HDPE, otherwise known as PEHD, is a thermoplastic polymer made from the monomer ethylene.
It has become a common material in modern society, with numerous products available on the market like grocery bags, plastic containers, drinking water bottles, cream cheese containers, etc.
With the spread of HDPE, questions are raised about its suitability for human use.
As such, the popularity of HDPE stems from its amazing properties, which make it an attractive option for use in a vast array of applications.
Its versatility is due to its high strength-to-density ratio, impact resistance, and corrosion resistance, as well as its chemical stability.
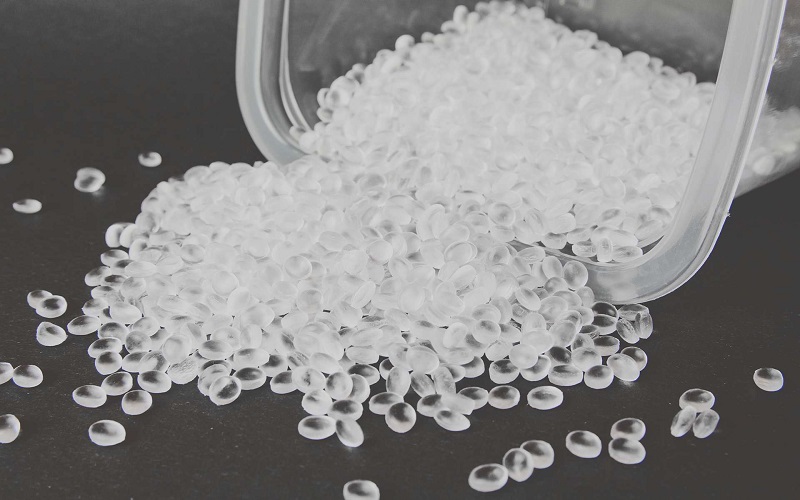
HDPE is used to produce plastic bottles, corrosion-resistant piping, geomembranes, or plastic lumber, as well as many everyday objects.
One of the main issues addressed with HDPE is related to its safety for human contact. PHDPE, in its final form, molded into containers or products, is usually safe.
In fact, HDPE is widely used in the manufacturing of food packaging under FDA rules.
This regulatory permission confirms it to be suitable for direct contact with consumables.
This is to note that although all food-safe containers are made from HDPE, not every HDPE is naturally food-safe.
This distinction thus highlights the need to know certain features and uses of HDPE in different settings.
The HDPE safety profile depends closely on the intended use and manufacturing processes.
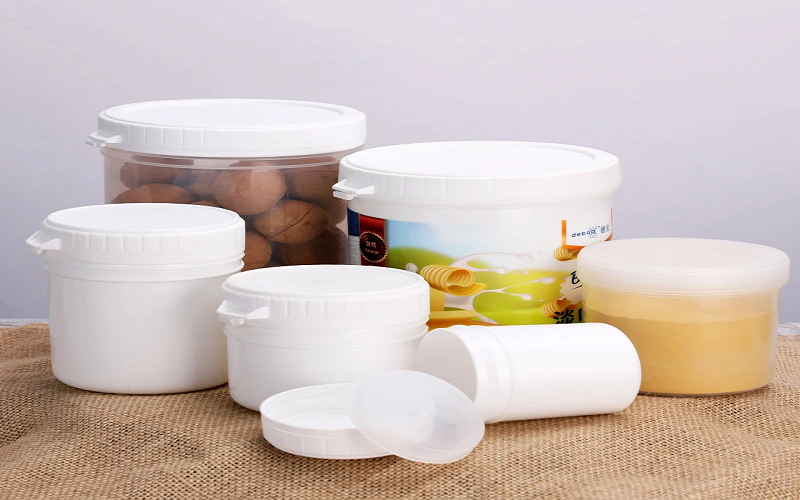
Composition of HDPE
HDPE, which is symbolized by the chemical formula C2H4n, is an omnipotent polymer with several common names like Polyethylene High-Density or alkaline and other similar designations as well as # 2 plastic.
0.958g/cm3 is the HDPE’s average density, and its material properties consist of a high strength-to-density ratio, impact, and chemical resistance.
Well, a recycling ability is smooth melt point surface finishing options that are easy in molding or working with it. HDPE is produced using a multi-stage process.
Since it is obtained from petroleum, the first part of this process has to be related to the breaking down of hydrocarbons found in petroleum into important monomers like ethylene molecules through high heat.
Then metallic catalysts like titanium tetrachloride, diethyl aluminum chloride, and chromium oxides on silica are used to turn the collected ethylene gas, along with other compounds, into polyethylene slurry.
After catalyst removal, the HDPE is extracted, filtered, and dried.When that is done, the HDPE developed can then be processed into stock or specific products.
Although this overview makes a simplified form of the complicated organic chemistry, it shows that HDPE results from petroleum.
And polymerizes in an elaborate fashion using catalysts to build up linear structures of high density with various uses.
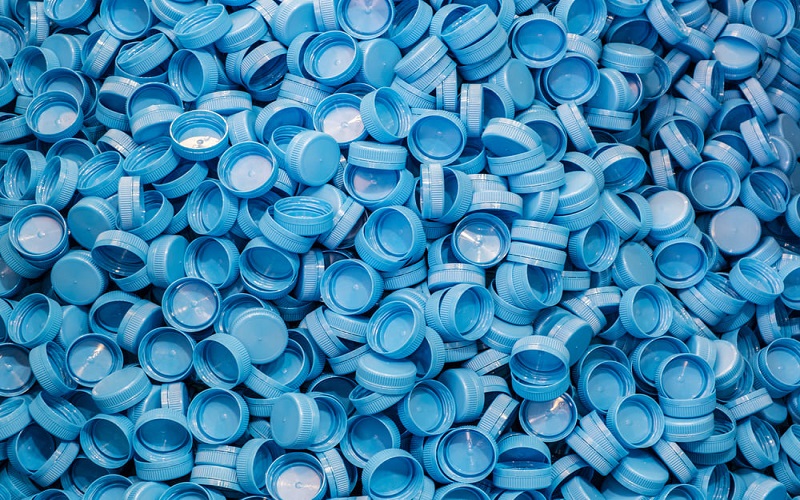
Production of HDPE
HDPE is produced from ethylene through Ziegler-Natta polymerization or the Phillips slurry process in industrial production.
One of the popular methods is the Ziegler-Natta method, which utilizes a joint action of catalysts, including titanium tetrachloride reacting with gaseous ethylene to precipitate high-density polyethylene.
Another procedure called the Phillips slurry process uses silica-based steady-flow ceramic and hydrocarbon as solids mixed,processing will decide the characteristics of HDPE.
The method of synthesizing the HDPE is an important factor because the microstructure will be different.
The Phillips-Slurry process produces HDPE with fewer branches and more accurate molecular weight than the Ziegler, but it produces less flexible types of polyethylene.
The molecular weight of HDPE means the length of polyethylene chains, which also will influence such properties as flexibility and yield strength or melt temperature.
After the precipitate has been formed, the extent of crystallinity will depend on processing temperature and pressure, including time for cooling.
Obviously, in some applications, it is desirable to have a high degree of crystallography for increased rigidity and chemical resistance.
After HDPE has been manufactured, it becomes ready for use in commercial products.
Methods for producing HDPE products industrially include HDPE injection molding, which is fit for designing toys with complex shapes.
Constant-profile products like pipes and films use extrusion molding.
Blow molding is used for the production of hollow products, such as bottles and plastic bags.
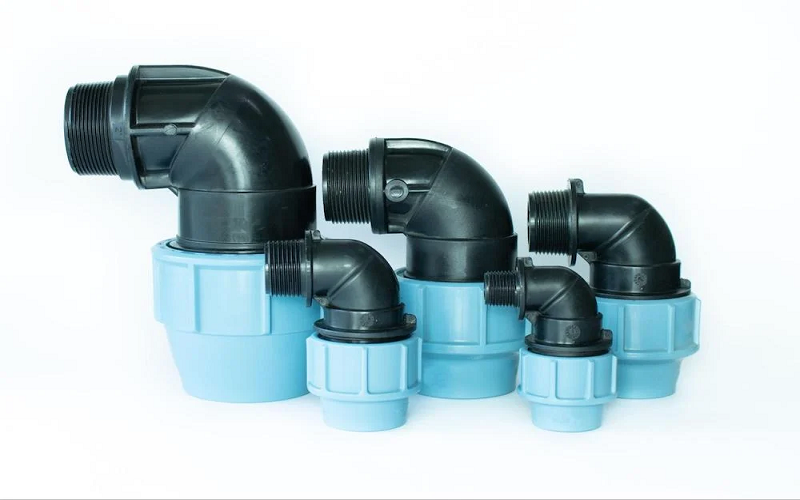
Applications of HDPE
HDPE is a famous material; it is considered very versatile owing to its various qualities.
It is a preferred material in multiple applications due to its strength, impact resistance, corrosion resistance, and chemical profile.
HDPE is widely used in corrosion-resistant piping, sheets, stock materials, fuel tanks, and food and beverage containers.
Plastic packages or bottles, namely milk lugs, cups, etcetera; personal care product packaging trash cans and bins.
Recycle bins and bread bags. Cereal box liners. Laundry detergent bottles, among others.
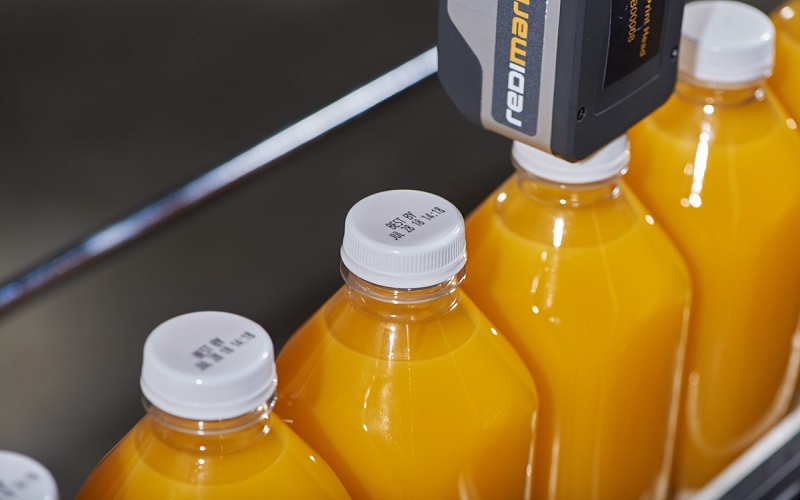
It can be felt in recycled plastic lumber, medical equipment, 3D printing filament boating components, coax cable insulators, sewage mains, and numerous others.
HDPE is widely used in medical tubing, films, connectors lab, ware catheters, IV bags, face masks, device housings, membranes, and drug-delivery components packaging.
Especially in hospitals due to its low moisture absorption, chemical resistance, recyclability, and the fact that it has a very low bacterial retention rate.
The specialized forms of PE(like ultrahigh molecular weight polyethylene)are used in orthopedic implants that have benefits such as a very low friction coefficient, great wear resistance, and impact strength, chemical stability, corrosive protection, and biocompatibility.
HDPE is such a versatile material that its uses encompass many different industries.
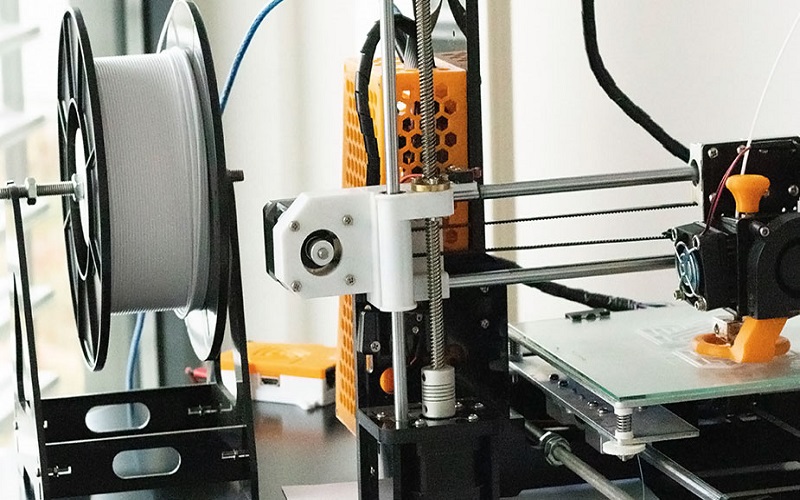
Advantages of HDPE
High Strength Type of Plastic
High-density polyethylene plastic is worth mentioning among materials due to the many advantages that make it so popular and widely used.
This is due to its high strength-weight ratio, positioning it as a lightweight yet durable solution that can be used in different areas.
Low Coefficient of Friction
HDPE possesses a low coefficient of friction and very little moisture absorption, making surfaces smooth at the touch and able to withstand different forces caused by environmental factors.
Its remarkable resistance to impacts makes it immune to dents and scratches, which guarantees its longevity in use.
Chemical Resistant
Chemical resistance of HDPE is one of its outstanding features as it resists getting damaged by chemicals, water, solvents, acids and detergents, and cleaning fluids.
This resilience also involves formability under moderate to low shrinkage, meaning that this material is suitable for many manufacturing processes.
HDPE can be used without the fear of toxic chemicals and harmful chemicals, and that is imperative for food industry.
Recyclable
HDPE can be recycled and used to fabricate sustainable products, thereby reducing environmental degradation.
The plastic’s boiling sterilizability, resistance to bacterial retention, and dishwasher safety are factors that make the use of such material in medical appliances suitable for food packaging purposes, shampoo bottles, soda bottles, yogurt containers, milk jugs, milk bottles, baby bottles, as well as everyday stuff.
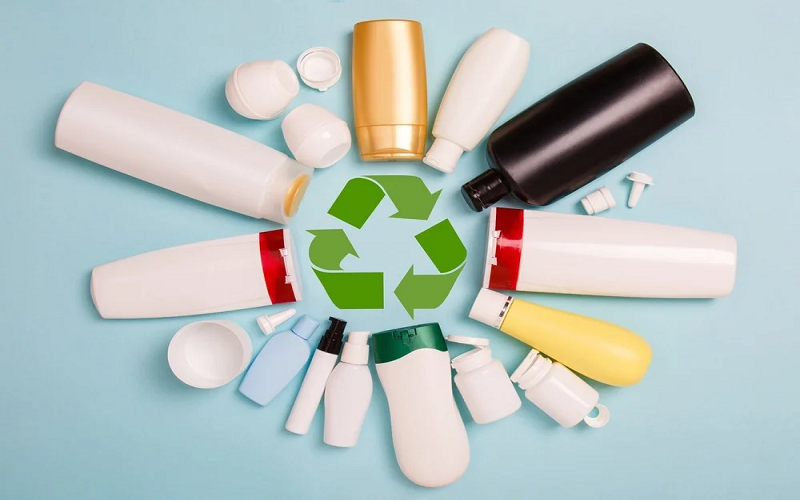
Incredibly Versatile
Concerning the potential of HDPE to be versatile, it replaces heavier materials in some cases and reduces weight without affecting performance for strength or use.
Cost-effectiveness makes it even more appealing, balancing performance and affordability.
HDPE benefits span a range of qualities that make this material the preferred option in industries from packaging to construction, reflecting its versatility and worth.
Is HDPE Safe for Humans?
To discuss the safety of High-Density Polyethylene, it is important to distinguish between its final form and how it is made.
Typically, when molded into containers or other items, once it is in its end product, HDPE does not pose as being dangerous. In fact,HDPE is a commonly used material for food packaging because it meets the regulations set by the US FDA.
Such regulatory approval highlights that it could be used in direct contact with consumables.
However, it must be stressed that even though all food-safe containers are made from HDPE, not all HDPE is naturally food-safe.
This division helps to emphasize the importance of knowing particular features and usages for HDPE in different settings. Safety precautions must be observed during the production process.
The production of dust or resin from the creation process of polyethylene may irritate the eye.
The vapors released every time one heats the resin is also a risk, and those involved in manufacturing should ensure that they put on proper safety gear during this.
These safety precautions are necessary to avoid accidental injuries and maintain the health of those working with HDPE.
HDPE is safe depending on the context— i.e., whether it’s in its final form as a food-safe HDPE container or when still being manufactured.
Although HDPE is generally safe for its application, safety precautions are still necessary during production to prevent the risks associated with inhaling dust and vapors.
Finally, the wide application of HDPE in several sectors, including food packaging, demonstrates that it is safe to use where there are proper usage recommendations.
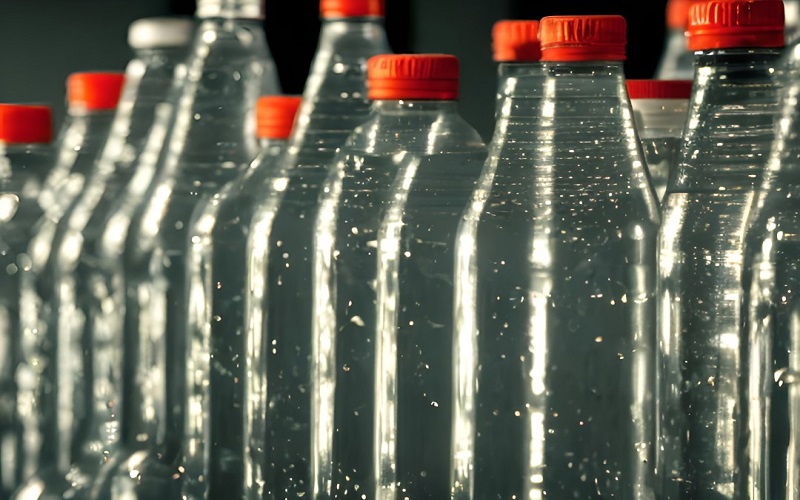
Conclusion
HDPE is a very flexible material that has many applications across several sectors of the industry.
The essence of manufacturing plastics is rather complex, beginning with the decomposition of oil-derived hydrocarbons and continuing polymerization using metal catalysts.
The HDPE produced, as a consequence, shows great material properties, including strength-to-density ratio, chemical and impact resistance, and recyclability.
Many areas in which HDPE is used include corrosion-resistant piping, food and beverage packaging containers, medical equipment, and 3D printing filaments.
These benefits, such as a high strength-to-mass ratio and low friction coefficient plus resistance to elements, make it popular.
It also enhances the adaptability and cost-effectiveness of material if, in some cases, it can serve as a substitute for heavier materials.
Despite the fact that HDPE is not considered hazardous to use during regular operations, precautions should be taken when producing this material because exposure to dust and vapors can pose a particular health threat.
The material meets the FDA specifications for food contact uses, which means that it can be used in some cases.
HDPE is applied in numerous fields, and its appearance across diverse industries shows that it suits different spheres of use.
Relevant usage recommendations and safety procedures additionally strengthen the responsible use of HDPE in multiple industries.