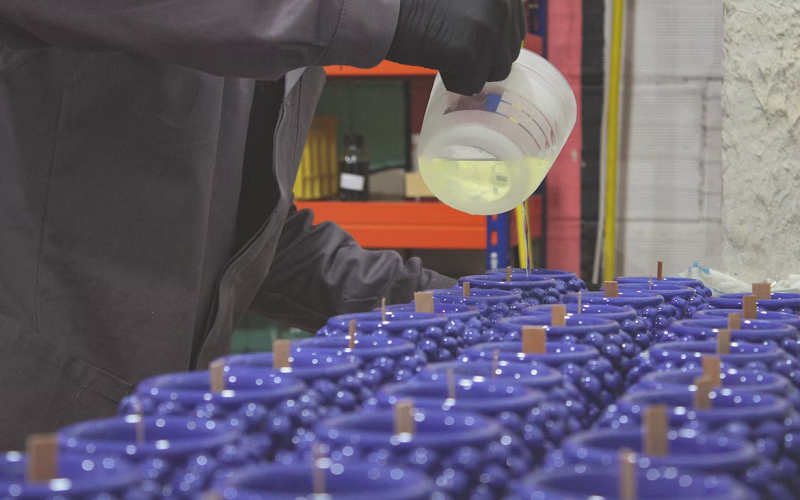
Share :
Share :
For injection molding, polystyrene is a commonly used polymer. Polystyrene comes in many grades, but the most used grades of the polymer for injection molding are General Purpose Polystyrene (GPPS) and High Impact Polystyrene (HIPS). These two polystyrene resins are different in properties as the former is more brittle, but the latter is more opaque.
This polymer is used in toys, automotive, plastic molded chairs, injection molding, food packaging, and dishes. Polystyrene owes its extensive usage to it being odorless and non-toxic. The way it is used to mold injections takes complete advantage of its properties to make a desirable and durable product.
Polystyrene is a fairly common kind of synthetic polymer. Mainly used during the packaging and molding of industry-based components, polystyrene is also one of the most often used plastics in the molding process of thermoplastic injections. In either the form of plastic or foam, the packaging material made of polystyrene is safe to be used in the food and beverages industry. The automation industry also finds the use of polystyrene as the polymer is transparent and sets to form solid components after molding. Other uses of polystyrene along with auto parts include it being used in the electrical industry and also as toys.
Polystyrene is a thermoplastic known as crystal polystyrene while it is traded. The injection molding of polystyrene is done in crystal, medium impact, and impact versions. The applications of the molding vary. The polystyrene homopolymer transforms into high impact polystyrene (abbreviated as HIPS) when it is mixed with elastomers. This leads to many grades of polystyrene polymer being available in the market.
Polystyrene is used in mould design because of its advantages. Since it is non-toxic and odorless, the polymer does not pose any threat to the health of the user. Polystyrene is popular for molding purposes because of its affordability as well. Some of the advantages of polystyrene are as follows:
The disadvantages one might encounter while using polystyrene for molding are:
Since polystyrene is fairly cheap to procure, it finds use in many domains across industries. From general household appliances to containers and light diffusers, polystyrene is used in various ways. The reason why polystyrene finds use in so many ways is because it is durable, lightweight, does not hold moisture and resists bacterial growth. The polymer is such that the product design provides insulation and is also recyclable. The ability to be recyclable makes it popular for use in the packaging industry, especially in the food and beverages industry, since the polymer also fights against bacterial growth.
Polystyrene is used in refrigerator liners, glazing, cutlery, audio or video cassette cases, beakers, housewares, and electrical housing. Foam molding of polystyrene is used in even more varied ways like for tools, business machine housings, boxes, and cases. The polystyrene beads made of foam are used for cushion filling and as cushioning agents during packaging. The more common uses are in egg boxes, food trays, and dishes.
For injection molding, polystyrene is favored mainly because of its physical and chemical properties. Like other amorphous thermoplastics, polystyrene has a uniform material shrinkage that can be predicted during the molding process. This predictability reduces the warpage of the molded injection plastic parts. This predictability of shrinkage becomes an advantage as the manufacturers can decide how to use this shrinkage to their benefit, and the overmolding of polystyrene is done while keeping the final dimensions in mind.
The polymer can be radiation sterilized. One of the ways in which polystyrene is prevented from UV degradation is by supplying it with UV inhibitors. The polymer is also colored so that the UV absorption can be minimized as much as possible. Still, this plastic used for plastic injection molding is not recommended to be used outdoors for long periods of time. Polystyrene is best used in controlled indoor conditions even though it will survive short-term outdoor usage.
Polystyrene is susceptible to damage when it comes in contact with organic chemicals. These include organic solvents like ketones, ethers, and esters. The polymer is highly resistant to water and moisture, which also prevents bacterial growth. Polystyrene is also chemically resistant to dilute mineral acids and alkalis.
The tensile strength of the crystal grade polystyrene lies in the range of 5000 to 7000 psi. The tensile strength of the low impact grade polystyrene falls in the range of 3000 to 4000 psi. This difference in tensile strength is due to the impact of the rubber impact modifier used in mold making technology. The notched impact strength of high impact polystyrene or HIPS is significantly higher than the crystal grade polymer, recorded at 2.5 ft-lbs./inch. Crystal grade polystyrene also sees heat deflection temperatures at the tensile strength of 264 psi when the temperature is in the range of 155°F to 200°F. Some special grades of this polymer can tolerate heat deflections up to 210°F.
The stiffness of a material is indicated by the flexural modulus, with a higher number signaling higher stiffness and vice versa. For crystal grade polystyrene, the flexural modulus is 450,000 psi. It drops to 250,000 psi for the high impact grade polystyrenes.
Chemical Formula | (C8H8)n |
Melting Point (°C) | ~215°C |
Melt Temperature | 210-249 °C (410-480 °F) |
Typical Injection Molding Temperature | 38 – 66 °C (100 – 150 °F) |
Heat Deflection Temperature (HDT) | At 0.46 MPa (66 PSI), HDT is 95 °C (284 °F) |
Polystyrene is a durable material, easy to handle, cheaply accessible, resistant to radiation and moisture, available in many grades due to infusion of elastomers, and used for a variety of purposes. One of the most important uses of polystyrene is for injection molding or insert molding. There are many other uses for this polymer which is due to the many grades of PS resins available for molding. The properties of the polymer vary depending upon the grade which is exploited by manufacturers across industries. With its own set of advantages and disadvantages, the polymer is used such that its benefits outweigh the cons.
Please contact us using the form below or emailing (harry@fowmould.com)