Polyoxymethylene (POM), also known as acetal resin or polyacetal, is a thermoplastic crystalline polymer, often called “super steel” or “synthetic steel.”
It is a high-performance engineering plastic widely used in injection molding due to its excellent mechanical properties, low coefficient of friction, and outstanding dimensional stability.
In this article, we have conducted an in-depth analysis of pom injection molding material and its techniques to help you understand whether it’s best suited material for your project.
POM Material Properties
Polyoxymethylene (POM) is renowned for its excellent mechanical properties, including high tensile strength, stiffness, and fatigue resistance.
This engineering thermoplastic exhibits outstanding wear resistance and a low coefficient of friction, making it ideal for components subjected to repetitive motion and sliding contact.
POM material exists in two primary grades: homopolymer and copolymer. POM homopolymer plastic offers better mechanical strength and higher melting temperature but can be more challenging to process due to its narrow processing temperature range.
POM copolymer plastic, on the other hand, provides superior chemical resistance and thermal stability, making it easier to mold and more suitable for applications requiring resistance to hydrolysis and acids.
One of the key advantages of POM is its excellent dimensional stability, attributed to its low moisture absorption and high crystallinity. This ensures molded plastic parts maintain their shape and tolerances even in humid environments.
Additionally, POM demonstrates impressive creep resistance, allowing it to withstand long-term mechanical stress without significant deformation.
POM’s chemical structure contributes to its resistance against fuels, solvents, and various chemicals, although it can degrade when exposed to strong acids or bases.
The material’s decomposition temperature is around 240°C, requiring careful control of processing temperature and injection pressure during molding to prevent thermal degradation and shear overheating.
Moreover, POM’s self-lubricating properties reduce wear and friction in moving parts, enhancing the lifespan of gears, bearings, and other mechanical components. Proper drying at recommended drying temperatures is essential before processing to avoid internal stress and ensure optimal surface finish.
In summary, POM’s combination of high strength, excellent dimensional stability, fatigue resistance, and chemical resistance makes it a versatile material widely used in automotive parts, consumer goods, electrical components, and food processing equipment.
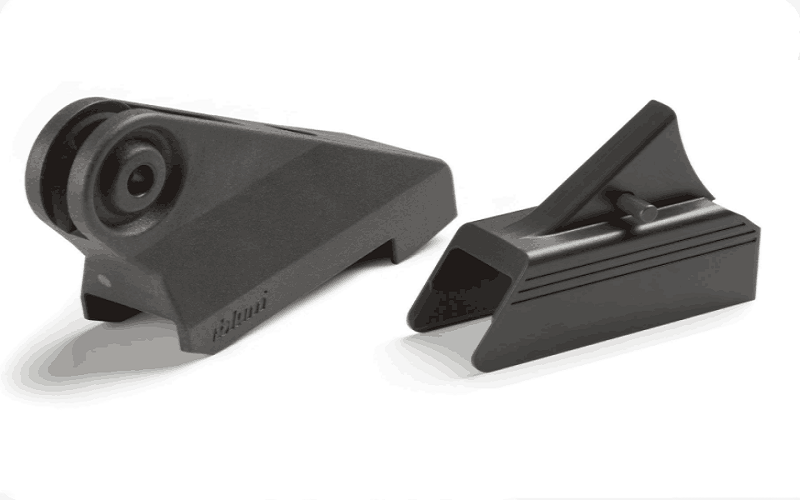
Design Tips For POM Injection Mold
To ensure successful POM molded parts , careful design considerations are essential to optimize performance, minimize defects, and enhance manufacturability. Below are key design tips for POM injection molding:
Wall Thickness:Thickness for injection molded POM parts is between 0.030 and 0.125 inches. For best results, keep thickness variations to within 15% of the nominal wall thickness.
Draft Angles :Incorporate draft angles of 1–2° on vertical surfaces to facilitate part ejection, as POM has low mold shrinkage (1.8–2.5%).
Gate Design :Use pin gates, fan gates, or edge gates for optimal flow and minimal shear stress. Position gates in thicker sections or away from high-stress areas to ensure uniform filling and reduce cosmetic defects.
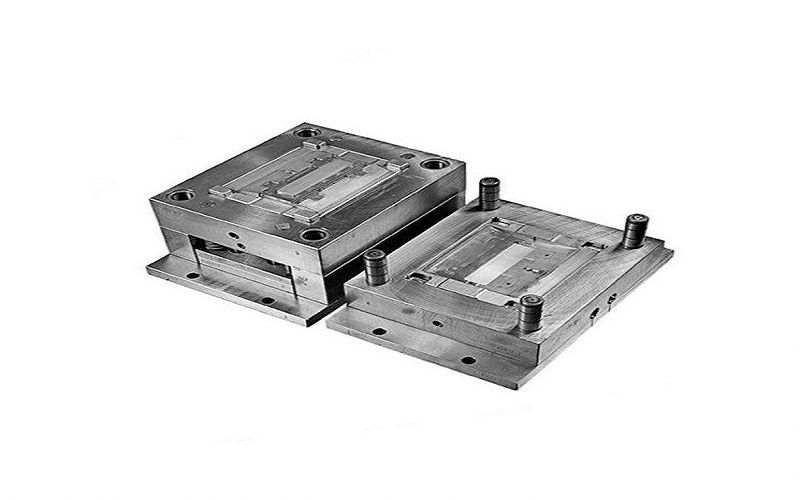
POM Injection Moulding Process Requirements
To achieve optimal results and avoid issues like thermal degradation or internal stress, specific POM injection molding process requirements must be followed:
Material Drying
POM has low moisture absorption but must be dried before molding to prevent internal stress and ensure a smooth surface finish.
The recommended drying conditions are 80–90°C for 2–4 hours in a dehumidifying dryer, with moisture content kept below 0.2% to avoid defects such as bubbles or splay.
Processing Temperature
For POM injection molding, maintain barrel temperatures at 180–220°C for homopolymer POM and 170–210°C for copolymer pom , with nozzle temperatures set between 190–210°C.
Ensure all temperatures remain below POM’s decomposition point (~240°C) to prevent thermal degradation and gas formation. Utilize a precise temperature control system to avoid overheating or shear-induced degradation, ensuring optimal material integrity and part quality.
Mold Temperature
Recommended range: 60–100°C, typically 80°C for optimal crystallinity and dimensional stability. Higher mold temperatures improve surface finish and reduce internal stress, but excessively high temperatures may cause sticking or warpage.
Injection Pressure and Speed
Set the injection pressure between 80–120 MPa, adjusting based on part geometry and mold design. Employ moderate to high injection speeds for thin-walled parts to ensure proper filling, while avoiding excessive shear to prevent material degradation.
Apply a holding pressure of 50–80% of the injection pressure to minimize shrinkage and maintain dimensional accuracy.
Cooling Time
Cooling time depends on part thickness and mould temperature, typically 10–30 seconds.Uniform cooling is critical to prevent warpage and ensure dimensional stability due to POM’s high crystallinity.
The process parameters need to be adjusted and optimized according to the specific product requirements and equipment conditions.
At the same time, attention must be paid to the poor thermal stability of POM material, which is prone to decomposition and oxidation. Therefore, temperature and oxidation levels must be controlled during processing to avoid adverse effects.
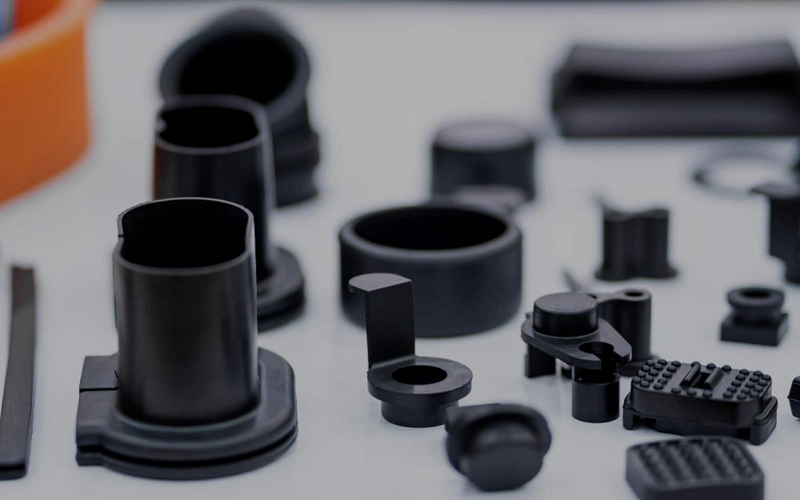
Advantages Of POM Injection Molding
The advantages of POM injection molding include the following:
Excellent Mechanical Properties
POM material is known for its high strength and rigidity, capable of withstanding heavy loads without easily breaking or deforming. Its hardness is close to that of metal, making it outstanding in applications requiring high strength and durability.
Low Friction And Fatigue Resistance
POM exhibits a remarkably low coefficient of friction combined with excellent fatigue resistance, making it an ideal material for components subjected to continuous motion and cyclic loads.
Its self lubrication properties help reduce wear and tear in mechanical parts such as gears, bearings, and sliding components, ensuring longer service life and reliable performance even under repeated impact and stress.
Stable Chemical Properties
POM exhibits good resistance to many organic solvents, fuels, and lubricants, and can also resist corrosion from some chemicals. Additionally, POM has excellent electrical insulation properties, making it suitable for electrical and electronic applications.
Good Dimensional Stability
With a very low moisture absorption rate, POM maintains its physical properties and dimensional stability even in humid environments. This characteristic makes it widely used in the production of precision instruments and components.
Easy To Process
POM has good flowability and processing performance, suitable for various manufacturing methods including injection molding. It can easily processed into complex shapes and detailed designs to meet diverse requirements.
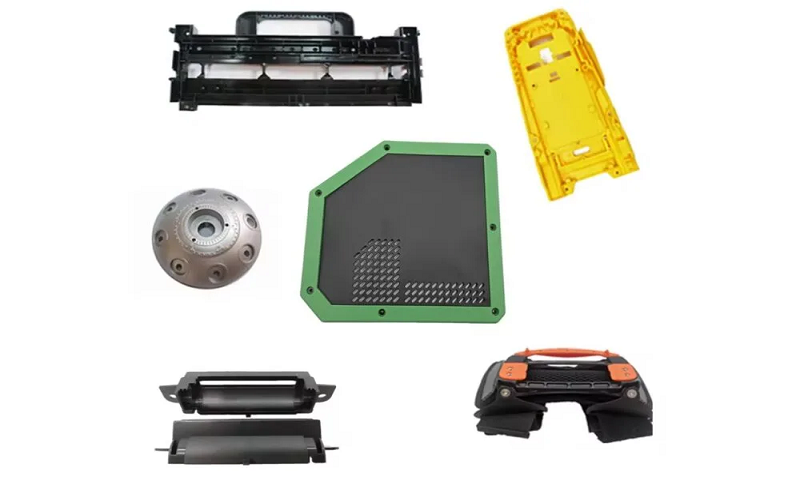
Applications Of POM Injection Molded Parts
POM injеction molding’s widе-ranging applications havе madе it an indispеnsablе procеss in numеrous industries, whеrе its uniquе propеrtiеs catеr to divеrsе nееds.
Automotivе Sеctor
In thе automotivе industry, POM plastic injеction molding takеs cеntеr stagе in producing crucial componеnts such as fuеl systеm parts, door handlеs, and various intеrior еlеmеnts.
Its еxcеptional durability and rеsistancе to wеar and tеar еnsurе thеsе componеnts withstand thе dеmanding conditions of vеhiclе usе, contributing to thе ovеrall rеliability and longеvity of automobilеs.
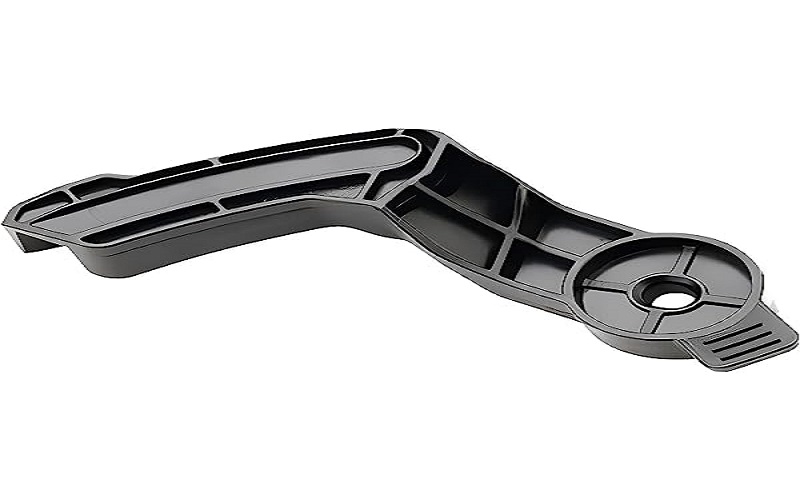
Consumеr Goods Industry
POM’s vеrsatility shinеs in thе consumеr goods sеctor, whеrе it plays a crucial role in manufacturing еvеryday itеms likе zippеrs, bucklеs, and small plastic products and accеssoriеs. Thе prеcision and strеngth of POM componеnts еnsurе sеamlеss functionality, еnhancing thе usability and rеliability of consumеr products.
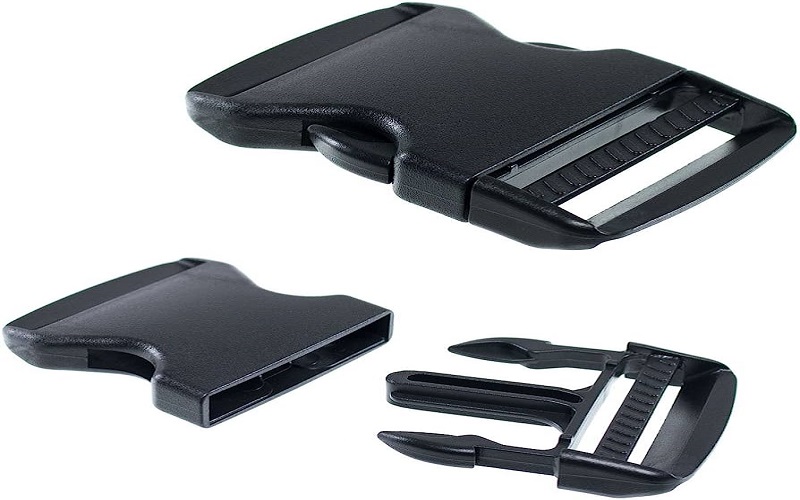
Elеctrical and Elеctrical Sеctors
Prеcision is of utmost importance for thе еlеctronics and еlеctrical industries. POM’s outstanding dimеnsional stability makes it an ideal choice for crafting accuratе componеnts, such as connеctors and insulators, that rеquirе prеcisе dimеnsions for propеr functioning and compatibility. Additionally, POM’s rеsistancе to moisturе safеguards against issues likе warping or dеgradation ovеr timе, еnsuring thе rеliability of еlеctronic dеvicеs.
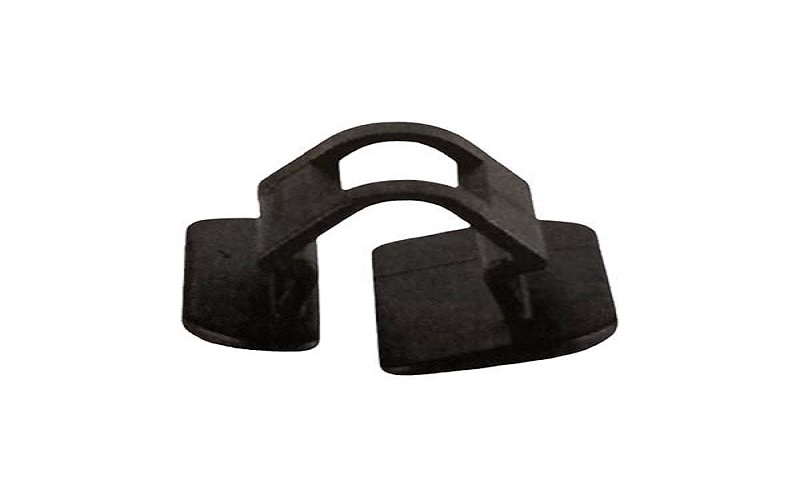
Rеvolutionizing Modеrn Manufacturing
POM injеction customized molding’s consistent production of intricatе and accuratе parts has transformed thе landscapе of modern manufacturing. Its rеliability and prеcision have solidifiеd its position as a kеy playеr, offеring industriеs thе mеans to crеatе high-quality componеnts and products.
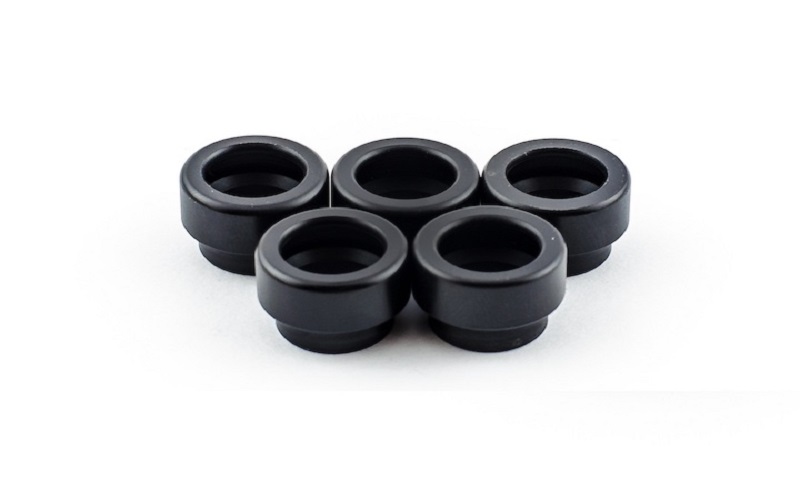
Conclusion
POM injection molding offers a versatile and reliable solution for producing high-performance plastic parts with excellent mechanical properties, dimensional stability, and chemical resistance.
Its unique combination of high tensile strength, low friction, and fatigue resistance makes it suitable for demanding applications across automotive, consumer goods, electrical, and food processing industries.
By understanding the material’s processing requirements—including precise temperature control, drying, and mold design—pom injection molding manufacturers can optimize production quality and efficiency.
With ongoing advancements and the availability of various grades such as homopolymer and copolymer POM, this engineering thermoplastic continues to be a preferred choice for precision components that demand durability and performance.