The world of manufacturing is vast, just like the universe itself… okay, maybe not as infinite, but you get my drift. Two shining stars in this expansive universe are injection molding and 3D printing. Now, if you’ve been a part of this universe, you’d know that these two are as different as, say, cookies and cream. Sure, they go great together, but they’re not the same thing.
Injection molding, the traditional manufacturing method, has been around for quite some time. It’s like that old song you always find yourself humming – classic, reliable, and excellent for mass production. On the other hand, we have 3D printing, the cool new kid on the block. This additive manufacturing process has stirred things up in the manufacturing world, giving us the power to create complex parts in the blink of an eye.
Now, you may wonder, “Which one’s better for my project?” We’ve heard you, loud and clear. So, buckle up, folks, as we set off on this journey of exploration – injection molding vs 3D printing.
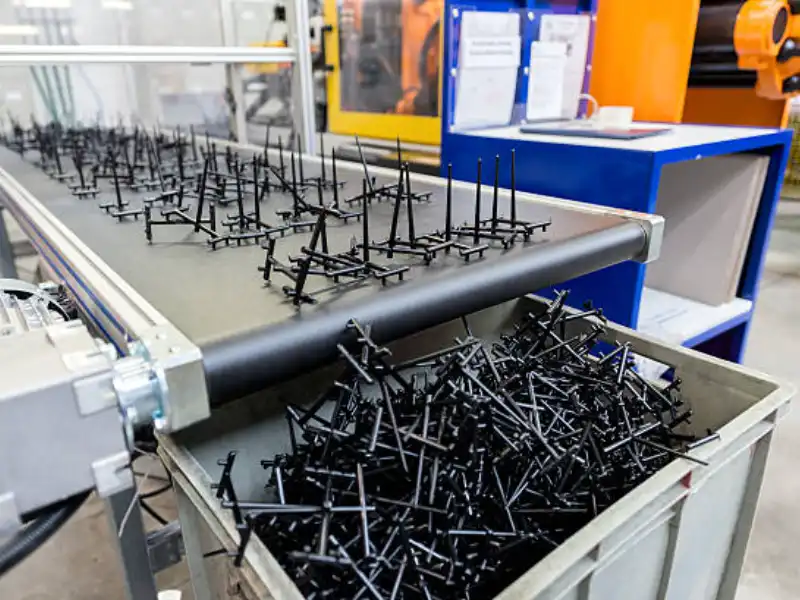
Key Takeaways:
Comparison Terms | Injection Molding | 3D Printing |
Production Volume | High volume production is more cost-effective due to initial high tooling costs. Used for mass producing identical parts. | Ideal for low volume production and prototyping because it has no initial tooling cost. |
Speed | Typically faster due to simultaneous production of parts once mold is created. | Slower process, as items are constructed layer by layer. |
Design Changes | Design changes can be costly and time-consuming because they require modification or recreation of the mold. | Design changes are relatively easy and cost-effective because they only require modifications to the digital model. |
Material Variety | Mostly limited to thermoplastics and metals. | Wide variety of materials, including plastics, metals, ceramics, and even biological materials. |
Surface Finish | Parts usually have smooth, polished surfaces right out of the mold. | Parts may require additional post-processing to achieve a smooth finish due to layer lines. |
Complexity & Detail | May struggle with extremely complex geometries. Parts with intricate designs may require multiple molds or assembly. | Excellent at producing complex and detailed designs as it builds from a digital model layer by layer. |
Cost | High initial costs due to mold creation, but per-unit cost decreases with larger production volumes. | Lower setup costs. However, per-unit cost remains relatively constant regardless of volume. |
Waste Generation | Typically less waste as excess material can be reused. | Can produce more waste due to support structures and non-reusable materials. |
What is The Process of Injection Molding?
In the world of manufacturing, injection molding is a steadfast friend. It operates on a principle that reminds me a bit of… well, baking a cake. A little odd, you say? Let me explain.
Just like preparing a cake, you start with your raw ingredients—in this case, thermoplastic material that acts as our cake mix. This material is then heated, similar to how you would beat eggs and sugar to form a smooth batter. The plastic is fed into a heating unit where it melts into a molten state, ready for shaping.
Now, imagine the mold in injection molding as your cake tin. This is where your ‘batter’ goes. The molten material is poured into the mold cavity under significant pressure, almost like you’re carefully spreading the cake batter into the tin, making sure it fills all the corners.
The filled mold then cools and hardens, just as a cake would in the oven. The molten plastic solidifies, taking the shape of the mold—the final reveal of your beautiful cake. The moment of magic arrives when you open the mold. Voila! Your plastic parts, just as perfect as a freshly baked cake.
While the process is simple and effective, it’s not without its challenges. The first one is the cost. The tooling costs for injection molding can be quite high, a bit like that pricey cake tin you’ve been eyeing in the bakery shop.
Then there’s the issue of design changes. They can be quite difficult to implement, almost like deciding halfway through baking that you wanted a chocolate cake instead of vanilla. Changes to the design often require a new mold, adding to costs and extending production time. All in all, injection molding, like baking, is a craft—one that demands precision, patience, and a willingness to invest.
How to Understand the 3D Printing Procedure?
Now, let’s hop onto the 3D printing train. Unlike injection molding, 3D printing is an additive manufacturing process. Think of it as building a sandcastle, layer by layer, until you have a masterpiece.
Here’s how it goes: you start with a digital design of the part you want to make. This design is then sliced into thousands of horizontal layers. The 3D printer reads this file and lays down successive layers of material (like ABS or nylon) until the part is complete. Each of these layers is a thinly sliced cross-section of the final part. Now, isn’t that pretty neat?
3D printing allows for intricate designs and a small batch of products. But don’t get too excited just yet. It also comes with its share of challenges – longer turnaround times, visible ridges, and the need for support structures, to name a few.
Comparing the Cost: 3D Printing vs. Injection Molding
So, we’ve established that both processes have their own set of strengths and weaknesses. But when it comes to dollars and cents, which one is more cost-effective?
For small volumes and prototypes, 3D printing often has the upper hand. Why, you ask? Primarily because there’s no need for tooling. On the other hand, injection molding has high initial costs due to the need for making molds. But if we’re talking about mass production, injection molding becomes the champion. The cost per part decreases with volume, making it a viable option for large batch production.
However, the cost isn’t the only factor to consider when deciding between injection molding vs 3D printing. Let’s peel back more layers in the next sections, shall we?
Efficiency and Precision: Injection Molding vs. 3D Printing
Accuracy and precision are crucial in the manufacturing process. Imagine ordering a pair of size 10 shoes and getting a size 8. Not cool, right? So, which process, injection molding or 3D printing, hits the mark when it comes to precision?
Injection molding, with its standardized process and high pressure, can produce highly accurate and consistent parts. Remember our cake metaphor? The cake comes out identical every single time. Plus, this method can work with a wide range of materials, which allows for robust, high-performance parts.
3D printing, on the other hand, can achieve precision that’s hard to match, especially for complex designs. It’s like being able to create a puzzle piece that fits just right. However, you might have to deal with issues like visible ridges due to the layer-by-layer building process.
Injection Molding and 3D Printing Material Choices: Strength and Durability Considerations
In the battle of injection molding vs 3D printing, the choice of material is another important factor. Kinda like choosing between hardwood and carpet for your flooring. Each has its pros and cons, and the choice depends on your needs.
Injection molding can use a variety of materials, from ABS and nylon to stainless steel and titanium. This diversity allows for parts that can withstand harsh conditions and last a long time. That’s why injection molded parts are often seen in industries like aerospace and medical.
3D printing also offers several material options, including thermoplastics, resins, and even metals. FDM (fused deposition modeling), for instance, uses thermoplastic filaments, while SLA (stereolithography) uses liquid resins. Depending on the technology and material used, 3D printed parts can range from somewhat fragile to reasonably durable.
Now, let’s move on to volume. How does the production volume affect the choice between injection molding and 3D printing?
Production Volume: A Key Consideration in Injection Molding vs 3D Printing
When deciding between injection molding and 3D printing, the quantity of parts you need plays a crucial role. Think of it as planning for a dinner party. Cooking for a few friends at home is one thing, but catering for a wedding is a whole different ball game.
Injection molding is a go-to method for large batch production. Once the mold is made, you can produce a high volume of parts at a low per-unit cost. But remember, the upfront cost for the mold can be pretty high. It’s a bit like buying a pizza oven – it’s an investment, but once you have it, you can make loads of delicious pizzas for a low cost.
3D printing, on the other hand, shines when it comes to low-volume production. If you only need a few parts, or if you’re making a prototype, 3D printing is a viable option. It’s quick, cost-effective for small batches, and allows for a lot of flexibility in design.
Now, let’s talk about design. How does the complexity of your part’s design influence the choice between these two processes?
Complexity of Design: How Injection Molding and 3D Printing Differ
Ah, design complexity… The playground for 3D printing. In the world of manufacturing, designing complex parts can be like trying to solve a Rubik’s cube – challenging but not impossible.
With 3D printing, you can create parts with complex geometries, internal structures, and intricate designs that would be difficult (if not impossible) to achieve with injection molding. It’s like having a magic wand that brings your most intricate designs to life.
Injection molding, on the other hand, can struggle a bit with highly complex designs. Sure, it can handle more than just your basic shapes, but there are limitations, especially when it comes to undercuts and internal structures.
Let’s shift gears and look at the time factor. When it comes to turnaround times, how do injection molding and 3D printing compare?
Time Factor: Speed of Injection Molding vs 3D Printing
We’re living in a fast-paced world, aren’t we? Everyone wants their orders delivered yesterday. So, when we talk about the speed of production in injection molding vs 3D printing, who crosses the finish line first?
Well, it depends. If you need a single prototype or a small batch of parts, 3D printing can be a faster option. The absence of tooling and molds means that you can start printing parts as soon as the design is ready. Like a fast-food joint, it’s a speedy way to get what you need in a short amount of time, which is great when you’re working on tight deadlines or just need to test the design before going full-scale.
Injection molding, on the other hand, can be slower during the initial stages, as the molds need to be made first. But once they’re ready, those molds can churn out parts at an impressive speed, which makes it ideal for mass production. Imagine an assembly line, where the same product is being produced efficiently and quickly – that’s the injection molding way.
So, while 3D printing seems quicker for smaller runs, in larger volumes, injection molding picks up the pace and races ahead.
Finishing and Post-Processing Comparison: Injection Molding and 3D Printing
Post-processing, the unsung hero of manufacturing, is the key to shiny, good-looking parts. No one wants a rough and bumpy part, right? So, which technique, injection molding or 3D printing, takes the crown for better finishes and post-processing ease?
Injection molding has a neat finishing advantage. The parts come out of the mold looking polished, as the process can create smooth, high-quality surfaces straight from the mold. Sure, there might be a bit of trimming and deburring required, but on the whole, the parts are close to perfection.
When it comes to 3D printing, the layer-by-layer process can leave visible ridges on the part’s surface. These ridges may require post-processing, like sanding, to smooth things out. And let’s not forget support structures. Depending on the design, 3D printed parts may need supports that will have to be removed after printing.
Environmental Impact: Considering Sustainability in Injection Molding and 3D Printing
As we continue to become more environmentally conscious, it’s essential to consider the sustainability of a manufacturing technique. Between injection molding and 3D printing, which is the greener choice?
3D printing has some eco-friendly advantages because it creates little waste, as it builds the parts layer-by-layer using only the necessary material. Plus, some 3D printing technologies allow for material recycling or reuse, making it even more sustainable.
Injection molding produces more waste because the plastic needs to fill the entire mold cavity, and the material doesn’t always get reused. However, it’s important to note that the overall environmental impact depends on various factors like material choice, energy consumption, and transportation.
Future Trends: The Role of 3D Printing in the Injection Molding Industry
As we look toward the future, how will 3D printing play a role in the injection molding industry? It’s like trying to predict the weather – it can be both exciting and uncertain.
However, there’s no denying that 3D printing has made significant strides in recent years. Some experts believe that we’ll see a rise in hybrid solutions that blend injection molding and 3D printing to unlock the best of both worlds.
For instance, 3D printed molds could streamline the production process, making it faster and more cost-effective. Plus, as 3D printing technology continues to advance and become more affordable, it might eventually become a stronger contender in large-scale production.
In conclusion, whether injection molding or 3D printing is best for your project depends on factors like your budget, project scale, and design complexity. Weighing the pros and cons of each technique and considering your specific requirements will help you make an informed decision. Whichever route you choose, always remember that innovation and sustainability should be on the forefront of your project goals.
Benefits of Using Plastic Injection Molding for Small Parts
The world of micro-sized parts is fascinating, and it requires precise attention to detail. When it comes to manufacturing small parts, injection molding is often the go-to choice. Now, let’s dive into why this traditional process is a popular choice for small, plastic parts.
First and foremost, injection molding enables high-precision in small, intricate components. As we’ve mentioned before, the high pressure during this process ensures that the molten plastic fills every nook and cranny of the mold, resulting in consistent and accurate parts.
Secondly, injection molding excels when it comes to material variety. From thermoplastics to metals, the wide range of material choices allows manufacturers to create durable and application-specific small parts. From aerospace to the medical industry, injection molding has got you covered.
Thirdly, manufacturing efficiency is a crucial factor when dealing with small parts, especially when you need large quantities. Injection molding can produce thousands of identical parts quickly and cost-effectively. So, if you have a product that requires plenty of tiny components, the mass production capabilities of injection molding cannot be overlooked.
Moreover, material waste is minimized in injection molding. Excess material and sprue from the molding process can often be recycled and reintroduced into the cycle, contributing to overall sustainability and lowering production costs.
In a nutshell, plastic injection molding offers precision, material variety, speed, and efficiency when producing small parts, making it the industry’s top choice.
Pros and Cons of 3D Printed Injection Molds
When it comes to making injection molds, can 3D printing enter the fray? As you know, traditionally, these molds are machined from blocks of metal, like steel or aluminum. But, with the advancements in 3D printing technology, we’re seeing a shift. Let’s explore the pros and cons of 3D printed injection molds.
Starting with the pros, 3D printing reduces the overall mold-making process time significantly. Since there’s no need for machining, highly complex molds that would be difficult to produce traditionally can be created with ease. Furthermore, design changes can be implemented instantly, without the need to modify physical molds.
However, using 3D printed injection molds also comes with its limitations. The most significant of these is durability. Compared to their metal counterparts, 3D printed molds, typically made of heat-resistant polymers like SLA or SLS materials, may not withstand the high pressures and temperatures during the injection molding process for an extended period. This makes them suitable only for low-volume production runs.
Finally, 3D printed molds may not provide the same level of surface finish as machined metal molds, which could affect the final product’s quality and appearance.
Although 3D printed injection molds present some advantages, they are best suited for prototyping or short-run applications. The technology is continually improving, though, and may become more suitable for higher-volume production in the future.
Alternative Technologies to Injection Molding and 3D Printing
While injection molding and 3D printing are popular choices when it comes to manufacturing, there are alternatives. It’s always good to keep your options open, right? Here are a few manufacturing methods you might want to consider for your project:
- CNC Machining: This subtractive manufacturing process takes a block of material and shapes it using computer-controlled cutting tools. It offers excellent precision and works with a wide range of materials, from plastics to metals. It’s also great for low to medium-volume production.
- Rotational Molding: A good option for manufacturing hollow plastic products, rotational molding involves heating a hollow mold filled with plastic, spinning it around to evenly distribute the material, and then cooling it to produce the final part. It’s a cost-effective technique with low tooling costs, making it viable for low to medium-volume production.
- Thermoforming: In this method, a plastic sheet is heated and then vacuum-formed over a mold. After cooling, the plastic retains the mold’s shape. Thermoforming is an excellent option for large, shallow parts and offers flexibility in design and materials.
Each alternative manufacturing process has its distinct advantages and drawbacks, so choosing the best fit for your project depends on factors such as required accuracy, volume, and material choices.
Conclusion: Is Injection Molding or 3D Printing Better for Your Project?
So, now that we’ve explored the world of injection molding and 3D printing, where do we stand? It ultimately boils down to your specific project needs and preferences. Each process has its perks, but they also come with their own set of challenges.
If your project demands high-volume production, precision, and robust material options, injection molding might be your best choice. For projects with lower volumes, rapid prototyping, and increased design flexibility, 3D printing could be the ideal solution.
In terms of cost efficiency, injection molding is typically the better option for large-scale production, while 3D printing is more affordable for short production runs and small quantities. When considering time constraints, 3D printing allows for quicker turnaround times and faster design iterations, making it perfect for rapid prototyping. Injection molding, on the other hand, often requires significant lead time in mold creation, but once the mold is ready, parts can be produced in a much quicker and repetitive manner.
Environmental impact should also be considered. 3D printing produces less waste compared to injection molding, as it only uses the material necessary for the specific design. However, injection molding has a greater potential for recycling, as excess materials can be reprocessed for future production.
Another aspect to factor in is the level of intricacy and detail you require for your product. While both processes are capable of producing complex parts, 3D printing has a slight edge in this aspect, as it can generate more intricate designs that may not be feasible using injection molding.
It’s important to carefully evaluate your objectives, priorities, and available resources when making the decision between injection molding and 3D printing. To make the best choice, ensure that you consider expectations around lead time, production volume, material options, cost efficiency, environmental impact, and desired intricacy of your end product.
In conclusion, the choice between injection molding and 3D printing is highly dependent on your project’s specific needs and goals. Each method has distinct advantages and disadvantages that should be carefully weighed to determine the optimal approach. By taking these factors into consideration, you can make an informed decision that ensures the most effective, efficient, and successful outcome for your project.