In the manufacturing industry, the choice between TPU and ABS is influenced by the varying requirements for material hardness and softness in different applications.
TPU’s excellent elasticity and flexibility make it suitable for applications such as phone cases, footwear, and flexible components.
On the other hand, ABS is a high-rigidity and tough plastic, which holds a significant position in applications requiring high durability, such as automotive parts and LEGO toys.
So, which material is superior, TPU or ABS?
To find the answer, this article will conduct a comprehensive TPU vs ABS showdown, examining their key properties, application areas, and advantages and disadvantages in different usage scenarios, helping readers better understand the differences between these two materials.
What Is TPU?
TPU, or Thermoplastic Polyurethane , is an elastomer that can be plastified by heating and dissolved by solvents.
It is primarily divided into polyester and polyether types, with a wide hardness range (60HA-85HD).
TPU boasts high strength, high toughness, excellent wear resistance, and oil resistance, along with good processing performance.
It is widely used in industries such as defense, medical, and food.
Additionally, TPU is an environmentally friendly material, with halogen-free flame-retardant TPU capable of replacing soft PVC to meet the increasing environmental requirements in various fields.
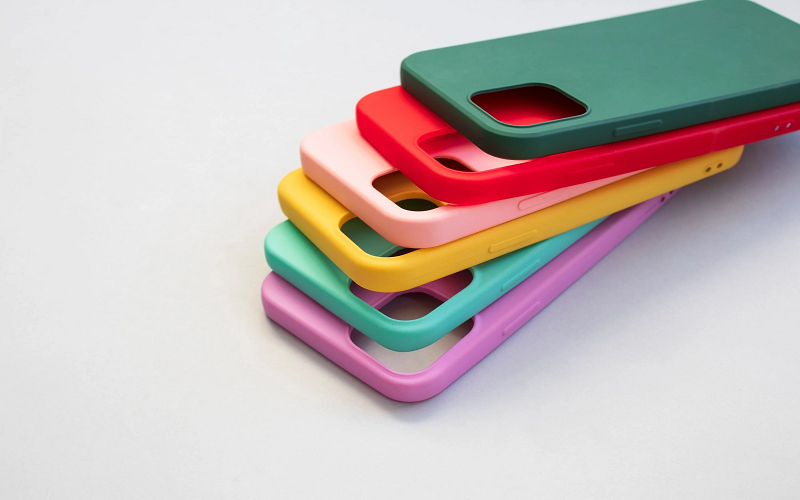
What Is ABS?
ABS plastic is a terpolymer of acrylonitrile (A), butadiene (B), and styrene (S), with adjustable monomer content to create various resins.
Acrylonitrile gives ABS chemical stability, oil resistance, and rigidity; butadiene enhances toughness, impact resistance, and cold resistance; styrene provides good dielectric properties and processability.
By adjusting the proportions of the three components in ABS, its properties can be modified, resulting in different types of ABS plastic to meet various application requirements, such as high-impact ABS, heat-resistant ABS, and high-gloss ABS.
Consequently, ABS plastic is widely used in automotive parts, electronic device housings, household appliances, and toys, making it an indispensable material in modern manufacturing.
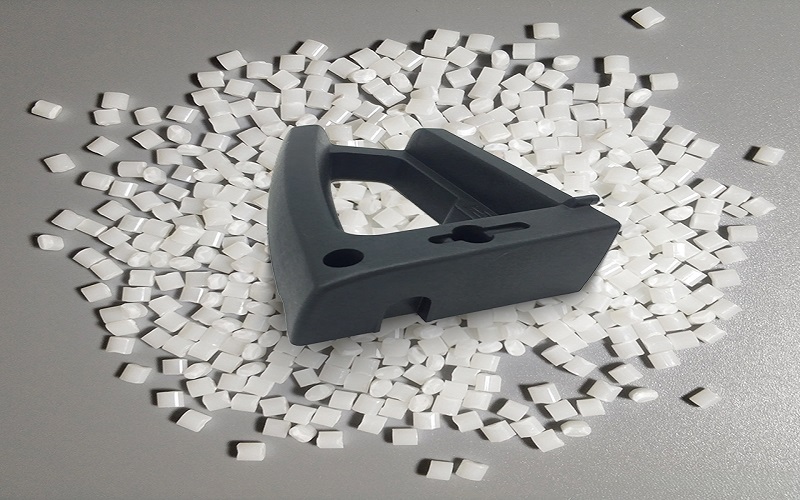
TPU vs ABS:Properties
From a performance perspective, TPU and ABS each exhibit unique and distinct advantages.
Properties of TPU
- Exceptional Wear Resistance: TPU’s wear resistance is more than five times that of natural rubber, making it a top choice for wear-resistant products.
- High Tensile Strength: TPU has a tensile strength of up to 70 MPa and an elongation at break that can reach up to 1000%.
- Excellent Water Resistance: TPU has excellent water resistance, showing no significant hydrolysis within 1-2 years, especially in the polyether series.
- Low-Temperature Performance: TPU can withstand temperatures as low as -50℃, making it suitable for low-temperature environments and capable of replacing PVC in applications where PVC becomes brittle.
Properties of ABS
- High Impact Resistance: ABS has excellent impact strength and can be used at extremely low temperatures. Even if ABS products are damaged, they tend to experience tensile failure rather than impact failure.
- Outstanding Mechanical Properties: ABS combines rigidity and toughness, making it ideal for manufacturing durable parts that can withstand mechanical stress.
- Excellent Electrical Properties: ABS has good insulation properties, making it suitable for housings and components of electrical and electronic products.
- Versatile Surface Treatment: ABS surfaces are easy to electroplate, paint, and process, allowing for various appearance effects and meeting diverse design requirements.
Table1 :The physical properties of TPU and ABS
Properties | TPU | ABS |
Density(g/cm3) | 1.10-1.25 | 1.05-1.18 |
Melting Point(℃) | 160-220 | 217-237 |
Tensile Strength(MPa) | 70 | 40-70 |
Water Absorption(%) | 0.1-1.0 | <1% |
Shrinkage(%) | 0.4-1.5 | 0.4-0.9 |
Impact Strength (J/m) | 100-150 | 200-300 |
Heat Deflection Temp (℃) | 40-80 | 93-118 |
TPU vs ABS:Processing Methods
TPU and ABS materials are suitable for many common processing methods such as injection molding, extrusion, blow molding, and thermoforming, but their performance and application fields differ in these processes.
Injection Molding
TPU injection molding can effectively create complex, flexible shapes, making it suitable for products that require high elasticity.
On the other hand, ABS injection molding leverages the plastic’s high rigidity and wear resistance to produce durable and sturdy parts such as housings, casings, components, and toys.
| TPU Injection Molding | ABS Injection Molding |
Melt temperature(℃) | 180-240 | 220-260 |
Mold temperature(℃) | 30-60 | 40-70 |
Injection pressure(MPa) | 80-140 | 50-100 |
Injection speed | Moderate | Moderate – High |
Extrusion
TPU is commonly extruded into films, sheets, and profiles.
Its melt viscosity allows for smooth extrusion, producing high-quality, consistent products.
ABS extrusion is often used to produce continuous profiles or pipes, such as ABS pipes and window frames.
Blow Molding
TPU’s elasticity and toughness make it ideal for manufacturing hollow products such as tubing and containers.
In contrast, ABS blow molding is less common but can be used to create durable, lightweight containers and hollow parts.
Thermoforming
Both TPU and ABS sheets can be thermoformed into various shapes.
3D Printing
In addition to the above processes, ABS is also a popular material in the field of 3D printing.
Its common uses in additive manufacturing include prototyping, gears, and even tools, as it withstands physical stress better than some other common 3D printing polymers.
As one of the most popular 3D printing filaments, many leading 3D printing companies offer ABS filaments.
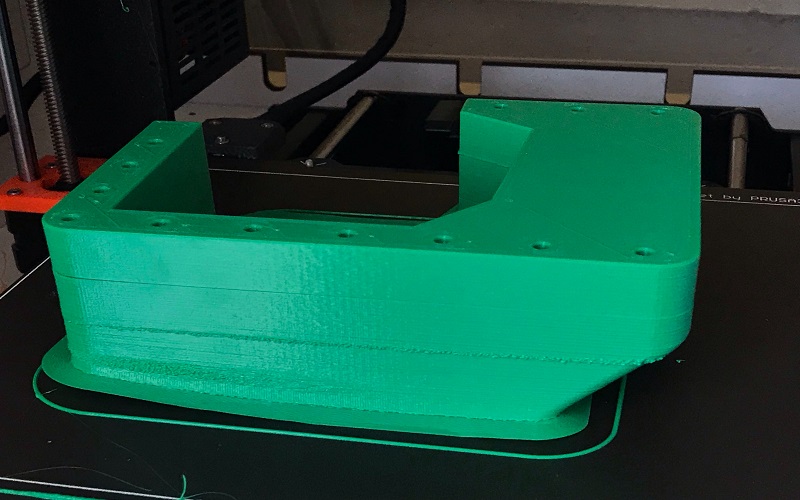
TPU vs ABS :Applications
ABS is commonly used in household appliances and is widely applied in boat hulls, decorative items, toys, and LEGO bricks.
Additionally, ABS’s electrical insulation properties make it an ideal material for manufacturing electrical component housings, as well as dashboards and bumpers in automotive parts.
Furthermore, ABS in 3D printing can be used to create high-precision and high-strength prototypes, gears, and tools.
In contrast, TPU with its excellent elasticity and wear resistance, is commonly used in footwear, sports equipment, phone cases, medical devices, and flexible tubing.
Due to its good low-temperature performance and oil resistance, TPU is also widely used in the automotive industry for seals and gaskets.
Meanwhile, TPU is used to manufacture transparent protective covers and films.
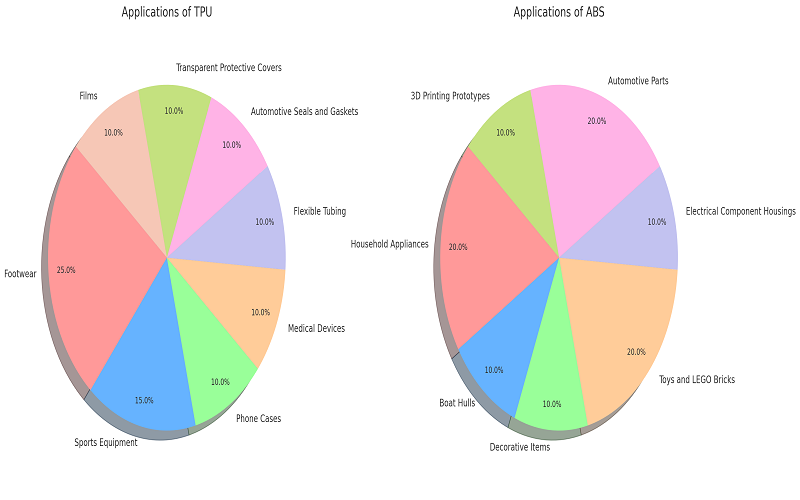
TPU vs ABS:Safety
With the widespread application of plastic products, many potential safety issues have emerged.
Therefore, it is necessary to evaluate the safety of TPU and ABS.
In the article “Is TPU Safe“, we learn that TPU is a non-toxic material with good biocompatibility, making it popular in medical applications such as catheters and medical tubing.
Additionally, TPU is considered an environmentally friendly material; its waste can be recycled and reused, and it does not produce unpleasant odors when burned, posing no harm to the environment.
In contrast, ABS plastic safety is far inferior to that of TPU. Although ABS itself is non-toxic, it releases harmful chemicals such as styrene and acrylonitrile when burned, accompanied by unpleasant odors, posing certain hazards to the environment and health.
Furthermore, the recycling rate of ABS products is low, and it is not biodegradable, which presents pollution risks.
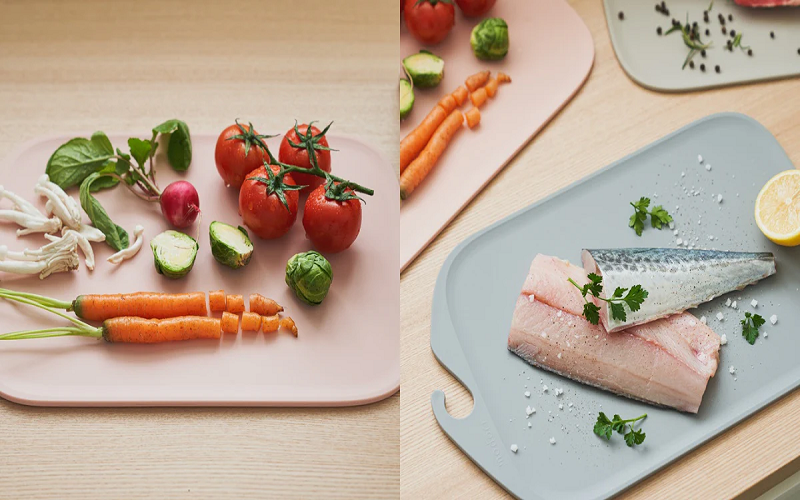
TPU vs ABS:Recyclability and Sustainability
TPU is widely recognized as a green, environmentally friendly, and high-performance new polymer material.
Polyester-based TPU, due to its strong hydrolytic and microbial degradability, exhibits significant natural degradability and environmental characteristics, capable of complete decomposition within months under specific conditions.
Additionally, TPU is recyclable. Waste TPU from cables, shoe soles, and phone cases can be sorted and processed for reuse in the manufacture of new polyurethane products, aligning with the principles of a circular economy and sustainable development.
In contrast, while ABS is theoretically recyclable, its actual recycling rate is low due to the complexity of the recycling process and the lack of recycling facilities.
Moreover, the quality of recycled ABS may not match that of the original material, limiting its widespread application.
Therefore, improving the recycling rate of ABS and reducing its environmental impact remains an important challenge.
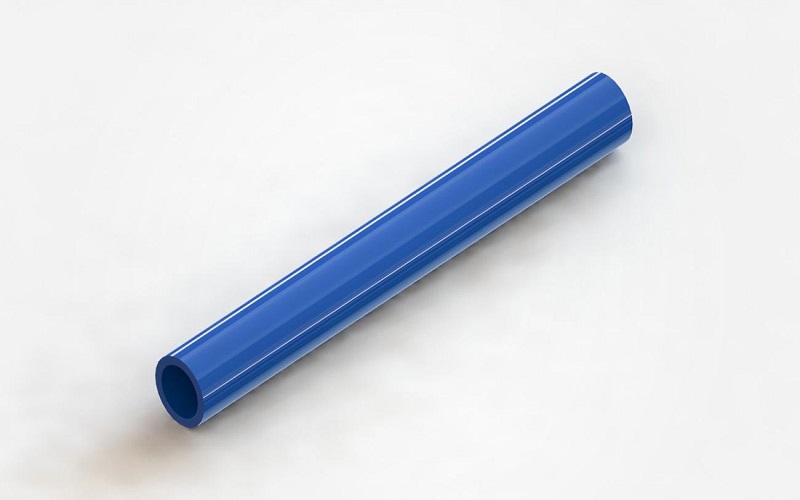
Conclusion
Overall, both TPU and ABS have their own unique advantages, making it difficult to determine which material is better.
TPU stands out in applications that require high flexibility and biocompatibility, such as medical devices, footwear, and sports equipment, due to its excellent elasticity, wear resistance, and environmental friendliness.
On the other hand, ABS is favored in fields that demand high strength and durability, such as household appliances, automotive parts, and toys, due to its high rigidity, impact resistance, and good electrical insulation properties.
The choice between TPU and ABS should be based on the specific application requirements.
For example, TPU might be a better choice for projects that require flexibility and prioritize environmental sustainability.
Conversely, ABS may be more suitable for applications that need high strength and impact resistance.