Nylon is the common name of polyamide polymer, is the second only to polyester textile synthetic fiber.
Among the different types of nylon, nylon 6 and nylon 66 stand out for their unique properties.
In this article, we will conduct a comprehensive comparison of nylon 6 and nylon 66 to help those who want to understand nylon materials to provide more effective information.
Introduction to Nylon 6 and Nylon 66
Nylon 6, also known as polyhexamethylene adipamide, is not precisely a condensation polymer since its polymer contains all the atoms of the caprolactam monomer.
Polyhexamethylene adipamide, commonly known as Nylon-66, is a thermoplastic resin generally produced by the condensation polymerization of hexamethylenediamine and adipic acid.
In the polymer chain of Nylon-66, hexamethylenediamine and adipic acid alternate, making it distinct from other polymers (such as proteins) in that the direction of its amide groups also alternates continuously.
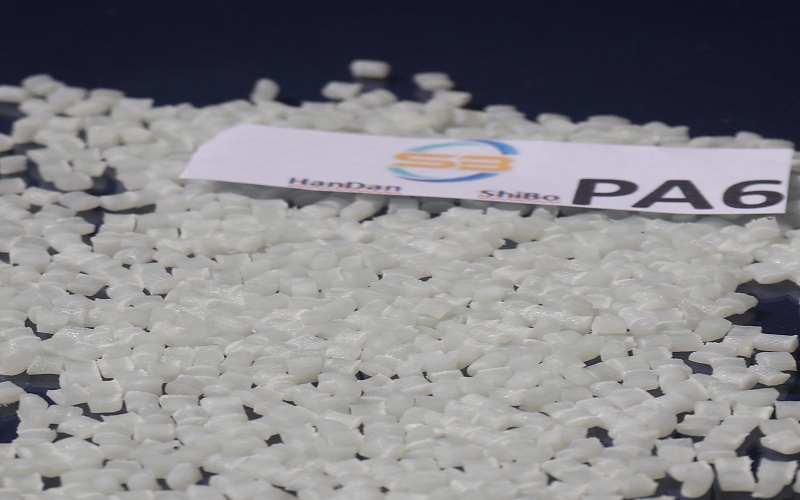
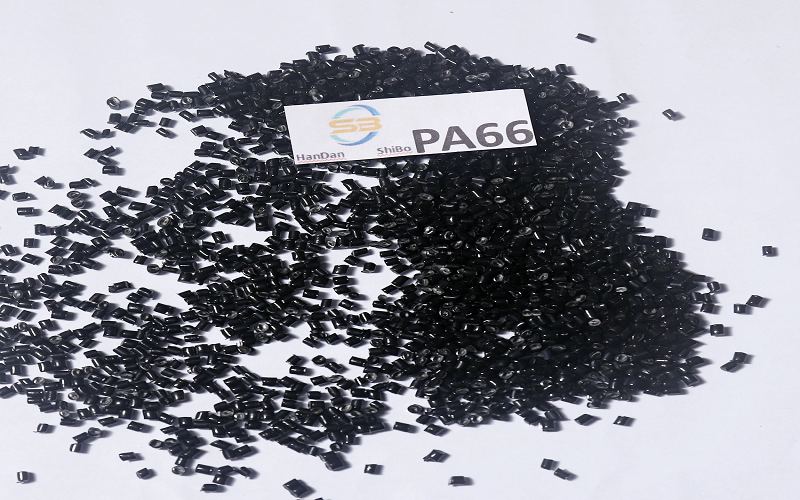
Origin Of Nylon 6 And Nylon 66
In 1935, W.H. Carothers at the American company DuPont successfully researched the synthesis of the “Nylon 66” polymer through the condensation of hexamethylene diamine and adipic acid.
Between 1936 and 1937, the technique for producing Nylon 66 fibers using melt spinning was discovered.
By the end of 1939, this innovation was industrialized by DuPont.
In 1938, Schlack at the German company IG Farben successfully developed a process to create polyhexamethylene adipamide (Nylon 6) using caprolactam as the sole raw material, with ε-aminocaproic acid as an initiator in a heat-driven polymerization process.
Experimental production of Nylon 6 fibers began in 1939. In 1943, it was industrialized by the German company Farben.
Today, Nylon 6 and Nylon 66 are the main varieties of polyamide fibers.
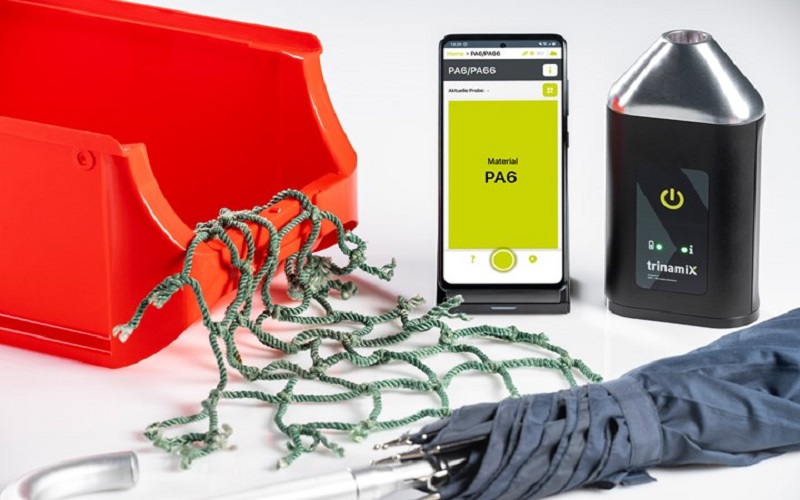
Production of Nylon 6 Versus Nylon 66
The polycondensation process of Nylon 66 salt takes place in a 50% aqueous solution at 250-270°C under a pressure of 16-17 kg/cm².
The polymerization lasts for 2-3 hours, resulting in a Nylon 66 polymer with an average degree of polymerization of about 100.
For Nylon 6, the polymerization of the caprolactam monomer initially involves a hydrolytic reaction in the presence of water, leading to ring-opening of caprolactam and subsequent addition with the formed aminocaproic acid.
The ring-opening reaction under conditions of 230-250°C takes about 30-40 minutes.
The entire process from heating to polymerization requires only 1 to 1.5 hours.
After 3 hours, the relative viscosity can reach a spinnable viscosity of 2.2.
However, achieving equilibrium takes a longer time since the removal of water during the polymerization process is relatively slow.
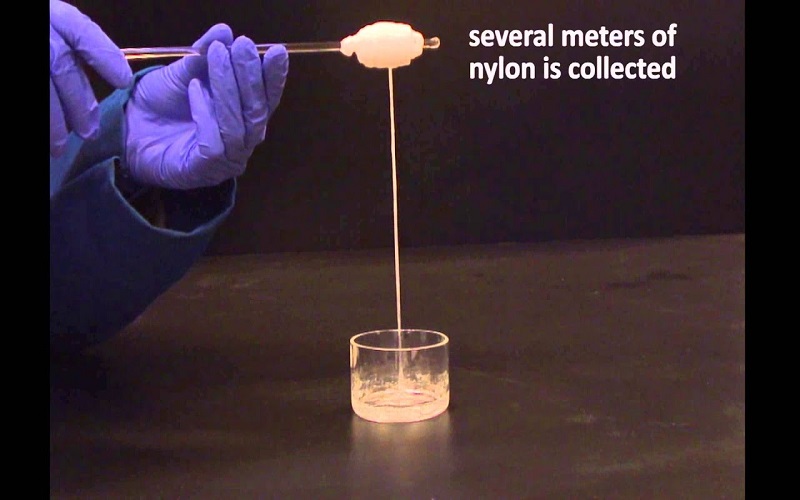
Properties of Nylon 6 VS Nylon 66
From a molecular structure perspective, both Nylon 6 and Nylon 66 consist of the same ratio of carbon, hydrogen, oxygen, and nitrogen atoms.
However, the monomer caprolactam in Nylon 6 undergoes ring-opening polymerization in a head-to-tail fashion to form polyamide.
In contrast, Nylon 66 is formed by the alternating arrangement of hexamethylene diamine and adipic acid to create the polyamide.
The difference in monomer materials leads to distinct polymer structures and physical properties between them.
Performance Differences Between Nylon 6 and Nylon 66 | ||
| Nylon6 | Nylon66 |
Chemical formula | (C6H11NO)n | (C12H22N2O2)n |
Density(g/cm3) | 1.13 | 1.14 |
Melting point(℃) | 215 | 250 |
Water absorption(%) | 2.7 | 2.5 |
Molding shrinkage(%) | 0.7-2.0 | 1.5-2.2 |
Glass transition temperature(℃) | 59 | 70 |
Crystalline organization | Loose structure | Tight structure |
Color fastness | Easy to stain | Difficult to stain |
Hand feeling | Loose | Dense |
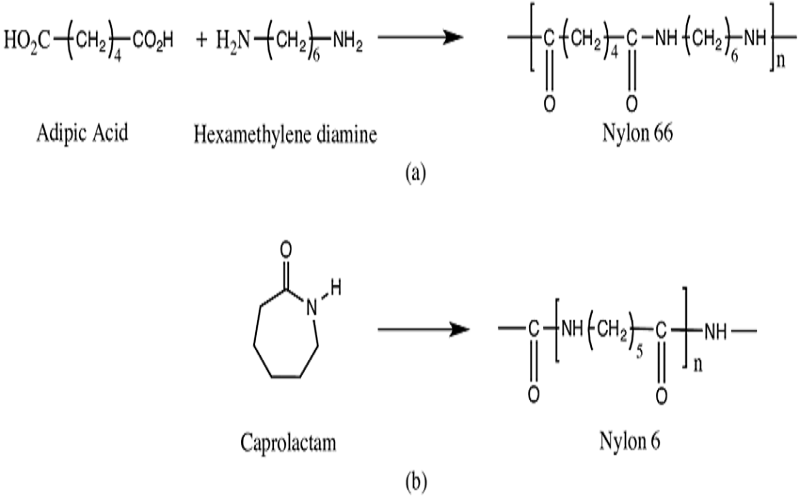
Nylon 6 shares many chemical and physical properties with Nylon 66, yet it has a lower melting point and a wider processing temperature range.
It offers better impact resistance and solubility resistance compared to Nylon 66 plastics, but also has a higher moisture absorption.
As many quality characteristics of injection-molded parts are influenced by moisture absorption, this factor must be carefully considered when designing products using Nylon 6.
To enhance the mechanical properties of Nylon 6, various modifiers are often added.
Glass fiber is the most common plastic additive, and sometimes synthetic rubbers like EPDM and SBR are included to improve impact resistance.
Due to Nylon 6’s propensity to absorb moisture, special attention to pre-processing drying is crucial.
If the material is supplied in waterproof packaging, the container should remain sealed.
If the humidity is greater than 0.2%, it is recommended to dry in hot air above 80°C for 16 hours.
If the material has been exposed to air for more than 8 hours, a vacuum drying at 105°C for over 8 hours is advised.
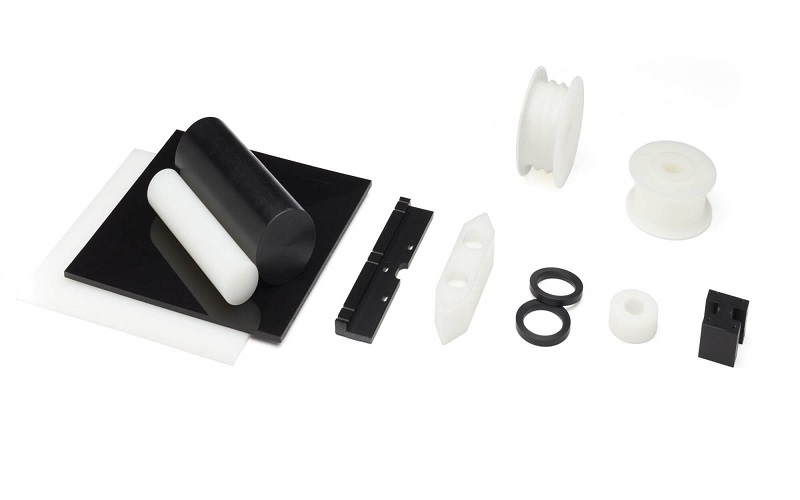
Although both materials have their unique characteristics, they also share many core performance features:
- Good abrasion resistance
- High mechanical strength
- Strong resistance to radiation
- Not resistant to strong acids, but both exhibit a certain level of alkali resistance
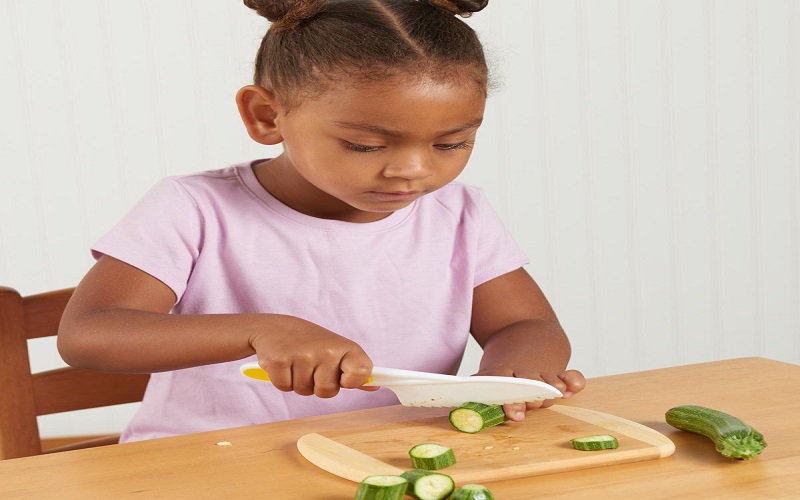
Application Comparison of Nylon 6 And 66
Nylon 6 and Nylon 66 are key members of the nylon family, playing significant roles in many application areas.
Due to Nylon 6’s lower melting point and excellent processability, it is often used to manufacture lightweight textiles and industrial parts.
These characteristics make Nylon 6 an ideal material for nylon injection molding, allowing for easy formation into various parts such as automotive interiors, household appliance components, and sports equipment.
Additionally, the elasticity and wear resistance of Nylon 6 make it a perfect choice for textiles like socks and sportswear.
On the other hand, Nylon 66, with its higher melting point and superior mechanical strength, is more suitable for applications requiring high temperature resistance and strength.
In nylon injection molding processes, Nylon 66 is commonly used for producing wear-resistant and high-pressure components, such as engineering plastics, automotive engine parts, and electronic devices.
Furthermore, the high-temperature stability and strength of Nylon 66 make it an indispensable material in the automotive and aerospace industries.
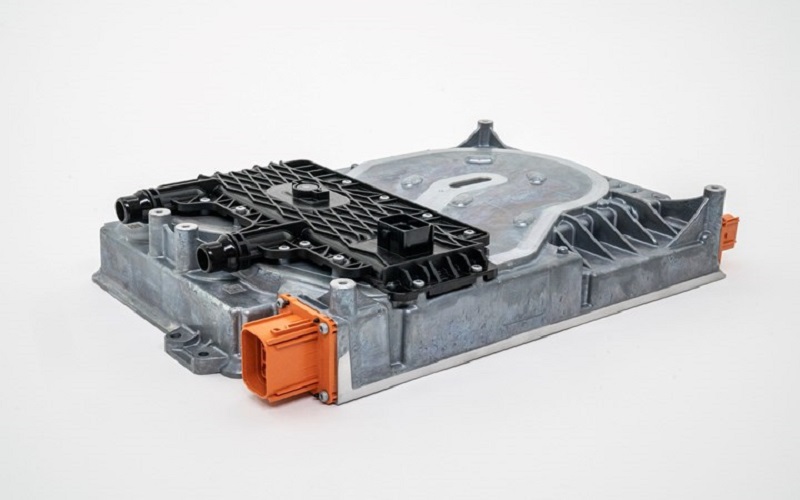
Other Common Nylon Grades
Nylon 610 and 612 are favored in the electrical insulation sector due to their low moisture absorption characteristics, but this trait also contributes to their relatively higher cost. Nylon 610 is renowned for its low moisture absorption and extremely low brittleness temperature.
Nevertheless, Nylon 612 is gradually replacing Nylon 610 because it offers not only a lower cost (although still higher than Nylon 6 and 66) but also superior heat resistance.
In terms of performance, Nylon 612 typically sits between Nylon 6 and Nylon 66, exhibiting slightly better creep properties than Nylon 66 under humid conditions.
Nylon 11 and 12 are also preferred for their low moisture absorption, particularly Nylon 12, which has the lowest moisture uptake among all unfilled nylons.
These materials surpass Nylon 6, 66, 610, and 612 in flexibility and impact strength, but they come at a higher cost, have lower strength, and a lower maximum service temperature.
They possess the best weathering resistance in the nylon family, although their status is being challenged by the emergence of super-tough nylons (which are essentially alloy materials).
Nylon 1212 offers better performance than Nylon 6 and 66 and is more cost-effective than Nylon 11 or 12.
Under high-temperature conditions, Nylon 46 demonstrates high impact strength, low creep, and higher stiffness.
It has better fatigue properties compared to Nylon 66, but it has a narrower processing window.
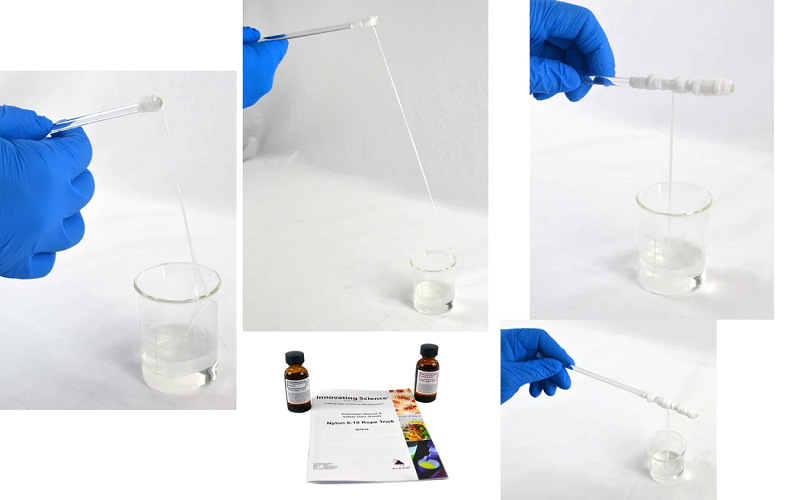
Conclusion
When selecting a type of nylon, it’s crucial to consider the specific requirements of the application.
Understanding the unique characteristics of each type of nylon can help us make more informed decisions, ensuring that the material chosen aligns closely with the performance requirements and cost-effectiveness of the application.
If you are interested in nylon injection molding, please contact us!
FOWMOULD will provide you with the most professional one-stop injection molding services and the highest quality nylon injection molded products.