Over time, exposure to UV radiation can cause plastics to become brittle, discolored, and even crack or break apart. This can be a serious problem for products that are designed to be used outdoors or in applications that requires exposure to sunlight.
In this blog, we will explore the beneficial properties of UV resistant plastics, different types, applications, injection molding of these plastics, and a reliable source to get these plastics.
Beneficial Properties of UV Resistant Plastics
UV resistant plastics offer a range of beneficial properties, including UV stability, resistance to discoloration and fading. These properties make them an ideal choice for a variety of outdoor applications.
UV Stability
UV radiation can cause plastics to break down and become brittle. It can also lead to cracking, fading, and discoloration.
In order to solve this problem, UV-resistant plastics need to be added into special additives, such as UV absorbers or stabilizers, to boost the uv resistance of plastics. These additives work by absorbing or scattering UV radiation, preventing it from penetrating the plastic completely and causing damage.
Resistance to Discoloring and Fading
The UV resistance of plastics is an important consideration for outdoor products, as exposure to sunlight can cause discoloring and fading and shorten the lifespan of the material. These plastics are designed to maintain their color and appearance over time, even when exposed to harsh environmental conditions. This property is particularly important in applications where aesthetics is very important, such as in outdoor furniture, building facades, and signage.
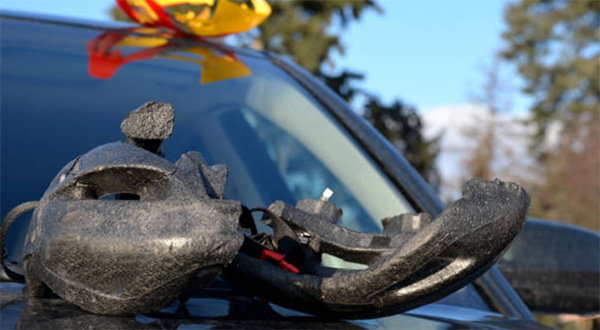
Mechanical Property
In addition to their UV stability and resistance to discoloration, UV resistant plastic also offers excellent mechanical properties. These plastics are typically engineered to provide high strength, stiffness, and impact resistance, making them suitable for a range of demanding applications.
Excellent Durability
Another key benefit of UV resistant plastics, is their excellent durability. In fact, they can last 10-20 years even when exposed to UV rays. This property makes them ideal for applications where longevity and reliability are essential.
Aesthetic Diversity
UV resistant plastics are available in a wide range of colors and finishes, providing a high degree of aesthetic diversity. This property allows designers and manufacturers to create functional and visually appealing products. And suitable for a variety of applications.
Low Cost
Despite their many benefits, UV resistant plastics are relatively more affordable than other materials with similar properties, such as metals or composites. This property makes them a popular choice for manufacturers and end-users looking to reduce costs without compromising on performance or quality.
UV Resistant Plastics for Injection Molding
UV resistant plastics such as Acrylics/ Polymethyl Methacrylate (PMMA) and Thermoplastic Elastomers (TPE), have excellent properties that make them suitable for injection molding.
Acrylics/ Polymethyl Methacrylate (PMMA)
Acrylics, also known as Polymethyl Methacrylate (PMMA), is UV resistant plastic that is suitable for different applications.
Besides the resistance of UV, Acrylics also have a high level of transparency and have the ability to withstand different weather conditions, including harsh weather. This property makes them an ideal material for outdoor applications.
Overall, acrylics are a versatile material that can be used for a range of products that require UV resistance.
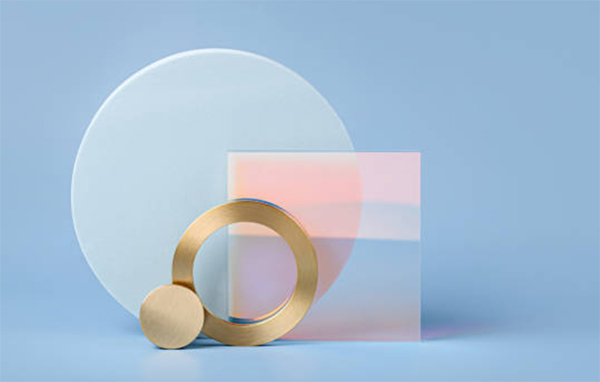
Also Read: >> Acrylic Injection Molding
Thermoplastic Elastomers (TPE)
Thermoplastic elastomers (TPE) are a group of materials that combine the favorable properties of rubber and plastic.
They have excellent plastic uv resistance properties and can withstand exposure to sunlight for extended periods without degrading. TPEs are often used for outdoor products such as garden hoses, seals, and gaskets. They are also commonly used for automotive parts, including weatherstripping and window seals.
While TPEs have many advantages, they can be more expensive than other plastics, and their properties can vary significantly depending on the specific type of TPE used.
Polybutylene Terephthalate (PBT)
Polybutylene Terephthalate (PBT) is a thermoplastic that is commonly used for injection molding because of its mechanical properties, thermal resistance, and electrical insulating property.
PBT has a high level of UV resistance and is often used for outdoor applications, including electrical components and automotive parts.
Polyethylene (PE)
Polyethylene (PE) is a widely used plastic that is known for its toughness and durability. PE is highly resistant to UV radiation and is often used for outdoor applications, including pipes, packaging materials, and playground equipment.
PE is also commonly used for injection molding due to its excellent impact resistance and low coefficient of friction. However, PE can be prone to stress cracking and has a lower heat resistance than some other plastics, which can limit its use in certain applications.
Polycarbonate (PC)
Polycarbonate (PC) is a transparent thermoplastic that is known for its high impact resistance and excellent plastic uv resistance. PC is often used for outdoor applications, including glazing and lighting fixtures. PC is also commonly used for electronic components and automotive parts due to its high level of heat resistance.
PC is prone to scratching and can degrade over time when exposed to certain chemicals. PC can also be more expensive than other plastics, which can limit its use in some applications.
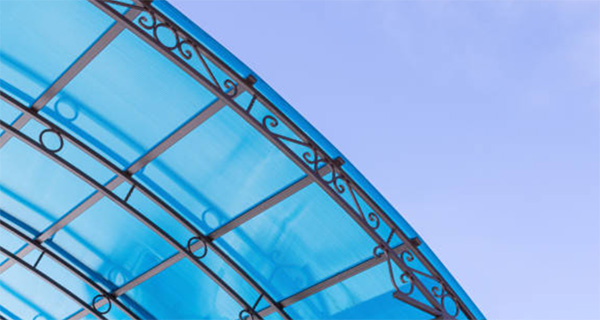
Polypropylene (PP)
Polypropylene (PP) is a thermoplastic that is known for its toughness and resistance to chemicals. PP is well-suited for injection molding because it can be easily melted and formed into complex shapes.
To ensure that the final product has adequate UV resistance, the proper amount of UV stabilizers must be added to the PP resin before injection molding. The type and concentration of UV stabilizers used may vary depending on the intended use and expected exposure to UV radiation.
Popular Applications for UV Resistant Plastics Injection Molding
UV protection plastic is used in a wide range of industries, including automotive, marine, farming, solar power, furniture, and consumer goods. The following paragraphs provide more detail on the specific applications in each of these industries.
Automotive Industry
UV resistant plastics have different applications in the automotive part manufacturing industry. They are commonly used for exterior components such as body panels, bumpers, and trim.
These plastics can withstand exposure to sunlight and maintain their color and finish over time, providing a long-lasting, durable solution for automotive manufacturers. Additionally, they are lightweight and easy to mold, making them a popular choice for many automotive applications.
Marine Equipment
Marine equipment is often exposed to harsh environmental conditions, including saltwater, sunlight, and extreme temperatures. It is therefore important to use materials that can easily be adapted to these extreme conditions.
UV resistant plastics are ideal for use in marine equipment such as hulls, decks, and instrument panels because they are resistant to corrosion and can withstand exposure to UV radiation without becoming brittle or discolored.
Farm Machinery
UV protective plastic is also used in the manufacturing of farm machinery such as tractors, combines, and other equipment. These plastics are ideal for use in agricultural applications because they are resistant to sunlight, chemicals, and other environmental factors.
Solar Power Infrastructure
Solar power infrastructure components, such as solar panels and mounting systems, are often exposed to high levels of UV radiation. UV resistant plastics are used in the manufacturing of different solar components to ensure that they can withstand exposure to sunlight without becoming brittle or discolored.
These plastics are also resistant to weathering and can maintain their strength and appearance over time, providing a long-lasting solution for solar power infrastructure.
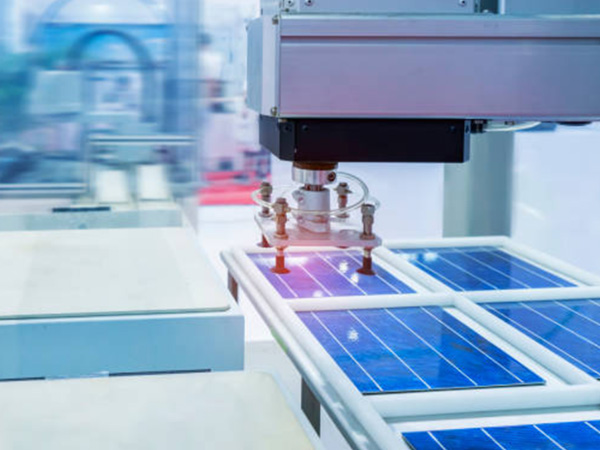
Outdoor and Indoor Furniture
UV resistant plastics are commonly used in the manufacturing of outdoor and indoor furniture such as plastic pet homes, chairs, tables, and other seating options. The use of UV protection plastic can help to prevent damage and discoloration caused by exposure to
Consumer Goods
Finally, UV resistant plastics are used in a variety of consumer goods such as electronics, sporting goods, toys and some home appliances. These plastics are resistant to discoloration and fading caused by exposure to sunlight, ensuring that these products maintain their appearance over time.
UV Resistant Plastics Injection Molding Services from FOW Mould
When looking for UV-resistant plastic injection molding services, choosing a reputable and experienced manufacturer is important. Those that use high-quality materials and advanced manufacturing processes. FOW Mould has been in the business of providing high quality UV plastics injection molding services to various businesses.
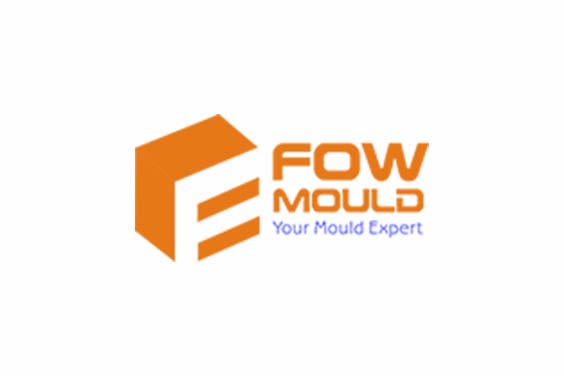
In addition to providing injection molding services for UV resistant plastics, FOW Mould can also enhance the UV resistance of plastic materials through the use of additives. This means that customers have the flexibility to choose from a wider range of plastic materials for their products without worrying about the impact of UV radiation on their product’s performance and longevity.
Comprehensive list of FOW Mould services:
- Plastic product design
- Mold design
- 3D printing
- CNC machining
- Mold making
- Injection molding
- Insert molding
- Overmolding
Conclusion
UV radiation can have a significant impact on the performance and longevity of plastic products, which is why UV resistant plastics are becoming increasingly popular for a variety of applications.
FOW Mould offers a comprehensive range of injection molding services for various industries and plastic materials, including uv protected plastic. Our team of experts can provide molding services to meet your unique requirements. Contact us today to learn more about our services and how we can help you with your next project.