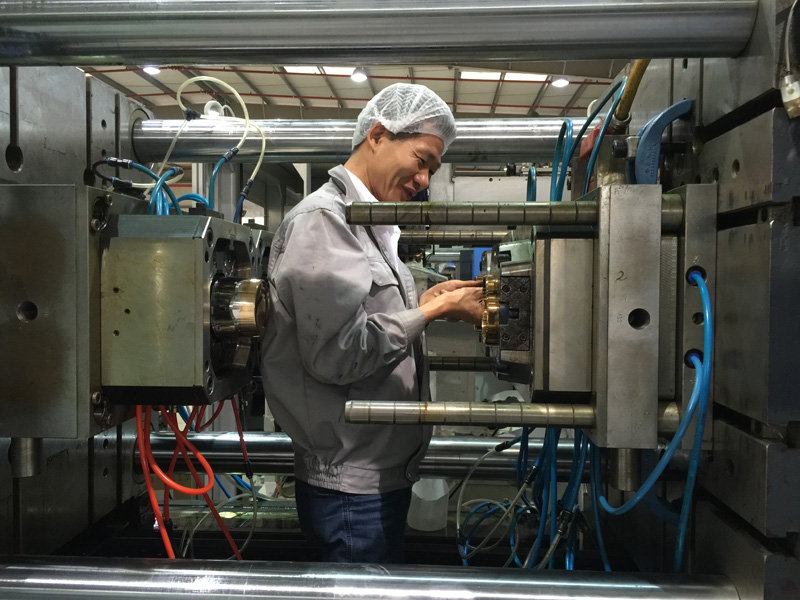
Share :
Share :
For years now, injection molding has been part and parcel of manufacturing, used for so many production processes for day-to-day items, especially those made of plastic. However, not many people understand how this works, and the many parts that have to work together to ensure the product that comes out at the end of it are up to standards. Of the many parts that make up an injection molding design, the most important is the mold runner.
We are going to look in detail at how runners are designed, what they do in the whole setup. The types of runners in injection molding that exist, how it affects the various plastic parts, and some consideration tips that you should pay attention to when selecting one.
Source: Pinterest
A runner is a special channel that is cut into the mold to allow for the easy injection of the plastic material from the nozzle to the empty cavity. It plays an important role in controlling how things work once the injection has taken place. Every slight change in pressure or the temperature of both the material and the mold will affect the final output. When all these factors combine, they tend to increase the internal stress in the product being made, and that may eventually undermine the structural integrity.
To avoid this, the runner is used as it has a significant influence on part formation. It has a direct impact on the pressure, melt temperature, warping, shrinkage, packing, and residual stresses. They can be cut into a variety of shapes and sizes depending on the production needs and the size of the item in question. The bottom line is that there will not be much efficiency in the injection molding process without runners being involved.
Source: Pinterest
A runner is basically the passageway through which molten material passes from the nozzle to the mold via the gate. The principle design layout for this important part has everything to do with managing pressure and heat, keeping the two at maximum levels to allow for the molten material to stay hot as long as it can for uniformity. It is made up of sectional shapes and branches that combine to ensure there’s nothing that impedes the smooth transition of materials from one part to the next.
Some common shapes that runners are designed in include circular, which provides a minimum area that switches sides once production begins for both plates to be aligned. Other shapes that are used range from rectangle, trapezoid, U-shape, and semicircle.
Source: Pinterest
There are basically two types of runners in injection molding that are used widely in mold making technology. We are going to quickly look at each and how they function to better understand how important runner systems are important.
A hot runner system injection molding is an assembly of heated parts that are used in the plastic injection molding process. They inject the molten material directly into the empty cavities. A hot runner system comes with a manifold and several nozzles. The function of the manifold is the distribution of the molten plastic through the various injection nozzles to ensure equal spread for equal cooling.
It has shorter cycle times with no runner controlling the cooling time. This makes it ideal for mass production.
Starting a hot runner design mold is easier, and since there are no runners that need to be removed, the cycle occurrence is much faster.
Products made through injection molding processes that use a hot runner system tend to have fewer sink marks and other defects like under-filled parts. There’s no heat loss.
The flexibility of the hot runner injection molding is unlimited, and this allows the machine engineer to locate the gare at any point along the entire part.
Hot runners have a balanced melt flow due to the reliable, insulated runner mold.
Cold runner systems are composed of an unheated injection channel that is used to convey molten materials into the empty cavity after being released from the nozzle. Cold runner systems have bigger channels that support a greater flow with each cycle, and this makes it even a better option for those that want to produce a lot of products at once.
They are less expensive to run, and this makes them ideal for mass production.
They are also much larger than hot runners, which again gives them the ideal capacity for injection molding manufacturers who deal with huge volumes.
They are easy to maintain, and this makes them a very cost-effective option, especially for new companies that are just starting out with injection molding.
Modifications like colors can be made quickly without affecting any other part of the item being made.
It also accommodates all types of polymers as far as molding materials are concerned.
It has faster cycle times, especially in situations where the manufacturing process has been automated.
Source: Pinterest
The runner being an important channel that allows molten materials into the cavity, it goes without saying that its design impacts the final product that is made. The first design factor that will determine the plastic parts of the product is the size of the hot runner. If you are looking to create bigger parts, then you will have to use a bigger runner and vice versa. You also have to decide whether you will go with a hot runner or a cold runner.
Each serves similar functions, but they are designed to handle different aspects of the manufacturing process. Other factors worth considering include the length and the cost. Any slight mistake added to the runner design will be reflected on the products that are made using it until changes are deliberately made to rectify the defect.
Source: Pinterest
As is the case with any machine, there are some factors you have to pay attention to designing a runner. These tips will help you address all the possible complications and defects that may derail injection molding. These factors include the following.
Material Volume: The volume of what you plan to manufacture plays a critical role in determining the mold design and choice of the runner. If mass production is your ultimate aim, then consider a cold runner, for instance.
Cycle Time: The speed of manufacturing should also help point you in the right direction. Most runners are decently fast, so that is never an issue. But you may run into trouble if you attempt to increase the volume of production with the same type of runners.
Maximum Injection Pressure: The injection pressure, in combination with the ability of the crucible to hold heat, plays an important role in ensuring the cooling process is uniform and without defects. When making your selection, go for the runner that has the maximum injection pressure.
Ease of Maintenance: With so many movable parts, minor mechanical issues are bound to appear, and the cost can be high if the runners in question are complicated. Always go for the type that is easy to maintain and repair.
Injection molding runners are essential for the whole process, and they come in many shapes and designs. Finding the right one for your needs can be a little confusing, especially if this is your first time getting into the injection molding process. For more information on how runners and other components work, check out our website at any time of the day to get professional plastic injection molding service.
Please contact us using the form below or emailing (harry@fowmould.com)