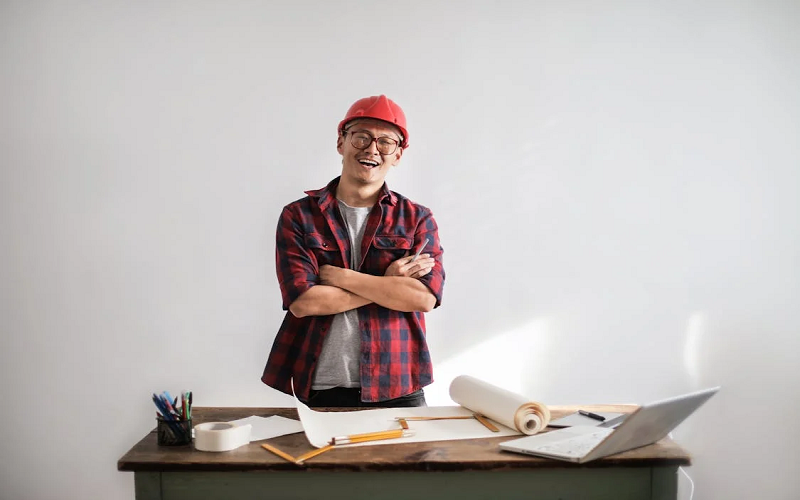
Share :
Share :
Plastics are used in a wide range of items that many of us use on a daily basis. When compared to metals and wood, plastics are less expensive, lighter, simpler to shape, and can be manufactured to any size. However, compared to more durable materials, one of the major disadvantages of plastics is their poor flexibility. However, this problem can be solved by implementing a rib design. Mold makers around the world implement several design methods to ensure the robustness of their plastics. This article will talk in detail about what plastic rib design is and a detailed guideline about how to reinforce plastic and increase its rigidity by using ribbed structures. Read on.
Ribs are an essential part of plastic designing. They are instrumental in increasing the bending stiffness of plastic without increasing the thickness of its walls.
Bending Stiffness = E (young’s Modulus) x I (Moment of Inertia)
Since Moment of Inertia and Bending Stiffness are directly proportional, increasing the former will lead to an increase in the latter. Ribs do exactly that because its presence in your injection mold design increases the bending stiffness of your plastic product.
Ribs are slim wall-like entities that give injection moulded parts support and strength. They are narrower than primary walls and run perpendicular to these structures to support these walls. To minimise sink marks, distortion, and voids, ribs are frequently used to replace thick wall segments. Instead of making a piece thicker, you may keep the support and stiffness you desire by putting ribs in a load bearing direction, such as lengthy unsupported stretches of your part. At the same time you can easily avoid the challenges posed by thick walls.
Here are some of the essential recommendations you need to remember while reinforcing rib design in your parts to increase its robustness.
Thick ribs can be highly disadvantageous for you. If a rib is excessively thick, it will thicken at the area where it connects to the main wall or boss. Sink marks, voids, and warp can readily occur when there is extra material. Sinks, in particular, are apparent signs of poor engineering, which will have an impact on the final appearance of your item. Sinks and voids, if severe enough, can diminish a part’s strength by acting as concentrated stress points.
To ensure maximum bendability and to prevent shrinkage in your injection molding products, the ideal rib thickness should be 105 to 0.75 times the wall thickness of your plastic products.
It’s crucial to remember that not all materials shrink at the same pace. Plastics with a high shrink rate should be made thinner, whereas those with a low shrink rate should be made thicker. Because low shrink materials do not exert as much pull on the surface or on the adjoining thin walls as high shrink materials do, they are less prone to sink or distort.
It is not advisable to have sharp corners in your rib base because they result in stress concentration. Sharp corners in your advanced prototype molding parts result in high stress formation on the body of the plastic, lowers material flow inside or through the plastic, and also reduces the plastic’s part strength.
The formation of areas of concentrated stress is highly detrimental to your plastic because they result in quick wearing of your product. Hence, to avoid a region of concentrated stress in the component, the base of a rib should always be rounded with a radius. Sharp corners also slow the flow of plastic down into the rib, which means it may not be able to fill completely before the material cools, resulting in voids. As a result, the recommended base of a rib is 0.25-0.5 times the width of the nominal wall. It should have a minimum radius of 0.010 inches.
Instead of increasing the height, the number of reinforcing ribs should be raised to enhance the rigidity of the product. However, there is a flip side to this. Although having several ribs provides additional support, you don’t want them to make a cluster. If the ribs of your appliance injection moulding are any closer than that, the ribs will be unable to cool rapidly. This implies the component will have to stay in the mold longer before it can be removed, lengthening the cycle time of your product and increasing the cost of the part. Additionally, rib spacing is ribs that are too close together may result in thin parts of your mold. These are the places where mold damage is most likely to occur.
Too-tall ribs might break during usage or ejection from the mold. Hence, rib heights should never exceed thrice your nominal wall thickness. If tall ribs are damaged during ejection, it is most likely owing to draught angles that narrow these ribs to slivers at their very ends. To avoid unnecessary damage that reduces the worth and functionality of your products, the ribs should be made as short as possible.
The plastic may not be able to reach the rib’s tip if you add one tall rib instead of numerous small ones. Additionally, if the plastic is unable to flow into the very tip of the rib, it can lead to the formation of voids. Thus, it is always advisable to have numerous ribs in your products.
Ribs, like the bulk of injection molded components’ surfaces, should always be drafted. The drafting of ribs is a crucial step in the rib designing process because they may be removed without breaking or damaging them. For the easy removal of plastic parts from your injection mold, the draft angle is implemented. The ideal draft angle for the outer rib is 0.5 degrees, while in the inner rib it is 0.25 degrees. In addition to the recommended draft angle, the inclusion of a rib intersection is also advised because it prevents excessive sinking on the rib’s opposite sides.
If you are a designer of plastic parts, there are several challenges that you have to face. However, an intelligent designer will keep their eyes and ears open for any adversities that they might encounter. Additionally, it will also help greatly if you keep the following factors in mind.
The key to excellent mold making is keeping your eyes open at all times. Keep an open mind. Seek to comprehend and be informed on the problems surrounding your design. Understand the rationale and reasoning behind the earlier art-based designing concepts and principles. You might benefit a lot by following them.
Find out if there are structures that are equally durable without ribs or if there are structures that can resist the stress concentration formed due to a thin ribbed design. Research about the threats posed by your design and do not settle for a pre-done and mechanical structure.
If the aesthetics of your plastic rib design are important to you, and you’re aware of the dangers of residual stressors and warpage, assess the severity of the danger. Evaluate the limitations of these design principles, as well as their link to the polymer’s properties and the resulting tooling and process needs.
Although guidelines are really instrumental while designing anything including furniture molding, at the same time, it is smarter not to follow them blindly. Use your own creativity and engineering to create your own designs. What is state-of-the-art today will definitely go out of practice a few days later. Hence, your creativity and the ability to think out-of-the-box is of paramount importance here. Do not settle for the common practices of the day. Instead, it is recommended that you conduct thorough research and find out some of the other ways to design ribs.
Please contact us using the form below or emailing (harry@fowmould.com)