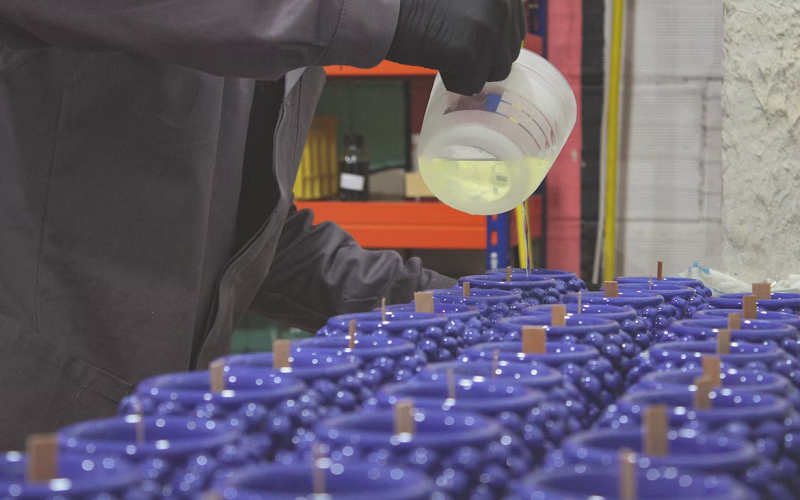
Share :
Share :
Injection molding is a process that needs to take multiple conditions in mind for the perfect product result. Many different materials are used by manufacturers in injection molding. What also needs to be taken into account during this procedure is that the tolerances of different materials used in molding are different. Each plastic polymer has different tolerances, which in turn will impact the product you are molding. Knowing the base material’s tolerance will help the manufacturers with the determination of the final cost of the manufactured product. In the molding market, mold manufacturers offer two types of injection molding tolerances, namely commercial and fine mold tolerance.
Both the moldability of the product and the cost of the injection molding process depend on the tolerance of the material. On a drawing, it is advised only to indicate the critical dimensions needed to establish the tolerance of a material. Commercial tolerance is preferred by manufacturers and buyers because it is cheaper. It is cheap because this tolerance is less strict than fine tolerance. Since fine tolerance produces the tightest tolerance possible, it requires specialized products, and the manufacturing costs of the product increase.
A practical tolerance limit is needed during production to minimize the many problems that might occur during the injection molding process. Some of these issues include warpage which happens due to uneven drying and shrinkage, not an option for sound mold design, the position of the gate and its size, and the choice of the material for a particular project.
Many factors like shrinkage of the material, the drying time, and the flow rate of the material are a part of common knowledge for the manufacturers. There might be minimal variations in parts depending on the material and the molding conditions. More significant variations and distortions can be avoided if the tolerance of the material selected can be taken into account. Greater variations are not accepted, and tolerance standards need to be set across the industries. These limits and standards are important because some parts of the molded products might not fit well together if the distortions are too great and tolerance limits are relaxed.
Typically, the injection molds across the molding industry are set to a machine tolerance of +/- 0.005 inches. These can be adjusted as per the needs of specific projects as well. Tighter tolerances will demand a variation of no less or more than 0.002 inches. Very tight tolerance supports a variation of +/-.001 inches. If a project demands tight or very tight tolerance, more specialization would be required, which makes the molding process all the more expensive than it is when the tolerances are as per the industry standards.
Following are some measures and tips that can help engineers and manufacturers with the tolerance of injection molding:
Choosing the right material for injection molding is of utmost importance. Material selection involves choosing from a wide variety of plastic resins. Depending upon the type of material used, the manufacturer might have to add additives to the resin for strength, elasticity, or stabilizing. Depending upon the characteristics needed for the product, the appropriate material can be chosen for the molding. The cost of the additives, the tools, and the manufacturing process would have to be considered before manufacture.
Different resins have different physical and chemical properties. They also have different rates of shrinkage and react differently to injection molding techniques. The design of the molding tool, the characteristics of the materials, and the application of the product to be constructed need to be factored in together while selecting the right product for injection molding. Different shrink rates would mean that for products made from different materials to be attached together, their manufacturing needs to be done after considering their response to the molding process.
During product design, it is the responsibility of the designer to make a mold that holds the material during the molding process, allows for proper setting with minimum shrinkage and no warping, and does not need redesigns. If a product has to require redesigning sometime later, it is less cost-effective for the manufacturer. Each and every designer should follow the industry standards while designing a mold and should think of manufacturability as the end goal for their product.
Some of the standards that should be followed include a uniform thickness of walls and the correct placement of draft angles. This will prevent shrinkage and warpage and will also help with the molding of high tolerances. Support ribs can also be added to the design, which does not require thick walls to increase the strength of the product. Bosses in injection molding are parts that are used to attach different molded parts together when it is time to assemble them. Bosses need to be aligned at the sidewalls of the modeled part to prevent warping in the product.
The tools used in injection molding primarily include the molds in which the liquid resin would go for setting. Generally, designers make the molds a little bigger than the intended size of the product as there is some extent of product shrinkage during the modeling process. The design of the mold should be in accordance with the material to be used in it, as the shrinkage rates of different materials are different. Different molds are important so that the products made follow the injection molding tolerance standards.
The mold tooling needs to be consistent with each repeated cycle for uniformity in product and less warpage. Heating and cooling during the molding cycle should be on point to keep up with the strict tolerance standards for a particular project. While heating can be uneven, which can lead to distortions in the product, uneven cooling can cause warpage and deviations from tolerance requirements. Engineers in charge of tool design can factor in the material viscosity, injection pressure, and the fill time; the designer can make sure that the pressure drop does not cause distortions in the mold.
Apart from the heating and cooling variations and the pressure difference, the location and size of the gate in the mold also impact the tolerance during injection molding. The right gate location will reduce the chance of the creation of a pressure drop and will henceforth prevent any warping from taking place. Location of the ejector pins is equally important, and the consistency of the product dimension is impacted in case the mold is removed when the product is not thoroughly cooled.
The tooling process, much like the insert molding process, is very minutely looked into for optimal production. The tolerance in manufacturing tools is also very controlled to ensure that tolerance standards are followed when the tools are used in injection molding. CNC machines ensure that the tools manufactured are refined and tightly controlled in terms of tolerance.
The injection molding procedure is a manufacturing method that is widely used because of its versatile applications. Apart from the benefits of mass production, injection molding involves the involvement of a variety of thermoplastics to create molds that are durable and also in great demand in the market. Since the process can easily be repeated, as many products as needed can be manufactured in a short period of time. The mold making technology, however, needs to be done with the industry standards of tolerance in mind for the best results. The mechanical requirements, along with the characteristics of the material, also need to be looked into for optimal production.
Please contact us using the form below or emailing (harry@fowmould.com)