Acrylic is a translucent thermoplastic, also referred to as PMMA or plexiglass. Although other forms like tubes and rods are available, sheet stock is the most typical format of this type of material. It is frequently used as a lightweight, break-resistant substitute for glass. But because it has so many appealing qualities, it may also be used in various other applications.
Acrylic injection molding involves many procedures, such as injecting heated materials into a mold. And this process enables you to form an Acrylic into any shape.
The injection molding method is designed to produce vast quantities of components. It necessitates an initial capital investment in tooling compared to other production methods like CNC machining and 3D printing.
Read on this The Ultimate Guide to Acrylic injection molding.
What is Acrylic and What are its Properties?
Acrylic injection molding is widely accessible and reasonably priced. When material strength is not a deciding issue, it is an excellent substitute for polycarbonate. To combine the scratch resistance of Acrylic with the impact strength of polycarbonate (PC), Acrylic is occasionally layered on top of the PC. This is how some “glass” that is bulletproof is manufactured.
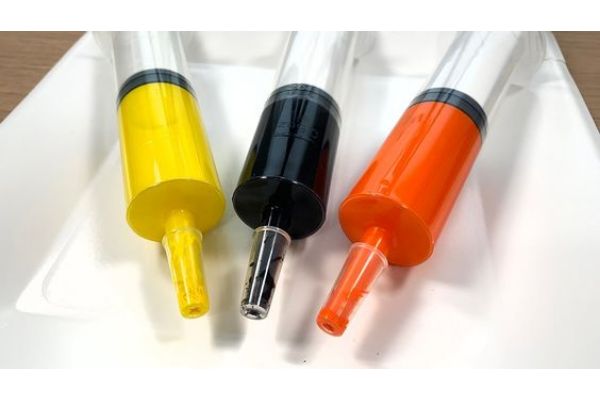
The Acrylic on the exterior provides scratch resistance for daily usage while the PC deflects the bullet.
The Applications of Acrylic Injection Molding
In the technique of Acrylic injection molding, organic glass or Acrylic is injected into a cavity to create a specific product after cooling and hardening. The molds created by Acrylic injection molding are used to create mobile phone displays, aquarium screens, and automotive windows. Because it has superior abrasion resistance to glass, Acrylic is favored.
When high impact resistance is not a concern, but transparency is required, Acrylic is a very useful material.
Compared to other transparent polymers, Acrylic is remarkably scratch resistant. In situations where strength is not a primary concern, it is a more lightweight substitute for glass and a more affordable option than polycarbonate.
Because the material vaporizes upon contact with the focused laser energy, it may be sliced into incredibly precise forms utilizing laser cutting technology.
Various Properties of Acrylic
In the previous paragraphs, some useful characteristics of Acrylic are mentioned, such as the abilities of abrasion resistance and high impact resistance. This part will list some of the properties of this material in detail so that you will get a deeper understanding of Acrylic.
- General Properties
Relative Density 1.19 g/cm3 Rockwell Hardness M 102 Water Absorption -.2% ~Flammability Class 3, (BS 476 pt 7) UL94 HB
In general, Acrylic has excellent delineation as well as a good resistance against impact. This lightweight material can play the role of an exceptional thermal insulator. Besides the heat, this material can also be used to block UV rays.
- Optical Properties:
Light Transmission > 92% Refractive Index 1.49
Acrylic plastic transmits 92 percent of white light, in other words, it has outstanding light transmission qualities, and this property gives it exceptional optical clarity (when either MOP or vapor polished) akin to glass. Like Perspex and Rohm Plexiglas, Acrylic is also one of the excellent materials for the production of light guides and lenses.
- Mechanical Properties
The tensile strength of Acrylic is around 8000 psi. This essentially means that to break Acrylic, 8000 pounds of weight is needed per square inch. It has a tensile modulus of 350,000-500,000 psi and a similar flexural modulus.
Acrylic is a better alternative to glass since it can withstand high pressure and has an impact as well water and UV resistance. All of this is a clear indication that Acrylic is a strong material.
- Thermal Properties:
Minimum Service Temperature -40⁰C Maximum Service Temperature 80⁰C Softening Point > 110⁰C Linear Expansion 7.7×10-5
Acrylic has a melting temperature of 130-140⁰C and a maximum operating temperature of 65-93⁰C. Because of this, acrylic is suitable for working at somewhat high temperatures but can also be easily heat-formed. Due to low conductivity, it is a remarkable thermal insulator.
Advantages of Acrylic in Injection Molding
The advantages of Acrylic as an injection-moldable material are numerous. When polymers are injected, both the application and the processing are considered. The benefit of the injection molding method is thus examined below.
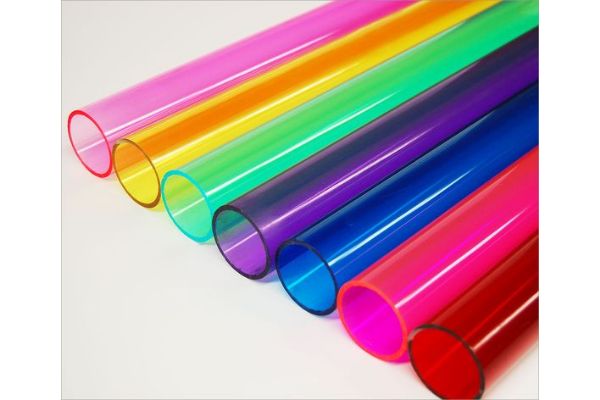
- Filter the Ultraviolet Light
Some people might be surprised to learn that Acrylic can ultraviolet rays, given that many products made with it are used indoors, so Acrylic’s outstanding ability of UV resistance is not well known to most people.
When applied outside, transparent Acrylic has been shown to remain colorless for up to 30 years. Styrene, PETG, and polycarbonate are other common transparent polymers that can be compared to Acrylic, although Acrylic gives far better weather ability.
The thermoplastic is very versatile and has good heat stability. This makes it easy to bind it to other substrates to create products that are stronger or more resistant to breaking. It is a popular alternative for many items because of its simplicity in production and excellent wearability.
- Superior Clear and Transparent
Acrylic injection molding may easily be seen through. In reality, Acrylic is frequently used as a lightweight, inexpensive alternative to glass. The Acrylic surface may even serve as a mirror with the proper care.
With exceptional manufacture, which is on par with glass, transparency may reach up to 92%. In reality, it is unquestionably preferable to glass for two reasons. First, it doesn’t develop a green tint over time as thick glasses do, and second, it doesn’t become yellow or fade even after prolonged exposure to sunshine.
- Rigidity and Durability
Acrylic injection molding has demonstrated the durability of Acrylic sheets and their byproducts. Acrylic molding may be utilized for various industrial applications since it is strong and impact-resistant, including face shields and motorcycle windscreens.
Although Acrylic is strong and long-lasting, it is also readily scratched. The production of Acrylic goods has the potential to emit extremely hazardous vapors. Everyone who works to create an Acrylic injection molding is given protective gear and attire.
Because of its extraordinary durability, Acrylic can be utilized in various temperatures and has better weather resistance than glass and other types of plastic. It won’t break under heavy force; if it does, it will break into big, blunt-edged pieces.
- Lightweight
An acrylic sheet of the same size and volume weighs half as much as glass. When it comes to significant installations, weight is the determining issue. Consider using it in the front of a structure; when Acrylic is selected as the overall weight, the framework must support the least weight, making it more dependable and more straightforward to construct.
Acrylic molding is incredibly lightweight compared to glass and other polymers. Acrylic materials can be mounted where glass or heavier items are problematic.
- Weather and Heat Resistant
All the Acrylic is waterproof. You can count on it to entirely keep you and the items dry. Acrylic creates an excellent external shell for many objects due to its waterproof nature.
Another aspect of the widespread use of Acrylic plastic sheets is their resilience to heat. If you use a regular plastic sheet, they can harden and shatter after a few years. On the other hand, Acrylic sheets may persist for several decades before needing to be replaced. They are ideal for tight fitting and sealing since they have a low expansion index.
- Ease of Plastic Injection Molding
Acrylic is a sturdy, stiff, and optically transparent material with the ability to withstand high temperatures up to a point, which makes it easy to thermoform. It can also be fabricated easily and bonds well with solvents as well as adhesives. Its high tensile strength, weathering abilities, dimensional stability, and low mold shrinkage ensure that it can be used in injection molding with ease.
- Dimensional Stability
Due to its ideal physical qualities, good esthetics, and relatively low toxicity compared to other plastic materials, polymethyl methacrylate (PMMA) is the only polymer material successfully used in making some special items, such as a denture base.
Both polymerization shrinkage and pressures produced during flask cooling contribute to the plastic product’s dimensional alterations. However, because of the reduction in the molecular weight of the resultant polymer chain, differences in the curing procedure could not significantly impact the pattern of dimensional Acrylic resin behavior.
- Non-toxic Composition
Acrylic may benefit the users by not containing or releasing Bisphenol A (BPA) during hydrolysis. Although there is conflicting evidence on the toxicity of BPA, the similar material Polycarbonate includes it, while Acrylic does not have the same problems.
The non-toxic nature of acrylic ensures that it can be used to manufacture domestic as well as industrial goods that come in prolonged contact with humans. Lenses, paint, acrylic nails, medical devices, device screens, windows, and kitchen equipment are some everyday use items that may contain acrylic in them.
Some Disadvantages of Acrylic
Acrylic injection molding plastic is a man-made substance that is first formed into a liquid or powder before being used as plastic. While Acrylic plastics offer many benefits, there are certain disadvantages associated with their production and use.
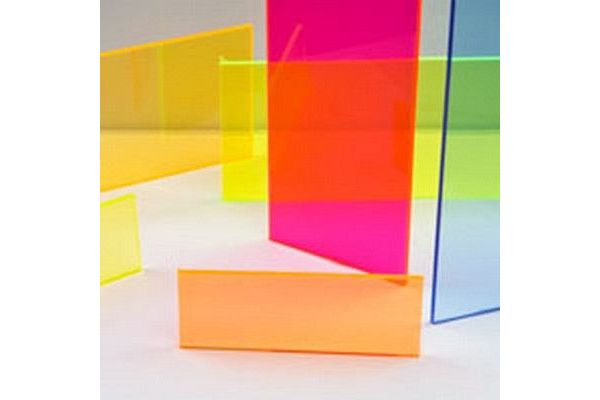
Acrylic has the drawback of scratching more easily than glass. It will thus require additional caution when being handled to slow the pace of scratching. However, it is simple for you to return it to its former shape if it unintentionally receives any scratches. To remove the scratches, all you have to do is polish the Acrylic.
- Not Resistant to Heat
The melting point of Acrylic is relatively low—160 degrees Celsius. Given that the summer heat won’t become much hotter than it already is, this is sufficient for everyday use, but this melting temperature may be too low for technical uses.
Acrylic injection molding is made simpler by the low glass transition temperature. However, it does have a drawback in terms of applicability. The glass transition temperature of Acrylic ranges from 85 to 150 degrees C. Depending on the grade, the exact value. It is as opposed to glass, which can tolerate temperatures up to 1000 degrees Celsius.
Under these circumstances, the silica-based glass would stay hard, whereas Acrylic would soften. As a result, Acrylic cannot be heated to disinfect it. This implies that Acrylic injection molding uses different sanitation techniques. Compared to heat, these cost more.
- Low Scratch Resistance
Acrylic’s poor scratch resistance is one of its worst flaws. Because of this, it’s essential to handle finished Acrylic pieces carefully to prevent leaving marks on the clear plastic. The Acrylic material you buy will often be covered in a protective coating to prevent scratches.
For applications that do need extra durability, such as public installations, there are scratch-resistant Acrylics on the market; however, as one might assume, they are more expensive than standard Acrylic material.
If you unintentionally scratched Acrylic injection molding, you may rapidly remove the damage with plastic polish solutions.
The Process of Acrylic Injection Molding
The most famous production method for creating plastic parts is injection molding. Injection molding is used to create a vast range of items, each with a unique size, level of intricacy, and use. A mold, raw plastic material, and an injection molding machine are required for the injection molding process.
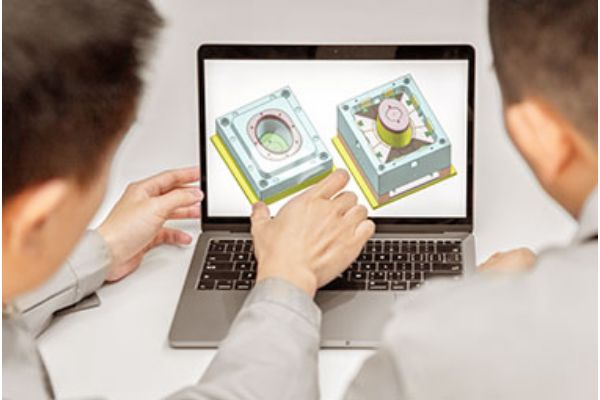
The plastic is melted and injected into the mold in the injection molding machine, which cools and solidifies to form the finished object. Let’s discuss the step-by-step guide to Acrylic injection molding.
- Prepare the Acrylic Injection Mold
The process of designing the molds is a crucial one and it involves the use of computer-aided design (CAD) software. Using the standard machining process, the designs produced by the CAD as well as CAM software are loaded into the CNC machines and constructed using 3D printing.
Renowned molding factories like FOW Mould have the above-mentioned practices set properly.
- Clamp the Acrylic Injection Mold
The clamping mechanism must first firmly seal the two mold halves before the material can be injected into the mold. One half of the mold is let slide while the other halves are each coupled to the injection molding machine.
The clamping device is hydraulically operated and forces the mold halves together with enough force to maintain the mold shut while the material is injected.
Depending on the machine, larger machines (those with more substantial clamping pressures) will take longer to seal and clamp the mold. The machine’s dry cycle time can be used to estimate this period.
- Inject Acrylic into the Mold
The raw plastic material is supplied into the injection molding machine and moved toward the mold by the injection unit, typically in the form of pellets. The material gets melted during this procedure due to pressure and heat. The fast Acrylic injected molten plastic packs and retained the material due to the pressure rise in the mold.
The shot is the term used to describe the volume of substance injected. Due to the complicated and erratic flow of the molten plastic into the mold, it is challenging to determine the injection time precisely. The shot volume, injection pressure, and power can predict the injection time.
- Cool the Acrylic and Open the Mold
As soon as the molten plastic within the mold makes contact with the internal mold surfaces, it starts to cool. The plastic will harden into the desired part’s shape as it cools. The portion might, however, experience some shrinking while cooling.
During the injection step, the material is packed to prevent apparent shrinkage and allow more material to flow into the mold. Unable to be opened until the requisite cooling period has passed is the mold. Several plastic thermodynamic characteristics and the component’s maximum wall thickness can be used to predict the cooling time.
- Eject the Acrylic Part
The ejection mechanism, which is linked to the back half of the mold, may expel the cooled item from the mold once enough time has passed. A device is utilized to force the part out of the mold when it is opened. Because the object shrinks and sticks to the mold during cooling, force must be used to remove it from the mold.
Before the injection of the material, a mold release agent can be sprayed over the surfaces of the mold cavity to make it easier for the component to be ejected. The machine’s dry cycle time may be used to estimate the amount needed to open the mold and eject the component, which should also account for the time it takes for the part to release itself from the mold.
The mold can be clamped shut so the subsequent injection can occur after the extracted part.
- Subsequent Finishing Process
The quality of the end product is significantly influenced by the design of the mold. The molded type determines the product’s strength, durability, form, and size. The mold must be robust to survive the pressures involved in the injection process.
Additionally, the polymer needs to move freely along the mold. The mold needs to be precisely planned to permit heat flow and regulate the cooling process.
Following the injection molding cycle, post-processing is frequently necessary. The substance in the mold’s channels will harden while still being bonded to the component during cooling. Removing this extra material and any flash from the component is necessary, usually using cutters.
For some materials, such as thermoplastics, the leftover trimmings can be recycled by being fed into a plastic grinder, also known as a regrind machine or granulator, which turns the leftover trimmings into pellets. Regrind must be blended with raw material in the correct regrind ratio due to some degradation of the material’s characteristics to be reused in the injection molding process.
A Trustworthy Acrylic Injection Molding Services Provider
This high-tech company called FOW Mould was founded in 1978 to offer affordable manufacturing solutions. They develop and produce premium quality mold in sectors such as bucket, warehouse & storage, baby products, home appliances, and automobiles, working closely with clients worldwide.
With 40 years of mold-making experience, the company’s global business network includes Russia, Europe, and the United States. They provide a wide selection of injection molding services at FOW Mould. Do you require creating a product design or a prototype to determine its viability? They are capable of meeting the demands.
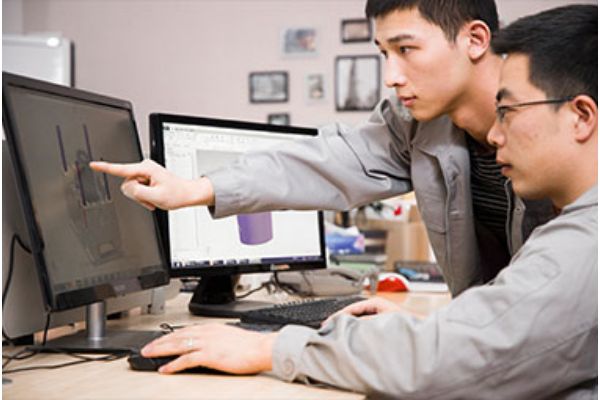
You can rely on them to provide precisely crafted, high-quality molds in only several days. They have adequate injection equipment on hand to complete the requirements quickly.
They give you innovative and affordable injection molding solutions by fusing this wealth of knowledge with the most recent technological advancements in the market. They also employ various designers and engineers with various industry specialties.
Advantages of FOW Mould Acrylic Injection Molding Services are:
- Quick Prototyping
The development of part designs may be completed more quickly with the support of quick prototype production. Additionally, it provides quick feedback on their feasibility. To help us provide the prototypes in the shortest amount of time feasible, they have invested in the best 3D printers and CNC equipment available.
- Scalability
Over hundreds of set molds may be produced annually by FOW Mould. FOW Mould has also built a trusted network of collaborators who collaborate with them and expand the manufacturing scale. Because they know that their clients service a variety of market sizes, they can easily accept low-volume requests.
- Excellent Quality
They work with a variety of materials that come solely from trusted providers. These processes are all carried out under the direction of professionals who adhere to high-quality standards. Only once parts and prototypes fulfill the quality management criteria are sent to clients.
- High accuracy
Fortunately, you won’t ever have to worry about accuracy as a client of theirs. The tolerance for CNC machines is around +/-0.02mm, but the tolerance for high-speed CNC models is +/-0.002mm. This complies with the advised worldwide business standards.
Conclusion
Acrylic is a multifunctional thermoplastic with many uses owing to its impressive mechanical, thermal, and optical properties. It is widely employed in several industries across all sectors and poses no harm to users due to its non-toxic nature. With the help of injection molding, acrylic can be molded into products that utilize its properties more and more creatively.
FOW Mould has expertise working with a large number of resins. On request, they explore unusual alternatives for the clients and provide a wide range of material options. Depending on the product amount and delivery date, FOW Mould can deploy numerous Acrylic injection molding to satisfy demand. Contact FOW Mould now.