Acrylonitrile Butadiene Styrene, commonly known as ABS, is one of the mainstream materials used in the 3D printing domain employing Fused Deposition Modeling (FDM) technology.
Its multifunctional characteristics make it suitable for producing a wide range of common products, from mechanical parts to LEGO bricks.
The emergence of PETG has disrupted this filament’s dominance in the industry, quickly becoming a versatile choice for creators.
But how do we differentiate between ABS and PETG materials?In the following discussion, we will delve into a comprehensive comparison of the capabilities of PETG vs ABS to uncover the essence of their differences.
An Introduction Of PETG and ABS
ABS (Acrylonitrile Butadiene Styrene) and PETG (Polyethylene Terephthalate Glycol) are two popular thermoplastic materials widely used in 3D printing. Each material boasts unique properties that make it suitable for various applications.
ABS is a thermoplastic polymer commonly known for its durability and heat resistance, making it ideal for creating mechanical parts and components that need to withstand high stress and temperatures. ABS parts are known for their strength, durability, and suitability for various mechanical applications, making them ideal for producing functional and aesthetically appealing components.
On the other hand, PETG is a thermoplastic polyester that offers excellent layer adhesion and chemical resistance, ensuring strong and durable prints. Understanding the distinct characteristics of ABS and PETG is crucial for selecting the right material for your specific project needs.
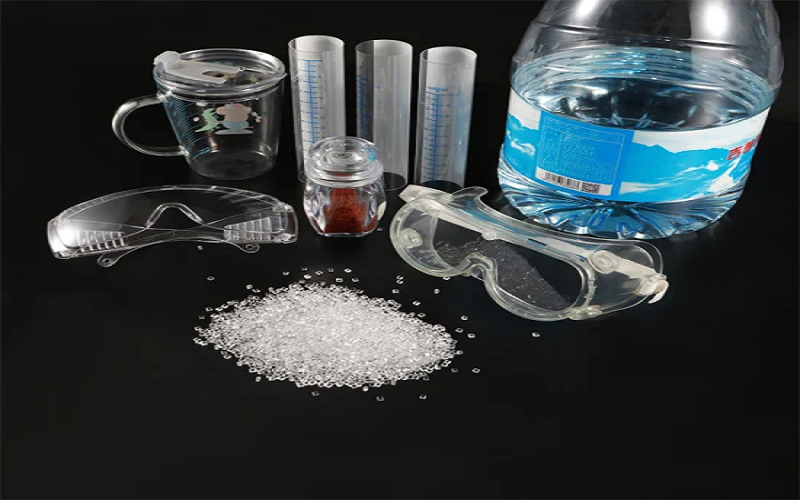
Overview of 3D Printing Materials
3D printing materials are a crucial aspect of the additive manufacturing process.
The choice of material can significantly impact the final product’s properties, such as strength, durability, and appearance.
PETG and ABS are two of the most popular materials used in 3D printing due to their unique characteristics and versatility.
PETG is known for its excellent layer adhesion and chemical resistance, making it ideal for applications requiring strong and durable prints. Its lower glass transition temperature allows for easier printing, while still providing sufficient strength for many projects.
ABS, on the other hand, is celebrated for its durability and heat resistance, making it suitable for creating mechanical parts and components that need to withstand high stress and temperatures. However, ABS can be more challenging to print due to its tendency to warp and shrink.
Understanding the properties and characteristics of different 3D printing materials is essential for selecting the right material for your specific project needs. By choosing the appropriate material, you can achieve the desired balance of strength, durability, and appearance in your 3D printed objects.
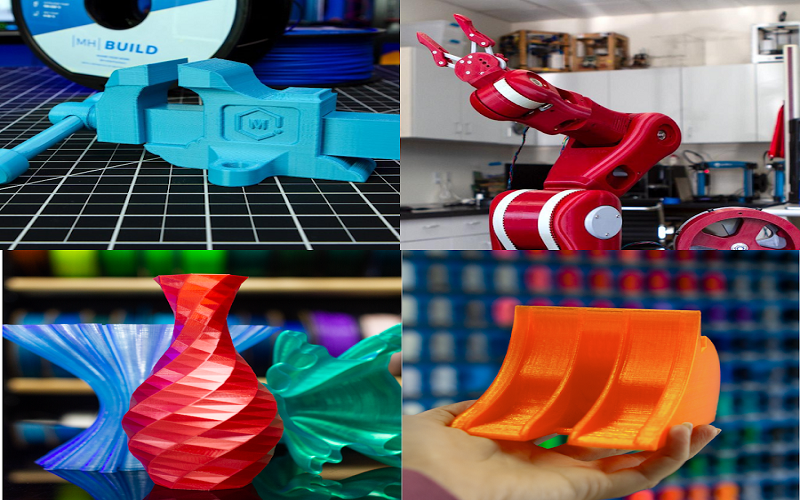
PETG vs ABS:Performance Description
When evaluating performance, both ABS and PETG exhibit distinct strengths and weaknesses.
PETG is recognized for its excellent optical properties as a non-crystalline or low-crystalline material, boasting high surface glossiness and transparency, making it ideal for manufacturing thick-walled containers or sheets.
It features chemical resistance, impact resistance, and ease of processing, finding widespread use in construction, medical, and industrial fields.
PETG has become one of the most popular building materials on the market, replacing traditional materials like PVC and PC.
On the other hand, ABS plastic, known for its ivory-colored translucency in granular or powder form, is renowned for its high strength and rigidity.
It has a thermal deformation temperature range of 93 to 118°C and can be used within temperatures of -40 to 100°C, exhibiting good electrical insulation.
However, ABS is sensitive to ketones, aldehydes, and chlorinated hydrocarbons, and susceptible to stress cracking when exposed to ice acetic acid and vegetable oils.
Here are the general performance metrics for both materials:
Properties | PETG | ABS |
Density(g/cm3) | 1.29-1.4 | 1.01-1.07 |
Shrinkage rate(%) | 0.2-0.5 | 0.5-0.8 |
Tensile Strength (MPa) | 50-75 | 40-52 |
Melting Point (℃) | 220-260 | 190-240 |
Glass Transition Temperature (℃) | 80-90 | 105 |
PETG vs ABS:Processing Methods
PETG plastic is suitable for traditional forming methods such as extrusion molding, injection molding, blow molding, and thermoforming, making it widely applicable for the production of sheets, films, high-performance shrink films, bottles, and profiles.
Additionally, PETG meets the U.S. FDA standards for food container storage, making it a safe and reliable material choice for food packaging and medical health sectors.
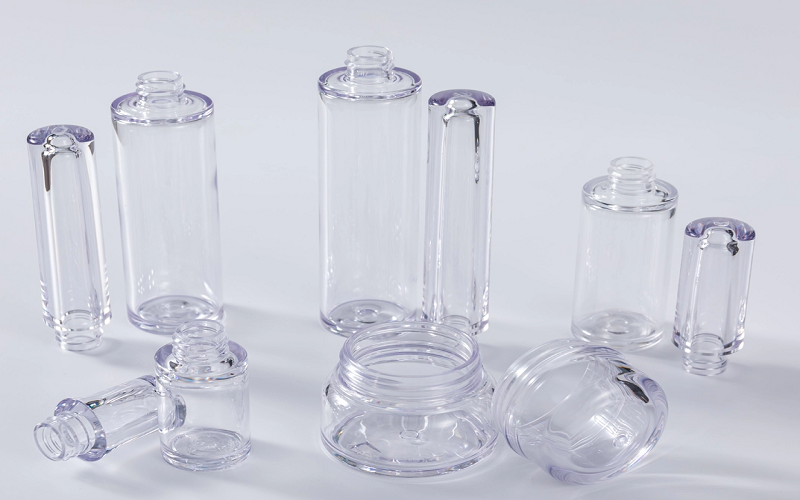
ABS is widely utilized in injection molding, one of its most prevalent processing techniques, allowing for the efficient creation of intricate, high-precision parts with consistent performance.
This processing benefit, paired with its superior mechanical properties and heat resistance, makes ABS injection molding components a staple in industries such as automotive, electronics, and toy production.
When 3D printing with ABS, achieving strong layer adhesion is essential. This requires higher temperatures to properly bond layers and avoid problems like weak interlayer fusion. Both ABS and PETG are prominent in the 3D printing realm.
As noted in comparisons like PLA vs PETG, PETG filament stands out for its excellent printability, delivering glossy, robust prints with smooth surfaces that resist breaking and offer a translucent finish.
In contrast, ABS is typically processed via FDM , where it’s melted and extruded through a fine nozzle, forming designs in 250-micron layers.
These layer lines can influence both the visual appeal and structural integrity of ABS prints, but post-processing methods—such as sanding or acetone vapor smoothing—can eliminate these lines, significantly improving the final quality.
ABS-printed objects tend to offer slightly greater strength, flexibility, and longevity, making it an ideal choice for prototyping. Its versatility shines in post-print treatments like machining, sanding, gluing, and painting, enhancing its suitability for a wide range of applications.
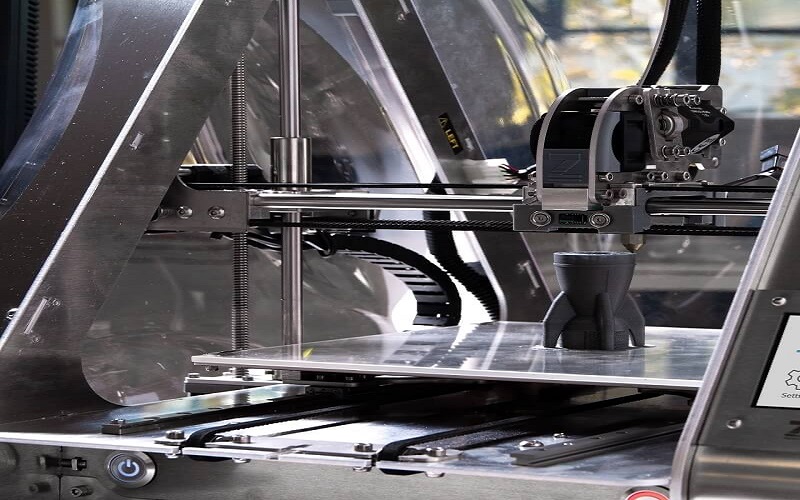
PETG vs ABS:Pros and Cons
In the above, PETG and ABS each demonstrate unique properties and application potential, which allows us to compare the advantages and disadvantages of these two materials in depth.
Advantages of PETG
Excellent Mechanical Properties: PETG exhibits outstanding wear resistance and impact resistance, maintaining integrity under high strength and pressure environments for extended periods.
Environmentally Friendly: It is one of the few environmentally friendly materials available (with certifications like SGS, FDA, MSDN), producing only CO2 and water upon combustion.
High Transparency: PETG boasts excellent transparency and light transmission, suitable for visually appealing applications.
Fire Resistance: PETG has a high level of fire resistance, capable of achieving a B1 fire rating or higher.
Disadvantages of PETG
In addition to the numerous advantages mentioned above, PETG also has some shortcomings.
For instance, PETG has a lower heat distortion temperature, which may lead to deformation at higher temperatures. Furthermore, the material itself is not very hard, making it susceptible to scratches, and it cannot withstand heavy loads, thus requiring careful consideration during use.
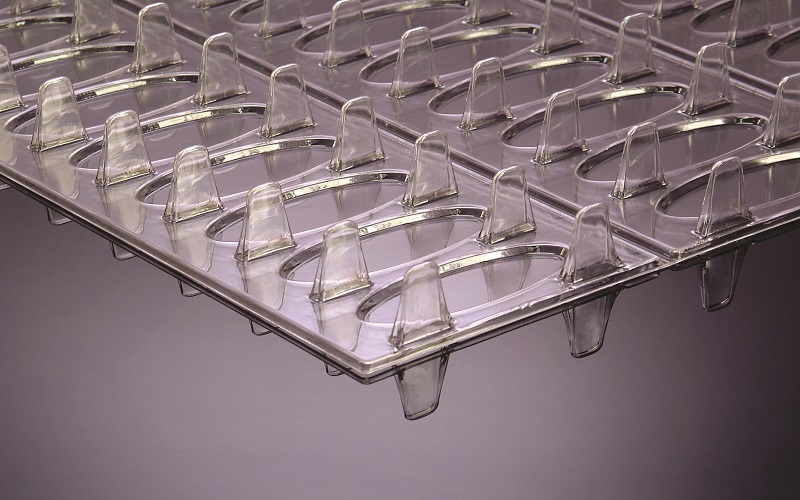
Advantages of ABS
Impact Resistance: ABS plastic has good abrasion resistance and dimensional stability, along with oil resistance, making it suitable for bearings under medium loads and at low speeds.
Electrical Insulation: ABS plastic exhibits good electrical insulation properties that are unaffected by temperature, humidity, and frequency, allowing its use in most environments.
Low-Temperature Resistance: ABS shows certain toughness at -40°C and can be used within a temperature range of -40 to 100°C.
Excellent Surface Finish: ABS products have a smooth surface that is easy to paint or bond, enhancing aesthetic appeal.
Disadvantages of ABS
During printing and melting, ABS produces strong fumes accompanied by an unpleasant odor.
Inhalation in poorly ventilated areas can be harmful to human health, so proper ventilation is necessary during processing.
Additionally, ABS has poor weatherability and easily degrades under the influence of ultraviolet light.
After six months outdoors, its impact strength can decrease by half.
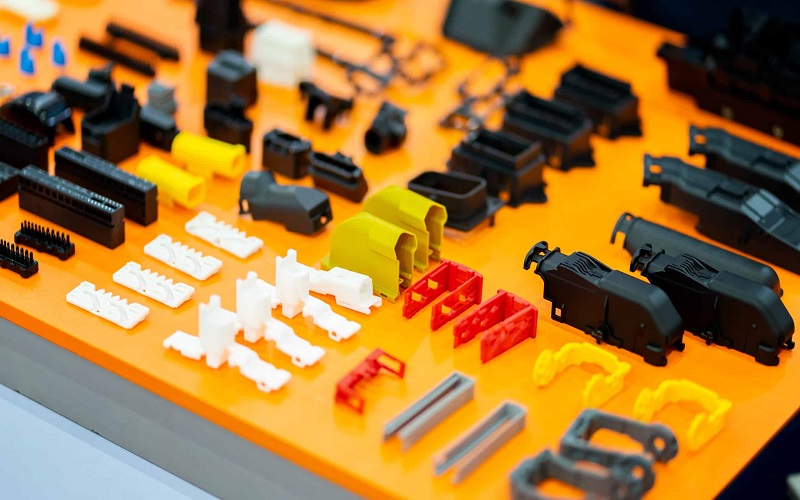
Safety and Handling
When working with ABS and PETG, it’s essential to ensure proper safety and handling procedures.
ABS emits volatile organic compounds (VOCs) and styrene, a potentially harmful chemical, when heated. Proper ventilation is necessary when printing with ABS to avoid inhaling these fumes.
PETG, on the other hand, is generally considered to produce fewer harmful fumes. However, it’s still important to ensure proper ventilation and follow safety guidelines when handling PETG. Both materials can be recycled, but PETG has a higher recycling rate due to its use in food packaging and other consumer products.
Practical Applications Of PETG and ABS
Due to the excellent chemical stability and biocompatibility of PETG copolyester, it is widely used in manufacturing medical devices and packaging, such as surgical instruments, infusion bottles, and medical syringes.
Transparent household items, furniture accessories, and bathroom fixtures also benefit from the use of PETG plastic. Its clarity creates a minimalist, stylish appearance while offering durability and impact resistance for a better user experience.
Moreover, PETG copolyester meets hygiene standards and is harmless to food safety, making it an ideal choice for manufacturing transparent food packaging due to its outstanding transparency.
PETG’s resistance to UV light makes it suitable for outdoor applications, ensuring that it won’t degrade quickly when exposed to sunlight, which is crucial for items like garden tools and furniture.
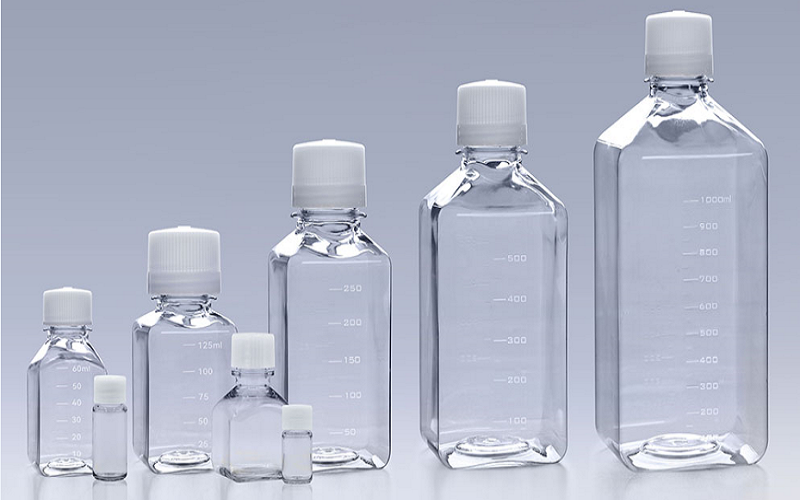
As for ABS material, its main application fields are in the automotive components and electrical industries.
Its strength and heat resistance are broadly utilized in the automotive industry for dashboards, interior trims, and exterior parts.
Thanks to the electrical insulation of ABS plastic, it is used to manufacture casings, plugs, switches, and circuit board supports for electronic devices.
This ensures safety while providing sufficient mechanical strength and wear resistance to protect sensitive electronic components.
Furthermore, ABS’s ease of processing and molding makes it widely used in consumer products like toys (LEGO bricks are a classic example), household appliances, sports equipment, and office supplies.
Its ease of painting and adhesiveness also grant it greater design flexibility in terms of aesthetics and functionality.
When it comes to 3D printing, specific tools and techniques, such as using Kapton tape as a build surface, are essential to enhance adhesion and reduce warping during the print ABS process.
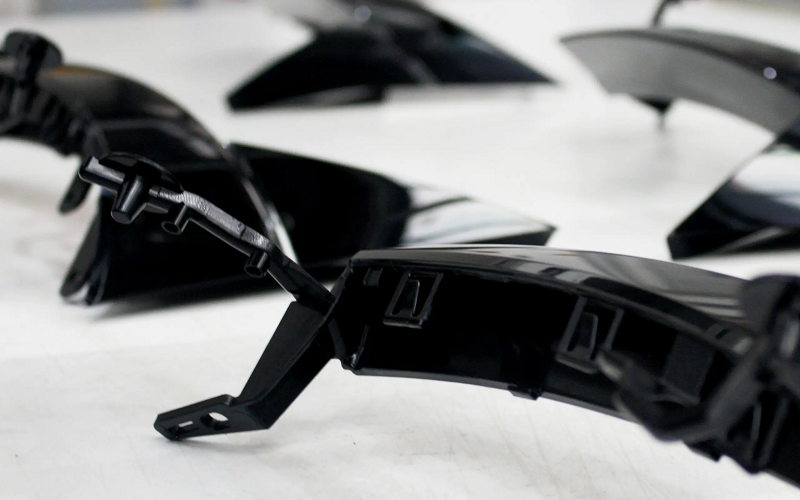
Cost, Availability, and Alternatives
The cost and availability of PETG and ABS can vary depending on the supplier and location.
Generally, ABS is less expensive than PETG, with prices ranging from $20 to $30 per kilogram. PETG, on the other hand, can cost between $30 to $50 per kilogram. Both materials are widely available from various suppliers, including online retailers and local hobby stores.
When considering alternatives to PETG and ABS, several options are available. PLA is a biodegradable and eco-friendly material that is suitable for printing prototypes and models. It is easy to print with and produces minimal warping, making it a popular choice for beginners.
Nylon is a strong and flexible material that is often used for creating mechanical parts. Its durability and resistance to wear make it ideal for functional prototypes and end-use parts.
TPU (Thermoplastic Polyurethane) is a flexible and highly elastic material that is commonly used for printing wearable devices and phone cases. Its flexibility and impact resistance make it suitable for applications requiring a soft touch and high durability.
When choosing between PETG and ABS, it is essential to consider the specific needs and requirements of the project. Factors such as durability, heat resistance, chemical resistance, and print quality should be taken into account.
Additionally, the cost and availability of the materials should be considered, as well as the availability of alternatives. By understanding the properties and characteristics of PETG and ABS, users can make informed decisions and achieve optimal results in their 3D printing projects.
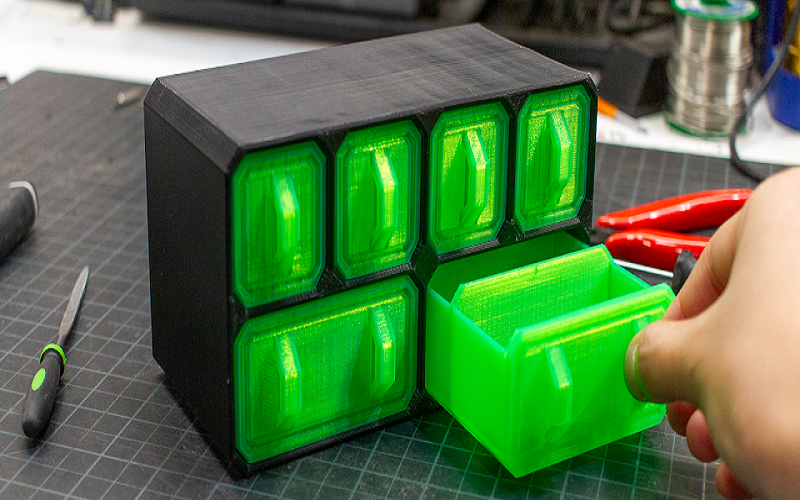
How To Choose Between PETG And ABS?
When we need to choose between PETG and ABS materials for our project, we should evaluate from the following perspectives:
1.Mechanical Performance and Durability
PETG is known for its excellent toughness and impact resistance, making it suitable for products requiring durability and flexibility.
ABS has higher strength and rigidity, capable of withstanding high stress or strain, ideal for making general mechanical parts and wear-resistant components.
2.3D Printing Characteristics
In 3D printing, ABS tends to warp during cooling, making it challenging to print large parts without adequate temperature control and a heated print bed.
Compared to ABS, PETG has lower viscosity and excellent adhesion properties, resulting in parts with smooth surfaces and rich details, making it an excellent choice for creating components, decorative items, and artworks.
3.Environmental Impact
PETG is considered an environmentally friendly material due to its recyclability and lower emission of harmful gases.
Although ABS can be recycled, its raw materials come from fossil fuels, which can cause environmental pollution if not managed properly.
In summary, both PETG and ABS have their unique features.
The final material choice should be based on a comprehensive consideration of the product performance, application, and processing method required by the project.
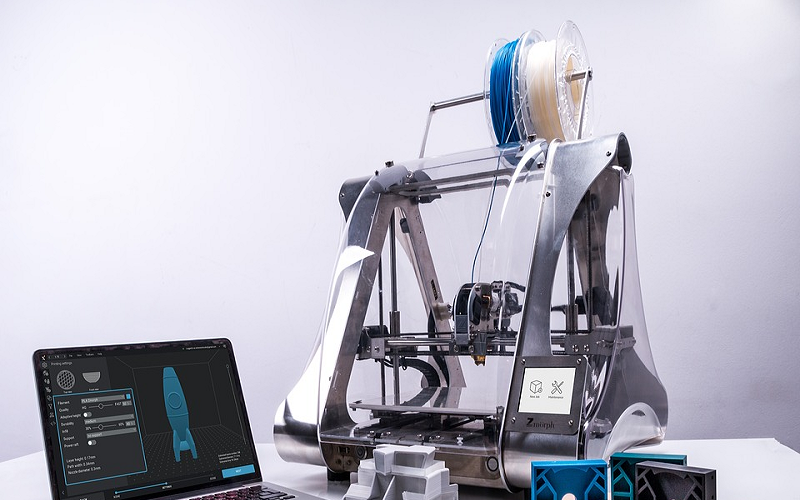
Conclusion
In conclusion, ABS and PETG are two popular thermoplastic materials used in 3D printing, each with unique properties and applications.
ABS offers durability and heat resistance, making it suitable for tough projects, while PETG provides flexibility and ease of printing, making it a good choice for projects requiring these characteristics.
By understanding the properties and applications of ABS and PETG, you can make informed decisions when selecting the right material for your 3D printing project.
Remember to follow proper safety and handling procedures, and ensure proper layer adhesion and post-processing techniques to achieve high-quality prints.