In the realm of transparent plastics, PET and PETG hold unique positions.
Although their names differ by only a single letter, their properties and application areas are vastly different.
These significant differences mean that each plays a distinct role in meeting various industrial requirements and consumer preferences.
This article aims to delve into the differences between PET and PETG, assisting readers in leveraging the advantages of these materials more wisely to meet the specific needs of their projects.
What Is PET?
PET, short for Polyethylene Terephthalate, is designated as number 1 in the plastic recycling symbols.
It is a polymer created through the esterification and polycondensation of ethylene glycol and terephthalic acid, appearing milky white or light yellow with a smooth and glossy surface.
Thanks to its lightweight, impermeable, water-resistant, and acid-alkali resistant properties, PET is often used to manufacture mineral water bottles, beverage containers, and other packaging, serving as a durable alternative to glass in food packaging materials.
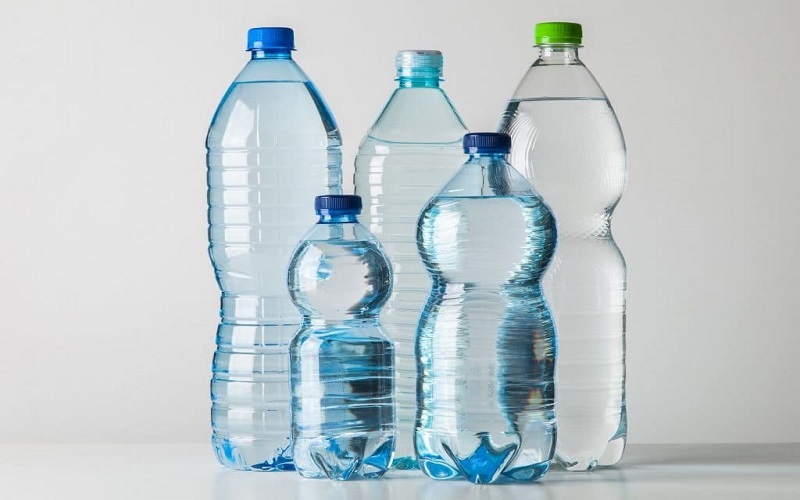
What Is PETG?
PETG is a variant of PET, known as Polyethylene Terephthalate Glycol-1,4-Cyclohexanedimethanol Ester, a transparent, non-crystalline copolyester.
It is synthesized by replacing part of the ethylene glycol in PET with Cyclohexanedimethanol (CHDM), making PETG a non-crystalline copolyester.
Consequently, PETG’s properties differ significantly from those of PET.
Thanks to its excellent thermal characteristics and semi-rigid physical strength, it is highly suitable for processing and injection molding.
The end products are highly transparent, making PETG widely used in clear plastic sheets and cosmetic bottles.
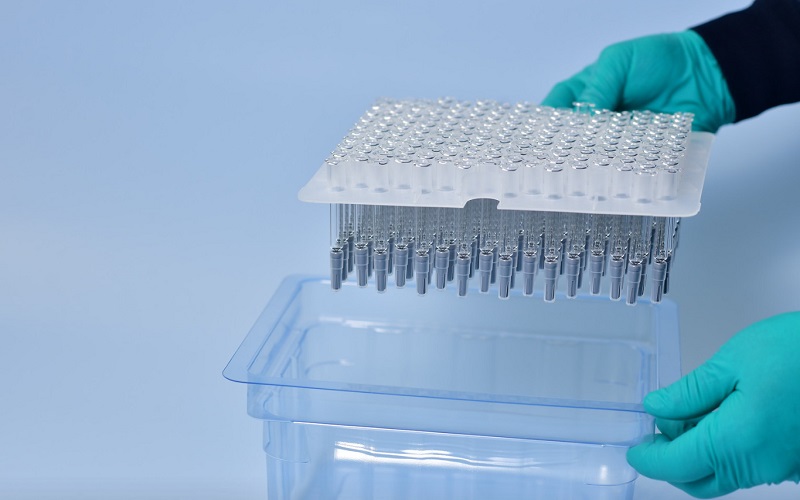
Main Properties of PET & PETG
PET exhibits the highest toughness among thermoplastic materials, being non-toxic with a low rate of water absorption, and resistant to weak acids and organic solvents, yet it is not suitable for prolonged soaking in hot water or contact with alkaline substances.
Despite being a polar polymer, PET possesses excellent electrical insulation properties, maintaining its performance even at high frequencies.
However, its poor resistance to corona discharge limits its application in high-voltage insulation.
By substituting ethylene glycol monomers in the structure of PET, the melting point of copolyesters is reduced, the glass transition temperature is increased, and crystallinity is decreased, resulting in PETG’s exceptionally high transparency.
The ethylene glycol and 1,4-cyclohexanedimethanol components in PETG’s structure provide enhanced flexibility and elasticity to the molecular chains, endowing PETG with superior physical properties.
Furthermore, PETG exhibits good chemical resistance, for example, resistance to household detergents, dilute acids, and alkalis.
It also has a strong barrier against oxygen and carbon dioxide.
The melting point of PETG is relatively low, only between 180°C and 200°C, ensuring its excellent processability and making it an ideal choice for a wide range of applications.
The following is a performance comparison chart of PET vs PETG:
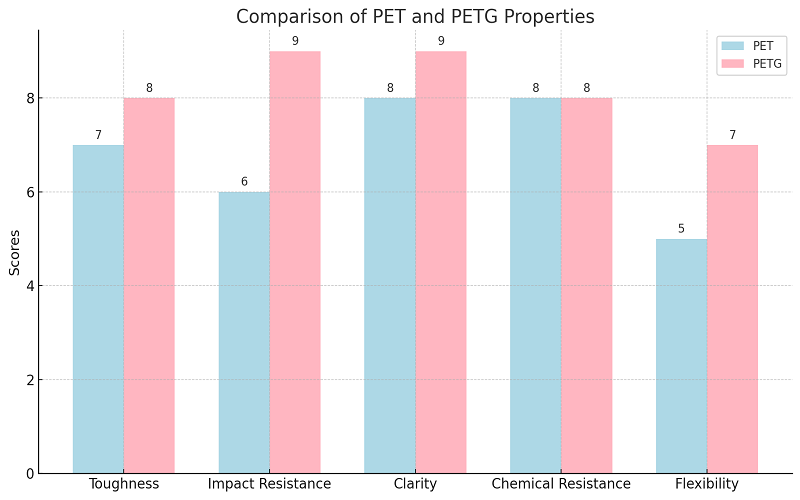
PET vs PETG:Application
PET and PETG hold crucial positions as materials in the food packaging industry, particularly in the production of transparent containers such as beer bottles, edible oil bottles, and beverage bottles.
However, each material also showcases unique advantages in their respective domains.
PET, especially when used to produce polyester fibers, finds widespread application in clothing, household textiles (such as bedding and curtains), and industrial products (like conveyor belts and safety belts), demonstrating its versatility.
In the realms of imaging and packaging, PET is the plastic material of choice due to its exceptional physical performance and chemical stability.
Furthermore, PET reinforced with glass fibers is utilized in the electronics, electrical, and automotive industries to manufacture various components and casings, highlighting its value in technical applications.
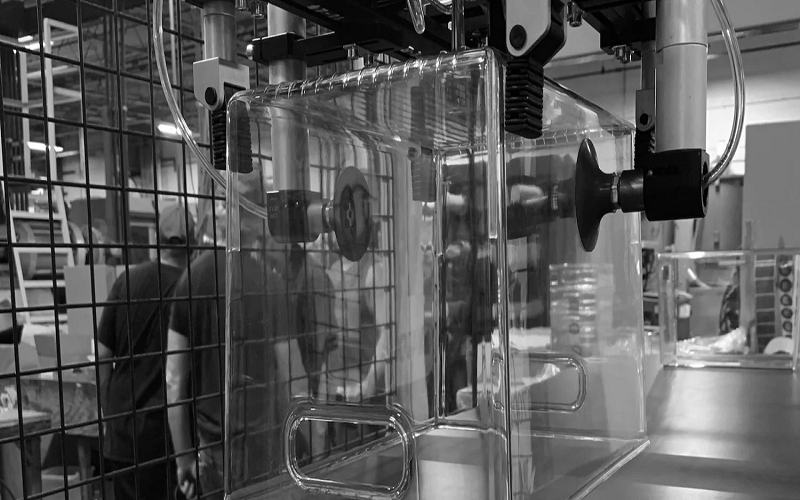
In contrast to PET, the application of PETG injection molding products is aimed at medical devices and household goods, and it sees broad application in building decoration and display materials as well.
In countries pursuing environmental sustainability, PETG serves as a more eco-friendly option, replacing PVC in the manufacture of card materials like the second-generation ID cards.
Additionally, as one of the few transparent materials for 3D printing, PETG offers nearly odorless printing and PLA+-like printability, providing 3D printing enthusiasts with more possibilities.
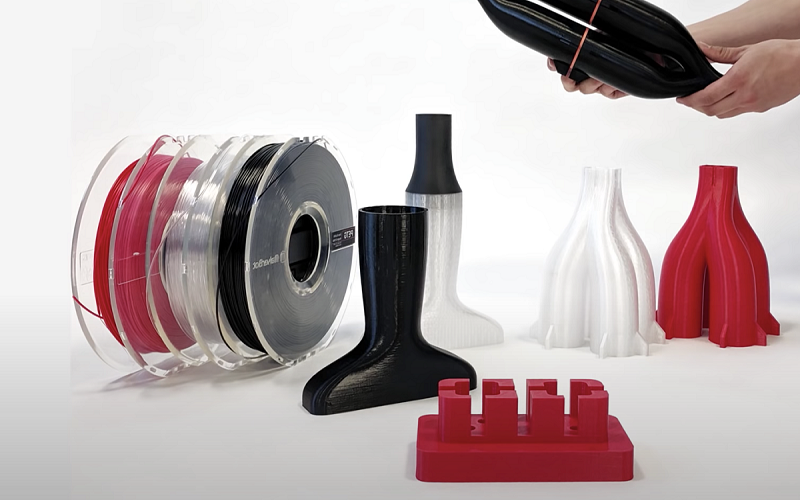
These applications not only reflect the multifunctionality of PET and PETG but also how they meet the unique requirements of specific sectors.
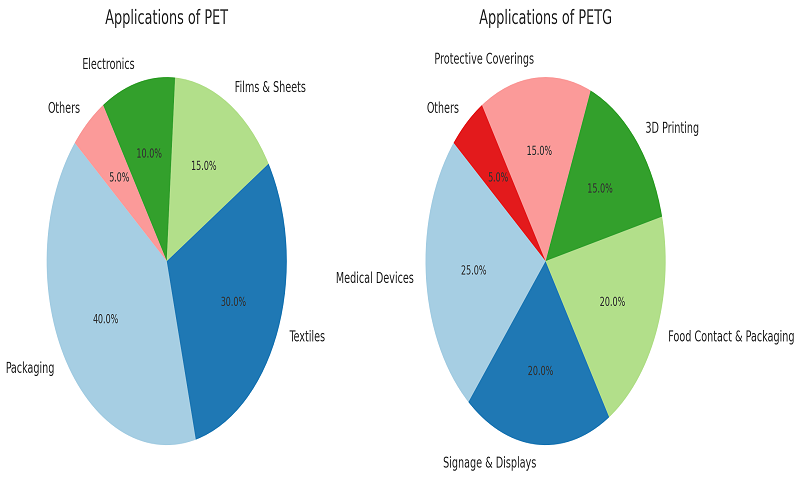
PET vs PETG:Security Perspective
In every corner of our daily lives, the presence of a “1” inside a triangular symbol at the bottom of plastic bottles, accompanied by the letters “PET” or “PETG,” has become a familiar sight.
As public awareness of health increases and concerns over the safety of plastic products grow, questions such as “Is PET plastic safe?” have become increasingly common.
It has been proven that PET plastic is safe. This material is made from polyethylene terephthalate and does not contain harmful organic solvents or heavy metals that could pose a risk to human health.
Thanks to its lightweight, transparency, and excellent chemical resistance, PET injection molding product is extensively used in the packaging of food and beverages.
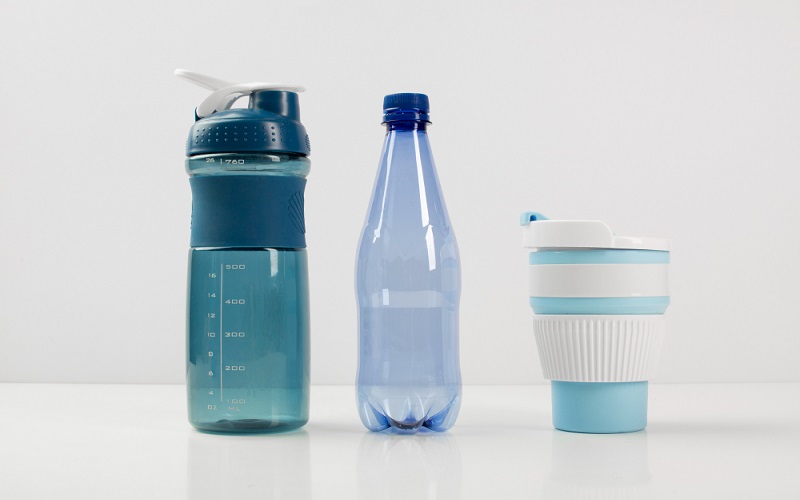
PETG is obtained by modifying PET with the addition of glycol, which enhances its toughness and impact resistance while maintaining PET’s excellent transparency and chemical stability.
These unique properties make PETG a popular choice for medical devices, food packaging, and other applications that require high transparency and chemical resistance.
Both materials have been approved by authoritative bodies, including the U.S. FDA, and are considered safe food-grade plastics that can be confidently used under normal conditions.
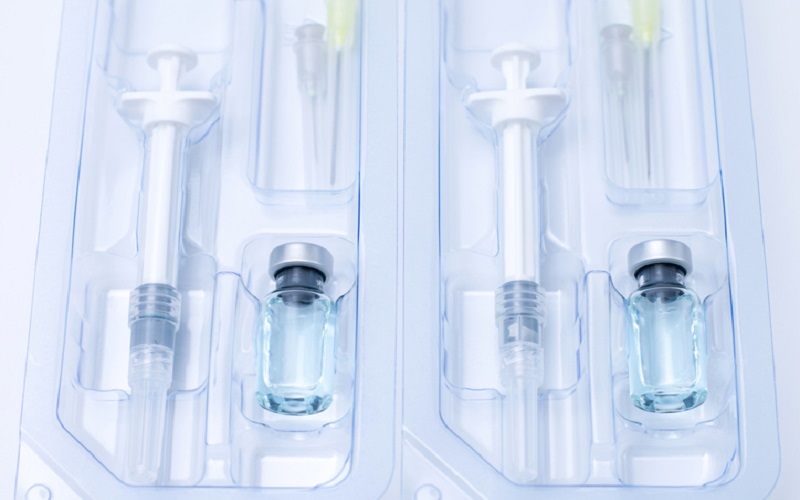
Recycling of PET And PETG
As the concept of sustainable development gains deeper traction, the importance placed on the recycling and processing of plastics has significantly increased.
PET stands out as one of the most recycled plastics globally, particularly those used in beverage bottles and food packaging.
This high rate of recycling is attributed to the well-established global recycling systems in place for PET.
Once recycled, PET can be transformed into new bottles or other plastic products, such as fibers for creating carpets or clothing, showcasing its versatility and recyclability.
On the other hand, while PETG is also recyclable, it tends to have a lower recycling rate and less widespread recycling infrastructure compared to PET.
This discrepancy arises because PETG requires different processing and recycling methods, sometimes necessitating separate collection and handling.
To ensure the effective recycling of both materials, it is advisable to segregate them for recycling and adhere to local recycling guidelines and procedures.
This approach not only facilitates efficient recycling but also supports the broader goal of environmental sustainability.
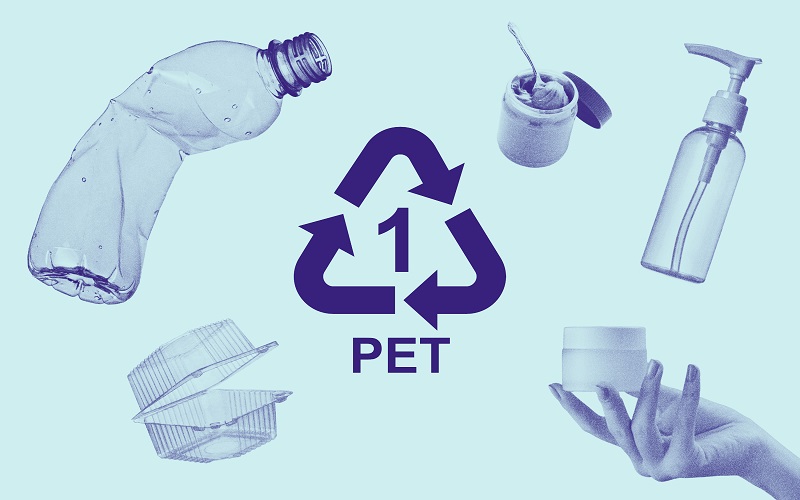
The Differences Between PET And PETG
PET and PETG are thermoplastic polyesters with distinct properties.
PETG outperforms PET in toughness, impact strength, and transparency, making it ideal for medical devices and special packaging.
PETG also shows superior chemical resistance in some cases and is easier to mold due to its lower processing requirements, unlike PET which needs pre-drying.
While PET leads in global recycling rates and application in food packaging and textiles, PETG excels in medical applications, premium packaging, and 3D printing.
The choice between PET and PETG hinges on the specific needs and priorities of the intended application.
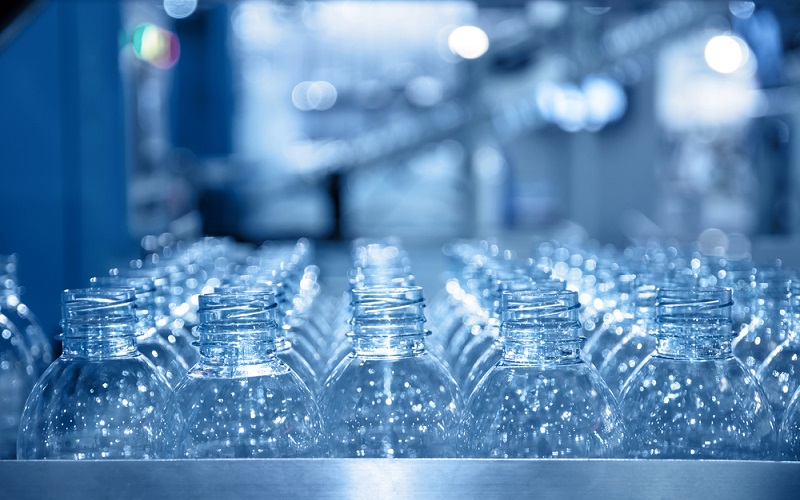