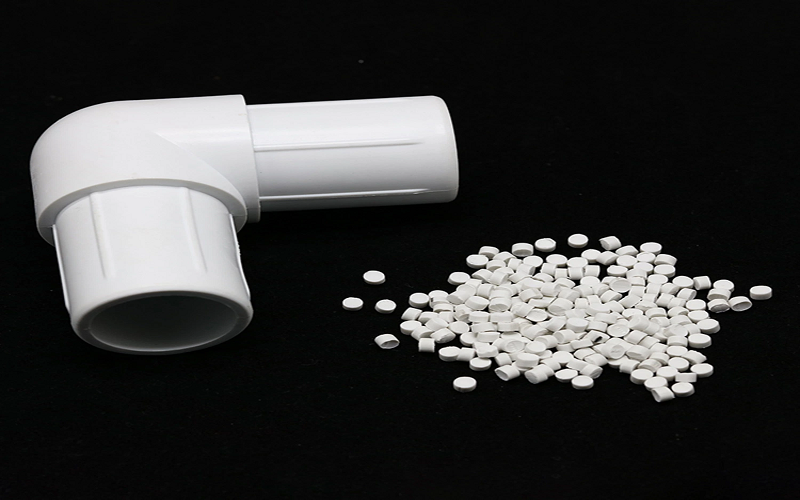
Share :
Share :
Plastic is one of the most abundant raw materials in manufacturing, and the fact that there are very many variations marks it the ideal go-to raw material when it comes to making all kinds of items. When it comes to molding, the most important part is plastic mould design. There are considerations that the manufacturer has to pay attention to for the process to be seamless.
We are going to look at some of these plastic part design considerations and how manufacturers can ensure the products they produce are well-engineered for functionality with as minimal defects as possible. If you are curious about the molding process and want to get plastic injection molding service from professional mould manufacturer, then you are in the right place.
Manufacturing is a complex process that has to follow certain protocols, and plastic part designs are one area of injection mold making technology that has to be taken seriously. The following are the main considerations one has to keep in mind before kick-starting the process.
There are hundreds of plastic raw materials, and each has its own attributes that make them ideal for certain processes. Injection molding manufacturers have to select the right resins that are optimally configured for the exact process they want to use them for. Selecting the right raw materials is governed by the following qualities.
The radius of the part design determines the thickness, which in turn has a lot to do with the strength of the end product. The radius of the part design has to be balanced in accordance with the curvature in order to balance out the stress. Some parts have to be slightly thicker than others. For example, corners tend to be a little thinner than straight parts, and this is for the sole purpose of eliminating chances of breakages due to high stress.
Wall thickness has to be consistent and well thought out. You don’t simply wake up and decide to come up with a random number for it. A well-balanced wall thickness will stop a lot of defects that may arise due to mechanical stress. Melted plastic tends to flow to the areas of less resistance; if the thickness is inconsistent, then the flow will tend to move towards the thick areas first, making them more thicker and causing a very bad imbalance on the entire structure.
Thicker areas also tend to undergo cooling at a much slower rate than their opposite counterparts. Uneven cooling is one of the leading causes of defects for molded products, and avoiding such a scenario is the best thing you can try in order to get functional end products.
In injection molding processes, the gate is an important part that determines a lot of things—for instance, the rate of flow. When molten plastic is allowed into the molding crate, it has to go through a gate that controls the speed. Move too fast, and the cauldron will fill up too fast, move too slow, and the cooling may begin before the inflow is over. The gate helps in distributing the molten materials around for uniformity, and this has an overall impact on the quality and viability of the final product.
This is the amount of taper found on the walls of the plastic part being designed. They are necessary for the ejection of the mold to take place. Without a draft, the ejection process would inflict serious damage to the molded part. On most occasions, the draft angles are usually set between 1-2 degrees, but they can go higher or lower depending on the nature of the molding process and the part being created.
Not all walls are made thick, there are items that require thin and regular walls, and this presents a new problem, the strength to counter the effects of that. The solution comes in the form of ribs that have to be added to the part design to reinforce the strength of the walls. The thickness of the ribs usually varies between 50% – 70% of the overall thickness of the walls in question. This is necessary to avoid the creation of sink marks. There are times where the core material will have to be gorged out to reduce the chances of any defect taking root in the final product.
Where heating and cooling are involved, mold shrinkage is part of the process. The trick lies in the ability to control and minimize the shrinkage as it can cause some serious defects later on in the product. The shrinkage in some processes can be up to 20% of the total volume, and this is more prevalent in raw materials that are crystalline-based. Amorphous raw materials, on the other hand, have a lower shrinkage rate among all the types of plastics that can be used for molding.
To counter mold shrinkage, you can try the following quick tips.
These are additional features and parts that are added to the molded part to make it more efficient. They include holes, shoulders, undercuts, and others that help reduce the chances of damage. Processes like ejection, for instance, use a lot of force that can damage the product if there are no special features to make the process more seamless. The item being pulled forcefully while another part is still stuck to the mold crate will automatically destroy it.
When designing mold parts, manufacturers must provide generous tolerances that will be able to give the end product the needed strength to deal with extreme conditions on either side of the spectrum. Tolerance variation is reliant on some variables that range from materials, tool design, and process control. All of these have to come into a seamless balance that gives the end product the strength and ability to tolerate anything that’s thrown at it up to a certain limit.
Failure to consider this will only lead to products that may look fine on the outside but have structural integrity issues. This is how you end up with mass recalls of items due to defects appearing in all the products that underwent the same manufacturing process.
You must be wondering why all these considerations have to be adhered to in the process of plastic part design. There are a number of reasons why this is important, and they include the following.
Plastic part design is a step that cannot be skipped in the production line. Every serious injection molding manufacturer has to spend a lot of time in the design part to get a clear image of what they want to see at the end of the assembly line. If you are planning to get into the molding industry and you are clueless about where to begin, check out our website to learn more and have all your concerns addressed by our team of experts.
Please contact us using the form below or emailing (harry@fowmould.com)