To choose between Delrin and PEEK, it’s essential to understand their distinct characteristics.
Delrin, a brand of acetal homopolymer, is widely recognized for its strength, stiffness, dimensional stability, and low friction, and is commonly used in automotive parts and medical equipment.
PEEK is a high-performance thermoplastic known for its excellent heat resistance, mechanical strength, and chemical resistance, making it a popular choice in aerospace, oil and gas, and medical implants.
In the following content, we will explore the detailed differences between Delrin vs PEEK to help you select the best material for your project.
What Is Delrin?
Delrin is the brand name for DuPont’s homopolymer acetal (POM) product. It exhibits properties similar to metal and is known as “super steel.”
Compared to copolymers, Delrin has higher tensile strength, stiffness, creep resistance, and fatigue resistance, as well as notable impact resistance.
It is suitable for designing thinner, lighter parts with shorter molding cycles, reducing overall costs.
Moreover, Delrin features excellent processing characteristics and can be manufactured into various shapes using injection molding, extrusion, and calendering.
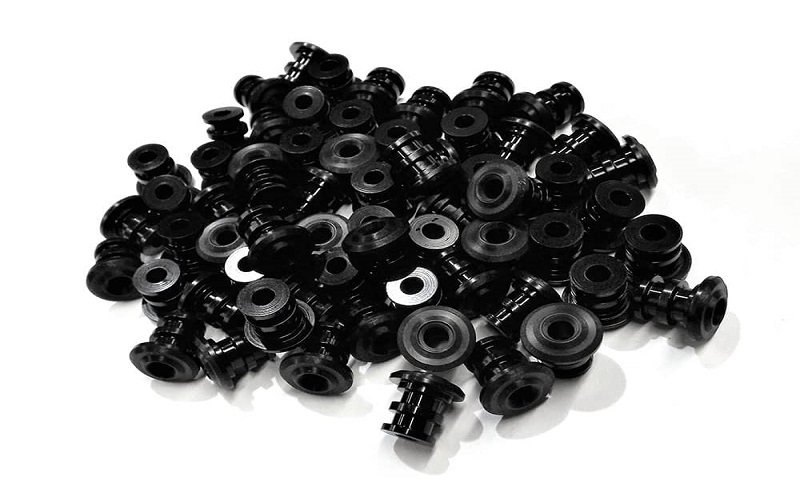
What Is PEEK?
Polyether ether ketone (PEEK) is a polymer consisting of repeating units with two ether bonds and one ketone bond in its backbone structure, making it one of the varieties of polyaryletherketone (PAEK).
Its outstanding mechanical properties, wear resistance, corrosion resistance,and heat resistance up to 260°C make PEEK one of the most resilient and widely used thermoplastics in the plastics industry.
PEEK is primarily used in aerospace, automotive, electrical, biomedical, and semiconductor industries.
Currently, the main preparation processes for PEEK include injection molding, fused deposition molding, selective laser sintering and hot press molding.
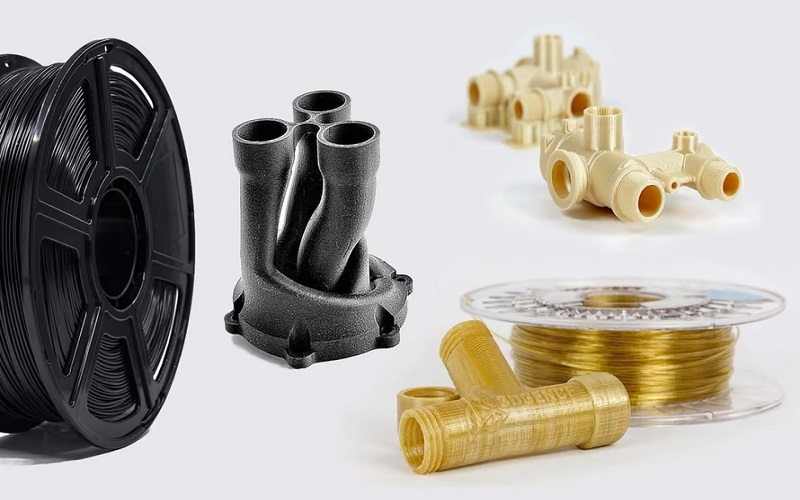
Delrin vs PEEK:Properties
This table below shows data on the performance comparison between Delrin and PEEK:
Properties | Delrin | PEEK |
Density(g/cm3) | 1.41 | 1.33 |
Melting Point(℃) | 175 | 343 |
Tensile Yield Strength(MPa) | 69 – 80 | 100-115 |
Tensile Modulus (GPa) | 2.8-3.5 | 3.6 |
Water Absorption(%) | 0.3 | 0.05-0.2 |
Shrinkage(%) | 1.8-2.1 | 1.0-1.3 |
Impact Strength (J/m) | 50-70 | 35-45 |
Heat Deflection Temp (℃) | 120-170 | 160-180 |
Chemical Resistance | Good (limited acids) | Excellent |
Friction Coefficient | Low (0.2 – 0.3) | Very low (0.1 – 0.2) |
Delrin vs PEEK:Pros And Cons
To make the most informed material choice that aligns with project requirements, it’s essential to analyze the strengths and weaknesses of Delrin and PEEK.
Advantages of Delrin
- High tensile strength, impact resistance, and stiffness
- Excellent wear resistance and self-lubricating properties
- Good dimensional stability and resistance to creep
- Electrical insulation
Disadvantages of Delrin
- Not resistant to strong acids, strong alkalis, and oxidizing agents
- Relatively poor flame resistance
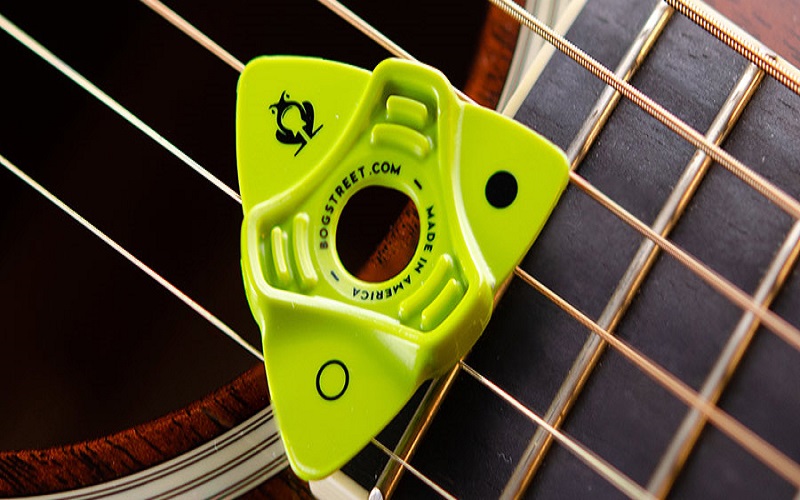
Advantages of PEEK
- High toughness and stiffness comparable to alloys
- Superior fatigue resistance
- Exceptional chemical corrosion resistance
- Self-extinguishing ,lowest smoke emissions
Disadvantages of PEEK
- Relatively low UV resistance
- High cost
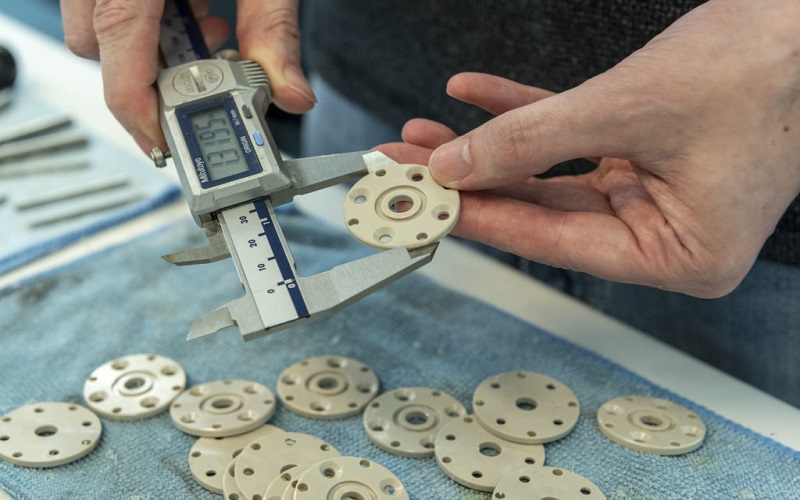
Delrin vs PEEK:Applications And Uses
Due to their different advantages and limitations, Delrin and PEEK are suitable for various industrial applications.
Delrin injection molding is a preferred technique among industry leaders for high-load mechanical applications, widely used in machinery gears, automotive seatbelt buckles, fuel system components, medical instrument handles, and insulating housings for electrical switches.
PEEK, with its excellent comprehensive properties, can replace traditional materials like metals and ceramics in many specialized fields.
PEEK Injection molding is the most common manufacturing process for PEEK plastic and plays a vital role in producing lightweight structural parts, automotive seals, and electrical connectors.
Meanwhile, PEEK’s biocompatibility and sterilization resistance make it an ideal material for spinal implants, orthopedic screws, and dental healing caps.
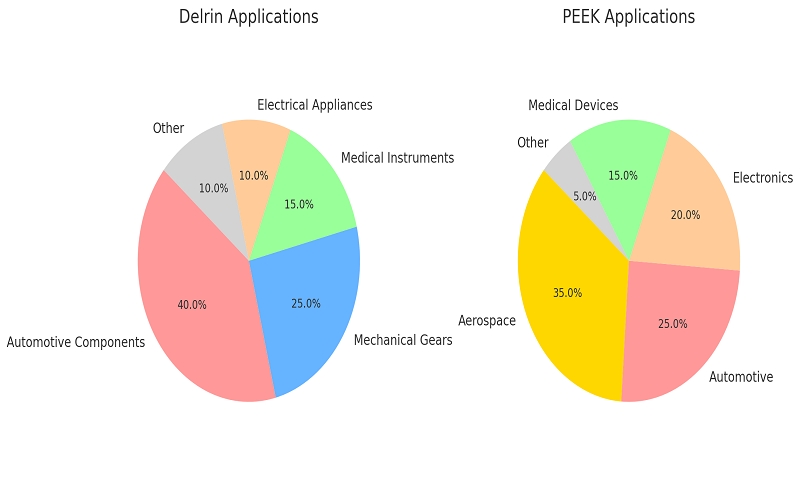
Delrin vs PEEK:Recyclability and Sustainability
From the perspective of plastic recycling, although Delrin and PEEK are theoretically recyclable, there are practical challenges involved.
Delrin can be mechanically recycled, but its recycling processes are not as widespread as those for plastics like PP and PET, which increases the difficulty of recycling.
It is important to note that Delrin releases toxic formaldehyde gas when burned, so caution is necessary when handling waste material.
Although the production of Delrin impacts the environment, its durability and longevity can reduce the frequency of replacements, thereby minimizing waste generation.
PEEK recycling is also feasible, but due to its typical use in high-temperature and high-pressure environments, the recycling process is more complex and costly.
In fact, PEEK recycling relies predominantly on chemical recycling methods, which allow it to be broken down and re-synthesized into new polymers.
The high performance and durability of PEEK plastic mean it can replace more environmentally detrimental traditional materials, such as metals, in many demanding applications, helping to reduce energy consumption and lessen the overall environmental footprint.
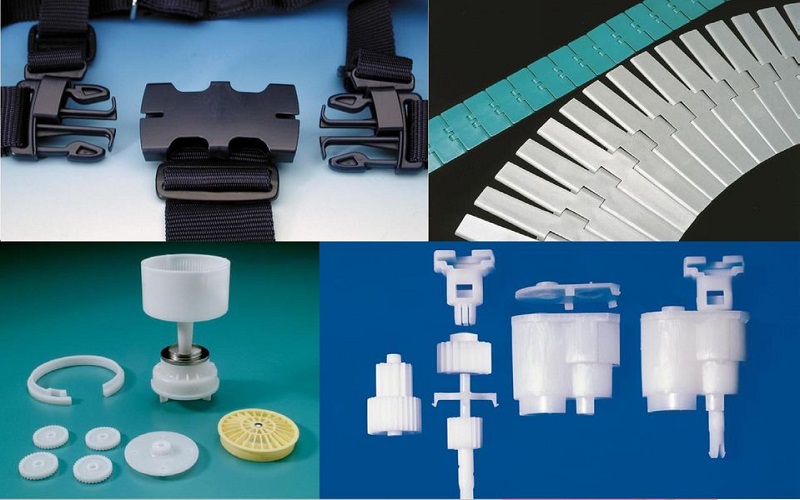
What Is The Difference Between Delrin And PEEK?
This paragraph systematically summarizes the main differences between Delrin and PEEK.
Composition
Delrin belongs to the polyoxymethylene homopolymers, synthesized through the catalytic polymerization of formaldehyde in an inert solvent with terminal capping, consisting of CH2O as the repeating unit in its backbone.
In contrast, PEEK is a high-performance polymer composed of repeating units containing one ketone and two ether bonds in its main chain, classifying it as a specialty polymer material.
Machinability
Both materials are suitable for plastic processing techniques such as injection molding, extrusion, and mechanical machining. For 3D printing, Delrin is not a primary material but can be processed using laser cutting and engraving.
Unlike Delrin, PEEK has ventured into various markets with 3D printing, including medical, aerospace, and automotive.
Temperature Tolerance
In terms of heat resistance, PEEK has an incomparable advantage over Delrin.
Delrin’s maximum long-term service temperature is below 90°C, and its short-term resistance reaches up to 120°C.
On the other hand, PEEK’s long-term service temperature can go up to 160°C, with a short-term capacity of up to 260°C.
The load thermal deformation temperature for grades reinforced with 30% glass or carbon fibers can reach as high as 316°C.
Application
Both materials are widely used in automotive, medical, electronics, and industrial machinery, but they are suited for different environments.
Delrin is ideal for applications requiring stiffness and low friction, whereas PEEK is better suited for high-temperature or highly corrosive environments.
Cost
Generally, the cost of Delrin ranges from $5 to $15 per kilogram for standard commercial grades.
In contrast, PEEK is significantly more expensive, with prices ranging from $90 to $400 per kilogram, depending on the type of PEEK (unfilled, glass-filled, or carbon fiber reinforced), its purity, and the quantity purchased.
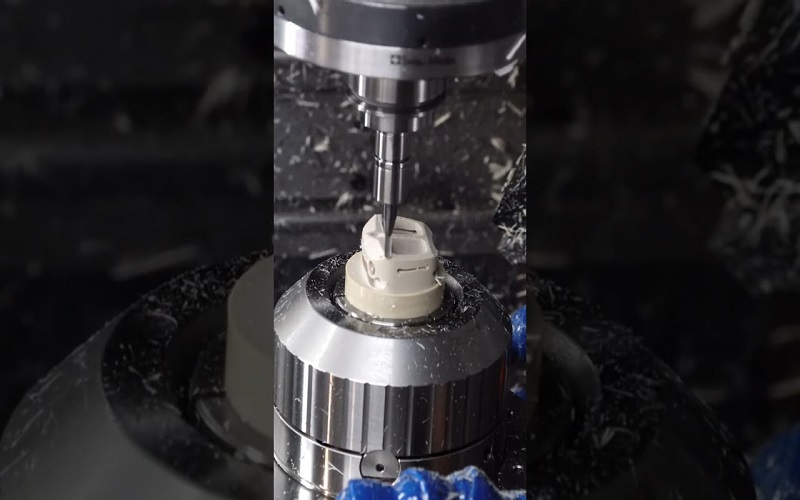
Conclusion
This article has provided a detailed comparison of Delrin and PEEK materials, explaining what they are, their characteristics, and their practical applications.
If you would like to learn more about Delrin and PEEK, please contact FOWMOULD.
FOWMOULD specializes in providing comprehensive injection molding services, meeting all your needs from prototype design to production.
Please visit our website to learn more or to request a free quote.