish | High start-up costs due to tooling, long lead times for tool production, not suitable for complex geometries in one half of the mold |
3D Printing (Additive Processing) | High degree of design freedom, excellent for prototypes and small quantities, quick design changes | Limited types of materials, slower and more expensive for large-scale production, surface finish and dimensional accuracy not as high as other methods |
Compression Molding | Suitable for molding complex, high-strength fiberglass reinforcements, preferred for large parts where tight tolerances are not necessary | Not suitable for all types of plastics, can be slower and more expensive for large-scale production |
Vacuum Forming | Cost-effective for large parts, quick design changes, shorter lead times | Not suitable for parts with complex geometries or parts that require tight tolerances, limited types of materials |
CNC machining
CNC machining is a preferred method for producing plastic parts due to its ability to produce complex parts with tight tolerances and superior surface finishes. CNC machines can handle the most advanced plastics, including PEEK, Vespel®, and Ultem®. There is also greater design flexibility with CNC machining as the machines can quickly be reprogrammed to produce the latest version of your part, minimizing downtime and outdated parts. This makes CNC machining an efficient choice for producing custom plastic parts.
Injection molding
Injection molding is another common method used in the production of plastic parts. It involves injecting molten plastic resin into a mold cavity, where it cools and hardens into the shape of the part. While injection molding has high start-up costs and long lead times, it is capable of producing millions of custom-designed plastic parts at a fraction of the cost of all other manufacturing processes. However, it is less suited for producing parts with complex geometries in one half of the mold, requiring multiple parts to be produced and then assembled together.
3D printing (additive processing)
3D printing, also known as additive processing, is a newer method of producing plastic parts. It allows for a high degree of design freedom, but it is notorious for poor surface quality and requires post-processing to achieve cosmetic standards and tight tolerances. 3D-printed parts are also limited in the types of plastics they can use. Despite these limitations, 3D printing can be a fast and cost-effective method for producing small quantities of custom plastic parts.
Compression molding
Compression molding is a method of molding in which the molding material, generally preheated, is first placed in an open, heated mold cavity. The mold is closed with a top force or plug member, pressure is applied to force the material into contact with all mold areas, while heat and pressure are maintained until the molding material has cured. The process employs thermosetting resins in a partially cured stage, either in the form of granules, putty-like masses, or preforms.
Vacuum Forming
Vacuum forming is a simplified version of thermoforming, where a sheet of plastic is heated to a forming temperature, stretched onto a single-surface mold, and forced against the mold by a vacuum. This process can be used to form plastic into permanent objects such as turnpike signs and protective covers.
Prototyping
Prototyping is a crucial step in the process of making plastic parts. It involves creating a sample or a preliminary model of the part to test its design and functionality. Prototypes reveal problems that can only be discovered in real-world applications, allowing you to hone your design as well as determine the efficiency and functionality of the part. Prototyping methods can include 3D printing or injection molding, depending on the project’s needs.
Refinement
After prototyping, refinement is the next essential step in the journey of how to make plastic parts. Based on the feedback and results from prototype testing, the design undergoes necessary adjustments. This iterative process ensures that the final product aligns perfectly with the desired specifications and quality standards.
Refinement might involve revisiting the design to optimize certain features, adjusting the material choice based on the prototype’s performance, or even switching the manufacturing method if the prototype reveals limitations in the initial choice. This step is crucial as it bridges the gap between the theoretical design and the practical application, ensuring that the final product is both functional and efficient.
Listing Specifications
Before moving to full-scale production, it’s imperative to list out the detailed specifications for the part. This includes defining the exact measurements, material properties (like the type of plastic resin, wall thickness, and color), durability requirements, and any other relevant details.
Having a comprehensive list of specifications ensures that the production process is streamlined and that each produced part adheres to the set standards. It also provides a clear reference for quality control, ensuring that every part meets the desired criteria.
Production
With a refined design and a clear list of specifications in hand, the production phase begins. This is where the bulk of the plastic parts are manufactured. Depending on the chosen method, whether it’s CNC machining, injection molding, or any other process, the production phase can vary in duration and complexity.
It’s essential during this phase to monitor the production closely, ensuring that the machinery is calibrated correctly and that the parts are being produced without defects. Regular checks and maintenance of the equipment can prevent potential issues and ensure a smooth production process.
Quality Control
Quality control is paramount when producing plastic parts. This phase involves rigorous testing and inspection of the produced parts to ensure they meet the listed specifications and maintain a consistent level of quality.
Tests might include dimensional checks, stress tests, and visual inspections. Advanced techniques, such as 3D scanning and digital microscopic review, can also be employed to ensure the highest level of precision and quality. Any parts that don’t meet the set standards are either reworked or discarded to maintain the integrity of the batch.
Post-Production
Once the parts have passed quality control, they move to the post-production phase. This might involve additional processes like assembly (if the product consists of multiple parts), finishing (like painting or polishing), and packaging.
Post-production ensures that the final product is ready for the end-user, whether that’s for direct sale or for integration into a larger product. Proper packaging is also crucial to ensure the parts are protected during transportation and storage.
Conclusion
Understanding how to make plastic parts efficiently involves a deep knowledge of each phase of the production process. From the initial design and prototyping to the final quality control checks, each step plays a crucial role in ensuring the final product meets the desired standards. With the right approach, tools, and expertise, producing high-quality plastic parts becomes a streamlined and efficient process.
Get a Quote With FOWMould
If you’re looking to produce custom plastic parts, FOWMould offers competitive pricing and expert guidance throughout the entire process. With years of experience in the industry, our team ensures that your project is handled with the utmost precision and care. Contact us today to get a quote and embark on your journey of creating high-quality plastic parts.