As one of the highest produced varieties in the plastics industry, polyethylene firmly holds its place as a premier material.
Depending on the polymerization method and molecular weight, High-Density Polyethylene (HDPE) and Low-Density Polyethylene (LDPE) emerge as the two prevalent forms.
In this article, we’ll dive deep into ldpe injection molding, exploring its inherent properties and the molding procedure, pinpointing the distinctions that differentiate it from other techniques.
What is LDPE Material?
Low-Density Polyethylene, commonly referred to as LDPE, is a thermoplastic resin obtained from the free radical polymerization reaction of polymer-grade ethylene with peroxides as initiators. Noted for its high degree of branching, it’s celebrated for its flexibility.
Ever since its first synthesis in the 1930s, it quickly became a material of choice in the manufacturing sector, catering to most thermoplastic molding processing techniques. Among these, ldpe injection molding stands out prominently.
This method leverages LDPE’s durability and versatility, making it a popular approach for producing both consumer and industrial products.
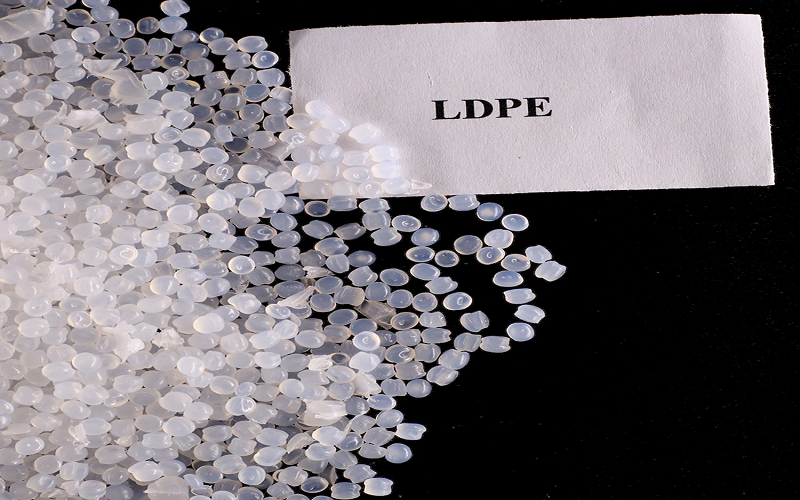
Properties of LDPE
- Molecular weight is generally 100000~500000
- Density is 0.91~0.93g/cm3, the lightest variety of polyethylene resin.
- Soft and ductile
- Translucence, easy to process
- Stable chemical properties, resistant to alkali and organic solvents.
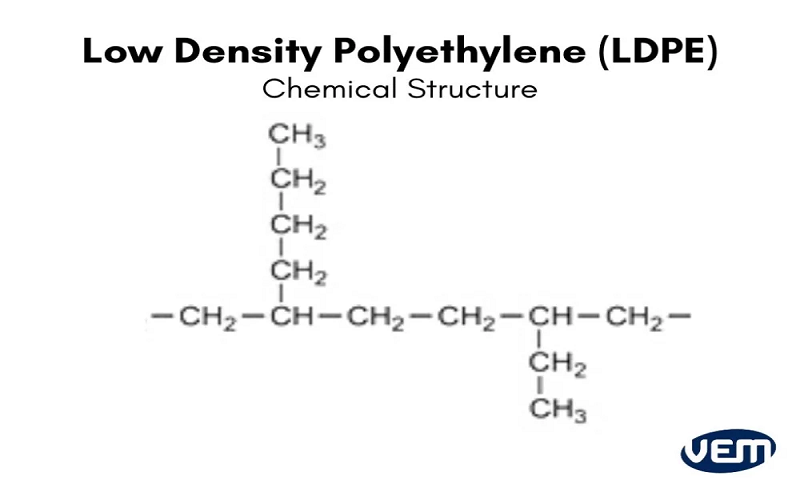
Conditions For LDPE Injection Molding Process
The injection molding of low-density polyethylene (LDPE) is technically similar to polyethylene injection molding. However, due to its unique material properties, the molding conditions required for LDPE differ. Below are some key parameters and conditions to consider in the LDPE injection molding process:
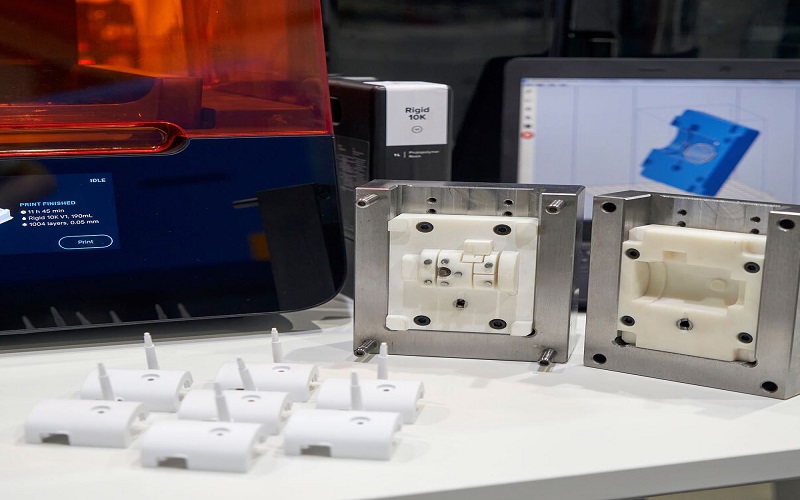
Melt Temperature
Low-density polyethylene has a relatively low melting point, hence the melt temperature typically ranges between 180°C to 240°C. The specific temperature still depends on the grade of low-density polyethylene (LDPE) being used and the characteristics of the part being molded.
Mold Temperature
A mold temperature set between 20°C to 60°C is considered suitable. To achieve uniform cooling and more economical heat removal, it is recommended that the cooling channel diameter be at least 8mm, and the distance from the cooling channel to the mold surface should not exceed 1.5 times the diameter of the cooling channel.
Injection Pressure
Due to its lighter weight, smaller molecular weight, and a higher number of branched structures in its molecular configuration, low-density polyethylene (LDPE) is typically molded under pressures of 500 to 1500 bar. Maintaining stable injection pressure prevents issues that affect product quality during high-pressure molding, such as melt fracture and annealing.
Injection Speed
For low-density polyethylene, it’s generally recommended to employ a medium to high injection speed to fill the mold rapidly. In actual production, the appropriate speed should be determined based on mold design and the grade of LDPE used.
Drying Treatment | Generally not required |
Melt Temperature (℃) | 180~240 |
Mold Temperature | 20~60 |
Back Pressure (MPa) | 5~15 |
Injection Pressure (MPa) | 50 ~ 150 |
Injection Speed | Rapid injection molding |
Shrinkage rate(%) | 1.5~4 |
Advantages & Disadvantages of LDPE Injection Molding
Although products made from low-density polyethylene (LDPE) injection molding are common in everyday life, it’s essential to weigh the pros and cons of LDPE injection molding to determine its suitability for specific application requirements.
Advantages
- Flexibility
LDPE is renowned for its soft texture and strong ductility, allowing it to stretch freely without easily breaking. It’s suitable for making plastic products of various sizes, shapes, and thicknesses.
- Transparency
Low-density polyethylene typically presents as milky-white waxy particles. It has a semi-transparent nature, and with its ease of processing, LDPE injection molding is a favored method for transparent applications and packaging.
- Machinability
Comparedto other thermoplastics, low-density polyethylene has a relatively low melting point, facilitating its processing, especially in complex designs.
- Chemical Resistance
LDPE demonstrates good chemical resistance, being able to withstand alkalis and most organic solvents. This ensures that products manufactured through LDPE injection molding possess extended durability.
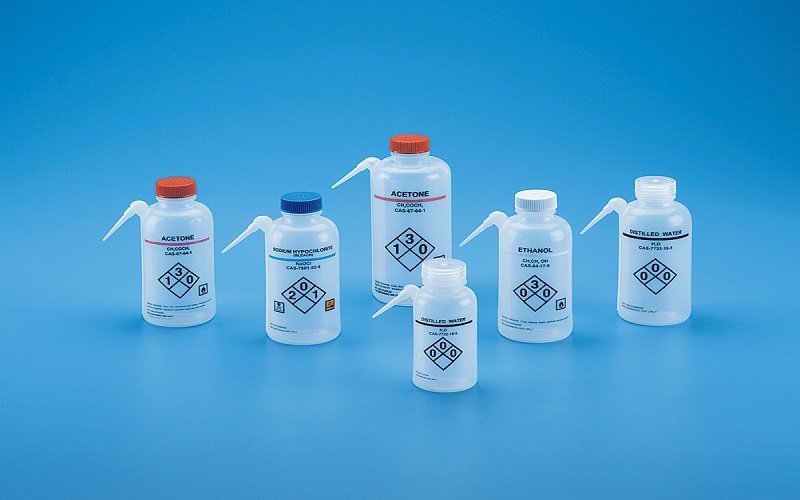
Disadvantages
- Temperature Sensitivity
LDPE has a relatively low melting point, so during the LDPE injection molding process, too high or too low a temperature may cause the product to distort or warp if it is exposed to heat for an extended period of time.
- Gas Barrier Properties
LDPE performs poorly in terms of gas barrier properties, with high permeability to carbon dioxide and other gases, and is not well suited for applications requiring hermetic seals, such as some food packaging.
- Lower Strength
Compared to HDPE materials, LDPE has poor mechanical strength and produces a lack of flexibility at low temperatures. Therefore, it may not be suitable for applications requiring high strength and rigidity.
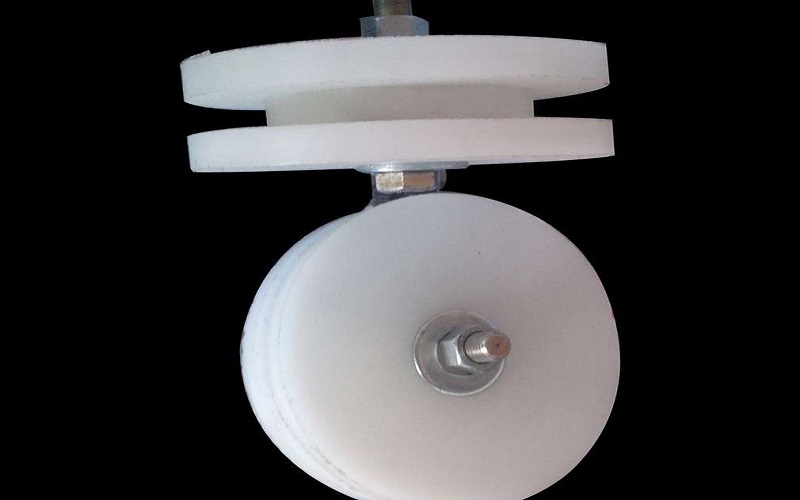
Applications of LDPE Injection Molding
LDPE injection molding technology has penetrated various aspects of our daily life. With its technical characteristics, it is highly favored in many industries.
Packaging
LDPE, due to its excellent transparency and oxygen barrier properties, is extensively used in the packaging product sector. For instance, LDPE injection molded items such as food bags, bread bags, and garbage bags are widely utilized in daily life.
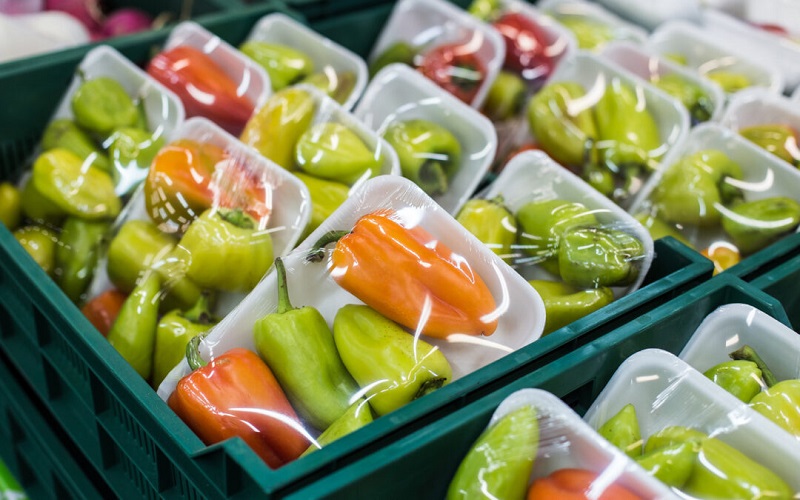
Medical
In the medical industry, where medical devices require excellent sealing, the flexibility of LDPE injection molding makes it commonly used for medical tubing, compressible dropper bottles and certain flexible caps.
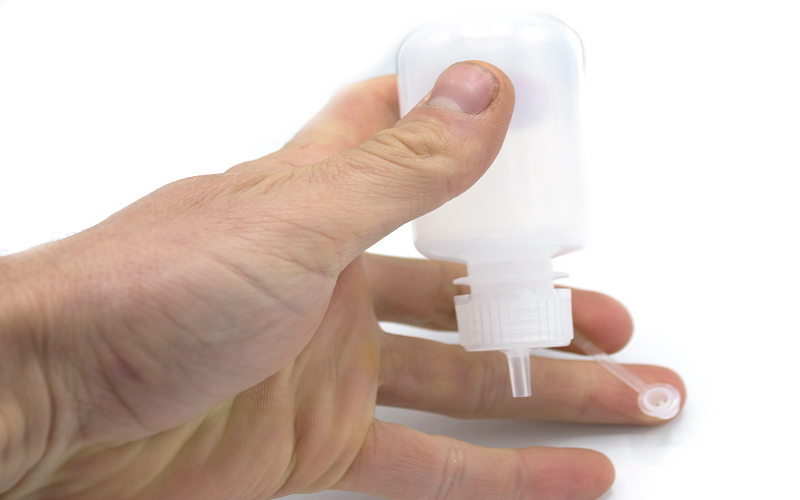
Electrical Insulation
Due to the wear-resistant, oil-resistant, and compression-resistant characteristics of LDPE material, it is widely used in the protection field of electrical wires and cables. LDPE injection molded protective tubes for wires and cables can protect the safety and lifespan of the wires and cables, preventing them from wear and compression issues.
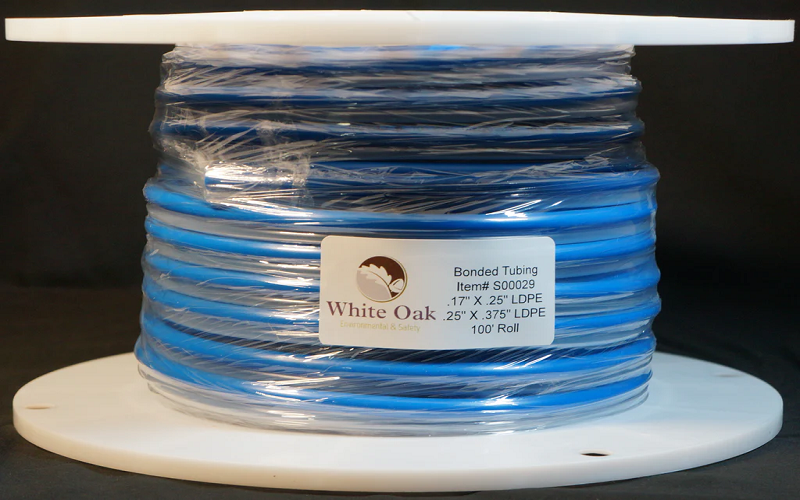
Agriculture
The molecular chain of low-density polyethylene has a strong affinity with water molecules, ensuring that the products molded from it have superior waterproof, moisture-proof, and impact-resistant properties. Thus, it’s commonly used in agriculture to produce irrigation tubes, ground films, and greenhouse coverings.
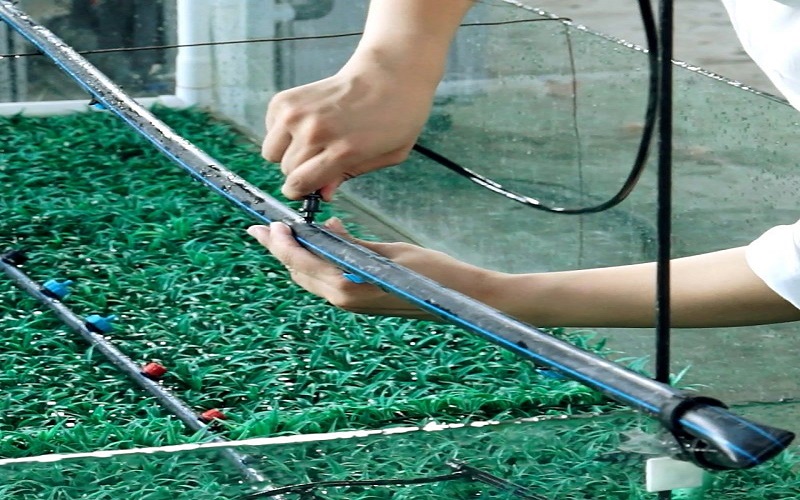
Comparison of LDPE Injection Molding and HDPE Injection Molding
LDPE and HDPE are two common forms of polyethylene that play important roles in the injection molding industry. In the following text, we will explore the similarities and differences between these two processes.
HDPE injection molding shares many similarities with LDPE molding. Both can be processed through injection molding, have good chemical stability, are recyclable materials, and are suitable for food-grade applications.
However, in terms of material structure, LDPE has a highly branched molecular structure, making it softer and having a lower melt flow. In contrast, HDPE is harder due to its dense molecular structure.
Additionally, LDPE injection molding has weaker tensile strength compared to HDPE injection molding. However, it can produce products with higher transparency.
Lastly, in terms of application, LDPE injection molding is commonly used in the flexible packaging industry, while HDPE injection molding is suitable for rigid containers and parts with wear resistance requirements.
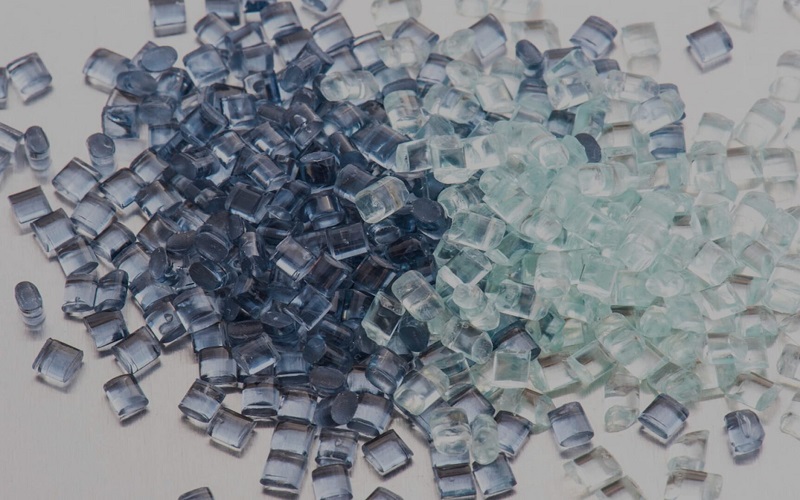
FOWMould’s Custom LDPE Injection Molding Services
As the leading injection molding service provider in China, FOWMould offers top-notch one-stop injection molding services.
If you need customized LDPE injection molded products, we have advanced manufacturing equipment, resources, and a professional technical team to provide the highest quality service.
This means that the injection molded products we help you manufacture are competitive in terms of both quality and price.
Additionally, our design team and injection molding engineering experts have professional expertise and extensive manufacturing experience in injection molding processes.
If you want to learn more about LDPE injection molding services, contact us now. We will provide a free quote for your drawings within 24 hours. Take action now!
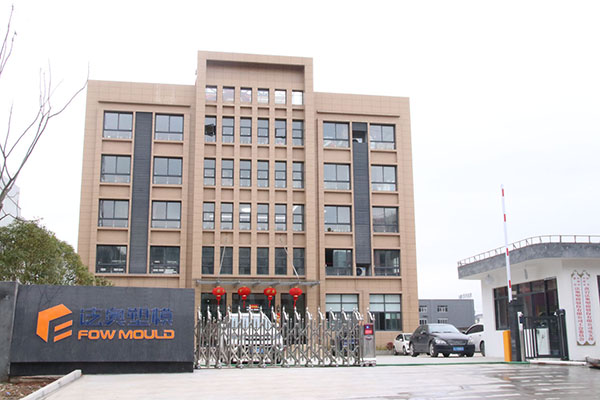
Conclusion
Relying on the unique material properties of LDPE, low-density polyethylene (LDPE) injection molding has secured a significant position in the modern manufacturing field.
From food cling films to medical equipment, the extensive application of LDPE injection molding underscores its irreplaceable role in the manufacturing industry.
If you’re in the hunt for an efficient, environmentally-friendly, and innovative plastic injection molding process, LDPE plastic molding would be an excellent choice. Embark on a new injection molding journey with FOWMould!