In the world of plastic manufacturing, two processes reign supreme: blow molding and injection molding. These two methods are widely used to create a vast array of plastic parts and products, from small medical components to large automotive parts. The choice between blow molding vs injection molding often depends on the specific requirements of the project, including the design of the part, the desired material, and the production volume. In this article, we will delve into the details of these two processes, highlighting their advantages, types, applications, and key differences.
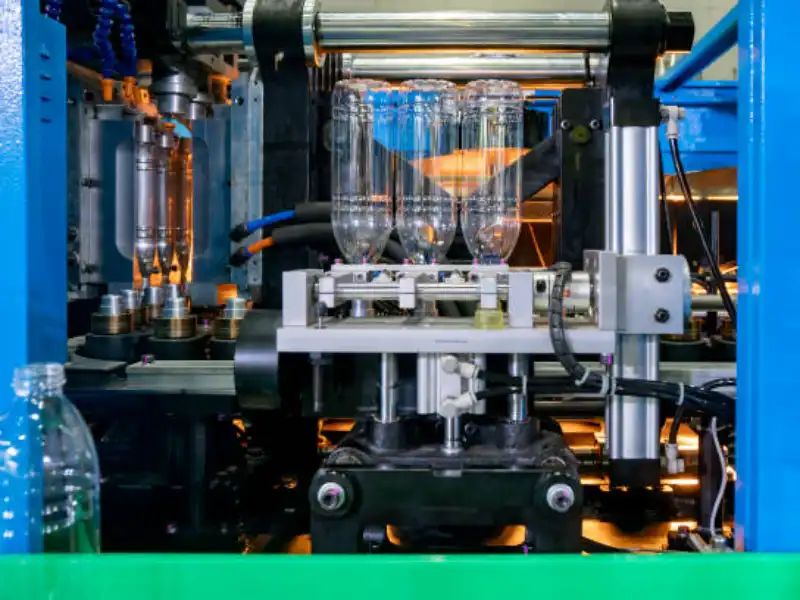
What Is Blow Molding?
Blow molding is a manufacturing process utilized to produce hollow plastic parts. The process commences with the melting of a plastic material, typically in the form of pellets. The molten plastic is then extruded into a tube-like piece known as a parison. This parison is enclosed within a mold, and air is blown into it, inflating the plastic to conform to the shape of the mold. Once the plastic has cooled and hardened, the mold is opened, releasing the finished part. Blow molding is particularly suited for creating lightweight, hollow products with complex shapes, such as bottles, containers, and fuel tanks. This process is a staple in industries such as packaging, automotive, and toys, where hollow, lightweight parts are required.
Advantages of Blow Molding
- Ability to produce complex and intricate shapes: The plastic can stretch and conform to the mold under the influence of air pressure, allowing for the creation of complex shapes.
- High efficiency: Blow molding can produce large quantities of parts in a short amount of time, making it cost-effective for high-volume production runs.
- Uniform wall thickness: Blow molding can produce parts with uniform wall thickness, which is crucial for products that need to withstand pressure or contain liquids, such as bottles and containers.
- Material flexibility: Blow molding allows for the use of a wide range of materials, including various types of plastics and polymers, giving manufacturers flexibility in their material choice.
Types of Blow Molding
There are three main types of blow molding: extrusion blow molding, injection blow molding, and stretch blow molding.
- Extrusion Blow Molding: The most common type, involves extruding a parison which is then inflated into the mold. This method is often used for larger, less precise parts.
- Injection Blow Molding: Involves injecting the molten plastic into a mold to form a preform, which is then blown into the final shape. This method is often used for smaller, more precise containers.
- Stretch Blow Molding: Involves stretching the preform axially during inflation to improve material distribution and increase the strength of the final product. This method is often used for products that require high strength and clarity, such as beverage bottles.
Applications of Blow Molding
Blow molding is used in a wide range of industries to produce a variety of products. In the packaging industry, it is used to create plastic bottles and containers with bottle caps for beverages, personal care products, and household cleaners. In the automotive industry, blow molding is used to manufacture fuel tanks, air ducts, and other hollow parts. Other applications include toys, sporting goods, and medical parts. The versatility of blow molding, combined with its cost-effectiveness, makes it a popular choice for many manufacturers.
What Is Injection Molding?
Injection molding is another widely used process for manufacturing plastic parts, including plastic injection molding. Unlike blow molding, which is used to create hollow parts, injection molding is used to create solid parts. The process involves melting plastic pellets and injecting the molten plastic into a mold under high pressure to achieve a high precision match. The plastic is then allowed to cool and harden within the mold, preventing any air leaks. Once the part has solidified, the mold is opened, and the excess material is trimmed off. Injection molding is known for its ability to produce high-precision parts with tight tolerances, making it ideal for applications that require a high degree of accuracy and repeatability.
Advantages of Injection Molding
- High precision and repeatability: Injection molding allows for the production of complex, detailed parts with a high degree of precision and repeatability, making it ideal for parts that require tight tolerances.
- High efficiency: Injection molding is a highly efficient process that can produce a large number of parts quickly, making it cost-effective for high-volume production runs.
- Material flexibility: Injection molding allows for the use of a wide range of materials, including various types of plastics and polymers, giving manufacturers flexibility in their material choice.
- Ability to produce solid parts: Injection molding is capable of producing solid parts, making it suitable for applications that require sturdy, durable components.
Types of Injection Molding
There are several types of injection molding, including overmolding, insert molding, and multi-shot molding.
- Overmolding: Involves injecting a layer of material over a pre-existing part, often to add a soft touch or decorative element. This method is often used for products that require a comfortable grip or aesthetic appeal.
- Insert Molding: Involves inserting a component, such as a metal part, into the mold before the plastic is injected, creating a single piece with combined materials. This method is often used for products that require the strength of metal with the benefits of plastic, such as power tools.
- Multi-shot Molding: Also known as two-shot molding, involves injecting two different materials into the same mold to create a single part. This method is often used for products that require different material properties in different areas, such as toothbrushes.
Applications of Injection Molding
Injection molding is used in a wide range of industries to produce a variety of products with complex designs. In the automotive industry, it is used to manufacture components such as dashboards, knobs, and interior parts. In the medical industry, injection molding is used to produce surgical instruments, implantable components, and diagnostic devices. Other applications include consumer electronics, household appliances, coolers, and aerospace components. The versatility of injection molding, combined with its precision and efficiency, makes it a popular choice for many manufacturers.
What Are the Differences Between Blow Molding and Injection Molding?
Blow Molding | Injection Molding | |
Advantages | Can create complex, hollow shapes.Efficient for high-volume production.Can produce parts with uniform wall thickness.Allows for a wide range of material choices. | Can create complex, solid shapes with high precision.Efficient for high-volume production.Allows for a wide range of material choices.Can produce sturdy, durable components. |
Disadvantages | Less precise than injection molding.Limited to hollow parts.Not ideal for heavy-duty applications. | Higher initial setup costs due to complex molds.Not suitable for creating hollow parts.Can lead to material wastage due to the runner system. |
Products Produced
One of the key differences between blow molding and injection molding lies in the types of products they produce. Blow molding is primarily used to manufacture hollow parts, such as bottles and containers, while injection molding is used to produce solid parts, such as automotive components and medical devices.
Blow Molding | Injection Molding | |
Products Produced | Primarily used to manufacture hollow parts, such as bottles and containers. | Primarily used to produce solid parts, such as automotive components and medical devices. |
Molding Processes
The molding processes of blow molding and injection molding also differ significantly. In blow molding, a parison is inflated within a mold to form the final shape, while in injection molding, molten plastic is injected into a mold and allowed to cool and harden.
Blow Molding | Injection Molding | |
Process | The blow molding process involves inflating molten plastic (parison) within a mold to form the final shape. | Involves injecting molten plastic into a mold and allowing it to cool and harden into solid plastic parts. |
Material Choice
Both blow molding and injection molding can work with a wide range of plastic materials. However, the choice of material can impact the process and the final product. For instance, some materials may be more suitable for blow molding due to their ability to stretch and conform to the mold, while others like polycarbonate may be more suitable for injection molding due to their flow characteristics and ability to fill complex molds. Polyethylene is another popular plastic material used in both blow molding and injection molding processes.
Blow Molding | Injection Molding | |
Material Choice | Some materials are more suitable due to their ability to stretch and conform to the mold. | Some materials are more suitable due to their flow characteristics and ability to fill complex molds, especially when it comes to thin-walled components like a molded part. |
Cost
The cost of blow molding and injection molding can vary depending on several factors, including the complexity of the part, the material used, and the production volume. Generally, blow molding tends to be more cost-effective for producing large quantities of simple, hollow parts, while injection molding can be more cost-effective for producing smaller quantities of complex, solid parts. However, it’s important to note that the initial setup costs for injection molding can be higher due to the complexity of the molds. Therefore, the overall cost-effectiveness will depend on the specifics of the project, including the production volume and the lifespan of the product.
Blow Molding | Injection Molding | |
Cost | Generally more cost-effective for producing large quantities of simple, hollow parts. | Generally more cost-effective for producing smaller quantities of complex, solid parts. |
Mold Design
The design of the mold also differs between blow molding and injection molding. Blow molds need to accommodate the inflation of the parison and are typically two-part molds, while injection molds can be more complex and may include multiple cavities and cores to create detailed, intricate parts. The complexity of the mold design in injection molding can lead to higher initial costs, but it also allows for greater precision and detail in the final product.
Blow Molding | Injection Molding | |
Mold Design | Molds need to accommodate the inflation of the parison and are typically two-part molds. | Molds can be more complex and may include multiple cavities and cores to create detailed, intricate parts. |
The Role of Air
Air plays a crucial role in blow molding, where it is used to inflate the parison and form the final shape. In contrast, air is the enemy in injection molding, as it can create air pockets or bubbles that lead to defects in the final part. Therefore, the injection molding process requires careful control of the injection speed and pressure to minimize the risk of air entrapment.
Blow Molding | Injection Molding | |
Role of Air | Air is used to inflate the parison and form the final shape. | Air is the enemy as it can create air pockets or bubbles that lead to defects in the final part. |
Blow Molding vs Injection Molding: What Factors Should Be Considered When Choosing for Projects?
- Design of the Part:
- Hollow parts: Blow molding is preferable.
- Solid parts: Injection molding is more suitable.
- Desired Material:
- Some materials are better suited for blow molding due to their ability to stretch and conform.
- Others are more apt for injection molding due to their flow characteristics and ability to fill detailed molds.
- Production Volume:
- High-volume, simple parts: Blow molding might be more cost-effective.
- Low-volume, complex parts: Injection molding might be more economical.
- Budget:
- Initial setup costs for injection molding can be higher due to mold complexity.
- Blow molding might have lower initial costs but can be more expensive per unit for low-volume runs.
- Precision and Detail:
- High precision and intricate details: Injection molding is the better choice.
- Less precision with uniform wall thickness: Blow molding is preferable.
- End-use Requirements:
- Products that need to withstand pressure or contain liquids: Blow molding is ideal.
- Durable, solid components for structural applications: Injection molding is more apt.
By considering these factors, manufacturers can make an informed decision on which process best suits their project needs.
Conclusion
In conclusion, both blow molding and injection molding offer unique advantages and can be used to produce a wide range of products. The choice between these two processes depends on the specific requirements of the project. By understanding the differences between blow molding and injection molding, manufacturers can make informed decisions and choose the process that best meets their needs.
Get an Instant Quote With FOWMould
If you’re considering using blow molding or injection molding for your next project, FOWMould can provide you with an instant quote today. With our extensive experience in both blow molding and injection molding, we can guide you through the process and help you choose the best solution for your project. Contact us today to get started.