With the rapid development of manufacturing, 3D printing technology is reshaping the traditional mold manufacturing model.
Compared to traditional CNC machining or handmade mold production, 3D printed molds have become the preferred solution in many industries due to their low cost, rapid iteration, and high design freedom.
Whether used for rapid prototyping, small batch production, or customized parts, 3D printed molds can significantly shorten production cycles and reduce costs.
This tutorial aims to provide beginners and professionals with a clear guide, leading readers through the entire process of designing, printing, and applying 3D printed molds with detailed steps and practical advice.
What Is 3D Printed Mold?
3D printed molds are molds created using additive manufacturing technology. Unlike traditional mold manufacturing methods such as CNC machining or hand carving, 3D printed molds are produced by layering materials according to a digital design.
This technology allows mold manufacturers to quickly transform complex designs into physical molds without the need for expensive equipment or lengthy processing times. The core advantages of 3D printed molds lie in their flexibility, cost-effectiveness, and support for rapid iteration.
They enable the production of customized molds tailored to different product requirements without the necessity of large-scale production lines, thus meeting the needs of personalized and small-batch manufacturing.
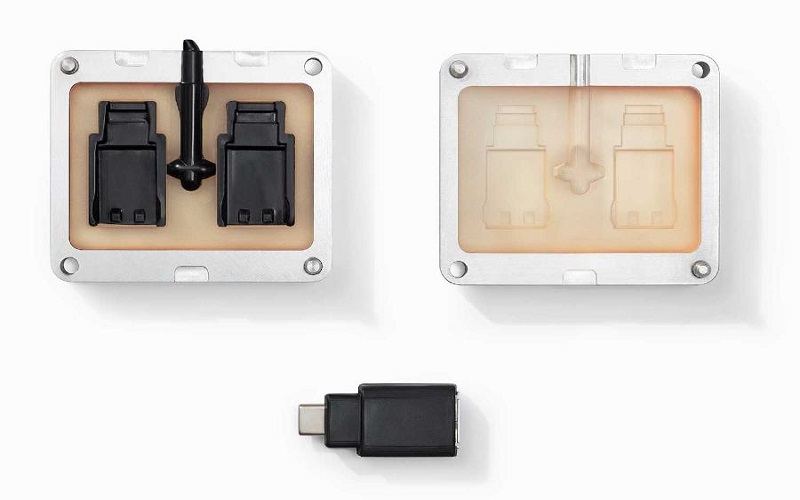
Types Of 3D Printed Mold
3D printed molds can be categorized based on their purpose and manufacturing process into the following types:
Injection Mold
The basic principle of 3D printed injection molds is to use 3D printing technology to build the mold layer by layer according to CAD design data.
In the injection molding process, 3D printed injection molds are typically used for small batch production or prototype testing due to their fast manufacturing speed and low cost.
Although 3D printed injection molds may not be suitable for long-term use under high pressure or high temperature conditions, their performance can be significantly improved by selecting high-strength materials (such as resin or metal composites) or combining post-processing techniques.
Casting Mold
Casting molds are used for casting processes involving metal, silicone, or other materials and are commonly employed to produce parts with complex geometries.
3D printing technology enables the rapid creation of casting molds with intricate internal structures, such as sand molds used in jewelry, aerospace parts, or art manufacturing.
The advantage of 3D printed casting molds lies in enabling one-time or small batch production while reducing the cumbersome steps of traditional sand casting.Keep in mind that a mold printed on an FDM machine will be much more difficult to open once the casting material has cured due to the layer lines.
Prototype Mold
Prototype molds are mainly used in the early stages of product development to help designers verify the design and functionality of parts. Thanks to their rapid manufacturing and low cost, 3D printed prototype molds are particularly suitable for scenarios requiring frequent design modifications.
For example, in consumer electronics or medical device development, prototype molds can be used to test the fit of product housings or the strength of structures. Since prototype molds usually do not require high durability, common 3D printing materials like PLA or ABS are sufficient to meet the needs.
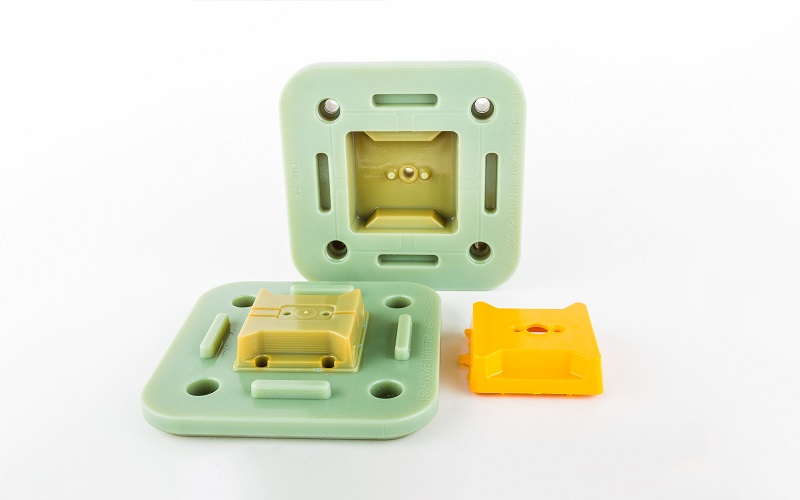
Advantages Of 3D Printing Mold
3D printed molds, as an innovative manufacturing technology, offer significant advantages for rapid prototyping and small batch production.
Shortened Manufacturing Cycle
3D printing technology can generate parts directly from computer graphic data without the need for traditional machining or molds, greatly reducing the product development cycle. This rapid delivery capability is especially suitable for projects requiring quick design validation or tight deadlines, such as new product development or market testing.
Cost Effective
3D printed molds provide notable cost advantages when manufacturing molds with complex geometries. By building molds layer by layer directly through 3D printing, there is no need for additional tools or mold fixtures. This makes it particularly economical for small batch production or customized molds.
Supports Rapid Design Iteration
The flexibility of 3D printed molds makes them an ideal choice for rapid design iterations. During product development, designers may need to modify molds multiple times to optimize part performance.
3D printing allows for quick redesign and printing of new molds without reconfiguring production lines or investing in new tooling. This capability is especially important in industries such as consumer electronics, medical devices, and automotive, where frequent design adjustments are common.
Adapted for Personalized and Small Batch Production
3D printing enables the manufacturing of customized molds tailored to specific needs, meeting the demands of personalized and small batch production. Unlike traditional methods that require large-scale production lines, 3D printing eliminates this step, thereby reducing costs.
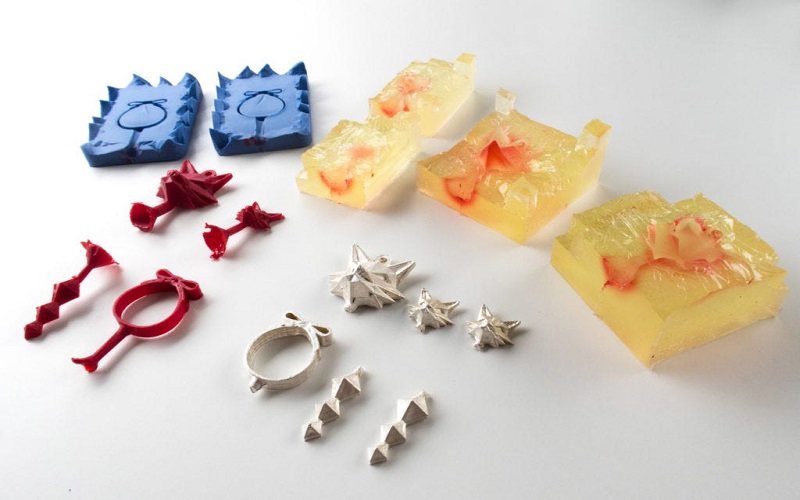
Disadvantages Of 3D Printing Mold
While 3D printed molds offer many advantages, they also come with certain disadvantages that should be considered.
One major limitation is the relatively lower durability compared to traditional metal molds, especially when exposed to high heat or pressure during the molding process. This can lead to wear, deformation, or even breakage after limited use.
Another challenge is the surface finish of 3D printed molds. Depending on the printing technology used, the mold surface may have visible layer lines or rough textures, which can affect the quality and detail of the final molded part. Post-processing steps such as sanding or coating are often required to improve surface smoothness.
Additionally, 3D printed molds may have limitations in producing very fine or complex internal features, as small holes or intricate edges can be difficult to print accurately or may become clogged during casting.
Material choices for 3D printed molds are more limited compared to conventional molds, often restricting the mold’s ability to withstand aggressive chemicals or high temperatures. This can limit the range of casting materials that can be used effectively.
Lastly, while 3D printing reduces tooling costs, the initial investment in high-quality 3D printers and materials can be significant, especially for metal printing technologies. This means that for very large production volumes, traditional mold manufacturing might still be more cost-effective.
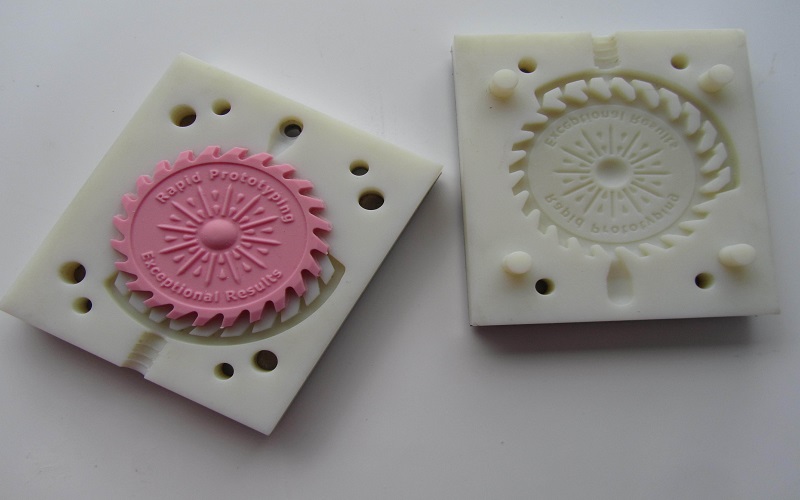
How To Create 3D Printed Mold?
There are two main methods to create 3D printed molds. You’ll either print the mold directly and pour in a softer material, or you’ll print the part and pour a softer material around it to create a silicone mold.
In the first method, the 3D printed mold acts as the actual mold cavity where casting material is poured directly. This approach is often used when the mold material is durable enough to withstand the casting process and the desired number of cycles.
Common materials for direct 3D printed molds include high-strength resins and metal composites, which provide good wear resistance and heat tolerance.
The second method involves printing a master pattern or model, Weigh out the amount of base (Part A if there are two parts) casting silicone you need into a plastic mixing cup.
Add a little bit of pigment (a little goes a LONG way) using the popsicle stick and mix thoroughly.Then used to create a flexible silicone mold by pouring silicone around it.
Once the silicone cures, the 3D printed master is removed, leaving a mold cavity that can be used repeatedly for casting various materials such as resin, rubber, or low-melting-point metals.
This technique is especially useful for producing complex shapes with fine features and undercuts that would be difficult to machine traditionally.
Both methods require careful mold design to ensure proper filling, venting, and easy demolding. Features like air vents and mold release agents are critical to prevent defects and facilitate the removal of the final part.
Additionally, designing molds in two halves or two part molds is common practice to simplify the molding process, allowing for better access to the cavity and reducing the risk of damage to the molded part.
By selecting the appropriate manufacturing method and materials, 3D printed molds can effectively balance cost, speed, and quality, making them suitable for prototyping, small batch production, and customized manufacturing.
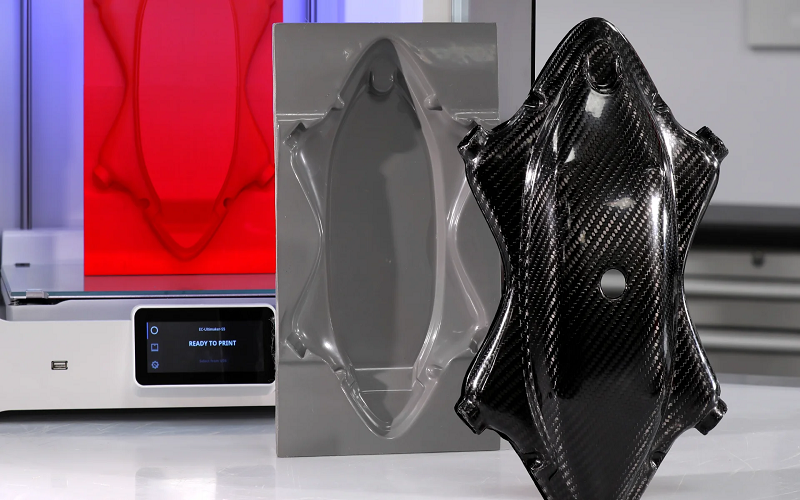
Manufacturing Technologies For 3D Printing Mold
The main manufacturing technologies for 3D printed mold include the following:
Stereolithography (SLA): This method uses photosensitive resin material and builds the model by curing the resin layer by layer with a laser. SLA is suitable for high-precision and small-batch production, especially for molds with complex shapes and rich details.
Fused Deposition Modeling (FDM): This method uses thermoplastic materials, building the model by melting and extruding the material layer by layer. Since we’re using an FDM printer, it can be useful to add a fine layer of vaseline to the inner faces where the two mold halves meet, making sure not to block the air vents.
Selective Laser Sintering (SLS): SLS uses powder materials, building the model by laser sintering the powder. This method is suitable for the manufacturing of complex structures and functional molds, especially for 3D printing with metal and plastic materials.
These technologies can produce part with high dimensional accuracy and are ideal for prints intricate details and very fine features.
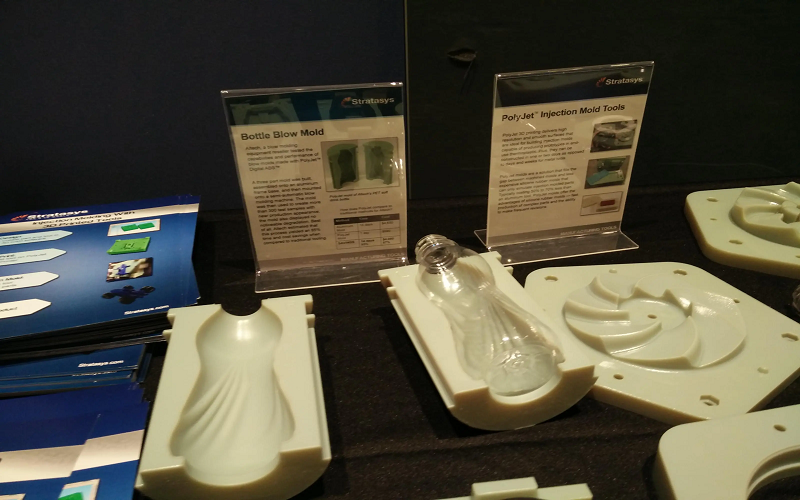
The Process Of Making 3D Printed Moulds
The process of making 3D printed molds involves several key steps to ensure the final mold meets the desired specifications and quality standards.
Mold Design
The first step is to create a detailed 3D model of the mold using CAD software. This design must consider factors such as mold geometry, draft angles, parting lines, air vents, and the placement of mold release agents.
Proper design is crucial to ensure that the mold functions correctly during casting and allows for easy demolding.
Preparing the 3D Model for Printing
After the design is complete, the file is converted into a format compatible with the 3D printer, typically STL. The model is then sliced into layers using specialized software, where printing parameters such as layer height, infill density, and support structures are set.
This step also involves verifying the model for errors and ensuring it is sealed and ready for printing.
Printing the Mold
Using one of the suitable 3D printing technologies such as SLA, FDM, or SLS, the mold is printed layer by layer. Depending on the material and technology, printing times and costs may vary. It is important to monitor the printing process to avoid defects such as warping or incomplete layers.
Post-Processing
Once printed, the mold undergoes post-processing steps which may include cleaning off support materials, curing (for resin-based prints), sanding, and sealing the surface to improve smoothness and durability.
Verification and Testing
Before proceeding to production, the printed mold should be inspected for dimensional accuracy and surface quality. Test casting may be performed to verify that the mold fills properly and releases the final part without defects. Adjustments can be made if necessary by modifying the design and reprinting.
Casting and Use
Finally, the mold is ready for use in the casting process. Depending on the application, materials such as silicone, resin, rubber, or low-melting-point metals can be poured into the mold cavity.
By following these steps carefully, manufacturers can produce 3D printing molds that are cost-effective, precise, and suitable for a wide range of applications, from prototyping to small batch production.
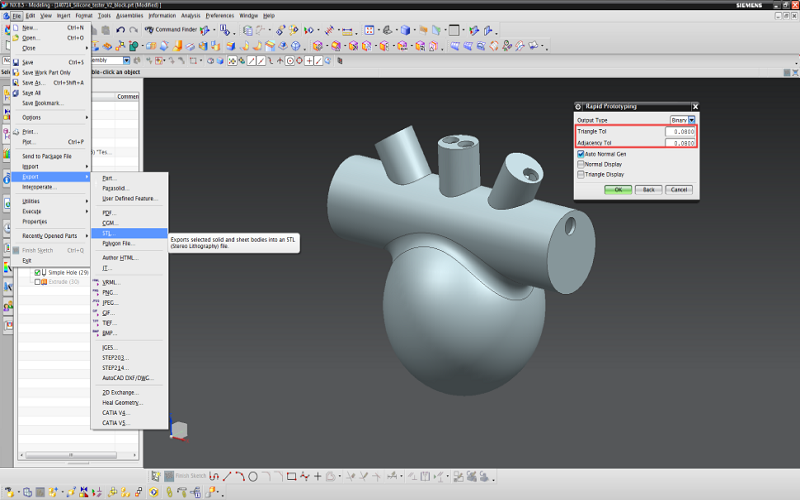
Application Of 3D Printing Mold
3D printed molds have a wide range of applications across various industries due to their versatility and cost-effectiveness. They are commonly used in rapid prototyping, allowing designers to quickly test and validate product designs before committing to expensive traditional tooling.
Automotive
In the automotive industry, 3D printed molds enable the production of customized parts and small batch components, facilitating faster development cycles and reducing lead times.
Aerospace
Similarly, in aerospace, these molds assist in creating lightweight parts with complex geometries that are difficult to achieve with conventional methods.
Medical
The medical field benefits from 3D printed molds by producing patient-specific devices, surgical guides, and implants tailored to individual needs.
Consumer Goods
Additionally, consumer goods manufacturers use 3D printed molds for limited edition products, personalized items, and intricate designs that require fine features and detail.
Education & Research
Furthermore, 3D printed molds are ideal for educational purposes and research, providing an affordable way to experiment with mold design and casting techniques.
Their adaptability also supports artistic and creative industries, where unique shapes and forms can be realized without the constraints of traditional manufacturing.
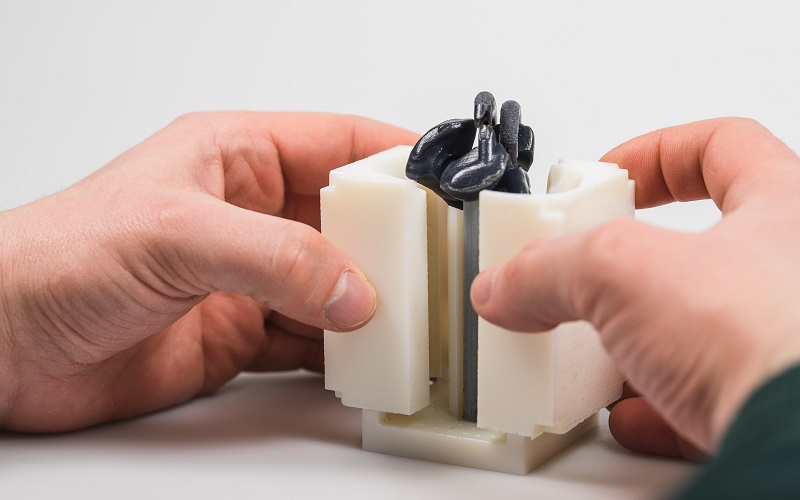
Conclusion
3D printed molds represent a transformative advancement in manufacturing, combining speed, flexibility, and cost-effectiveness to meet the evolving demands of modern production.
They empower designers and manufacturers to quickly respond to market changes, produce individual parts with intricate details, and reduce the overall weight and complexity of molds.
Embracing 3D printed mold technology is not just about adopting a new manufacturing method; it’s about unlocking new creative potential and driving innovation across industries.
Whether for prototyping, small batch production, or customized manufacturing, 3D printed molds offer a cost-effective, efficient, and versatile solution that is shaping the future of mold production.
Start your 3D printed mold journey today and experience the benefits of this cutting-edge technology firsthand.