Thermoplastic Elastomers (TPE), also known as thermoplastic rubbers (TPR), are copolymers or blends of compounds that deliver the processing properties of thermoplastics and service properties of elastomers. TPEs exhibit the durable characteristic features of thermoplastics above their melt temperatures and the rubber-like properties of elastomers at ambient temperatures, allowing them to be processed into flexible plastics that can be remolded or reshaped.
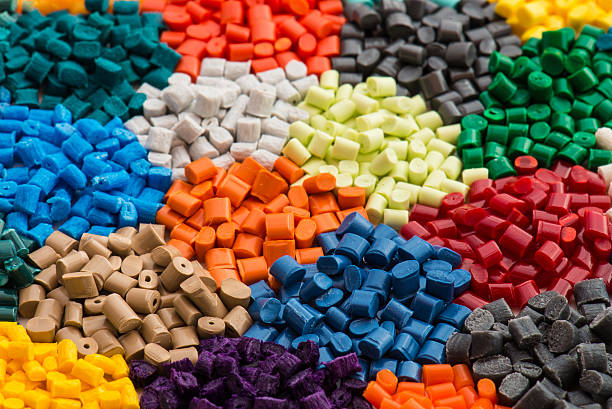
During the TPE molding process, TPEs are not subjected to cross-linking, making the fabrication reversible. TPEs demonstrate flexibility that provides excellent value in today’s market as they significantly replace the use of rubbers in several applications.
TPEs’ cost-effectiveness, versatility, and design flexibility enable them to be used in various end-user markets such as consumer goods, automobiles, electronics, and many more. This comprehensive guide will help you with all you need to know about TPEs and how their unique properties are harnessed.
1. What is TPE and 6 Types of TPE
Thermoplastic elastomers differ from thermoset elastomers in their chemical bond and properties. thermoset elastomers are crosslinked, giving them a more permanent bond. Thermoplastic elastomers (TPEs) are flexible plastics that melt when heated and harden when cooled without changing the chemical structure.
One major reason for TPE’s acceptance in different parts of the world is that it can easily be recycled. Like every other thermoplastic, TPE can be molded and remolded into a different product. Thermoplastic elastomers are molded into different shapes at a high temperature using either TPE injection molding, blow molding, extrusion, or rotational molding methods.
There are 6 primary categories of TPE; they are Thermoplastic Vulcanizates (TPV), Thermoplastic Urethanes (TPU), Thermoplastic Olefins (TPO), Styrenic Block Copolymers (SBC), Copolyester Elastomer (COPE), and Polyether Block Amide (PEBA). Each differs in chemical structure and composition.
1.1 Definition of TPE
TPE is a short form for ‘thermoplastic elastomer.’ Thermoplastic elastomers are synthetic plastics that belong to the thermoplastic family. This explains why they have the same chemical properties as thermoplastics. They change to a molten state at a high temperature and maintain a solid state at a lower temperature.
Thermoplastic elastomers (TPEs) were commercially introduced in the 1960s. This recyclable polymeric material combines the high elasticity of elastomers at room temperature and the excellent processability of thermoplastics at high temperatures.
TPE products typically have high elasticity, longevity, and resistivity to oil which are common with traditional rubbers and the wide range of processing methods associated with ordinary plastics.
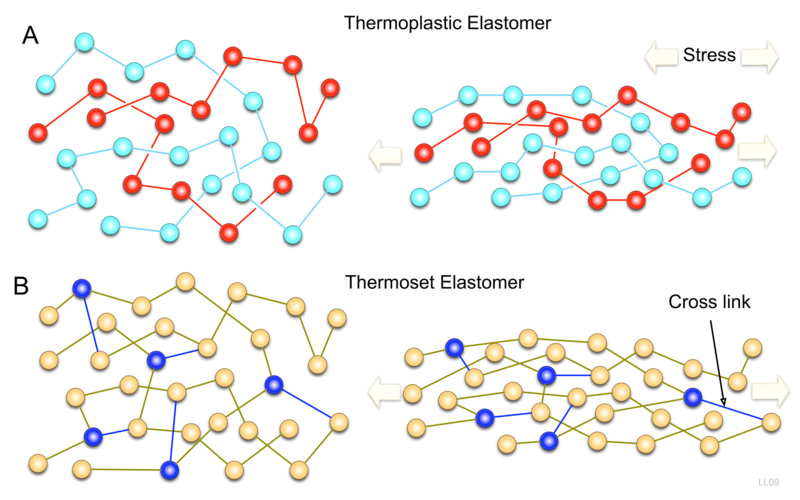
1.2 Six Primary Categories of TPE
Based on chemical composition and structure, TPEs are classed into:
- Thermoplastic Vulcanizates (TPV or TPE-v): TPVs are elastic thermoplastics formed from the mixture of polypropylene (PP) and synthetic rubbers (EPDM). They have good dimensional stability and are now increasingly used for seals, under-hood applications, bumpers, and other applications where a heat resistance of up to 120°C is required.
- Thermoplastic Urethanes (TPU): TPUs are a mix of hard and soft regions based on polyester or polyurethane backbone linkages. They provide resistance to weather elements. Hence they are suited for outdoor applications which require abrasion and weather resistance, good tear strength, and flex fatigue resistance. Applications include footwear, ski boots, wires, cables, industrial belting, etc.
- Thermoplastic Olefins (TPO): TPOs are compounds of hard PP and soft non-crosslinked EPDM rubber. They can be slightly modified and cross-linked to enhance their heat resistance and compression properties. They are comparatively inexpensive to TPUs and are used in applications like automotive bumpers and dashboards.
- Styrenic Block Copolymers (SBC): Although SBCs are plastics, they behave like rubbers. This is because they are formed from two-phase block copolymers with hard styrene and soft elastomeric segments. The styrene ends provide thermoplastic properties, while butadiene mid-blocks supply elastomeric properties. They are the most versatile of TPEs.
- Copolyester Elastomer (COPE): COPEs are blocked linear copolymers with hard crystalline polyester and soft amorphous segments. The hard segment provides strength and high heat resistance (up to 140°C) to the structure, while the soft segment gives it aging resistance. Examples of applications include wires and cables, industrial hoses, and automotive applications.
- Polyether Block Amide (PEBA): PEBAs are newly developed alternating blocks of copolymer elastomers consisting of hard polyamide segments and soft elastomeric regions. They are used in aerospace components, cable jacketing, etc.
2. Properties of TPE Materials
When selecting TPE materials, it is important to understand their properties, advantages, and disadvantages. These can impact their moldability and affect the outcome of the finished product. TPE materials have good to excellent electrical insulation properties and are UV stable. The elastic soft phase also makes them flexible, with some tensile strength arising from strain-induced crystallization of their chain segments.
Now, let’s take a look at the advantages and disadvantages of TPE materials.
2.1 Advantages of TPE Materials
TPE materials have a wide range of advantages, particularly over conventional rubber, some of which include the following:
- Chemical Resistance: TPEs can withstand exposure to a wide range of acids, including strong acids like hydrochloric acid and sulfuric acid. Also, they are resistant to a range of bases, including strong bases like sodium hydroxide and potassium hydroxide. This makes them suitable for use in applications where they will be exposed to alkaline environments. In addition, they are not easily affected when exposed to different environmental factors and ultraviolet rays.
- Consistency between Batches: One advantage of using TPE (Thermoplastic Elastomer) molds is the consistency between batches. This means that the produced parts or products will have consistent quality, dimensions, and performance from one batch to the next. This consistency is due to the ability of TPE molds to maintain their shape and dimensions even after multiple uses and high-pressure injection molding processes.
- Stability and Durability: The excellent flexural fatigue, strong abrasion, aging resistance, high impact strength, and low compression property of TPEs give the needed material stability during and after the molding process.
- Easy Coloration: TPEs have a low permeability compared to other polymers. This property makes it easy to apply different finishes and colors to the surface of the TPE product. TPEs respond well to dyes and other coloring agents.
- Energy Efficiency: Thermoplastic elastomers typically do not require a lot of energy to manufacture. They involve simple processing methods with shorter fabrication times compared to other materials. Since cross-linking is avoided, the production cycles are faster. TPEs are therefore considered cost-effective for this reason.
- Recyclability: Thermoplastic elastomers are considered recyclable because they can be reused for other purposes by TPE molding or extruding. They can be ground and used as 3D printing filaments, filler materials, or melted down to create new products. They are also non-toxic to the environment.
- Cost-effective Molding Process: One advantage TPE has over other polymers like TPEs like silicone and natural rubber latex, is their lowered cost of molding. They are relatively cheaper to mold, from the start to producing the final product. Their simple molding process and short molding cycle help to lower the final cost of molding.
2.2 Disadvantages of TPE Materials
When compared to other materials, TPEs have some disadvantages including:
- Melting at Elevated Temperature: Despite their good temperature resistance, TPE products perform poorly at high temperatures. Increased temperatures (>150°C) can cause a decrease in the physical properties of TPEs. If heated to relatively elevated temperatures, TPEs melt and lose their rubbery properties restricting the scope of applications of TPE parts.
- Moving and Deforming under Sustained Stress: Thermoplastic elastomers tend to creep under pressure and temperature. This means that they tend to move and deform when influenced by stress for prolonged periods. The durability and resilience of TPEs under stress are worse than those of rubber due to viscous flow.
- Costly Tooling Process: Thermoplastic elastomers (TPEs) have higher material costs than conventional thermoset rubbers and plastics. This is a major disadvantage of the tooling process involved in making TPEs. Despite their higher price, however, they are cost-effective when it comes to small runs because they cure almost immediately.
3. TPE Mold Design and Making
TPE mold design is one of the steps to take in constructing your plastic products. There are certain things to consider when deciding on the mold to design. After designing the TPE mold, the next thing is to make it. If you have ever wondered how molds are designed and made, read on to discover the basics of this process.
3.1 TPE Mold Design Basics
- Gate Design: The gating system of the TPE mold plays a critical role in the quality and overall appearance of the finished product. The TPE molding gate’s measurements directly impact the product quality, including appearance, warping deformation, flow marks,weld lines, trapped gas, etc.
- Cooling System Design: A carefully designed cooling system can increase production capacity and reduce costs by shortening the molding cycle significantly. If designed improperly, the cooling system will cause an increase in the length of molding time while uneven cooling will lead to product deformation, warpage, and other unappealing features.
- Molding System Design: Note that when the molding system is designed in n unreasonable manner, it can impact the mold-making and injection molding cycles. It can even cause a deformed product appearance and poor product performance. Therefore, pay close attention to the core and cavity design of the molding system.
- Ejection System Design: An ejection system clears the crate for another injection. It determines the product’s health since it causes deformation and rupture if done inaccurately. There are different ejection systems, and you need to pay close attention to them to know your TPE product’s fit.
3.2 TPE Mold-Making Procedures
- Mold Engineering
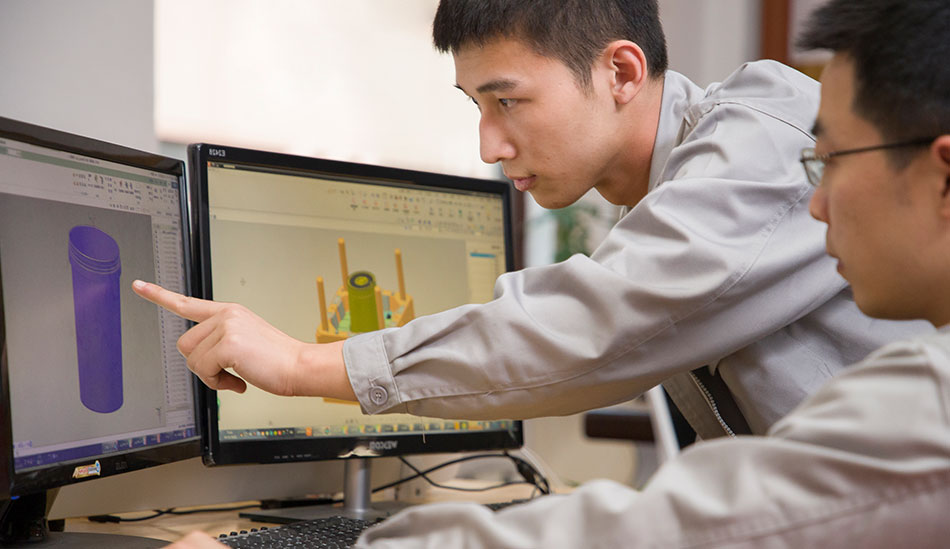
As a part of the mold-making process, mold engineering is carried out by mold design engineers using Computer-Aided Design (CAD) software such as SolidWorks and MoldFlow. This software has built-in tools that guide the TPE mold engineer to ensure high precision. The engineer can view the designs from different angles before prototyping.
- Mold Assembly: This is a crucial step in the mold-making process. All the TPE mold parts are joined together depending on the structural pattern. Assembling the parts is important for the TPE product to function properly.
4. TPE Injection Molding Technique
The TPE injection molding technique is one of the methods used in making TPE products. This technique allows the remolding or reshaping of TPE products. Once the product is solidified, it can be melted back into liquefied form and into a different design. The molding process can be reversed by melting and the plastics can be reused multiple times.
Although the TPE injection molding technique is a high tooling cost process, the advanced properties of the TPE pellets deliver short cycle times and allow parts to be produced at a rapid rate and high volume.
4.1 The Process of TPE Injection Molding
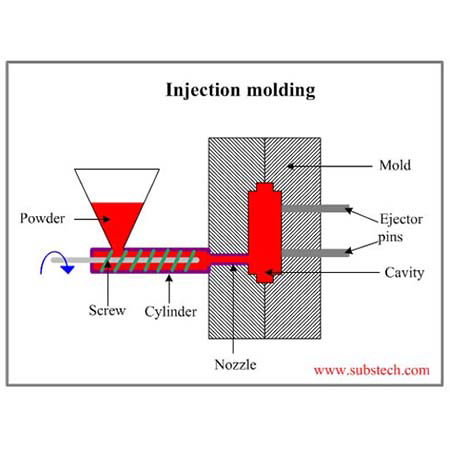
- Collect the pallets into the heated barrel: Feed the TPE pellets through the hopper into the spinning auger of the machine. The plastic pellets will then pass into a heated chamber or barrel where applied pressure and heat liquefy the TPE pellets.
- The heat from the barrel turns the material into a liquid resin: As heat and pressure are simultaneously applied to the pellets in the barrel, the melting process begins. The pellets are liquefied into viscous resin and move to a mold.
- Inject the liquid into a closed mold under high pressure: Once the pellets have melted in the barrel, the liquid resin is introduced into a cylinder-shaped injecting tool. This tool then injects the molten pellets into a mold under high pressure. The moving part of the mold is forced against the fixed part of a hydraulic ram, and the plastic enters the mold cavity through a gate and runner system. After the cavity is filled, the mold is held closed during the injection.
- Cool the molten polymer: The cooling cycle begins and continues until the plastic solidifies. While this happens, the auger screw and barrel return to their original position in preparation for the next cycle.
- Remove the finished part from the mold: The mold is forced open by the hydraulic ram when the molded part is completely cooled, and the molded TPE product is ejected from the mold for further processing. As soon as the mold closes and plastic is injected into the mold cavity, the next TPE injection molding cycle begins.
4.2 The Benefits of TPE Injection Molding
- Shorter molding cycles: TPE injection molding method is well known to guarantee improved product quality as well as production cycles. The TPE injection molding process utilizes low-energy and simple manufacturing procedures that do not involve cross-linking. This helps to reduce the time required for molding cycles. Compared with similar molding methods, it is evident that this method is very fast.
- Rapid production: Following the short fabrication cycles of TPE injection molding, there is a rapid production rate of TPE products. This method is very effective in facilitating swift production to ensure high TPE output. Thanks to injection molding, a high volume of diverse TPEs can be manufactured, thereby overcoming the demand and supply limitations.
5. TPE Overmolding Technique
TPE over-molding is a unique molding process in which one material (TPE) is formed in a mold followed by another rigid plastic material by heating with liquid silicone. There is no need to bond the two materials with adhesives or primers. The process seamlessly combines the primary and secondary materials into a component.
The TPE over-molding technique creates a soft product surface and increases the product’s functionality, thereby giving it more value. TPE over-molding helps in a wide range of applications providing better functionality, ergonomics, and feature enhancements such as shock absorption, noise reduction, water resistance, and durability.
5.1 The Process of TPE Overmolding
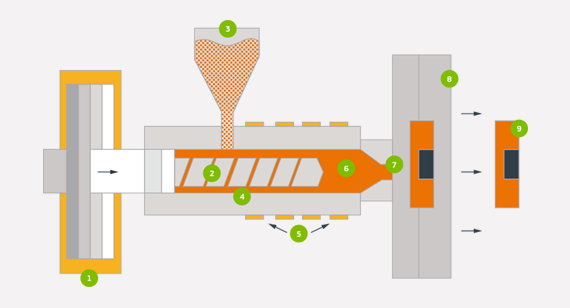
- Fix the first molded part onto the over-molding mold: The first thing to do is to secure the cavity tightly. After this, the first molded part is fixed onto the over-molding mold.
- Inject the TPE materials onto the hard parts: The soft TPE rubber is injection-molded on the hard rubber parts at predetermined temperatures and high pressure. The pressure and temperature used in this injection molding step is dependent on the hard rubber material. For TPEs overmolding PP material, the injection temperature is usually between 170°C-190°C while for overmolding ABS material, it is about 200°C-220°C. In the case of overmolding PA nylon, the injection temperature can be up to 240°C and slightly higher than the injection molding temperature of overmolding ABS for overmolding PC material.
- Cool the TPE materials: As soon as the injection is complete, the over-molded material is left to set and cool. It may take a while for the resins to bond cohesively and form a structural product.
- Remove the finished part: Now that the structure is well and fully bonded, the mood is opened and the ejector pins automatically push the finished part out of the mold slowly. Draft angles ensure smooth ejection of the finished part.
5.2 The Benefits of TPE Overmolding
- Comfort touch: When plastic components are overmolded, the finished product has a soft feel and comfortable handles. Also, it helps to create an aesthetically pleasing protective layer that helps the product survive in extreme conditions. This, in turn, increases the reliability and lifespan of the TPE product.
- Impact resistance: Overmolding means an extra protective layer for the TPE product. This layer provides the overmolded product with resistance to shock and abrasion. Overmolding offers insulating and encapsulation properties for electrical components, making these products durable and safe for consumers.
- Anti-slip performance: TPE materials generally have good slip resistance and elastic touch, enhancing the grip of the product. The covering provided by overmolding thermoplastic elastomers gives them extra slip resistance. They can be adjusted to appropriate physical properties and hardness range to meet desired grip levels. This anti-slip property enhanced by overmolding makes the TPE materials useful in different applications.
6. A Reliable TPE Molding Services Provider
FOW Mould in China has been a reliable provider of quality injection mold solutions for over 40 years. We have representatives in different parts of the world. Also, we have a wide range of products, such as plastic baby toy sets, buckets, home appliances, plastic molded chairs, plastic auto parts, and many more.
At FOW Mould, you can be assured of good quality at reasonable prices, technical efficiency, lifelong free repair, and prompt response delivery for any queries. FOW also maintains a close relationship with clientele to help with troubleshooting. Our company has a Quality Management System that is internationally certified with internal quality control processes and measures that monitor and check our daily TPE mold products.
Regarding TPE mold, FOW Mould is the best company to have as a supplier and business partner. With different mold-making techniques, including insertion molding, overmolding, and plastic injection molding, FOW is able to achieve an annual capability of 900 molds, 300 of which are bucket molds. Our mold-making and injection molding services have since expanded to other industries such as furniture, automobile, warehouse & storage, baby products, and home appliances. Our team of experienced engineers can help you achieve all-inclusive, cost-effective solutions with no compromise on quality, guiding you from the ideation phase with product sketches and drawings through the mold construction phase and the final production of your designs.
Products & Services We Offer:
- TPE molding and mold designs for bucket pails
- TPE molding for auto parts
- TPE molding for Toys & baby products
- TPE molding for home appliance products
Mold Designs We Offer:
- Unique TPE molding for plastic toys
- Quality and creative plastic chair mold designs
- Crate molds and storage boxes
- TPE injection molding service for solar panel parts
Conclusion
Thermoplastic elastomers have seen an increase in global use for several decades and this post is a comprehensive guide on how TPE injection molding and TPE overmolding work. Although they have some drawbacks, TPEs possess many desirable features that make them valuable in many contexts including automobiles, consumer products, medical equipment, home appliance, and so on. Many industries are still discovering innovative ways to use TPEs.
FOW Mould is a reliable provider of premium quality mold services across the globe. FOW Mould offers on-demand OEM and ODM services for all your production and prototyping needs, and our customer service team is available to guide customers on matters such as cost saving to minimize unnecessary burdens while still preserving the quality. You can also upload your designs for the professional help from our team. Check out our website today to learn more about TPE molding or to request a quote from us.