Vacuum casting is an elastomer casting process in which liquid plastic or metal is injected into a silicone mold under vacuum, thereby producing plastic and rubber components.
Despite its wide range of applications, many people have limited knowledge of this technology and are unsure how to use it effectively.
Therefore, this article will delve into the vacuum casting process, providing a comprehensive technical guide covering the basic principles, equipment selection, process flow, characteristics, and limitations of the process.
What Is Vacuum Casting?
Vacuum casting, also known as urethane casting, is a process where liquid materials are injected into molds in a vacuum environment to cast parts.
Unlike the metal molds used in injection molding, vacuum casting uses soft silicone molds, offering higher production efficiency and cost-effectiveness.
This process ensures that the casts are bubble-free, with smooth and flawless surfaces, making it particularly suitable for small batch production and rapid prototyping in a short timeframe.
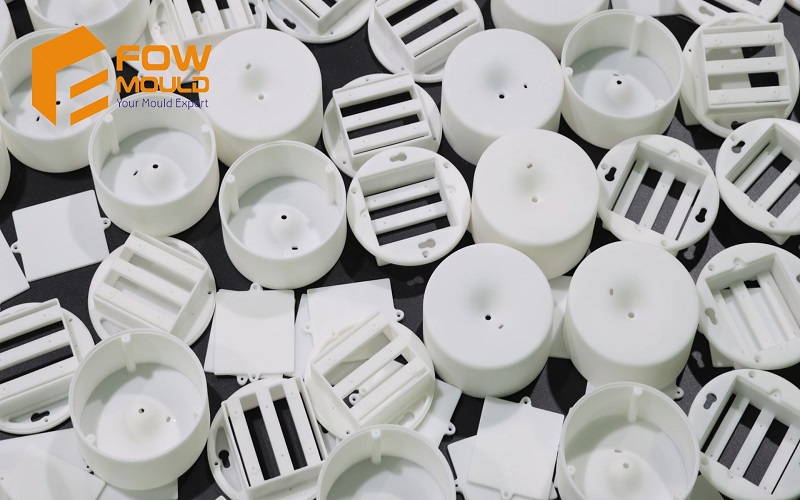
The History Of Vacuum Casting
Vacuum casting technology originated in 1943 with the first silicone resins.
In the 1960s, it was further developed at Dresden and Cottbus technical universities in the former GDR.
Initially used with flexible molds by restorers and sculptors, it gained popularity in Japan’s automotive industry in the 1970s and later in Europe’s R&D departments.
The introduction of thermosetting plastics in the 1980s brought significant advancements.
Modern technologies like CAD and 3D printing have since been integrated, enhancing its use in rapid prototyping and small-scale production.
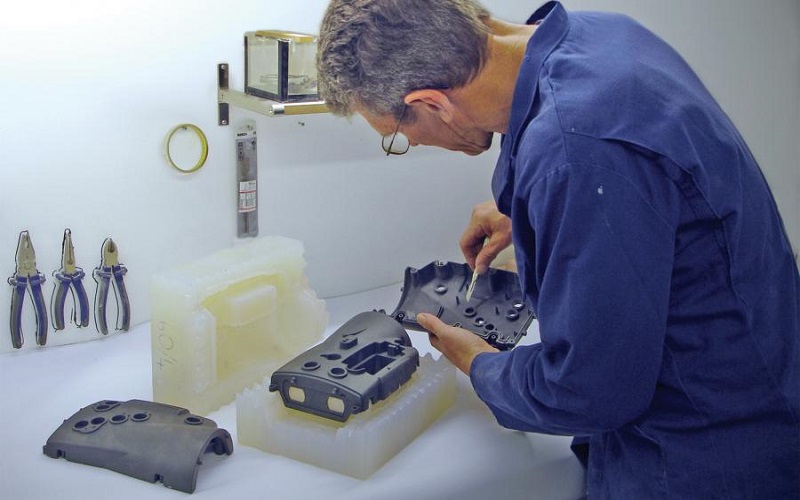
How Does Vacuum Casting Work?
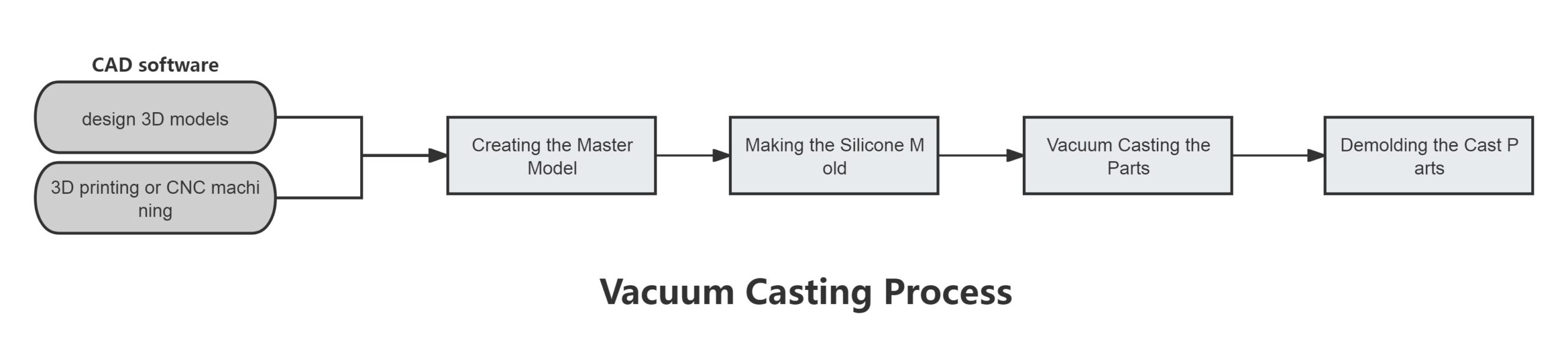
The manufacturing principle of vacuum casting is similar to injection molding, as both use molds to replicate identical parts, but the manufacturing process differs significantly. The main steps are as follows:
Vacuum casting works by creating a mold using a 3D-printed master model and liquid silicone rubber. The process involves placing the mold in a vacuum chamber to eliminate air bubbles, ensuring a higher quality replica. This technique is efficient, allowing for multiple reproductions from a single mold.
Step 1:Master Model Creating
The first step in the vacuum casting process is to create a high-quality master model. This model serves as the basis for the mold, and its accuracy and detail are crucial for producing high-quality parts.
The master model can be created using various methods, including 3D printing, CNC machining, or additive manufacturing. It’s essential to ensure that the master model is designed with the correct wall thickness and geometry to facilitate the vacuum casting process.
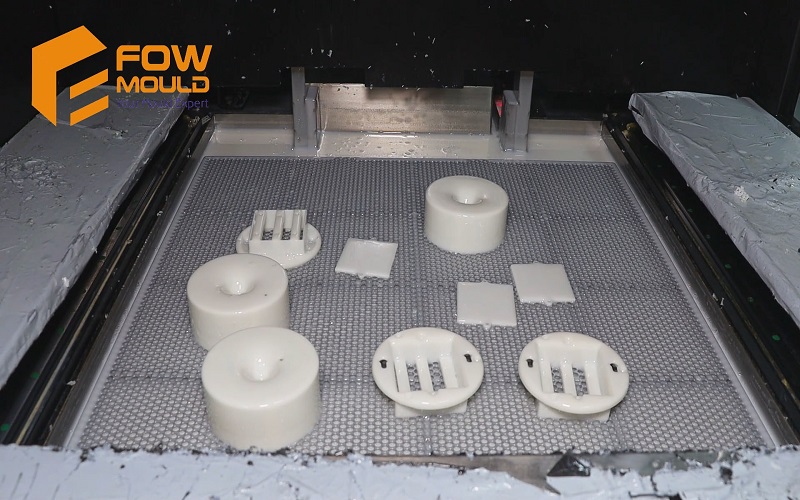
Step 2: Silicone Mold Making
Suspend the master model in a casting box and fix risers to the components to allow air to escape from the silicone mold.
Then, under vacuum conditions, pump liquid silicone into the casting box around the master model.
Allow the silicone to cure in an oven at 40°C for 8-16 hours, depending on the size of the silicone mold.
Once the silicone has cured and dried, carefully cut the mold with a knife to expose the negative mold of the part.
To avoid sticking and surface defects, a mold release agent can be used.
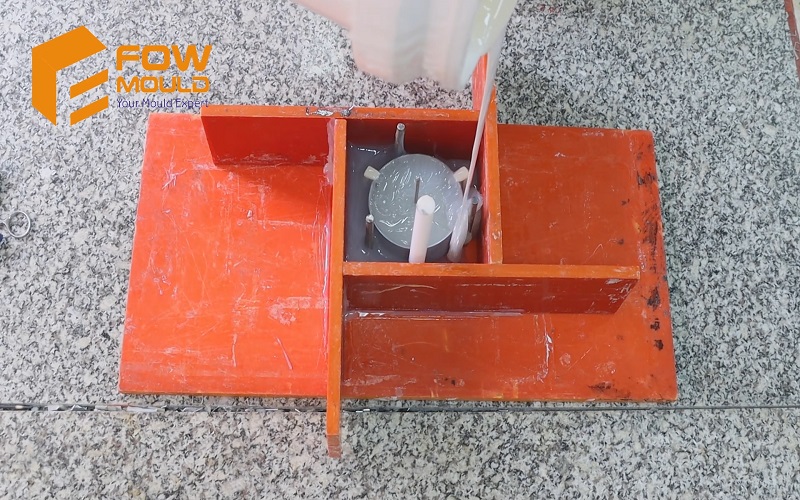
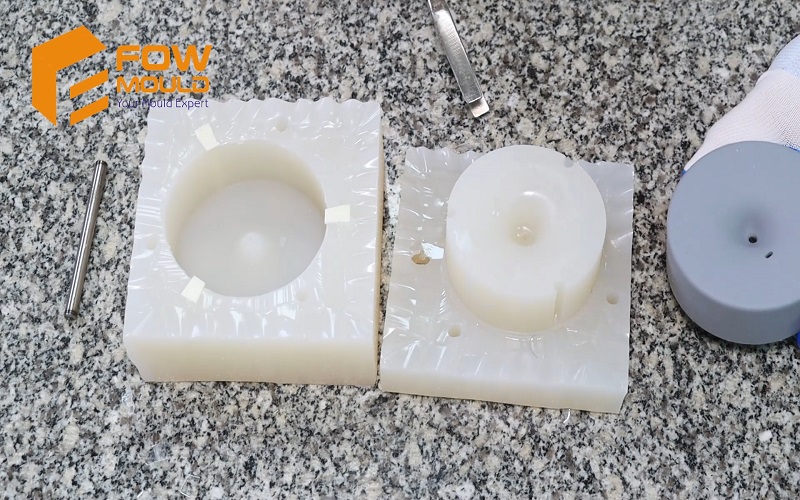
Step 3: Casting the Parts Under Vacuum
Prepare the polyurethane resin by preheating it to approximately 40°C before use.
Mix the two-component resin in the correct ratio, then thoroughly stir and degas it under vacuum for 50-60 seconds.
Pour the resin into the mold inside the vacuum chamber, then cure the mold again in an oven. The average curing time is about one hour.
After curing, remove the cast part from the silicone mold.
This process can typically be repeated 10 to 20 times.
If these limits are exceeded, the mold will gradually lose its shape, affecting dimensional accuracy.
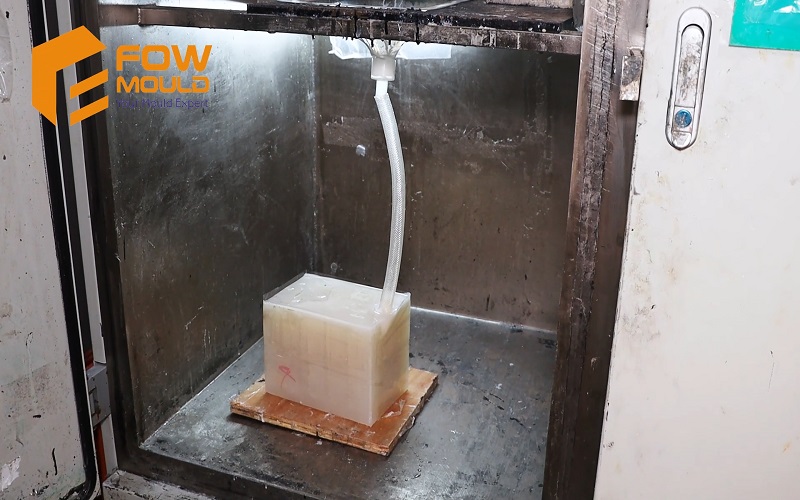
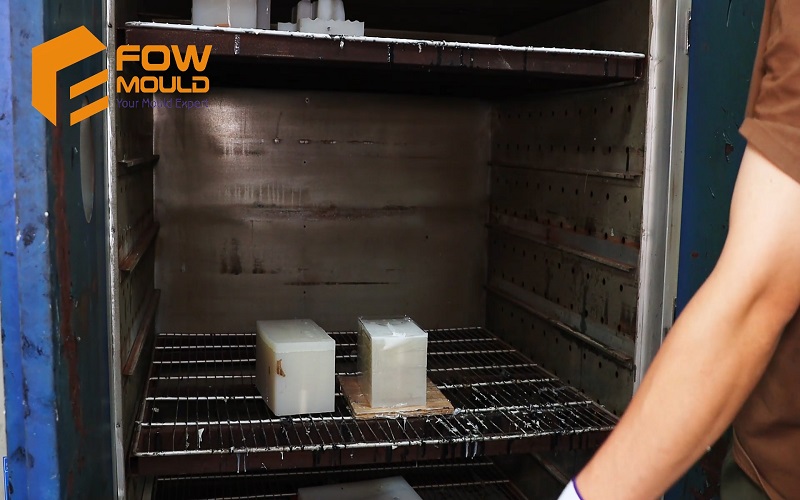
Step 4: Demolding the Cast Parts
Remove the cured product from the silicone mold and trim any excess material and other details.
If the product requires specific colors and surface treatments, spray painting and polishing can be performed.
Finally, conduct a quality check to ensure the product meets design specifications.
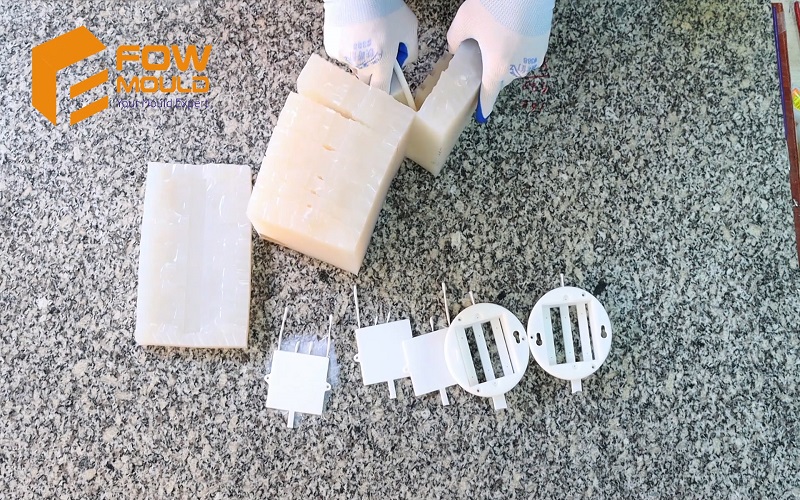
What Materials Are Used For Vacuum Casting?
Many types of materials can be used in vacuum casting, including thermoplastics, rubbers, and resins.
Here are some commonly used materials in vacuum casting and their advantages:
Material Type |
Specific material |
Benefits |
ABS-like general purpose resin |
PU8150,PU8260 |
Smooth surface and dimensional stability |
Polycarbonate-like resins |
PU8098,PX510 |
Ability to withstand impacts and stresses without cracking |
PP-Like Resins |
PU8570,UP5690 |
High Flowability,Low Shrinkage,Flexibility and Toughness |
Glass-filled nylon-like material |
|
Increased stiffness |
PMMA/Acrylic-like |
PX5210HT,UPX5210 |
High transparency,excellent UV resistance |
Rubber Grade Materials |
UPX8400,T0387 |
Design Freedom,Flexibility and Durability |
Additionally, there are some less common polyurethane casting materials, including food-grade, conductive, low-density, and flame-retardant alternatives, as well as materials that mimic broken glass, wax, epoxy resin, ceramics, and composites.
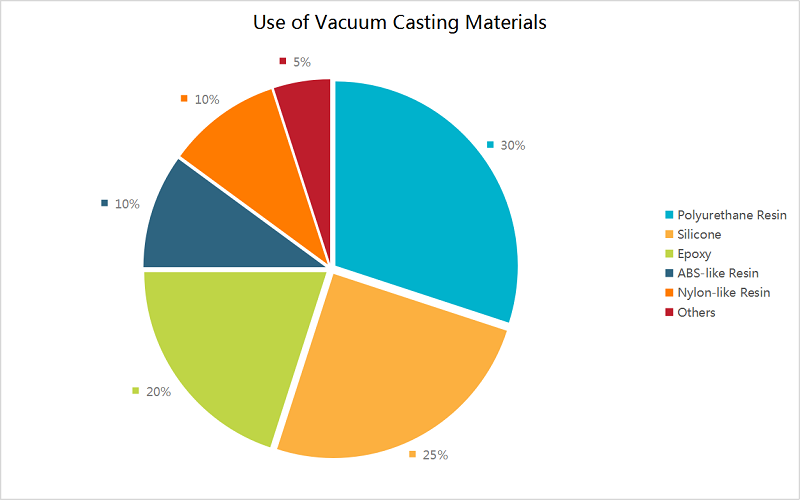
Vacuum Casting Equipment
Advanced machinery is crucial for producing high-quality vacuum cast parts.
The main equipment required for vacuum casting includes:
- 3D Printers
Purpose: Mainly used for creating product prototypes, precisely manufacturing models that meet design specifications.
Brand Manufacturers: Stratasys, 3D Systems, Ultimaker, Formlabs
- CNC Machining Centers
Purpose: Used for precise machining of master models and molds, ensuring high accuracy and surface finish, laying a solid foundation for subsequent casting processes.
Brand Manufacturers: Haas, DMG Mori, Mazak, Tormach
- Vacuum Casting Machines
Purpose: The vacuum casting machine includes a silicone mixer, silicone injector, vacuum chamber, and electrical control module, featuring fast evacuation speed, high vacuum degree, and reliable and convenient operation.
Brand Manufacturers: Renishaw, Proto Labs, Smooth-On, Castaldo
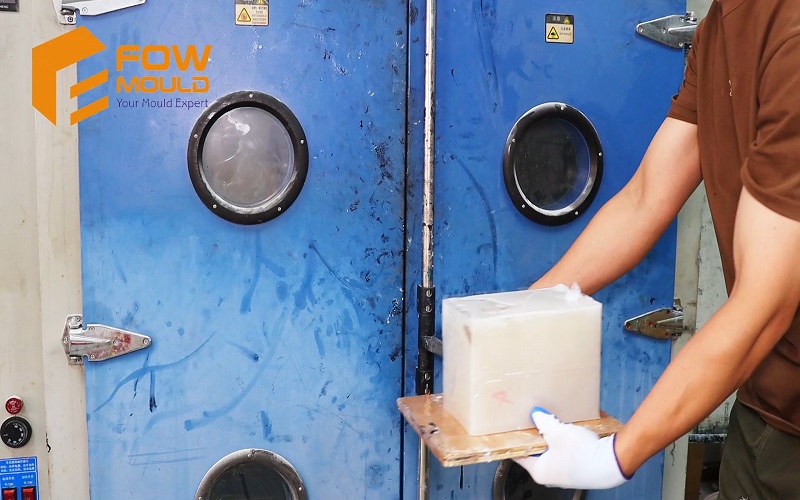
Technical Specifications Of Vacuum Casting Process
The technical specifications of vacuum casting are critical to understanding its capabilities and limitations. Here are some key specifications to consider:
Mold Material: Silicone rubber is the most common material used for vacuum casting molds. It’s flexible, durable, and can be easily removed from the cast part.
Casting Material: A wide range of materials can be used for vacuum casting, including polyurethane, epoxy, and silicone. The choice of material depends on the desired properties of the final part.
Wall Thickness: The minimum wall thickness for vacuum casting is typically 0.5 mm, but it can vary depending on the material and application.
Tolerance: The tolerance for vacuum casting is typically ±0.1 mm, but it can be improved with advanced mold design and manufacturing techniques.
Surface Finish: The surface finish of vacuum cast parts can be smooth and glossy, with a roughness of Ra 0.1 μm.
Color: Vacuum cast parts can be colored using various methods, including painting, dyeing, or adding colorants to the casting material.
By understanding these technical specifications, designers and engineers can optimize their designs for vacuum casting and take advantage of its benefits, including rapid prototyping, low-volume production, and high-quality plastic parts.
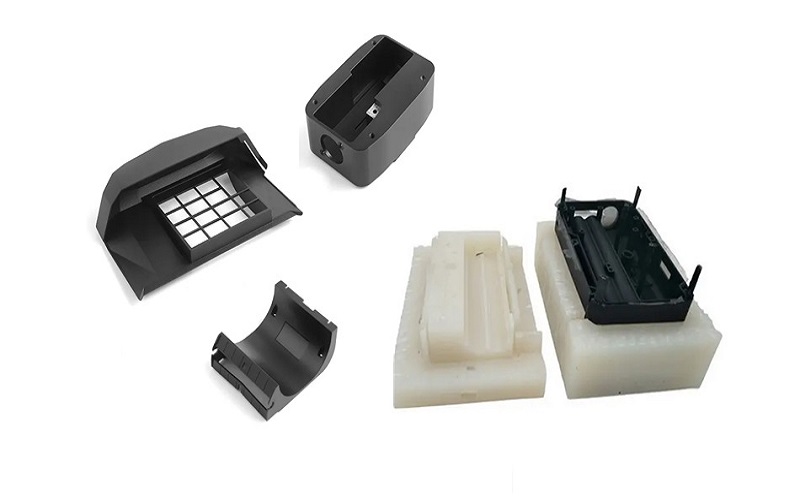
Applications Of Vacuum Casting
Vacuum casting technology allows for the low volume production of engineering plastic parts without the need for steel molds, making it widely used in various industries.
Automotive Industry
In the automotive industry, vacuum casting is used to manufacture high-precision and complex automotive parts such as interior components, dashboards, intake manifolds, and lighting housings.
It enables rapid production, supports functional testing and assembly verification, and accelerates the development of new vehicle models.
Medical Devices
The high precision and rapid prototyping capabilities of vacuum casting align well with the safety and quality standards of the medical industry.
This technology can be used to produce custom prosthetics, medical device prototypes, and dental implants.
Aerospace components
Pre-testing the manufacturability and assemblability of aerospace components is crucial, and vacuum casting technology supports design for assembly and manufacturing.
To achieve the high-precision details required in the aerospace industry, vacuum casting is often used to manufacture fuel systems, air ducts, and certain exterior components of aircraft.
Consumer Goods
Vacuum casting offers high flexibility, allowing for the production of products in various sizes, shapes, and geometries. It is widely used in the consumer goods industry for the small-batch production of everyday items such as electronics, baby toys, household appliances, packaging, and accessories.
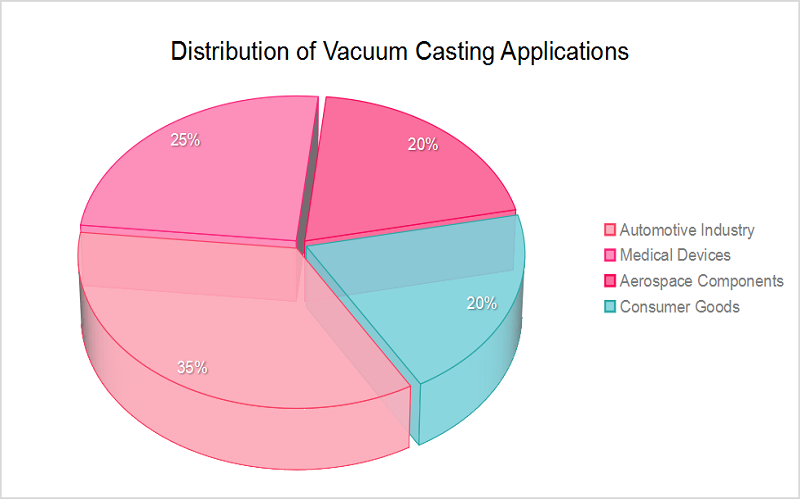
Advantages of Vacuum Casting
- Fast Production Speed
Silicone molds for vacuum casting can be made within a day, and the molds can produce 30-50 parts within 15-20 days.
- Low Production Cost
For the same volume, the price of aluminum molds is more than twice that of liquid silicone.
Using silicone molds for casting polyurethane parts significantly reduces both the cost and time of mold production compared to injection molding.
- Material Versatility
Vacuum casting allows for the use of various materials, including polyurethane resins, which can effectively mimic the properties of different plastics: such as the flexibility of rubber; the high impact strength and flame retardancy of ABS; and the high light transmittance of PMMA.
- Excellent Surface Finish
In small-batch production, silicone-cured molds can accurately replicate surface details, saving time and costs for subsequent treatments.
This also avoids inconsistencies that may occur during individual treatments, improving testability.
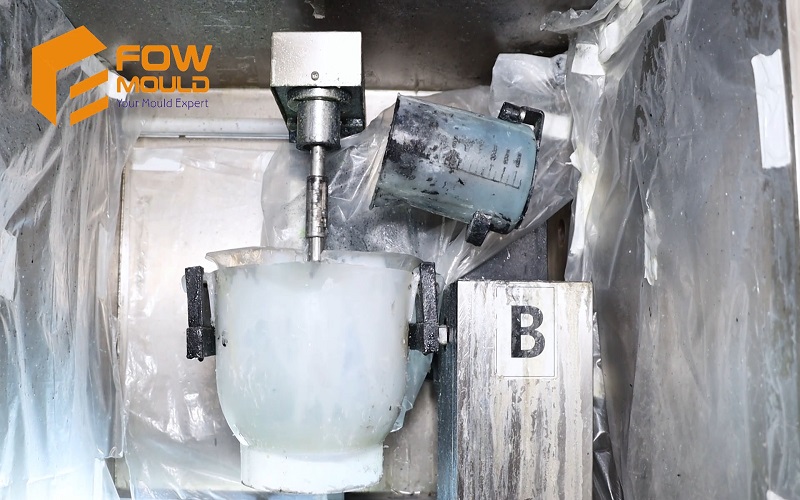
Limitations of Vacuum Casting
- Short Lifespan of Molds
Quickly made silicone molds have a very short lifespan, with each mold capable of producing a maximum of 20-50 parts. Beyond this limit, the silicone mold will gradually deform due to excessive use and become unusable.
- Bubble Issues
Air bubbles are a potential problem in vacuum casting. This occurs because when the mold walls are too thick, the outer parts cure faster than the center, causing insufficient filling in the center and resulting in vacuum bubbles.
- Continuous Defects
Continuous errors are a common issue in all mold production methods. Any defect in the master model or the mold that goes unnoticed will result in defects in the replicated parts, potentially leading to the rejection of an entire batch of parts.
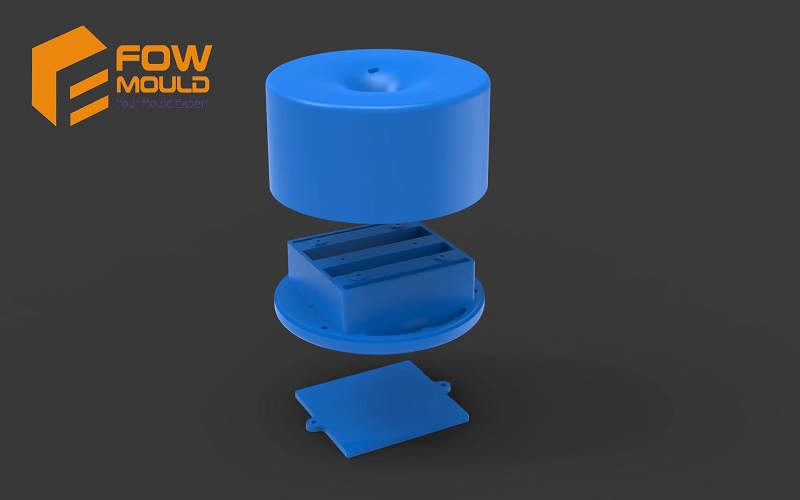
Vacuum Casting vs Injection Molding
Injection molding is a plastic processing method where molten plastic is injected into a closed mold cavity by a plunger or reciprocating screw to form a product.
This method can form complex shapes, precise dimensions, and molded parts with metal or non-metal inserts in one go.
Due to its strong adaptability and high production efficiency, it is commonly used for mass production.
Vacuum casting is similar to injection molding in that it also requires a tool with a cavity that matches the final part shape.
The main difference is that vacuum casting uses “soft” molds made of silicone, while injection molding uses “hard” metal molds machined by CNC.
Although the initial mold-making cost for vacuum casting is lower, silicone molds wear out more quickly, resulting in a shorter lifespan.
However, for producing small batches of prototype plastic parts that require production-grade quality and surface finish, vacuum casting is a more cost-effective solution.
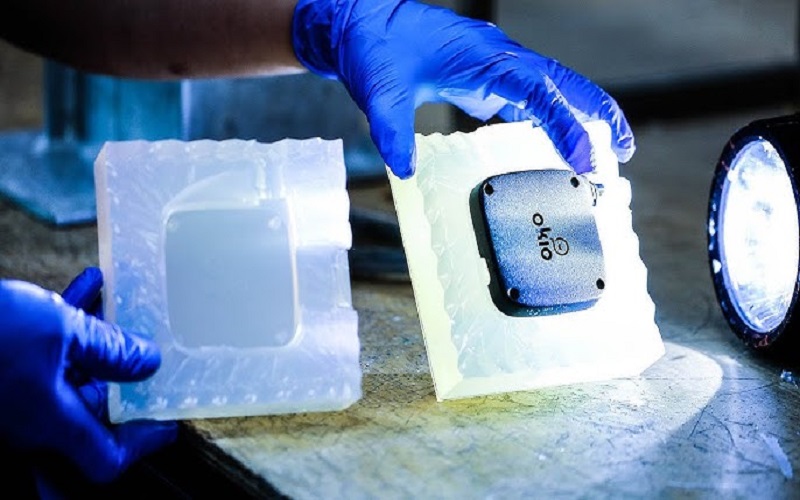
Vacuum Casting vs 3D Printing
Vacuum Casting is a replication process that uses silicone molds to cast liquid materials like polyurethane under a vacuum environment.
This method is typically used when customers have specific material requirements or need small batch production.
It avoids the high costs of mold making while enabling mass production, making it more cost-effective.
3D Printing is an additive manufacturing technology that creates three-dimensional objects by layering materials.
It relies on digital models, converting designs into printing instructions via software, and then the 3D printer constructs the object layer by layer according to these instructions.
Its standout features are speed, flexibility, and high design freedom, though it requires extensive post-processing to achieve a near-finished state.
If considering time and flexibility, 3D printing is an excellent choice.However, if cost and surface finish are priorities, vacuum casting is more suitable.
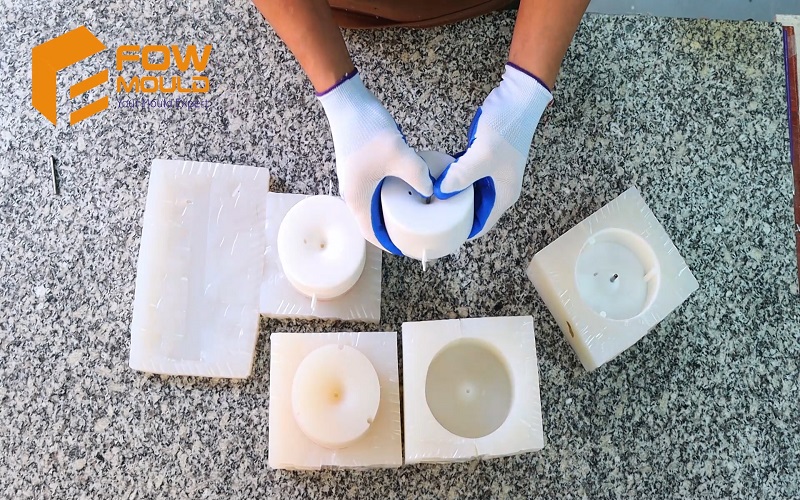
Custom Vacuum Casting Service Of FOWMOULD
Vacuum casting provides an efficient and cost-effective solution for producing high-precision prototype plastic parts in small batches.
If you’re looking to start a new vacuum casting project, FOWMOULD will be your most reliable vacuum casting service provider!
Whether you need complex designs for high-precision prototypes or functional testing of small batch products, we will customize the most cost-effective vacuum casting manufacturing solution to meet your specific needs.
Conclusion
Overall, vacuum casting is an ideal choice for prototype manufacturing and small-batch production due to its characteristics of mold-free production, low processing cost, short production cycle, and high fidelity.
With the development of new materials and advancements in manufacturing technology, vacuum casting will continue to overcome its technical limitations and create broader application prospects.
For more information about vacuum casting, please contact FOWMOULD for a free quote.
FAQ
1.What quantity is suitable for silicone vacuum casting?
Silicone vacuum casting is ideal for quantities ranging from 1 to 100. If the quantity exceeds this range, injection molding would be a more suitable option.
2.What tolerances can I expect for parts produced via silicone vacuum casting?
Parts produced using silicone vacuum casting typically have tolerances within the range of +/- 0.1mm.
3.When is vacuum casting suitable in terms of quantity?
Vacuum casting is suitable for small-scale production, typically in the range of 1-100 units.
For quantities exceeding this range, it is recommended to use injection molding.
4.How many parts can be produced from a single silicone mold?
This depends on the material used, but typically a single mold can produce 20-25 parts. This number may vary depending on the geometry of the parts and the PU material used.
5.I have limited knowledge of plastic processing. How can I ensure my parts can be produced using silicone vacuum casting?
You can send us your 3D drawings. Our team of designers and engineers will analyze your parts and advise you on any necessary adjustments to your 3D design to ensure successful production.