In modern life, we often encounter various plastic products from long-lasting vibrant plastic flowers to fire-resistant plastic goods, these seemingly ordinary items actually conceal a key technology — plastic additives.
The application of these additives not only makes plastic products more durable and safe but also injects new vitality into the entire plastic industry.
With the continuous advancement of technology and growing market demand, the plastic additives market is showing tremendous economic potential and prospects for innovation.
Next, let’s follow FOWMOULD to delve into the classifications, working principles, and their roles in various everyday applications of these additives.
What Is Plastic Additives?
Plastic additives are compounds added during the molding process of polymers (synthetic resins) to improve their processing performance or to enhance the properties of the resin itself.
Their main function is to improve the processability of polymers, optimize processing conditions, increase processing efficiency, and enhance the performance of the products, thereby increasing the value and lifespan of the products.
For example, plasticizers are added to reduce the molding temperature of PVC resins and to make the products soft.
Or, blowing agents are added for the preparation of lightweight, shock-resistant, heat-insulating, and sound-insulating foam plastics.
Some plastics have a thermal decomposition temperature very close to the molding processing temperature, making it impossible to mold them without the addition of heat stabilizers.
Therefore, plastic additives hold a particularly important position in plastic molding process.
To better demonstrate the role and characteristics of plastic additives, we will list specific types of plastic additives below.
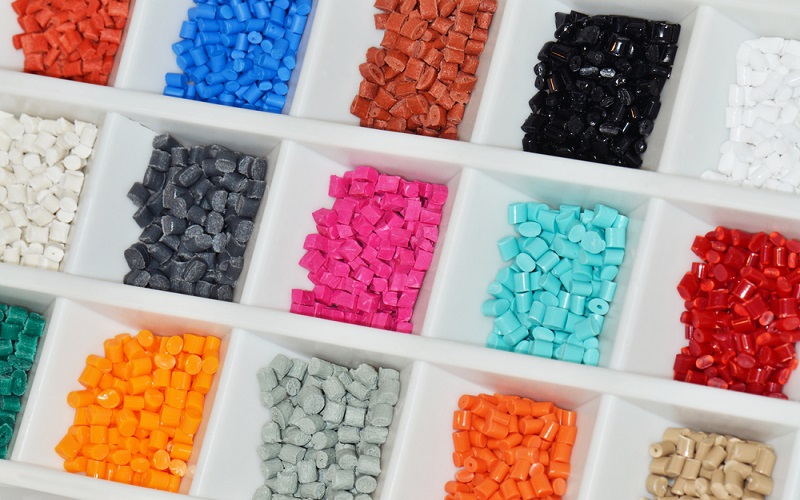
The Main Types Of Plastic Additives
1. Stabilisers
- Heat Stabiliser
Heat stabilizers are crucial additives in plastic processing, especially for polyvinyl chloride (PVC) and its copolymers, to prevent thermal degradation.
These stabilizers act by neutralizing hydrogen chloride, a catalyst released during PVC processing that can cause molecular chain breakdown.
The primary stabilizers typically include heavy metal salts and soaps like lead sulfate and lead stearate, while auxiliary stabilizers consist of epoxidized oils and esters that also impart plasticizing properties.
Their collective role is to maintain the integrity of PVC by preventing decomposition and enabling effective molding and processing.
- Antioxidant
Unsaturated double bonds in plastics are attacked by oxygen atoms, heat and light, causing breakage and free radicals, which leads to chain reactions.
This causes the molecular chain to break or form chain cross-links, leading to a reduction in the strength of the finished plastic product or making it brittle.
The function of antioxidants is to delay the decomposition of plastics due to oxidation and extend the life of plastic products.
Commonly used antioxidants for plastics are generally divided into five categories according to their molecular structure and mechanism of action: hindered phenols, phosphite, thio, composite and hindered amines (HALS).
- UV absorbers
Polymers undergo photodegradation when exposed to UV light.
UV absorbers are a class of chemical substances that absorb UV light or reduce the transmission of UV light.
It is capable of energy conversion, converting high-energy ultraviolet light into the form of heat or non-destructive longer light waves to release the energy, thereby protecting polymers from ultraviolet damage.
UV absorbers can be divided into the following categories according to their chemical structure: salicylates, phenyl ketones, benzotriazoles, substituted acrylonitrile, triazines and hindered amines.
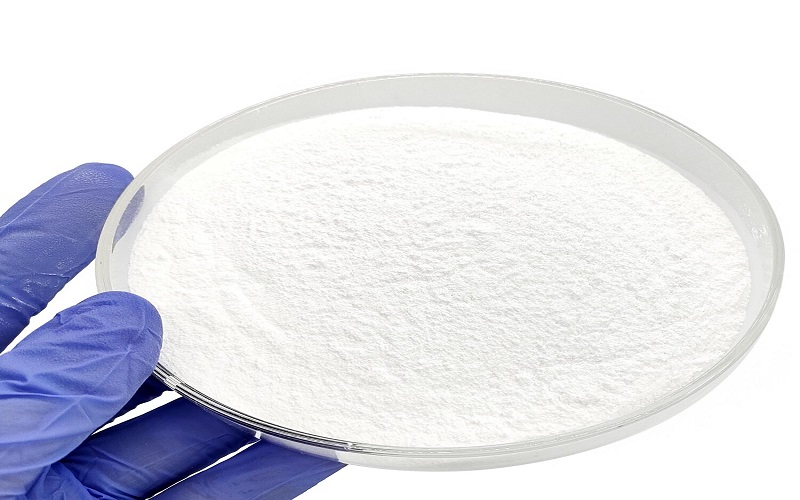
2.Processing aids
Processing aids are additives used to improve the rheological properties of plastics processing as well as moulding properties, usually low viscosity or surface energy, with a certain lubricating effect.
- Plasticiser
The vast majority of synthetic resins have plasticity, but the size of plasticity is not the same.
In order to make the resin easy to plasticise and give the products softness, generally in the resin to add some low molecular substances, these low molecular substances are called plasticisers.
These low molecular substances are called plasticisers. Plasticisers are liquid or low melting point substances, and should have good miscibility with resin.
Commonly used plasticisers are benzene dicarboxylic acid esters, sebacate esters, chlorinated paraffins and so on.
- Lubricant
Lubricants can be divided into internal and external types.
The primary function of internal lubricants is to improve the internal flowability of the resin by reducing the internal friction between the resin molecular chains, such as fatty acid esters (e.g., glyceryl monostearate).
External lubricants, on the other hand, reduce the adhesion of the resin to processing machinery and enhance the smoothness of the product surface, facilitating demolding, such as HoechstWax.
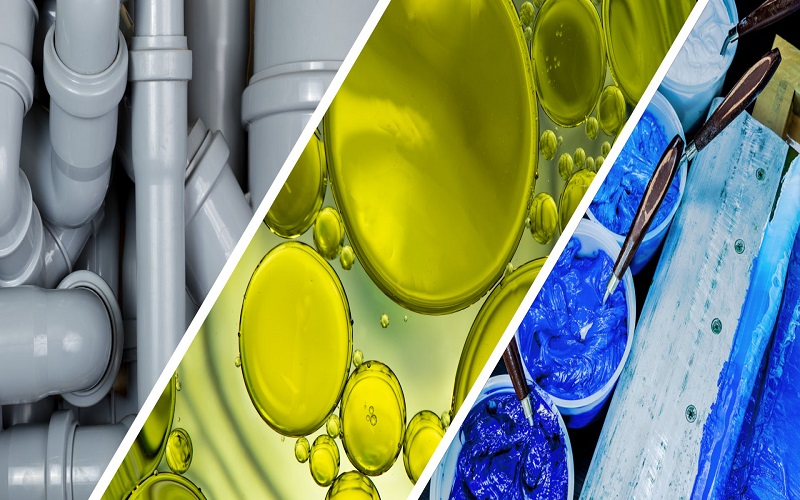
3.Fillers
Fillers are one of the common additives in plastics, serving to enhance material properties, reduce costs, and improve processability.
The amount of filler added typically ranges from 5% to 50%, varying according to the type of filler and the specific application of the plastic.
Common fillers include inorganic materials like graphite, calcium carbonate, and aluminates, as well as natural organic fillers like wood flour, coconut shell powder, and cotton.
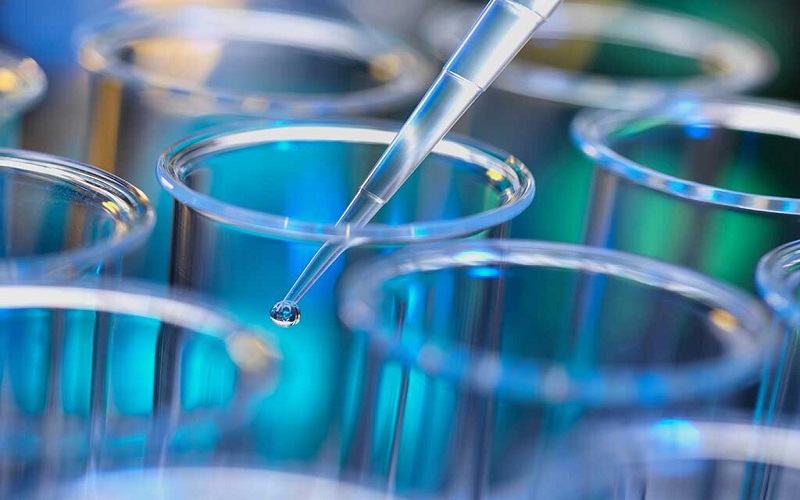
4.Coupling agent
The main function of coupling agent is to improve the interfacial properties between filler and polymer material.
It can reduce the viscosity of synthetic resin melt in the process of plastics processing, improve the dispersion of filler to improve processing performance.
In turn, the products obtain good surface quality and mechanical, thermal and electrical properties.
Its dosage is generally 0.5-2% of the filler dosage.
Coupling agent is generally composed of two parts: one part is pro-inorganic group, can be with inorganic filler or reinforcing material。
The other part is pro-organic group, can be with the role of synthetic resin.
Of the many coupling agents, organosilanes are the most widely used, while organotitanates are a more efficient alternative.
5. Cross-linking agents
Crosslinking agent is mainly used in polymer materials (rubber and thermosetting resin).
Because the molecular structure of polymer materials is linear, without crosslinking low strength, easy to pull off, and no elasticity.
The role of the crosslinking agent is to produce chemical bonds between the linear molecules, so that the linear molecules are connected to each other to form a mesh structure.
This improves the strength and elasticity of rubber, rubber crosslinking agent is mainly sulfur, in addition to add accelerator.
General crosslinking agent refers to organic peroxide, such as polyethylene crosslinking agent can be used peroxide diisopropyl benzene.
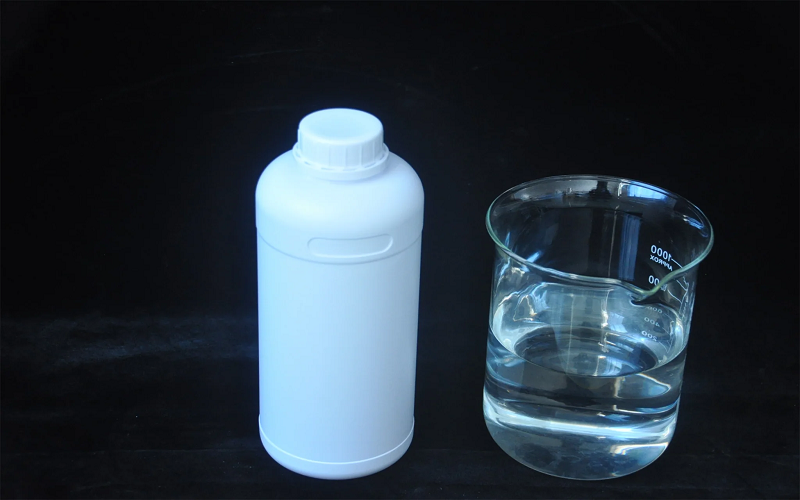
6. Foaming agent
There are three main types of plastic blowing agent:
(1) nitrogen, carbon dioxide, and air, directly pressed into the plastic melt to make foam;
(2) volatile liquids such as butane, pentane, petroleum ether, difluorodichloromethane, etc., in the temperature that is volatile expansion, and make the plastic body foam.
Common polystyrene foam belongs to this type.
(3) decomposition of chemical blowing agent, this kind of blowing agent is generally solid powder.
They decompose when heated to release gas (usually nitrogen or carbon dioxide), and the plastic to produce a cellular structure, and reduce weight.
This kind of foaming agent is mostly organic azo compounds, such as azobisformamide, azobisisobutylene (AIBN for short).
The main plastics for foaming are: ABS, PS, PVC, PU, EVA, PE, PP and so on.
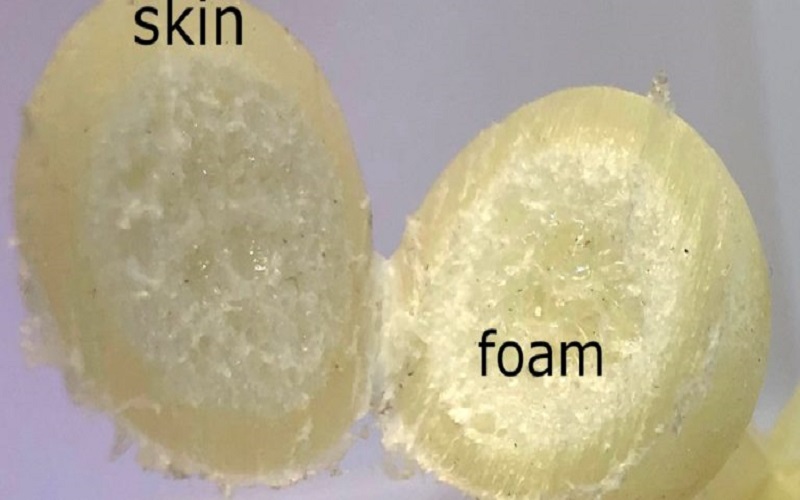
7.Nucleating Agents
Nucleating agents, as a type of functional additive, primarily modify the crystallization behavior of resins.
They accelerate the crystallization rate, increase the density of crystallization, and promote finer crystal grain size.
This leads to shorter molding cycles, enhanced product transparency, surface gloss, tensile strength, impact resistance, and other physical and mechanical properties.
Nucleating agents are suitable for use in partially crystalline plastics such as polyethylene and polypropylene.
8.Colorants
Colorants are chemicals insoluble in ordinary solvents, requiring mechanical methods to evenly disperse pigments in plastics for ideal coloring performance.
Inorganic pigments have excellent thermal and light stability and are cost-effective, but they offer weaker coloring power and have a higher relative density.
Organic pigments, known for their high coloring strength, bright colors, and complete color spectrum, have a lower relative density, but their heat resistance, weather resistance, and opacity are not as good as inorganic pigments. Colorants mainly include masterbatches and optical brighteners.
9.Antimicrobials
Antimicrobials are chemical substances that can keep the growth or reproduction of certain microorganisms (bacteria, fungi, yeasts and viruses, etc.) below the necessary level for a certain period of time.
The antimicrobial effects of antimicrobial agents are generally categorized into bactericidal and bacteriostatic effects.
The concentration and duration of action of an antimicrobial agent have a great influence on the antimicrobial effect.
Silver, copper, mercury and other metal ions, strong oxidizing agents mainly play a bactericidal role, while organic antimicrobial agents mainly show bacteriostatic effect.
The same antimicrobial agent, low concentration often shows bacteriostatic, high concentration is bactericidal.
10.Flame retardant
The additives that slow down the burning performance of plastics are called flame retardants, and most of the plastics containing flame retardants are self-extinguishing or have the effect of slowing down the burning rate.
The principle of flame retardant used in plastics can be roughly divided into three kinds:
(1) Reactivetype flame retardant can react with oxygen to form an inert gas, shrouded in the burning material around, reducing the oxygen content of the burning material, in order to achieve the purpose of terminating combustion.
Where the combustion can produce CO, CO2, NH3 and halogen compounds, such as PVC, PU foam, polyester or epoxy resin are selected for this method.
(2) Non-reactive type of flame retardant is containing halogen, phosphorus, nitrogen or boron compounds.
When combustion occurs, it can decompose a kind of inert material, phi cover in the surface of the plastic combustion material, forming a layer of obstacles to isolate the outside world of oxygen, to achieve the purpose of flame retardant.
(3)Water-containing oxides such as alumina flame retardant encountered when burning, can release water, absorb the heat of the combustion process.
So that the temperature around the burning material to inhibit the spread of flame, to prevent the formation of smoke.
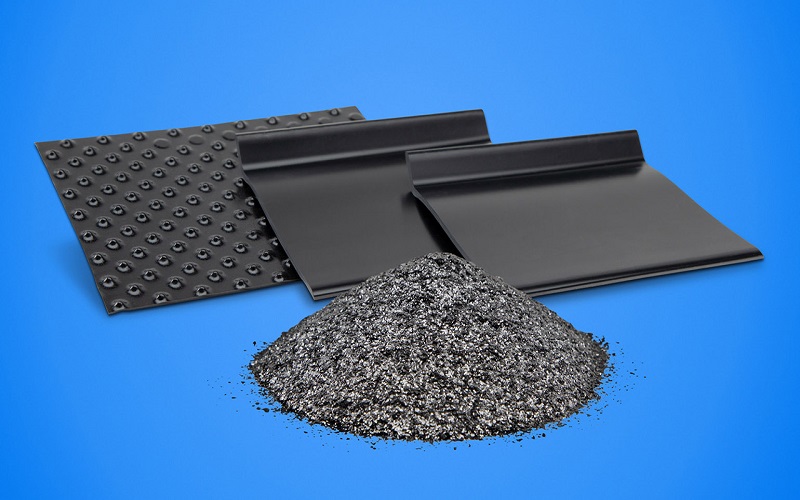
11. Antistatic agents
The main function of the antistatic agent is to give the plastic to produce electrical conductivity, in order to avoid the accumulation of static electricity caused by friction.
Commonly used antistatic agents are Quaternary ammonium salt (Quaternaryammoniumsalt), ethylene oxide amine, fatty acid esters and sulfonated wax (Sulfonated wax) and so on.
Additives | Functions | Applications |
Plasticizer | Increases the plasticity and flexibility of plastics and reduces brittleness | PVC soft products |
Heat Stabilizer | Delays or stops the degradation of plastics due to heat, light, or oxidation, including cracking, cross-linking, and chain scission, thus extending the lifespan of plastic products. | PVC products |
Flame Retardant | Reduces the flammability of plastics | engineering plastic products |
Processing Modifier | Improves the plasticity of rigid PVC, enhances the rheological properties of thermoplastic melts, and increases the impact resistance of hard polymer products | PVC rigid products |
Antioxidant | Inhibits the thermal oxidative degradation of polymer resins | polymer resins |
Lubricant | Reduces friction between polymer materials and the surfaces of processing machinery, as well as between polymer molecules themselves, improving processing flow | Various plastics |
Blowing Agent | A substance in resin and rubber formulations that promotes the release of gases, used to reduce product costs and decrease weight | foamed plastics |
How to choose additives for plastic modification?
Before processing each type of plastic, once the polymer is selected, the next consideration is the choice of additives and their quantities.
The correct selection of plastic additives directly affects the processing, performance, and lifespan of the product.
Selection by Purpose
To Improve Processability: Lubricants, release agents, stabilizers, plasticizers, PVC stabilizers.
To Enhance Mechanical Properties: Plasticizers, toughening agents, impact modifiers.
To Enhance Optical Properties: Nucleating agents, optical brighteners.
To Improve Aging Properties: Antioxidants, PVC stabilizers, UV absorbers, biocides.
To Improve Surface Properties: Antistatic agents, anti-blocking agents, anti-fog agents.
To Reduce Costs: Diluents, fillers.
To Improve Other Properties: Blowing agents, combustion aids, chemical crosslinking agents, coupling agents, etc.
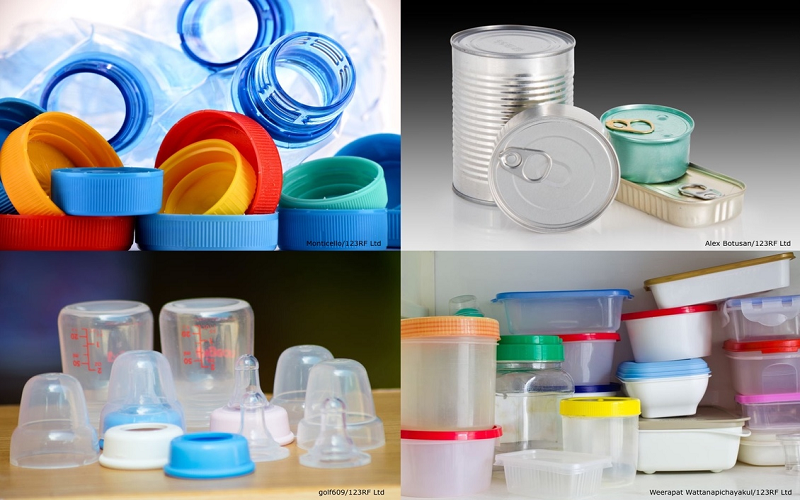
Compatibility with Polymers
Compatibility refers to the ability of additives to mix uniformly with the polymer without phase separation or precipitation.
Additives must remain stable in the product over time to be effective, so those with good compatibility with the polymer should be chosen.
However, each additive has a specific compatibility range with a given polymer; exceeding this range can lead to precipitation of the additive.
Adaptability to Processing Conditions
If polymer processing requires high temperatures for extended periods, additives that can withstand these conditions without decomposing or volatilizing should be chosen.
For example, in the processing of polypropylene, which requires higher temperatures, stabilizers that do not decompose or volatilize at these temperatures should be used, as well as colorants that do not decompose or fade at high temperatures.
Different processing methods for the same polymer may require different additives.
Quantity of Additives
Some additives have an optimal quantity range. For instance, with conductive agents, only enough to form an electrical pathway is needed; adding more is ineffective.
Similarly, for coupling agents, only enough to coat the surface is required; any more is redundant.
Likewise, with antistatic agents, only enough to form a discharge layer on the product surface is necessary.
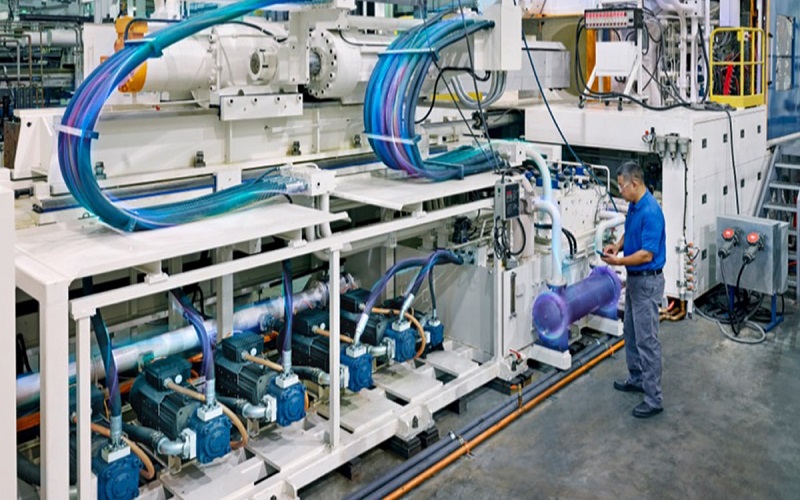
Development Trend Of Plastic Additives In China
The plastic additives industry in China is currently facing the most stringent environmental restrictions in history.
Against the backdrop of global advocacy for green and environmental protection, eco-friendly and efficient plastic additives are the main development trend of China’s plastic additives industry.
Leading plastic additive manufacturers are committed to promoting product structural adjustments and upgrades.
They are accelerating the development and application of green, energy-saving, and efficient production processes and technologies, driving technological innovation and high-quality development in China’s plastic additives industry.
Jike Chemical, as one of the most significant enterprises in China’s plastic additives sector, is also increasing its investment in research and development and product upgrades.
Chinese plastic additive manufacturing enterprises will focus on optimizing product structure, moving towards diversified product development, improving product quality, and developing customized products based on specific customer requirements.
Gradually, they aim to gain a competitive edge in the global plastic additives industry.
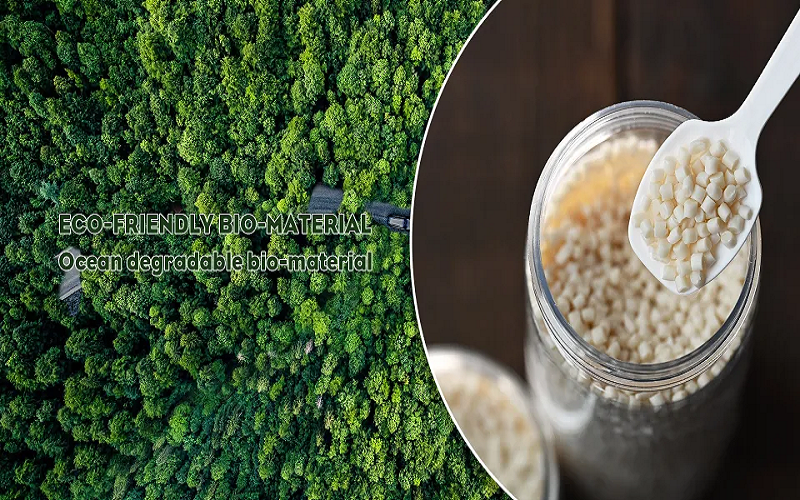
Conclusion
In conclusion, plastic additives play a pivotal role in the plastic manufacturing industry, significantly enhancing the properties, processability, and performance of plastic products.
They not only improve the durability and functionality of plastics but also contribute to cost-effectiveness and sustainability.