As environmental sustainability and material performance increasingly gain attention, PPCO (Polypropylene Copolymer), with its recyclability and superior performance, has become a hotbed for research and innovation.
As the primary process,PPCO injection molding technology is seeing its vast market potential being progressively tapped.
In the following content, we will delve into the physical and chemical properties of PPCO, analyze its behavior in the injection molding process.
What Is PPCO?
PPCO, also known as Polypropylene Copolymer, is a type of thermoplastic polymer.
Its fundamental molecular structure consists of repeating unit sequences of ethylene and propylene, combining the characteristics of both polyethylene and polypropylene.
It maintains the high-temperature and high-pressure resistance of polypropylene while inheriting the low-temperature tolerance of polyethylene material.
This enhances the low-temperature performance of polypropylene, which would otherwise be prone to brittleness.
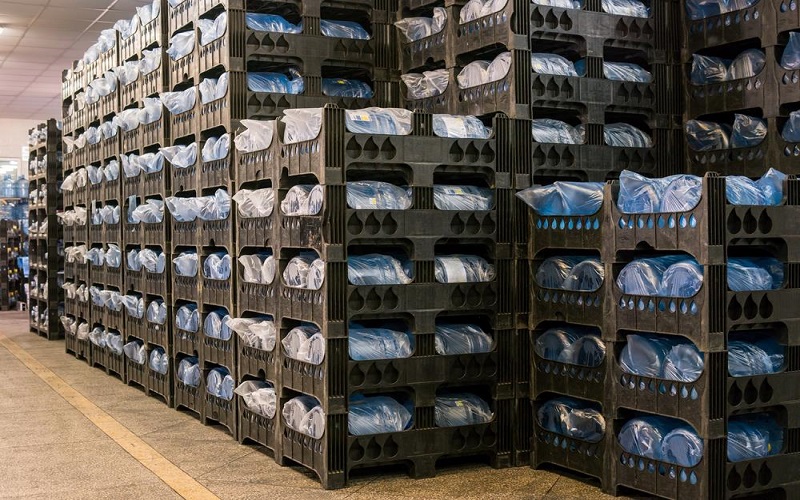
Properties of PPCO Plastic
PPCO, or Polypropylene Copolymer, is created by copolymerizing a small amount of ethylene with polypropylene (PP).
This copolymerization process alters the molecular structure of the polymer by introducing ethylene units, thereby enhancing the material’s flexibility and impact strength.
The introduction of ethylene units disrupts the regularity of the polypropylene chains, leading to a lower degree of crystallinity in PPCO.
Compared to pure polypropylene, which significantly impacts its physical properties.
High Strength-to-Weight Ratio
PPCO typically has a density ranging between 0.89 to 0.91 g/cm3.
This attribute allows PPCO to provide sufficient structural strength and durability while maintaining a lower weight, making it an ideal choice for applications where lightweight yet strong materials are desired.
Excellent Chemical Resistance
PPCO exhibits outstanding resistance to a wide variety of chemical substances, including acids, bases, and solvents.
This quality makes it an ideal choice for containers and equipment used in chemical processing and storage.
Good Low-Temperature Resistance
Compared to pure polypropylene, PPCO maintains its physical properties better at low temperatures, showing enhanced freeze resistance and toughness.
This reduces the risk of becoming brittle in cold environments.
Strong Impact Resistance
Thanks to the copolymerization of ethylene units, PPCO generally has a higher impact strength than traditional PP, especially in low-temperature conditions.
This makes it particularly valuable in applications where resistance to impact or stress is essential.
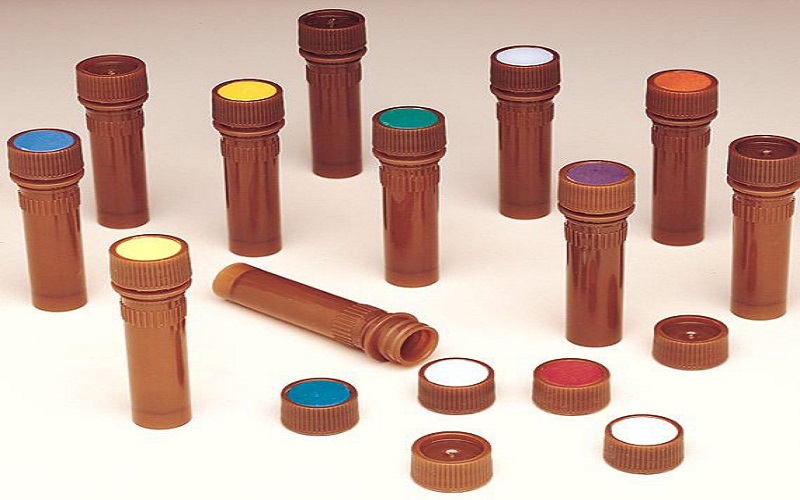
Conditions for PPCO Injection Molding
Creating a high-quality PPCO plastic product is not an overnight achievement; it is the result of a complex PPCO injection molding process.
Before starting the injection moulding, PPCO materials typically require proper preheating, usually within a temperature range of 80°C to 110°C for about 2 to 4 hours.
The purpose of this is to remove any residual moisture, thereby preventing defects during the molding process.
In actual production, precise control of injection molding conditions is crucial.
Below are some key parameters for PPCO injection molding:
PPCO Injection Molding Parameters | |||
Melt Temperature | 200-300℃ | Mold Temperature | 40-80℃ |
Injection Pressure | 500-1500 Bar | Holding Pressure | 50-65% of injection pressure |
Back Pressure | 50-150 Bar | Injection Speed | fast |
It should be noted that the rheological properties of PPCO plastic during the injection molding process have a decisive impact on the quality of the final product.
Rheological properties refer to the flow behavior of the material under heat and pressure.
PPCO with a high flow rate can easily fill injection molds, but it may lead to overpressure and flash, while a low flow rate might result in insufficient filling.
The viscosity of PPCO is influenced by the injection molding temperature and pressure; too high viscosity can make filling difficult, whereas too low viscosity may lead to poor control and quality issues.
Additionally, the variation in viscosity of PPCO at different shear rates is crucial for the selection of injection speed. Inappropriate injection speeds can cause uneven material distribution, leading to flow lines and bubbles.
Furthermore, cooling and shrinkage behavior determine the dimensional stability and shrinkage rate of the product.
Uneven cooling can lead to warping or internal stress.
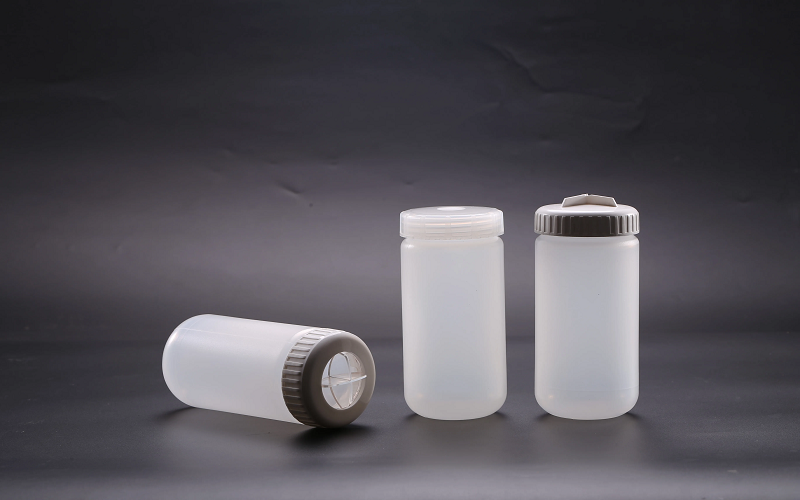
Characteristics of Injection Molded PPCO Products
Leveraging the exceptional properties of the material and complex plastic injection molding processes, injection molded PPCO products have acquired a range of characteristics that enable their widespread use across various industry sectors.
Good Mechanical Strength
PPCO plastic products have high strength and rigidity, making them suitable for applications that require bearing heavy loads or mechanical stress.
Customization Options
The physical and chemical properties of PPCO can be adjusted by adding various additives, such as flame retardants, plasticizers, and colors, to meet the product needs of different businesses.
Dimensional Stability
In environments with temperature and humidity fluctuations, PPCO molding plastic products exhibit good dimensional stability.
Recyclability
PPCO is a thermoplastic polymer, meaning it can be melted and reformed. Consequently, PPCO injection molded products can be recycled, reducing their environmental impact.
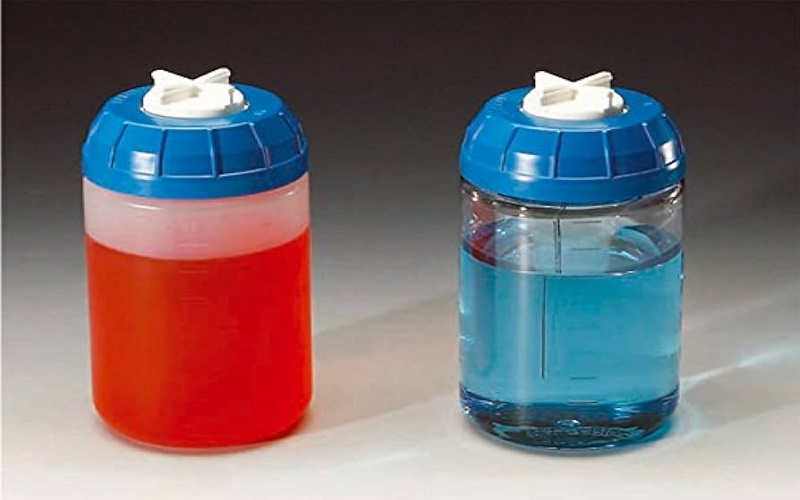
Diverse Applications of PPCO Molding
With its remarkable versatility, PPCO molding products are favored by plastic companies and have found widespread applications across multiple industry sectors.
Medical Industry
In the medical field, PPCO is widely used to manufacture test tubes, collection bottles, and specimen containers, thanks to its chemical stability and high-temperature resistance.
The high strength and impact resistance of injection molded PPCO products also make them the material of choice for certain components of surgical instruments, such as handles and casings.
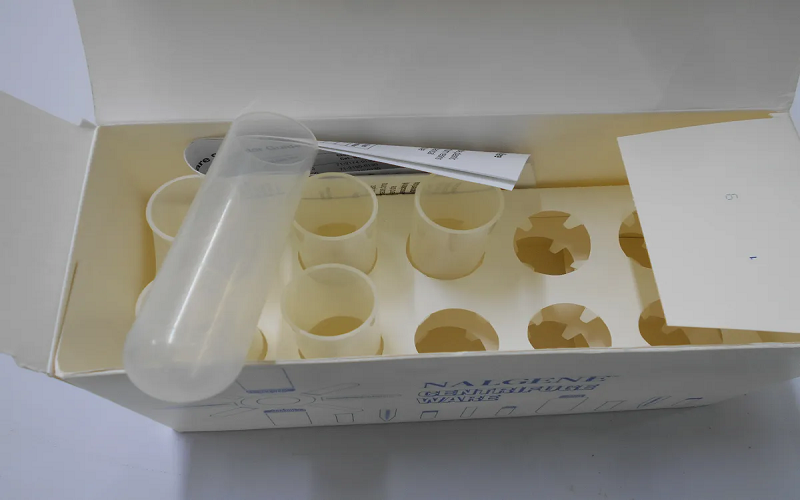
Automotive Industry
Due to the need for car components like bumpers and protective panels to withstand high-impact forces, PPCO plastic is commonly used to make these automotive protective components.
Additionally, its wear resistance and heat tolerance make it a suitable material for automotive interior parts such as dashboards, door panels, and air conditioning vents.
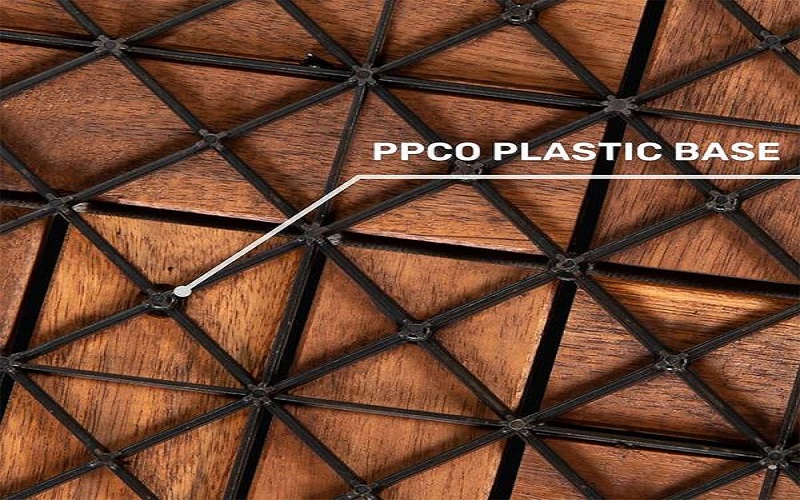
Packaging Industry
Food storage containers and beverage bottles have very high standards for the materials used in their production.
The non-toxic and odor-resistant properties of PPCO injection molded products make them safe for direct contact with food, making them ideal for containers and bottles.
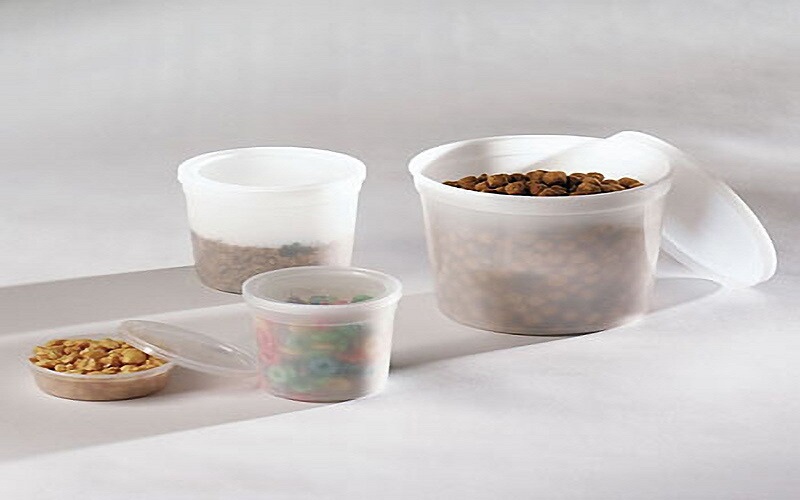
FOWMOULD——Custom PPCO Injection Molding Service
As a leading Chinese injection molding company, FOWMOULD is committed to providing clients with one-stop injection molding services.
Utilizing professional expertise and advanced equipment, we tailor-make high-quality, high-precision PPCO injection molded products for our clients.
FOWMOULD is equipped with the latest injection molding machines and auxiliary equipment, ensuring precision and efficiency in the PPCO molding process.
These machines are capable of handling a variety of complex design requirements, ensuring consistency and quality in the products.
Whether for small-batch production or large-scale projects, FOWMOULD can accommodate customized production needs.
Our professional design team and manufacturing staff work collaboratively to oversee the process from product design to final production, ensuring every step meets the specific requirements of our clients.
When you choose FOWMOULD, you get a reliable, efficient and cost-effective solution for PPCO injection molding.
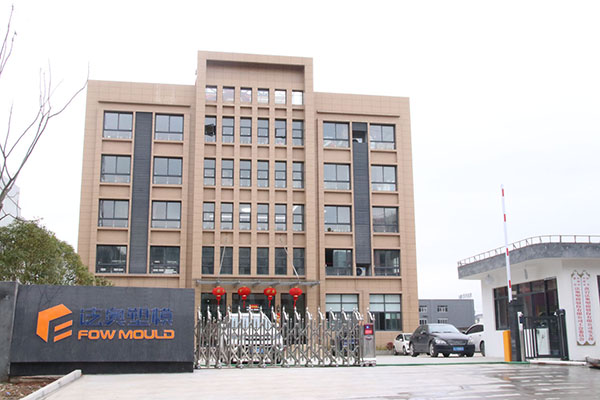