As innovations in plastic manufacturing continue to advance, insert injection molding technology serves as a foundational technique, bridging different materials and cutting-edge manufacturing technologies.
Insert injection molding seamlessly integrates different materials, such as metal and plastic, into a single component, ensuring a tight bond between the insert and plastic, combining strength and flexibility.
This article will delve into the concept, process, advantages and disadvantages, and application range of insert molding, uncovering the mysteries of this complex molding technology.
What Is Insert Injection Molding?
Insert molding is a process where inserts are pre-positioned in the mold, and then plastic is injected to form the part.
Once the mold opens, the inserts are encased in the cooled and solidified plastic, resulting in products with embedded components such as threads or electrodes.
The simplest method of inserting inserts is manually or using robots to place the separately manufactured inserts into the mold cavity.
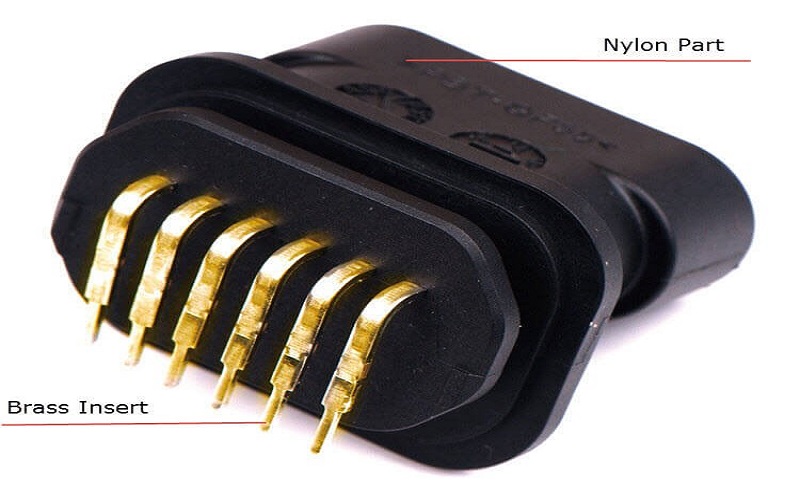
Steps of The Plastic Insert Molding Process
Insert injection molding is a specialized technique within traditional injection molding processes.It embeds metal or other material parts into molten plastic, creating an integrated component.Here are the steps to successfully execute plastic insert molding:
1.Placing Inserts into the Mold
Before the injection molding process begins, inserts must be manufactured according to precise specifications to ensure they match the dimensions and shape of the mold.
Special slots or cavities are designed to ensure accurate placement of these inserts.
There are two main methods for placing inserts:
- Manual Placement:
This method significantly increases the injection molding cycle and is suitable for small batch production or products with complex structures.
- Automated Placement:
This is the better choice for mass production, as it helps reduce human error, increase efficiency, shorten the injection molding cycle, and improve product reliability.
2.Injecting Molten Plastic into the Mold
Once the inserts are securely in place, molten thermoplastic resin is injected into the mold.
Under high pressure, the molten plastic is forced to fill all parts of the mold, and venting holes ensure that air is expelled, allowing the plastic to completely encapsulate the inserts.
3.Solidifying the Plastic in the Mold
After injection, the mold is maintained at a set temperature to allow the plastic to solidify evenly.
During this cooling phase, the plastic and inserts fuse together, forming a unified bond.
4.Separating Molded Parts from the Gates
In the insert molding process, the molded parts are connected to the gates.
It is essential to use specialized tools and precise operations to carefully separate them from the gates to avoid damage or quality issues.
5.Post-Processing
After demolding, the molded parts may require further treatment to meet final product requirements.
These treatments may include:
- Deburring
Removing excess plastic or flash, usually done manually with simple tools.
- Heat Treatment
Eliminating internal stress through heating to improve the quality of the molded parts. The treatment temperature should be 10-20 degrees Celsius higher than the part’s service temperature but lower than its deformation temperature.
- Surface Treatment
Choosing a surface treatmentmethod based on design requirements, such as surface printing or electroplating. Different surface treatments can enhance material strength, physical properties, or aesthetic appeal.
- Humidity Control
Placing molded parts in hot water at 80-100 degrees Celsius to speed up moisture absorption, stabilize dimensions, and prevent oxidation.
Following these steps, insert-molded parts can achieve the desired quality and appearance standards.
What Materials Are Used In Insert Molding?
Due to the material compatibility of the injection molding process, a variety of materials can be used in insert moulding.
This allows for the creation of plastic components that integrate multiple properties.
- Thermoplastic:Polyethylene(PE),Polystyrene (PS),Nylon(Polyamide, PA),Polypropylene (PP)and ABS;
- Thermoset:Phenolic Resins,Epoxy Resins,Melamine Formaldehyde,Urea Formaldehyde
- Elastomers:Natural Rubber,Polyurethane,Thermoplastic Elastomers (TPE)
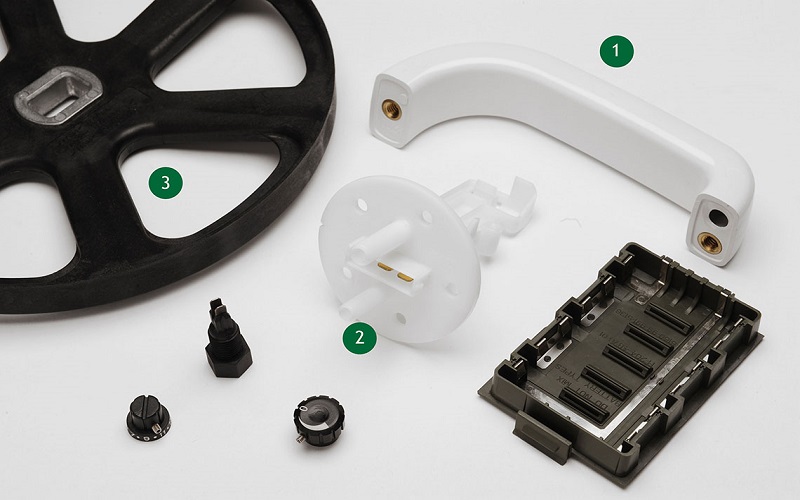
How to Design Inserts for Insert Molding
To ensure successful insert molding, it’s essential to consider the process characteristics and design inserts scientifically. Here are key points:
Selection of Insert Material
Choose materials with thermal expansion coefficients similar to the plastic used. Suitable materials include copper, aluminum, steel, ceramics, glass, and plastics.
Structural Form of the Insert
Inserts should be round or axially symmetrical, avoiding sharp edges to ensure uniform shrinkage and prevent stress.
Surface knurling or grooving increases friction, securing the insert in the plastic.
Placement of the Insert
Inserts should be placed in bosses or raised areas, with the depth greater than the height of the raised area for strength.
Symmetrical placement of multiple inserts prevents bending or deformation.
Increasing wall thickness in stress-prone areas can also help.
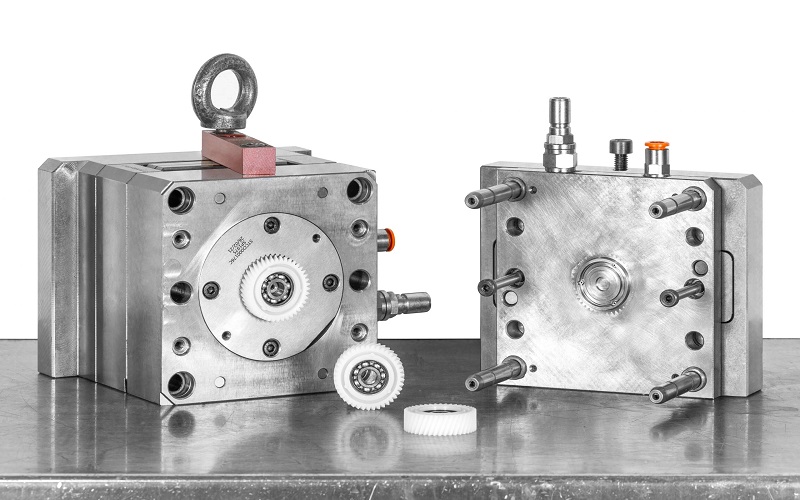
Considerations During Insert Injection Molding
Before undertaking insert molding, injection molding companies need to consider several factors to ensure the success of the process and the quality of the products.
Here are some key considerations:
Type of Inserts
Choosing the right type of insert is the primary consideration. Inserts must withstand the extreme temperatures and pressures that may occur during the molding process.
Common insert materials include metals, glass, and preformed plastic parts.
facilitates the easy placement of inserts and ensures their accurate fixation during the injection process.
Insert Location
The location of the insert is crucial to its functionality and long-term stability.
The chosen location must not only consider the role of the insert in the product but also ensure that there is enough plastic to hold the insert in place, preventing it from becoming loose or shifting during use.
Narrowing the Gap Between Metal Inserts
Since the material is molten when it bonds with the metal insert, the gap between the metal insert and the molten material can be designed to be narrower compared to press-fitting methods. This results in higher reliability for composite product molding.
Selection of Resin and Molding Conditions
Selecting the appropriate resin and molding conditions is critical, especially for products prone to deformation or damage, such as glass, coils, and electrical components.
The right resin can also provide sealing and fixation.
Choosing the Right Mold
The mold determines the shape of the molten material and plays a role in securing the insert during the molding process.
Therefore, selecting a mold that can firmly hold the insert in place is key to successful insert molding.
Cost
Cost is a crucial factor in insert molding. This includes the cost of the inserts, the cost of hiring operators, and the increase in unit price due to the addition of inserts.
For more information on the design elements of insert molding, click here to read!
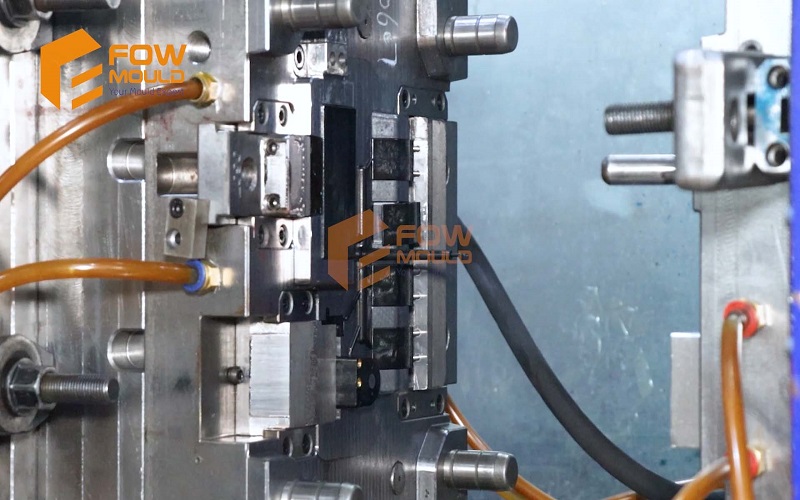
Advantages And Disadvantages Of Injection Molding Insert
Insert molding is a technology that integrates two or more materials during the injection molding process.
It offers several notable advantages:
Reduced Assembly Time
Compared to traditional assembly methods, insert molding can complete the assembly of two or more parts in one step, significantly reducing production cycles and process steps.
Enhanced Performance
By embedding high-strength materials like metal, the product can combine the flexibility of plastic with the strength of the insert, improving overall mechanical performance.
Design Flexibility
Different materials can be combined in a single component, allowing for more flexible designs to meet various functional requirements.
Improved Product Quality
Insert molding ensures a tight bond between the insert and the plastic, reducing the risk of loosening or shifting, and enhancing the reliability and durability of the product.
However, this process also has some drawbacks:
Complex Design Requirements
Compared to traditional assembly, insert molding requires consideration of more factors, such as the insertion angle and perpendicularity, leading to more complex mold designand higher demands on the process and equipment.
Precision Control Needed
If the insert position is not accurate or the pressure, temperature, and time controls are inadequate, the insert effect may be suboptimal, affecting product quality.
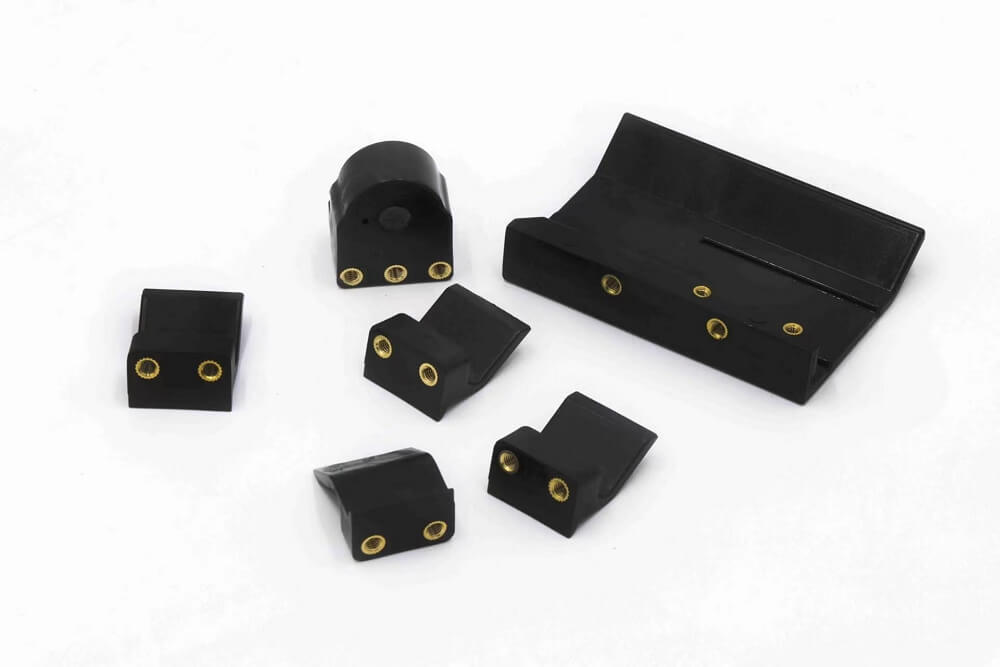
Applications Of Insert Injection Molding Parts
Plastic insert molding allows for a seamless combination of materials to produce quality, durable and innovative products. Its versatility and benefits make it a popular choice for a wide range of industries.
Electronics Industry
One of the most common application areas for plastic insert molding technology is the electronics industry. Parts such as terminals, connectors and pins, for example, are often embedded in plastic housings. This provides insulation, structural support and protection from environmental factors while maintaining electrical conductivity.
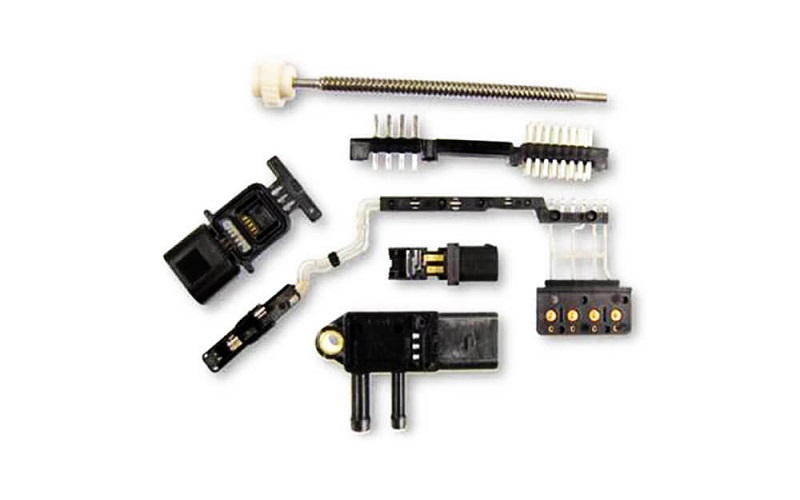
Automotive Components
The combination of metals and plastics used in insert molding technology is utilized to manufacture many automotive components such as sensors, switches and electronic controls. This reduces weight while ensuring durability – a key factor in automotive design.
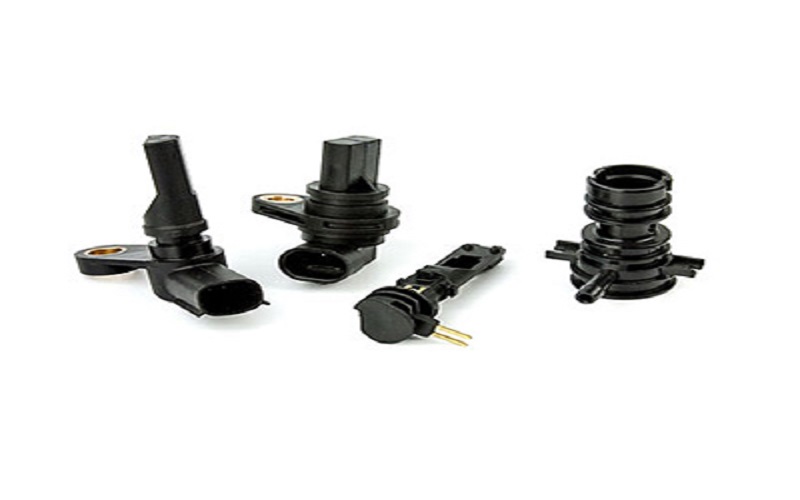
Medical Devices
In the medical industry sector, insert molding technology is used to produce a variety of medical devices, including surgical instruments with ergonomic plastic handles and components for wearable medical devices. The insert molding process is widely used in this industry for its ability to sterilize integrated products and ensure patient safety.
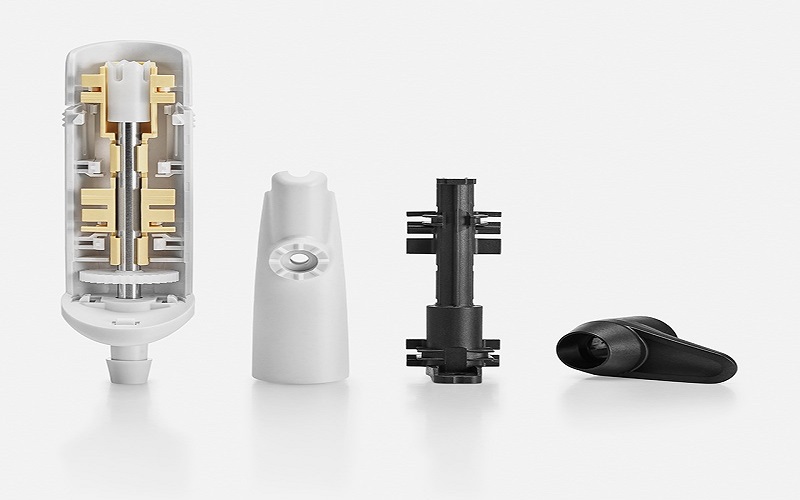
Consumer Products
In everyday life, insert molding is used to integrate metal components into plastic designs for the production of items such as toothbrushes, kitchen utensils, and power tools. The objective is to enhance the product’s functionality, durability, and overall user experience.
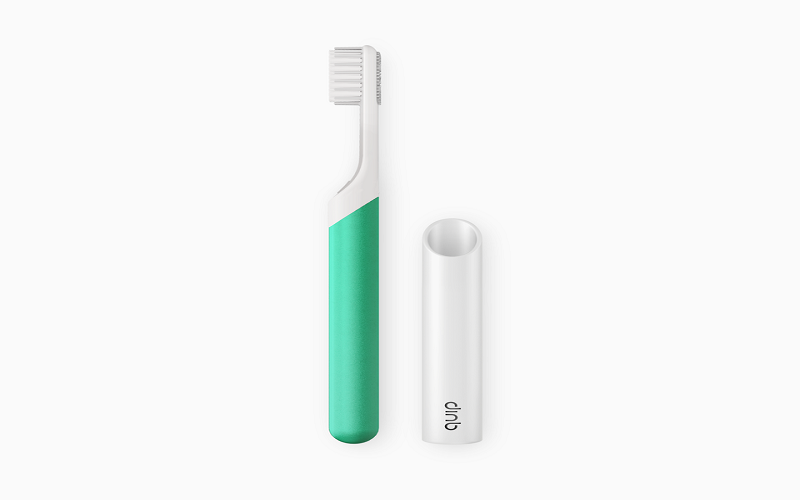
The pie chart below shows the distribution of injection molded inserts in different application areas.
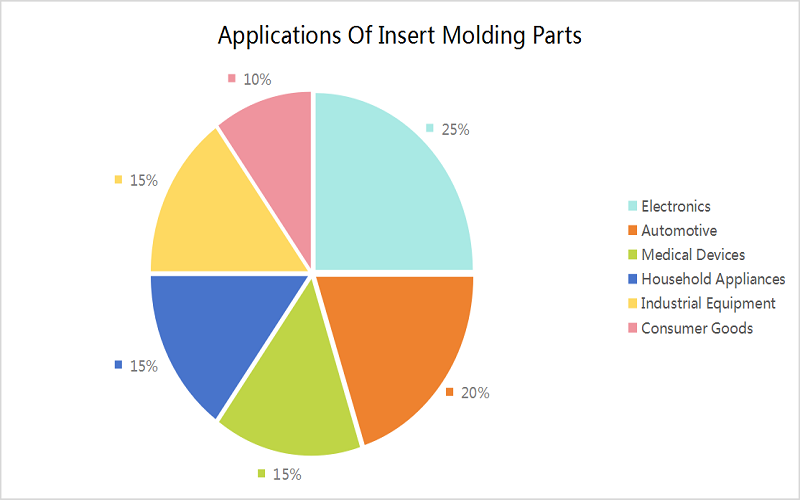
Insert Molding vs Overmolding
Insert molding and overmolding are two common methods in plastic molding technology, both involving the combination of different materials, but they differ significantly in their processes.
Insert molding is a process where pre-prepared inserts of different materials are placed into a mold, and then resin is injected, causing the molten material to bond with the inserts, forming an integrated product.
One of the most common applications is metal insert molding. By embedding metal inserts into plastic, products can have the strength of metal and the flexibility of plastic.
This not only speeds up the molding process but also reduces the amount of material used.
On the other hand, overmolding is a secondary injection molding process where one or more layers of different materials are applied over an existing plastic part (substrate).
These overmolded layers are usually different types of plastics or rubber, which improve the product’s feel, appearance, or add functionality.
However, this process also increases manufacturing costs.
To learn more about the differences between these two processes, please click to read “Insert Molding vs Overmolding“.
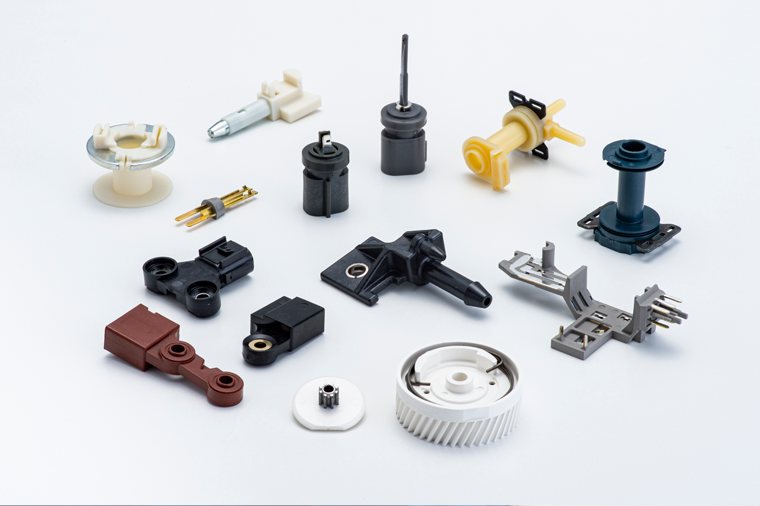
Custom Insert Molded Parts Service
Are you still searching for a reliable insert molding service but unsure if it can meet your part manufacturing needs?
Look no further—FOWMOULD is your most trusted injection molding partner.
Our professional design and manufacturing team will offer you expert advice and provide free quotes for your project!
We are dedicated to offering you one-stop injection molding services and solutions.
Contact FOWMOULD now to start customizing your insert molded parts!
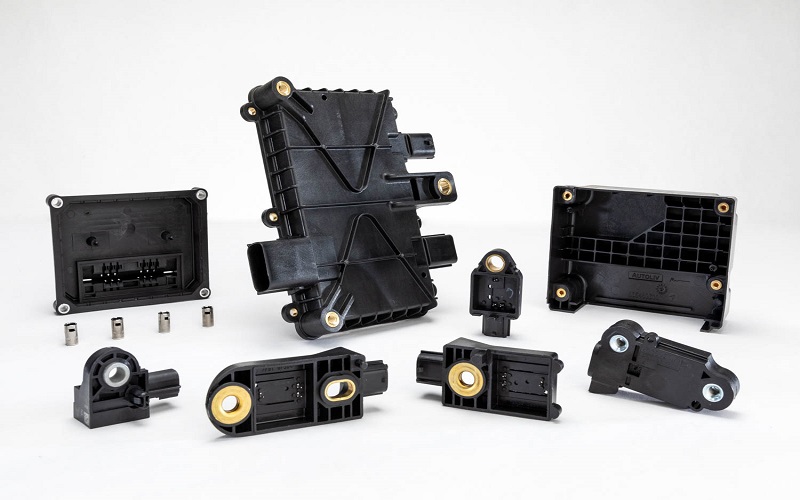
Conclusion
In summary, insert molding is a process that molds thermoplastic material around a pre-formed component (insert) to create parts that incorporate multiple materials.
Due to its efficient and high-precision characteristics, and the ability to combine the advantages of metal and plastic, it is widely used in industries such as medical, automotive, and consumer products.
If you are looking to start a new insert molding project, contact FOWMOULD. We will customize high-quality molded parts to meet your specific needs.