In the diverse world of plastics, Polycarbonate (PC) and Acrylonitrile Butadiene Styrene (ABS) hold a position of critical importance.
Despite many similarities, there are distinct differences in their specific properties and applications.
This article aims to offer a comprehensive perspective, analyzing characteristics, processing methods, and applications of both materials.
It seeks to provide reference information for injection molding suppliers who are making a decision between these two materials.
What Is Polycarbonate?
Polycarbonate (abbreviated as PC in English) is a high molecular weight polymer containing carbonate groups in its molecular chain, named after the -CO3 group present in its structure.
It can be synthesized from Bisphenol A and phosgene (COCl2). The more commonly used method today is the melt transesterification process, where Bisphenol A and diphenyl carbonate undergo transesterification and polycondensation reactions.
Based on the structure of the ester group, it can be classified into several types such as aliphatic, aromatic, and aliphatic-aromatic.
However, due to the lower mechanical properties of aliphatic and aliphatic-aromatic polycarbonates, their application in engineering plastics is limited.
Currently, only aromatic polycarbonates have achieved industrial production.
Due to the unique structure of polycarbonate, it has become the fastest-growing general engineering plastic among the top five engineering plastics.
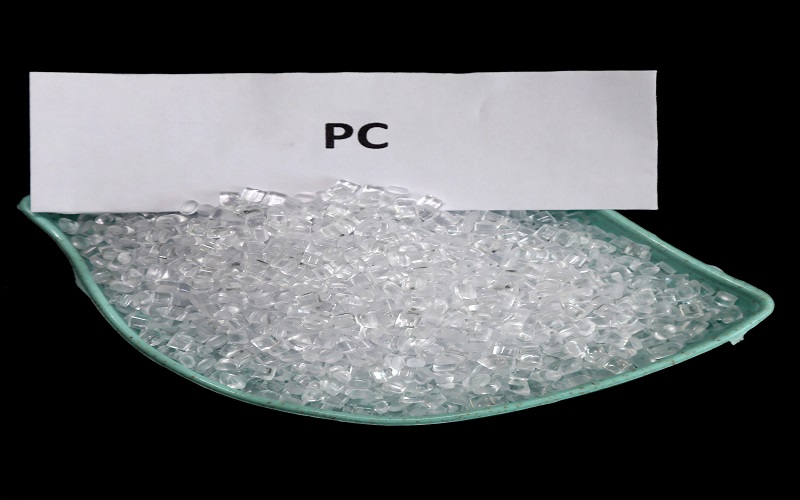
What Is ABS?
ABS material is a graft copolymer of three monomers: Acrylonitrile, 1,3-Butadiene, and Styrene.
Its molecular formula can be written as (C8H8·C4H6·C3H3N)x, but in reality, it is often a mixture of a butadiene-containing graft copolymer and an acrylonitrile-styrene copolymer.
ABS is usually a light yellow or off-white granular non-crystalline resin, and it is currently the most produced and widely used polymer.
The three polymers are mixed in a certain proportion and processed by adding organic solvents and plasticizers to ultimately form ABS material.
This mixed composition ensures that ABS material combines the advantages of different polymers, such as the impact resistance of acrylonitrile-butadiene-styrene copolymer, the rigidity of polypropylene, and the heat resistance of polystyrene.
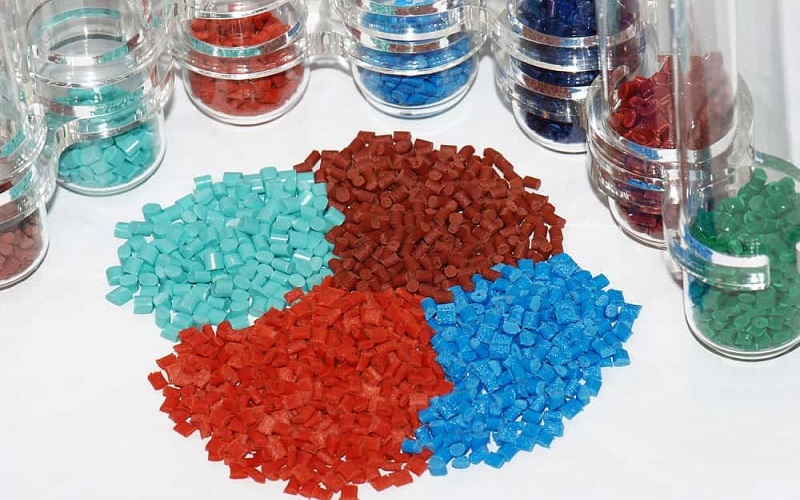
Polycarbonate vs. ABS: Physical Properties
When comparing PC and ABS, it’s important to look at their physical properties to understand their their respective characteristics.
Here is a comparison of key physical properties of PC and ABS:
Property | Polycarbonate | ABS |
Density(g/cm3) | 1.18-1.22 | 1.05-1.18 |
Shrink rate (%) | 0.5-0.7 | 0.4-0.9 |
Tensile Strength (MPa) | 61~75 | 27-52 |
Melting index(g/10 min) | 5-30 | 10-40 |
Water Absorption (%) | 0.2 | 1 |
Heat deflection temperature(℃) | 135 | 93-118 |
Young’s Modulus – Rigidity (GPa) | 2.3 | 2 |
Compared to ABS, Polycarbonate boasts superior tensile strength, greater resilience, and enhanced thermal stability.
However, the melt flow index of ABS is higher than that of PC, which translates to a stronger fluidity when melted, making it more conducive to processing in manufacturing applications.
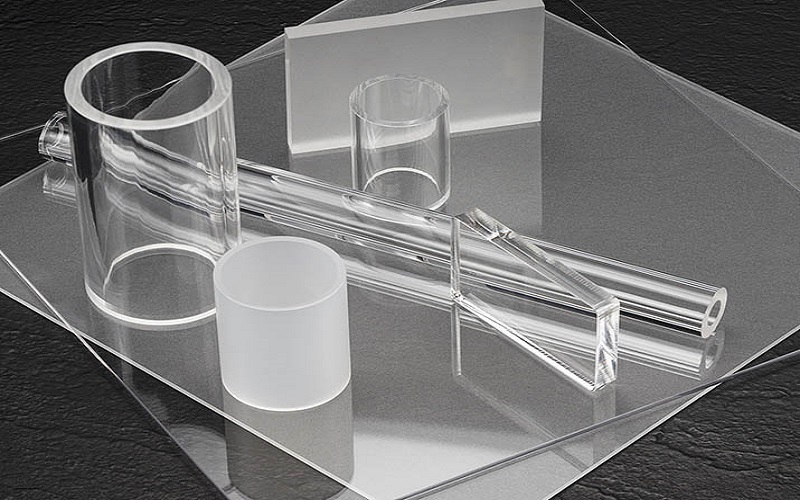
Polycarbonate vs. ABS: Pros and Cons
Polycarbonate (PC) high molecular weight resin exhibits high toughness, with a cantilever beam notch impact strength of 600-900 J/m.
Compared to polymethyl methacrylate (PMMA) with similar properties, PC offers better impact resistance, a higher refractive index, and superior processing performance, featuring UL94 V-2 grade flame retardancy without the need for plastic additives.
However, PC’s main drawbacks are its limited hydrolysis stability, making it unsuitable for products repeatedly exposed to high-pressure steam.
It is sensitive to notches, has poor scratch resistance, and tends to yellow when exposed to ultraviolet light over long periods.
On the other hand, ABS is easier to process than PC due to its lower melting point and higher flowability, making it suitable for complex shapes and sizes.
ABS has a smooth finish and can be easily painted, making it ideal for consumer goods where appearance is important.
In addition, ABS materials are resistant to a number of chemical corrosion, including alkalis, acids, and salts.
Generally less expensive than PC plastic, ABS is a more budget-friendly option for various applications.
And it amenable to surface treatments (like metal plating), making it the most commonly used material in injection molding and 3D printing services.
However, the presence of unstable, easily oxidized double bonds formed during the polymerization of butadiene in ABS makes its weather resistance and impact strength inferior to PC, limiting its use as a standalone material.
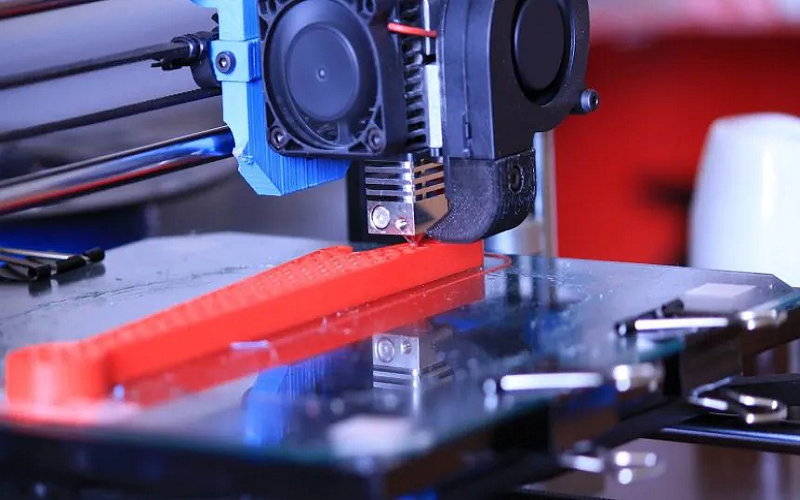
Polycarbonate vs. ABS: Applications
As two popular injection molding materials, Polycarbonate (PC) and Acrylonitrile Butadiene Styrene (ABS) overlap in several application areas.
Despite their differences in performance, the versatility of these materials makes them suitable for a wide range of products and applications.
Here are some common areas where PC and ABS are used in injection molding:
| Polycarbonate | ABS |
Automotive Parts | Dashboard systems and interior decorations | |
Medical Devices | High-pressure syringes, disposable dental tools | |
Electrical Enclosures | Distribution panel components, relay housings | |
Luggage | Generally, PC has better strength, but it is prone to notch effects, whereas ABS has better moldability but not as strong as PC |
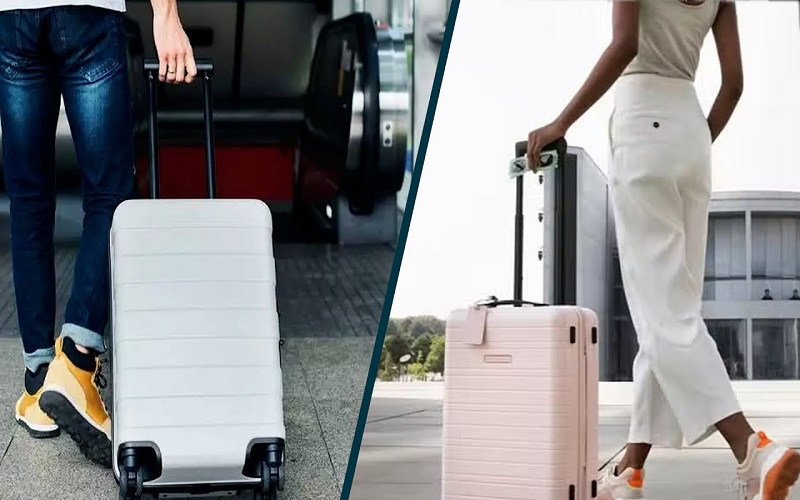
Common PC Examples:
Optical Applications: High transparency makes PC ideal for eyewear lenses, CDs/DVDs, optical lenses, and lampshades.
Packaging: PC injection moldingbottles (containers) are transparent, lightweight, impact-resistant, withstand certain high temperatures and corrosive solutions, making them suitable for recyclable bottles (containers).
Equipment Parts: PC is used for low-load parts in household appliances like motors, vacuum cleaners, hair washers, coffee makers, toasters, and handles of power tools.
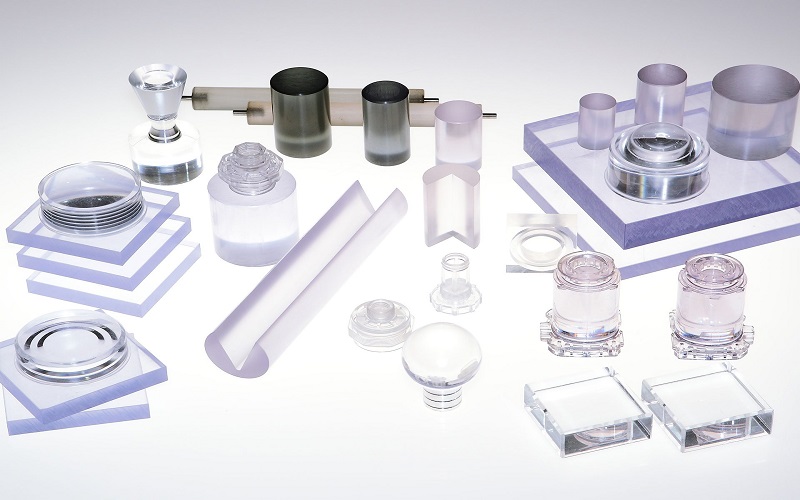
Common ABS Examples:
Children’s Products: Injection Molded ABS, known for its bright colors and durability, is a primary material for many children’s toys and Lego bricks.
Pipe Fittings: ABS pipes, known for their chemical resistance and durability, are used in wastewater and drainage systems.
3D Printing: ABS is one of the commonly used materials in 3D printing, suitable for printing various models and components.
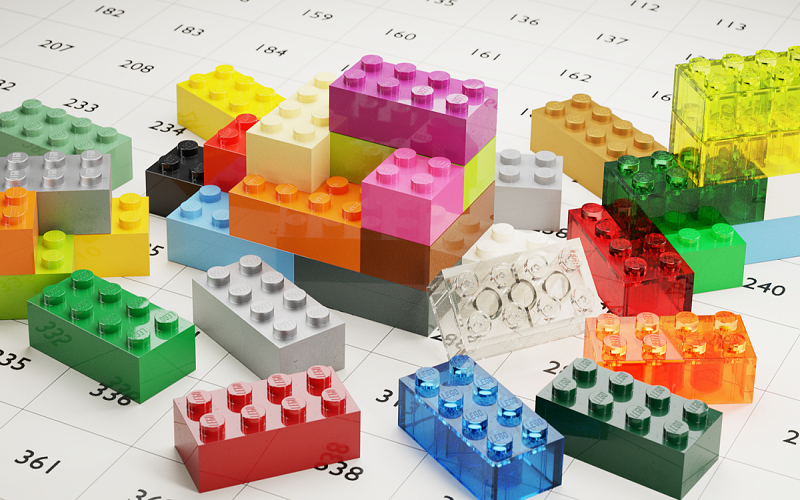
Blending of Polycarbonate and ABS
Due to the distinct advantages and limitations of polycarbonate plastic and Acrylonitrile Butadiene Styrene, these materials are blended to form PC-ABS material, overcoming some drawbacks.
PC/ABS is actually comprised of PC, Styrene Acrylonitrile (SAN), and grafted rubber.
When there is an excess of PC, it envelops the SAN, which in turn surrounds the grafted rubber.
This means the PC phase and the grafted rubber phase are separated by the SAN phase, creating a complex rubber phase structure.
The PC/ABS alloy merges the excellent features of both polymers, improving on certain deficiencies of PC and ABS.
Compared to pure PC, the PC/ABS alloy offers better flowability and processing capabilities, and its product stress sensitivity is decreased.
When compared to pure ABS, the PC/ABS alloy significantly enhances mechanical strength, heat resistance, and flame retardant properties.
Hence, it’s extensively used in manufacturing automotive interiors, communication devices, electronic appliances, and lighting equipment.
For more information on PC/ABS vs. ABS, please continue reading here.
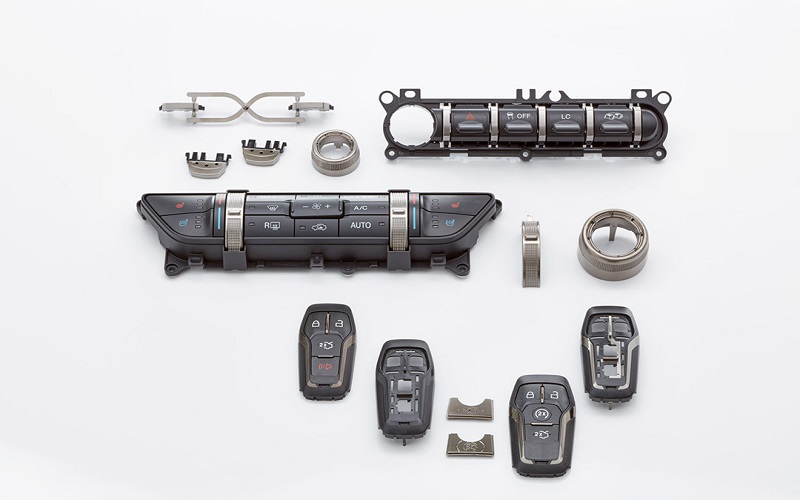
Conclusion
From the above content, we have gained an understanding of the material characteristics, advantages, and disadvantages of Polycarbonate and ABS, as well as their various applications. For further information about Polycarbonate and ABS, please contact FOWMOULD.
FOWMOULD offers a one-stop injection molding service from product design to actual production.