Impact-resistant plastics have a wide range of applications in various industries, from automotive and aerospace to consumer electronics and sports equipment.
This blog will discuss all you need to know about impact-resistant plastics, 5 of the popular types of impact-resistant plastics, and how to improve the performance of the plastics.
What Are Impact Resistant Plastics?
Impact-resistant plastics are materials that have the ability to withstand sudden and forceful impacts without breaking or cracking. These plastics are designed to offer a high degree of toughness, durability, and strength, making them ideal for applications that require resistance to impact and high stress.
Commonly used impact-resistance plastics include polycarbonate, ABS, PVC, PET, and polypropylene. These materials are often used in manufacturing safety equipment, automotive parts, electronic enclosures, and sports equipment.
Impact-resistant plastics are highly valued for their ability to provide safety and protection in various applications, and their popularity is expected to grow in the coming years.
One of the Best Impact Resistant Plastics: ABS
ABS (Acrylonitrile Butadiene Styrene) is a widely used impact-resistant plastic. Its unique combination of properties makes ABS injection molding a great choice for many applications.
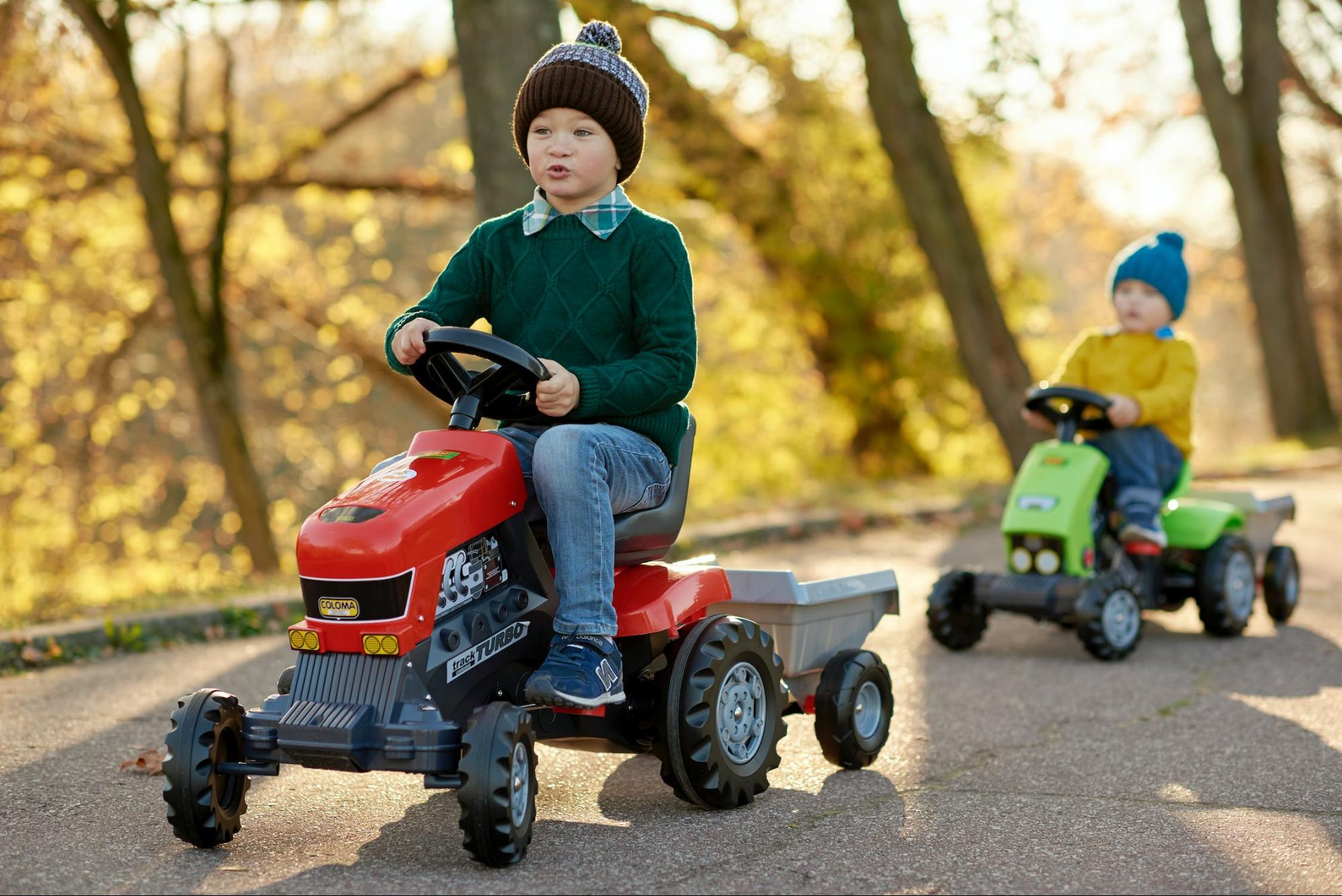
Advantages:
- ABS is tough, rigid, and impact resistant, making it an excellent material for applications that require strength and durability.
- It has good chemical and heat resistance.
Disadvantages:
- ABS can be prone to warping and shrinkage during the molding process.
- It has a relatively low melting point, which can limit its use in high-temperature applications.
Applications:
- ABS is commonly used in automotive parts, toys, electronics, and household appliances.
- It is also frequently used in 3D printing due to its ease of printing and strength.
- ABS is often used in the construction industry for piping, fittings, and roofing.
One of the Best Impact Resistance Plastics: HDPE
High-density polyethylene (HDPE) has a high strength-to-density ratio. HDPE is a good impact resistant plastic because it has tightly packed polymer chains in its structure. This makes it a tough and durable material that is suitable for various applications.
Also, it is a highly flexible material that is capable of absorbing impact energy without breaking or cracking.
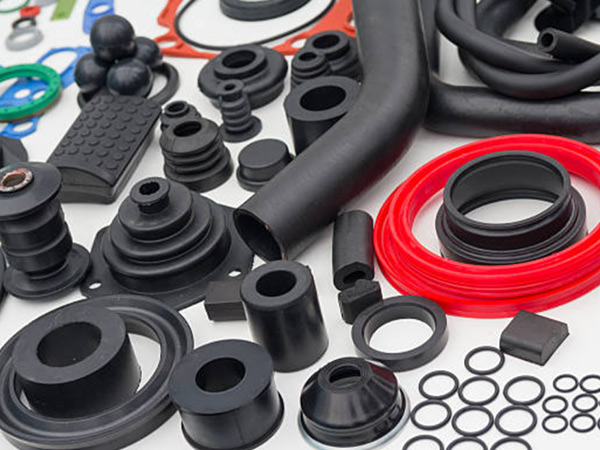
Advantages:
- HDPE is highly impact-resistant, making it ideal for tough and durable products.
- HDPE is lightweight, easy to machine and weld, and has a low coefficient of friction.
Disadvantages:
- HDPE is not as heat-resistant as some other materials and can melt at high temperatures.
- It is not as rigid as some other plastics, which can limit its use in specific applications.
Applications:
- HDPE is commonly used in packaging materials, such as bottles and containers.
- It is used in the construction industry for piping, insulation, and sheeting.
- HDPE is also used to manufacture toys, playground equipment, and automotive parts.
One of the Best Impact Resistance of Plastics: PC
Polycarbonate (PC) is a thermoplastic polymer with unique properties that make it ideal for various applications.
Advantages:
- It has excellent optical clarity and can transmit light better than most other plastics.
- PC is resistant to heat, chemicals, and weathering, making it ideal for outdoor and high-temperature applications.
Disadvantages:
- PC is prone to scratching, which can affect its optical clarity.
- It is more expensive than some other plastics, which can limit its use in certain applications.
Applications:
- PC is commonly used in the manufacturing of impact-resistant material and safety equipment, such as helmets, face shields, and safety glasses.
- It is used in the automotive industry for headlights, taillights, and instrument panels.
One of the Best Impact Resistant Materials: PAI
Polyamide-imide (PAI) is a high-performance engineering thermoplastic that is known for its exceptional strength and impact resistance.
Advantages:
- It is resistant to high temperatures, chemicals, and wear.
- PAI has excellent dimensional stability and is resistant to creep, making it ideal for high-stress applications.
Disadvantages:
- PAI is relatively expensive compared to other impact-resistant plastics.
- It can be difficult to process due to its high melting point and viscosity.
Applications:
- PAI is commonly used for engine components, bearings, and gears in the aerospace and aviation industries.
- PAI is also used in the manufacturing of medical devices, electronics, and automotive parts.
One of the Strongest Plastic: HIPS
High Impact Polystyrene (HIPS) is a thermoplastic polymer that is known to be one of the strongest plastic because of its excellent impact-resistant material and strength.
Advantages:
- It has good dimensional stability and can maintain its shape even under high stress. This characteristic earns it the title ‘strongest plastic’
- HIPS is lightweight, easy to process, and has a low coefficient of friction.
Disadvantages:
- HIPS is not as heat-resistant as some other materials and can melt at high temperatures.
- It is not as chemical-resistant as some other plastics, which can limit its use in certain applications.
Applications:
- It is used in the construction industry for wall insulation and roofing.
- HIPS is also used in the automotive industry for interior parts, such as dashboards and door panels.
How to Improve the Impact Resistance of Plastics?
There are various ways to improve the impact resistance of plastics, which can make them more durable and resistant to high stress. Here are some of the most common methods:
Copolymer Addition
One effective way to improve the impact resistance of plastics is to add copolymers to the base material. Copolymers are composed of two or more different monomers, which can enhance the toughness and strength of the plastic. For example, adding acrylonitrile-butadiene-styrene (ABS) copolymers to polystyrene (PS) can improve its impact resistance and make it more suitable for high-stress applications.
Polymer Blending
Another method to improve the impact resistance of plastics is to blend different polymers together. This can create a material with a unique combination of properties that are tailored to the specific application. For example, blending polycarbonate (PC) with acrylonitrile-butadiene-styrene (ABS) can create an impact-resistant and heat-resistant material, making it ideal for applications such as automotive parts.
Addition of Glass Fibers
Adding glass fibers to plastics can help improve their impact resistance and strength. Glass fibers are strong and stiff, reinforcing the plastic and making it more resistant to deformation and breakage. For example, adding glass fibers to polypropylene (PP) can increase its strength and toughness, making it more suitable for applications such as automotive parts and household appliances.
Other Methods
Other methods to improve the impact resistance of plastic include adding fillers, such as carbon fibers or silica, to the base material and incorporating elastomers, such as polybutadiene or ethylene-propylene-diene monomer (EPDM), into the polymer matrix. In addition, altering the processing conditions, such as adjusting the temperature and pressure during the molding process, can also affect the impact resistance of the plastic.
Proper Plastic Injection Molding Optimizes Your Impact Resistance Plastic
Proper plastic injection molding is crucial for optimizing the impact resistance of plastic products. By using the right injection molding techniques, it is possible to ensure that the plastic material is distributed evenly throughout the mold, reducing the risk of defects and improving the product’s overall performance.
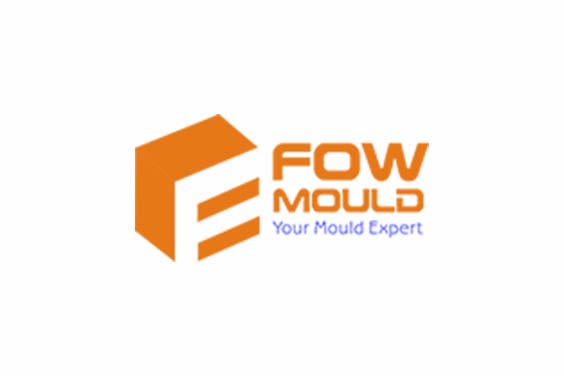
FOW Mould Has Fitted With Ultra-Modern Equipment for Injection Molding
FOW Mould is a leading manufacturer of plastic injection molds and provides a range of services that can help optimize the impact resistance of plastic products. With its state-of-the-art equipment and advanced technology, FOW Mould can provide precision injection molding that ensures uniform material distribution and reduces the risk of defects.
FOW Mould Provides One-Stop Plastic Injection Molding Services
FOW Mould offers one-stop plastic injection molding services, from CNC machining to over-molding, making it easy for customers to meet all their impact resistance plastics manufacturing needs in one place. By providing a comprehensive range of services, FOW Mould can ensure that the impact resistance of plastic products is optimized throughout the entire production process.
Conclusion
As a leading manufacturer of plastic injection molds, FOW Mould provides one-stop plastic injection molding services, including CNC machining and over-molding, to help businesses improve the impact resistance of their products. With its state-of-the-art equipment and commitment to quality, FOW Mould is a trusted partner for any business seeking to improve the performance of its plastic products.
Contact FOW Mould today to learn more about its plastic injection molding services and how they can help enhance the impact resistance of your products.