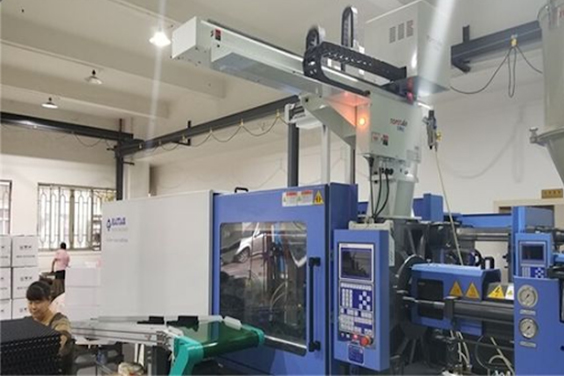
Share :
Share :
Injection molding is a manufacturing process that is highly relied upon by different businesses when it comes to producing their products. There are different aspects to injection molding that you should keep in mind. For instance, there are different types of injection molding including low and high-volume injection molding processes.
These processes come with distinct variations and are designed to feature different advantages when used. For this to be effective you need to work with quality injection molding manufacturers who will ensure that you get the best plastic injection molding service. In this post, we’ll be covering low-volume injection molding and take a deep dive into the different options available.
Low-volume injection molding is also referred to as short-runs and features the fast production of fewer products. The products to be manufactured in this setting will vary from one manufacturer to another. However, the general number that you can expect to be working with is 10,000 products or less.
These numbers are manageable and allow you to invest in products that will allow you to easily break into the market. Low volume injection molding is a great way to test the waters and see how your business idea performs. It will give you the courage to invest in a set number of products without feeling like you’ve invested a huge chunk of your capital. When things work out, you can then invest in more products for your business.
When it comes to the low-volume injection molding manufacturing processes, there are a few steps that will be featured. These are the manufacturing processes you can expect to be featured when working with an injection mold manufacturer. These steps include:
If you want to design a specific mold for your products, working closely with your manufacturer will help you bring this to life. Mold design is an important part of the process especially if you plan to invest in unique product designs. The mold design process is done in any CAD software and is designed to feature specific design rules that you should follow. This is why it is so important to work with qualified designers for this process.
Different printing materials can be used at this stage to give a clear presentation of the mold that has been designed. Working with advanced prototype molding on your molds makes it easier to use in the injection molding process. Once the 3D printing stage is done and the mold has been cured, you can then comfortably integrate it into your manufacturing processes.
For an easier time when working with your mold, you must take the time to polish and assemble it. Assembling your mold will require the use of a metal frame that will act as support for your mold. This supporting frame will help keep your mold strong and avoid any damage that could come from pressure during the manufacturing process.
Once the mold is secured in the metal frames, the next step is to securely clamp the two sides. This will ensure that they are accurately positioned and ready for the injection molding process. This is an important aspect to ensure that is taken care of for accuracy in the design of your products.
The injection process entails molten material that is introduced into the mold to help it take the desired shape. This process may require a few tweaks especially with the injection pressure and temperature. Your manufacturers will ensure that the results meet your desired needs.
As earlier mentioned, low volume injection molding is a process that caters to short runs and small amounts of productions. This is a manufacturing process that comes in handy when looking to invest in a few parts for your products. This is especially the case when investing in product parts that may change or have the potential to be improved over time.
The marketplace is an ever-changing dynamic where product designs continue to evolve changing the customers’ preferences. Additionally, this is a process that is quite useful when looking to test out new products in the market.
It will give you the freedom to experience and see what performs well without putting in too much time and money. If you have been looking for a way to break into a certain product market, low-volume injection molding will make this easier for you.
Now that you have a better understanding of what low-volume injection molding is, let’s take a look at the different benefits that are featured when working with this manufacturing process. This will give you more insight into why this is a great manufacturing process to consider.
There are 2 distinct processes that you can expect to be working with when it comes to low-volume injection molding. This includes injection molding itself and 3D printing. The different processes provide for a smoother production process that you can always rely on. Additionally, this also allows the manufacturer to work on producing quality products that are designed to meet your specific needs.
The materials used when it comes to the molds that will be used in this manufacturing process can vary greatly. Different material options are perfect for this process given that it does not bring too much force on the molds themselves. This goes to show that other cheaper materials can also be used and will withstand the manufacturing process just fine. The best thing is to ensure that you consult with your manufacturer to ensure that your injection molding materials are perfectly in line with your needs.
For most people, when it comes to the cost-saving aspect of this, it comes with different opinions. However, low volume injection molding is a manufacturing process designed to ensure that your manufacturing efforts come in at a more affordable price. It is cheaper compared to other options especially when you are looking to test the market and invest in new products.
Low volume injection molding features a fast turnaround time on all the products that are produced. This allows you to invest in products knowing that they will be delivered to you in the shortest time possible. Low volume injection molding is a worthwhile manufacturing system that will allow you to work on your products with so much ease.
With this manufacturing process, you have the freedom of investing in different designs as you see fit. If one design doesn’t take off in the market, you can then invest in another one to test its performance. This flexibility is not easily found in other production processes and if it is, it comes with a huge investment. Enjoy the flexibility and the ease to experiment that this production process offers. It is designed to be the perfect option for businesses that are working towards finding their go-to products in the market without going all-in with their budget.
Low volume injection molding is a manufacturing process that caters to short runs of about 10,000 products or less. It is a great manufacturing option that is designed to cater to your needs and ensure that you get products that meet your specific requirements.
Overall, the manufacturing process is quite fast and offers great design flexibility when in use. It comes with a variety of benefits that you should keep in mind. If you are looking to get into this, consider working with a reliable low-volume injection molding manufacturer who will cater to all your needs and ensure that you get the best.
Please contact us using the form below or emailing (harry@fowmould.com)