What Is a Thermoset?
Thermoset is a type of polymer that becomes irreversibly hard when heated. This hardening process, known as curing, is induced by the application of heat or suitable radiation. It results in a chemical reaction that creates strong cross-links between the polymer chains. These cross-links provide thermosets with their unique material properties, including high heat resistance, excellent dimensional stability, and superior mechanical properties. Examples of thermosets include epoxy, polyurethane, and phenolic resins.
Advantages and Disadvantages of Thermoset
Advantages | Disadvantages |
High Heat Resistance: Thermosets can withstand high temperatures without melting or deforming, making them ideal for applications such as engine parts, cookware, and electrical insulation. | Non-Recyclable: Once cured, thermosets cannot be remolded or recycled. This limitation can lead to waste and challenges sustainability. |
Dimensional Stability: Thermosets maintain their shape and size even under heat or mechanical stress. This property, along with its unique physical properties, is crucial for applications that require materials with high strength and rigidity. | Difficult to Process: Thermosets require specialized equipment and techniques for processing, making them more difficult and potentially more costly to manufacture than thermoplastics. |
High Strength-to-Weight Ratio: Thermosets provide high strength without adding much weight, making them suitable for lightweight, high-strength applications like aerospace and automotive components. |
Applications of Thermoset
- Automotive Industry: Used for parts like brake pads, engine components, and body panels due to high strength and heat resistance.
- Electronics: Utilized in circuit boards and components because of their excellent electrical insulation properties.
- Construction: Employed in adhesives, sealants, and coatings that need to resist environmental conditions.
- Aerospace: Used in components due to high heat resistance and strength-to-weight ratio.
- Industrial Machinery: Chosen for durability and resistance to wear.
- Consumer Goods: Incorporated in various products benefiting from thermoset properties.
Materials of Thermoset
- Epoxy Resins: Known for mechanical properties and chemical resistance; used in adhesives, coatings, and electronics.
- Polyurethane: Versatile; flexible types are used in mattresses and upholstery, while rigid types are in car parts and building materials.
- Phenolic Resins: Recognized for heat resistance and electrical insulation; found in circuit boards and brake linings.
- Polyester Resins: Used in fiberglass composites.
- Silicone Resins: Employed in coatings and sealants.
What Is a Thermoplastic?
Thermoplastics are a type of polymer that can be heated, shaped, and cooled multiple times without undergoing any chemical changes. This property makes thermoplastics highly versatile and recyclable. When heated, thermoplastics become soft and pliable, allowing them to be molded into various shapes. When cooled, they return to a solid state, retaining their new shape. Examples of thermoplastics include polyethylene, polypropylene, PVC, and polystyrene.
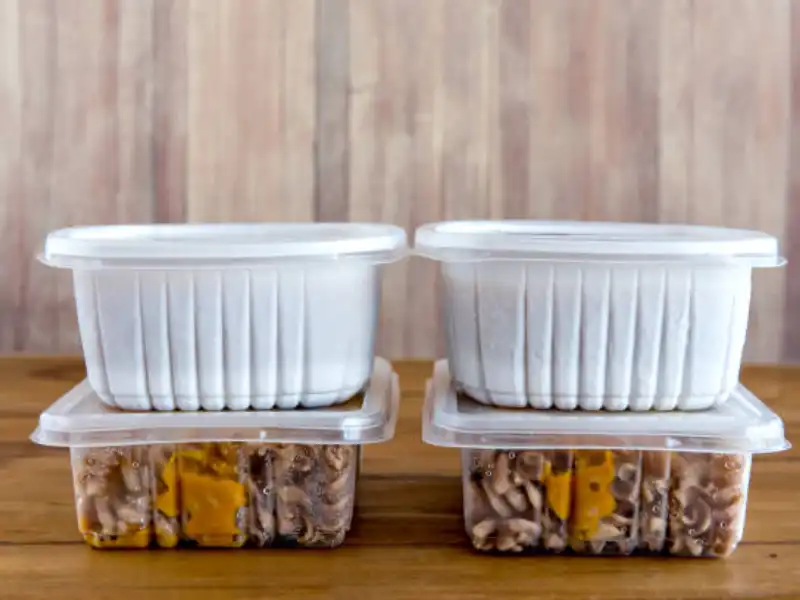
Advantages and Disadvantages of Thermoplastic
Advantages | Disadvantages |
Recyclability: Thermoplastics offer a wide range of material options that can be reshaped and recycled multiple times, promoting sustainability and reducing waste. | Lower Heat Resistance: Compared to thermosets, thermoplastics have a lower heat resistance. They can deform or melt at high temperatures, limiting their use in certain applications. |
Ease of Processing: Thermoplastics are generally easier to process than thermosets. Common manufacturing methods like injection molding, extrusion, and thermoforming can be used, often translating to lower manufacturing costs and efficient injection moulding. | Potential Lack of Rigidity: While thermoplastics can be strong, they might not offer the same level of hardness, rigidity, or structural integrity as some thermosets, which could be a disadvantage in applications requiring high structural strength and deformation resistance. |
Transparency: Thermoplastics can be transparent, providing clear visual properties essential in applications like packaging. | |
Impact Resistance: Thermoplastics exhibit excellent impact resistance, crucial in products that need to withstand mechanical stress in different applications. |
Applications of Thermoplastic
- Packaging: Backbone of products like plastic bottles and food containers.
- Automotive: Used in parts such as bumpers, interior panels, and fuel tanks.
- Eyewear: Transparency makes them ideal for lenses.
- Medical: Flexibility is perfect for medical tubing.
- Toys and Household Appliances: Due to their malleability and safety.
- Electronics: For components and casings.
- Aerospace: In specific components requiring lightweight materials.
Materials of Thermoplastic
- Polyethylene: Widely used in packaging due to its chemical resistance.
- Polypropylene: Suitable for automotive and textile applications because of its high melting point.
- PVC (Polyvinyl Chloride): Known for electrical insulation.
- Polystyrene: Valued for rigidity and transparency.
- Nylon: Recognized for strength and flexibility.
- Polycarbonate: Impact-resistant and transparent.
- ABS (Acrylonitrile Butadiene Styrene): Combines properties of its components for versatility.
Difference Between Thermosets and Thermoplastics
Comparing the Melting Points
One of the most significant differences between thermosets and thermoplastics is their behavior when exposed to heat. Thermoplastics, including thermoplastic polymers, have a distinct melting point, the temperature at which they transition from a solid to a liquid state. This property allows them to be repeatedly melted and reshaped, contributing to their recyclability. For instance, polypropylene, a common thermoplastic, has a melting point in the range of 130 to 171 degrees Celsius, which allows it to be molded into a variety of shapes and forms, from automotive parts to packaging materials.
On the other hand, thermosetting polymers, due to their cross-linked molecular structure, do not have a clear melting point. Instead, they undergo a curing process when initially heated, which forms a rigid, three-dimensional network of chemical bonding. This process is irreversible, and once cured, a thermoset cannot be remelted or reshaped without causing its decomposition. If a thermoset is subjected to excessive heat, it will not melt but instead begin to degrade, losing its structural integrity. This high heat resistance makes thermosetting plastics suitable for applications that require materials to withstand high temperatures, such as in the case of epoxy resins used in electronic circuit boards.
Aesthetics and Finishing
The aesthetic and finishing properties of thermosets and thermoplastics also differ significantly, influencing their use in various applications. Thermoplastics, due to their ability to be melted and reshaped, can be molded into intricate designs with a high level of precision. They can also be made transparent or dyed into a wide range of colors, offering aesthetic versatility. For instance, polystyrene, a type of thermoplastic, is often used in applications that require transparency, such as food packaging and laboratory ware.
Thermosets, on the other hand, are typically opaque and are often used for their mechanical and thermal properties rather than their aesthetics. However, they can be finished to a high gloss or textured finish depending on the application. For example, thermoset composites are often used in the automotive industry where a high-quality surface finish is required. Despite their lack of transparency, thermosets can also be colored using pigments or dyes, allowing for some level of aesthetic customization.
Corrosion Resistance
Corrosion resistance is a crucial property in many applications, and both thermosets and thermoplastics offer varying degrees of resistance to corrosion. Thermoplastics such as polyethylene and polypropylene are inherently resistant to many common forms of corrosion, including resistance to a wide range of chemicals and moisture. This makes them suitable for use in harsh environments, such as in chemical storage and handling equipment, as well as in outdoor applications where they may be exposed to the elements.
Thermosets, due to their cross-linked structure, also exhibit excellent resistance to corrosion. They can withstand exposure to a wide range of chemicals without degradation, making them suitable for use in applications such as coatings, linings, and seals in chemical processing equipment. However, the specific type and degree of corrosion resistance can vary depending on the type of thermoset and any additives or fillers used. For instance, epoxy resins are known for their excellent resistance to chemical corrosion, while polyester resins offer good resistance to weathering and environmental degradation.
Durability and Heat Resistance
Durability and heat resistance are two key factors that often influence the choice between using thermosets and thermoplastics. Thermosets, due to their cross-linked structure, generally offer superior durability and heat resistance. Once cured, they form a rigid, infusible structure that can withstand high temperatures and mechanical stress without deforming. This makes them ideal for applications that require materials to maintain their shape and properties under harsh conditions, such as in automotive components, industrial machinery, and high-temperature electrical insulation.
Thermoplastics, while durable, do not offer the same level of heat resistance as thermosets. They soften upon heating and can deform under high temperatures or prolonged exposure to heat. However, they offer excellent impact resistance and can withstand mechanical stress without cracking or breaking. This makes them suitable for applications that require toughness and flexibility, such as in protective helmets, plastic containers, and medical devices.
Cost Analysis
The cost of thermosets and thermoplastics can vary widely depending on the specific material, its properties, and the manufacturing process used. In general, thermoplastics are often cheaper to produce due to their ease of processing. They can be easily melted and reshaped, allowing for high-speed, high-volume manufacturing processes such as injection molding and extrusion. This can result in lower production costs, especially for large-scale production runs.
Thermosets, on the other hand, are typically more expensive to produce. The curing process requires additional time and energy, and the resulting products cannot be remelted or recycled, which can lead to waste. However, the superior properties of thermosets, such as their high heat resistance and dimensional stability, often justify their higher cost in applications that require these properties.
Manufacturing Process
The manufacturing processes for thermosets and thermoplastics also differ significantly. Thermoplastics are typically processed using techniques such as injection molding, blow molding, and extrusion. These processes involve melting the thermoplastic material and shaping it into the desired form, followed by cooling to solidify the material. The ease of processing and the ability to produce complex shapes make thermoplastics suitable for a wide range of applications.
Thermosets, in contrast, are processed using techniques such as compression molding, transfer molding, and reaction injection molding. These processes involve shaping the thermoset material and then heating it to initiate the curing process, which forms a rigid, infusible structure. The processing of thermosets is more complex and requires more time and energy than the processing of thermoplastics, but it allows for the production of parts with superior heat resistance and dimensional stability.
Conclusion
In conclusion, the main difference between thermosets and thermoplastics lies in their molecular structure, behavior when heated, and their respective advantages and disadvantages. Understanding these differences is crucial when choosing the right material for a specific application.
Contact Us
If you have any further questions about the major difference between thermosets and thermoplastics, or if you need assistance with your plastic molding needs, please don’t hesitate to contact us at FOWMould. Our team of experienced professionals is always ready to help.