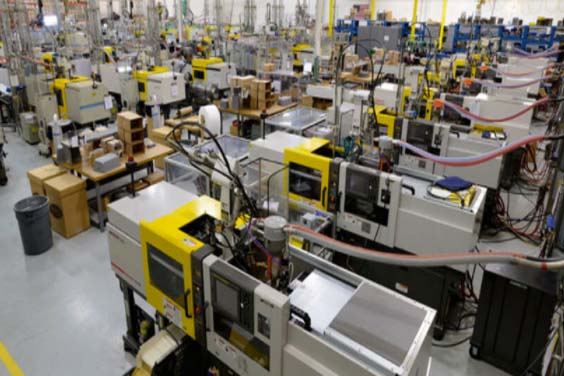
Share :
Share :
In the plastic industry, injection molding is a widely deployed thermosetting process. The process takes in raw plastic and turns them into finished products. The ejector pins of molds into which the molten plastic is injected often leave marks on the products made by injection molding. The causes for the same can be many, but the quality of the final fabricated material degrades as a result.
Ejector pins are long retracting pins that are used to push the solidified material out of the mold. Once the plastic polymer cools down in the mold, the ejector pins force the solidification out from the cast. They go back into the mold to get the thermosetting apparatus ready for the next round.
While the ejector pins do what they are supposed to, pushing out the fabricated product, the marks left by their pressure are a common problem. They usually occur in the form of small convex/concave depressions or as distinctly visible imprints on the material surface. It is essential for injection molding products manufacturers to avoid ejector pin marks for certain reasons, as stated ahead.
The more complicated the product’s design, the more ejector pin marks it is likely to have. However, it is not always the product design that is responsible; several factors lead to these deformities. On the brighter side, ejector pin marks are easy to eliminate. One has to take care of the thermosetting process from beginning to end, along with the suitable materials and correct use of the machine.
When customers buy products such as phone cases, furniture molding, etc., a dentless surface is the first deciding factor. Moulded plastic products with ejector pin marks are more likely to be rejected at the customers’ end.
The sticking of the mold with the plastic while ejector pins push the material out leaves dents and depressions on it. This unevenness compromises the integrity of the products by making them prone to breakage. Consequently, the products with lowered aesthetic appeal and integrity become a deal-breaker for manufacturers.
Almost all the time, the cause of ejector pin marks is not the ejector pins themselves. The ejector pins usually function smoothly, with the problem being elsewhere. While you face the issues of ejector pin marks, you might want to examine whether you are working with the right parameters. These can be categorized into machine parameters, product design, and mould design.
The process of making injection moulding plastic products is not free from errors. Owing to many parameters that go in, defects could be anywhere. A primary role in injection moulding is played by pressure. Holding pressure, the pressure required to set the resin, leads to excessive shrinkage, flashes, and varying dimensions, if not kept within the optimum pressure and speed range.
The sinking of the material where the ejector pins apply force can be due to a higher ejection force than required. This creates stress in the plastic material, causing sticking and pin marks.
Inappropriate temperatures during processing and in the mould cooling system result in concave or convex indentations in the product.
Non-uniform cooling of the mould, which is due to quick cooling time, results in an increase in the internal stress of the material. When the mould is cooled quickly, the temperature of the material’s outer surface lowers while it remains hotter inside. The tension which builds up leads to dimensional instability. Eventually, it becomes harder to detach the finished product from its mould.
When it comes to the mould design, few things are crucial for the successful ejection of the material. Draft angles are one of them. Without a sufficient draft angle in the mold, it gets harder to release the material. The vacuum which gets created between the mould walls and the material creates a suction force. Consequently, the material gets stuck, and while trying harder to push, ejector pins leave indentations on the material surface.
Fewer ejector pins and their placement deeper into the product can be why your ejection system leaves ejector pin marks. Along with these, unbalanced pressure and less pin diameter are also other supplementing factors to the ejector pin mark problem.
Wrong filling of the resin into the mould is one factor determining how much stress the material will carry. The wrong type and dimension of the chosen gate resist the flow of resin into the mould, resulting in increased internal stress in the resin. Multiple unbalanced gates degrade the strength of the finished products as well.
The product thickness should be optimum. If possible, thicker dimensions should be preferred for the places which will be in contact with ejector pins. A thickness of less than 2.5mm is unsuitable since it will be easier for the material to get stuck to the pins. And also, it might not come out of the mold cavity and core.
Churning out flawless products from injection molding is crucial for the proper functionality and aesthetics of products. There are ample measures that technically reduce the impact of ejector pins on the end product. They mainly focus on reducing the internal stress and increasing the dimensional stability of the material.
Injection molding sees broad uses in industries where bulk production is required. The finish of a molded product depends on the final step in the injection molding process: ejection. The technical aspects of creating a plastic product with an excellent cosmetic finish are numerous. Therefore, knowing how to manufacture plastic products comes with a certain experience. It is important to find a reliable manufacturer who provide professional plastic injection molding service.
The takeaway is ensuring that your melt is evenly filled and the mold design is robust. Also, optimum temperature, pressure settings, and sound design of ejector pins are crucial to producing a seamless plastic product. All these measures will guarantee that the end product comes out with no ejector pin marks.
Please contact us using the form below or emailing (harry@fowmould.com)