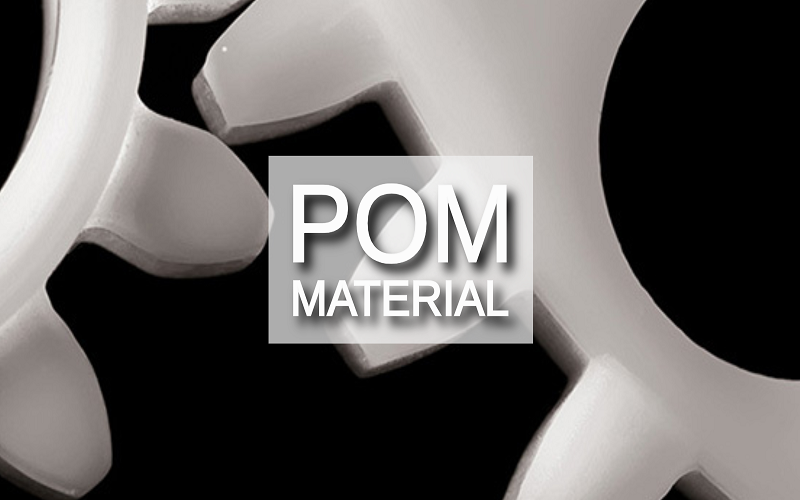
Share :
Share :
Plastic buckets are tiny to medium-sized portable circular containers used for transporting or storing a variety of goods in modest quantities. All plastic containers are made using either blow molding or plastic injection molding service equipment.
A lot of buckets are constructed of high-density polyethylene. HDPE is a long-lasting, non-reactive thermoplastic that can withstand impact and harsh weather conditions either in transit or storage.
Let’s walk through the plastic manufacturing process, detailing each minor process that you might need to know. Read on to find out more.
Take the following criteria into consideration while selecting a production process for plastic bucket mould:
Popular molding processes for plastic buckets and other containers include;
Plastic combs, mugs, buckets, and containers are considered home necessities. According to the 2001 census, the North-Eastern region of India has a population of 3.90 crore people. Given that the home consists of five individuals, the total number of households in the region is 78,00,000.
Again, assuming that there is a replacement need for these products by at least 30% of the total number of homes each year, the demand for these items on this basis equals 23,40,000 numbers. This could be in addition to the annual increase in demand for these products by at least 15% of the total number of households, which stands at 11,70,000.
All plastic containers are made using either blow molding or injection molding equipment. A lot of buckets are constructed of high-density polyethylene. HDPE is a long-lasting, non-reactive thermoplastic that can withstand impact and harsh weather conditions either in transit or storage.
In blow injection molding, raw HDPE polymer, known as stock at the start of the molding process, is fed into a hopper. The stock is then directed by the hopper into a conveyor tube, where a huge screw pushes it toward a mold. The mix of contact & pressure warms the stock as the screw spins.
This heat treatment, along with the additional heat produced by heating elements installed along the channel, warms the stocks to the threshold of liquefaction. The liquid stock now fills a mold cavity and develops form.
After that, pressurized air is pushed into the cavity, hollowing out the center of the plastic mold. The item is cooled and hardened when the molding process is completed. It is then expelled from the mold, cleaned of any defects (if any), and either dispatched or moved for further processing.
Plastic buckets, like cups and containers, can also be produced on a semi-automatic extrusion blow molding machine. The key process phases are as follows:
The following are the major phases in the production of plastic combs:
The following are the key pieces of equipment required by the unit for the production of mugs, buckets, and containers:
The following are the major pieces of equipment needed to make plastic combs:
Plastic bucket molding should preferably include the use of mold making technology in their manufacturing. Bucket manufacturing is critical since these items are widely utilized in-home activities such as water storage and other packaging procedures.
The above procedure explains how to create your own plastic buckets; all you need is a molding machine (size depends on your production demands) from a reputable plastic molding OEM, polymer/plastic, and enough time and patience to study and go through the manufacturing process outlined above.
Please contact us using the form below or emailing (harry@fowmould.com)