Polyethylene is a thermoplastic plastic made from ethylene monomers through a polymerization reaction, and it is one of the most widely used plastic materials globally. Polyethylene is a widely used consumer plastic due to its versatility and durability.
Despite its simple molecular structure, it boasts excellent performance, including good chemical stability, flexibility, impact resistance, and electrical insulation. As a result, it is widely used in various fields such as frozen food bags, bottles, cereal liners, yogurt containers, etc.
As a lightweight, cost-effective, and easy-to-process material, polyethylene plays an indispensable role in modern industry and daily life. This article will delve into the properties, types, and diverse applications of polyethylene, helping readers gain a deeper understanding of this material.
What Is Polyethylene?
Polyethylene (PE) is a thermoplastic resin obtained through the polymerization of ethylene molecules. In industrial applications, it also includes copolymers of ethylene with a small amount of alpha-olefins. Ethylene, the building block of polyethylene, is derived from both crude oil and natural gas.
It was first synthesized in 1922 by the British company ICI. The current polyethylene process uses metallocene catalysts or non-metallocene catalysts to produce polyethylene products with a narrow molecular weight distribution.
Polyethylene is odorless, non-toxic, and feels similar to wax. It has excellent low-temperature resistance, with a minimum operating temperature reaching -100 to -70°C.
PE exhibits good chemical stability because the polymer chains are linked by carbon-carbon single bonds, allowing it to resist most acids and alkalis (though it is not resistant to oxidizing acids).
With the development of the petrochemical industry, polyethylene production has rapidly expanded, accounting for about one-quarter of the total plastic production.
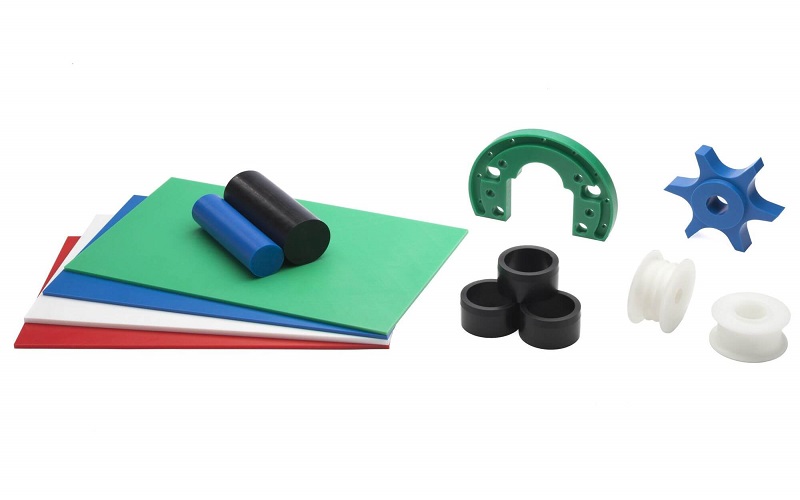
Chemical Composition Of Polyethylene
Polyethylene is a thermoplastic polymer with a simple yet versatile chemical structure. It is primarily composed of long-chain polymer compounds formed through the polymerization of ethylene monomers (CH₂=CH₂).
The ethylene molecule, with its double bond, plays a crucial role in this process, breaking during polymerization to form long polymer chains.
Each ethylene monomer consists of two carbon atoms and four hydrogen atoms, linked by a double bond that breaks during polymerization to form a repeating -CH₂-CH₂- unit in the polymer chain.
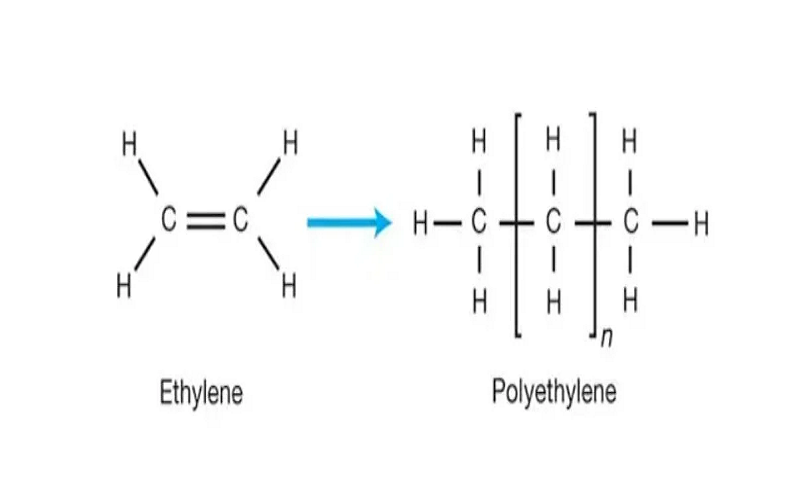
Types of Polyethylene
Depending on the polymerization method, molecular weight, and PE chain structure, it can be categorized three types of polyethylene :High Density Polyethylene (HDPE), Low Density Polyethylene (LDPE), Linear Low Density Polyethylene (LLDPE), and Ultrahigh Molecular Weight Polyethylene (UHMWPE).
A basic distinction can be made between different crosslinking methods used in polyethylene, such as peroxide, silane, electron beam, and azo crosslinking techniques.
High Density Polyethylene (HDPE)
HDPE is produced using a low-pressure process, typically in the presence of Ziegler-Natta catalysts or metallocene catalysts. The reaction occurs in a slurry or gas-phase reactor, where ethylene molecules polymerize into long chains with high molecular weight and a low degree of branching.
This results in HDPE having a high density, high stiffness, and high abrasion resistance. These properties make HDPE used in products and packaging such as milk jugs, detergent bottles, butter tubs, garbage containers, and water pipes .
Low Density Polyethylene (LDPE)
LDPE is manufactured using a high-pressure process, often involving a free-radical initiator. The reaction takes place in a tubular or autoclave reactor, where ethylene molecules form polymer chains with a low molecular weight and a high degree of branching.
This results in LDPE having a low density, low stiffness, and high impact resistance. Its density is about 0.920 g/cm3, melting point 108℃~126℃.
LDPE is widely used for applications such as packaging film, frozen food bags, and other LDPE injection molding products that benefit from its flexibility and resilience.
Linear Low Density Polyethylene(LLDPE)
Linear low-density polyethylene is a ethylene copolymers and small amounts of higher α-olefins (such as butene-1, hexene-1, octene-1, or tetramethylpentene-1), synthesized via high- or low-pressure polymerization. Its density ranges from 0.915 to 0.940 g/cm³.
The structure of LLDPE has a linear backbone with short and uniform branches (unlike longer branches of LDPE).
Compared to LDPE, LLDPE offers superior environmental stress cracking resistance, electrical insulation, heat resistance, impact resistance, and puncture resistance. It is primarily used in agricultural films, packaging films, wire and cable insulation, pipes, and coated products.
Ultra-high Molecular Weight Polyethylene (UWMPE)
Ultra-high molecular weight polyethylene refers to polyethylene with a molecular weight exceeding 1 million. Gel spinning is a method used to produce UHMWPE, where a heated gel of UHMWPE is extruded through a spinneret and cooled in a water bath, resulting in fibers with exceptional tensile strength.
It is employed in high-end applications such as plastic modification, pipes, high-strength plates, and fibers due to its exceptional properties.
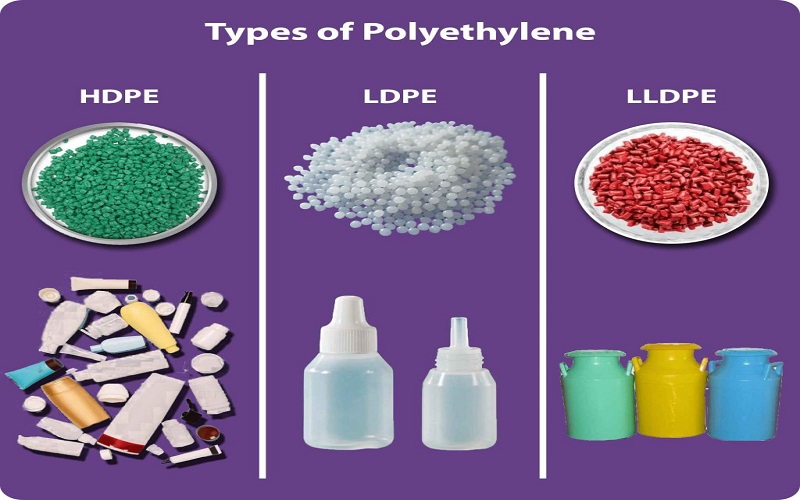
Properties Of Polyethylene Material
Polyethylene resin is a non-toxic, odorless white powder or granule with a milky white appearance and a waxy texture.
Polyethylene burns slowly with a blue flame having a yellow tip and gives off an odour of paraffin (similar to candle flame).
Polyethylene exhibits good water resistance. The surface of the products is non-polar, making it difficult to bond and print on, but this can be improved with surface treatment.
The surface properties of polyethylene, influenced by its molecular structure and crystallinity, require pretreatment for effective bonding and printing. It has a low water absorption rate, less than 0.01%.
Mechanical Properties
Polyethylene generally has moderate mechanical properties, with relatively low tensile strength and poor creep resistance but excellent impact resistance. Ultra-high molecular weight polyethylene (UHMWPE) possesses a low coefficient of friction, making it ideal for applications requiring durability and resistance to wear. Its resistance to environmental stress cracking is limited, though it improves with higher molecular weight.
Impact Strength: LDPE > LLDPE > HDPE
Thermal Properties
Polyethylene has limited heat resistance, with LDPE suitable for use at approximately 80°C and HDPE capable of withstanding long-term use up to 121°C. High temperatures and high pressures are crucial in the manufacturing processes of polyethylene, where gaseous ethylene is polymerized under these conditions, significantly affecting its properties and applications.
Its low-temperature performance is exceptional, with a brittle temperature typically below -50°C, and as low as -140°C for higher molecular weight variants.
Polyethylene has a high linear expansion coefficient, ranging from (20–24) × 10⁻⁵/K, and relatively high thermal conductivity.
Electrical Properties
Due to its non-polar nature, polyethylene boasts excellent electrical properties, including low dielectric loss and high dielectric strength. It is suitable for applications such as frequency-modulated insulation materials, corona-resistant plastics, and high-voltage insulation.
Chemical Properties
As an inert alkane polymer, polyethylene exhibits excellent resistance to acids, bases and vegetable oils but is vulnerable to strong oxidants such as fuming sulfuric acid, concentrated nitric acid, and chromic acid.
Below 60°C, polyethylene is insoluble in most solvents, but prolonged exposure to aliphatic hydrocarbons, aromatic hydrocarbons, or halogenated hydrocarbons may cause swelling or cracking.
Environmental Properties
Polyethylene is weather resistant but can become brittle when exposed to sunlight for extended periods of time.Incorporating antioxidants and light stabilizers is necessary to enhance its durability.
Processing Properties
LDPE and HDPE exhibit excellent flowability, low processing temperatures, moderate viscosity, and high decomposition temperatures (stable up to 300°C in inert gases), making them highly processable plastics.
Polyethylene pellets are utilized in various manufacturing processes, where they are melted and molded into different final forms. The molecular weights of polyethylene, especially in ultrahigh-molecular-weight variants, significantly affect the material’s properties and applications.
However, LLDPE has slightly higher viscosity, requiring 20–30% more motor power during processing. It is prone to melt fracture, necessitating larger die gaps and processing aids.
LLDPE also requires higher processing temperatures, typically 200–215°C. Polyethylene’s low water absorption eliminates the need for pre-drying before processing.
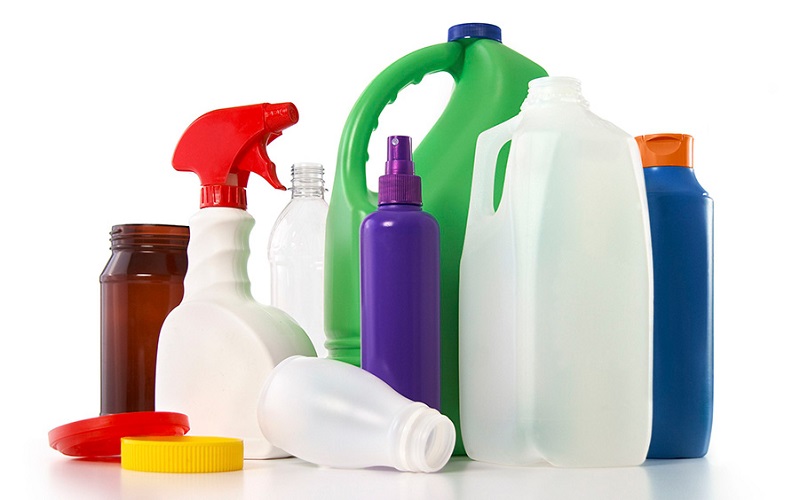
Process Methods Of Polyethylene Plastic
Polyethylene can be manufactured using a variety of processing methods. Using ethylene as the primary raw material, along with comonomers such as propylene, 1-butene, and hexene, and under the influence of catalysts, slurry polymerization or gas-phase polymerization processes are employed.
The resulting polymers undergo processes such as flash evaporation, separation, drying, and granulation to produce uniformly granulated finished products. These production methods include sheet extrusion, film extrusion, pipe or profile extrusion, blow molding, injection molding, and rotational molding.
Injection Molding
Polyethylene exhibits excellent flowability, allowing it to fill mold cavities smoothly during the injection molding process. Molten polyethylene is injected into a mold cavity under high pressure, cooled, and solidified to form precise, complex parts.
HDPE injection molding typically results in products with high strength and dimensional stability, making them suitable for solid form or thin walled injection molding products requiring high precision and complex structures, such as turnover boxes and containers, plastic bottle caps, and barrels.
Blow Molding
PE blow molded products range from bottles that hold bleach, motor oil, detergents, milk, and distilled water to large refrigerator components, automotive fuel tanks, and drums.
Injection-blow molding is commonly used to manufacture smaller containers (less than 16 oz) for packaging pharmaceuticals, shampoos, and cosmetics.
One advantage of this processing method is the automatic removal of excess material, eliminating the need for post-production trimming steps typical in conventional blow molding processes.
Sheet Extrusion
In the sheet extrusion process, molten polyethylene is extruded through a flat die to form continuous sheets. This method is suitable for applications such as packaging, liners, and construction panels.
HDPE is typically used for rigid sheets, while LDPE is suitable for flexible sheets. Sheet extrusion offers the advantage of producing uniform, flat products that are ideal for further processing, such as thermoforming.
Film Extrusion (Film Blowing)
In the film extrusion (film blowing) process, molten polyethylene is extruded through a circular die, inflated into a bubble, cooled, and rolled into thin films.
This method is widely used for producing packaging films, agricultural films, and plastic bags. LDPE and LLDPE are suitable for this process due to their flexibility and clarity.
The advantages of this method include the ability to produce thin, durable films with excellent tensile properties. However, precise control of bubble stability and the cooling process is essential to ensure product quality.
Pipe or Profile Extrusion
In the pipe or profile extrusion process, molten polyethylene is forced through a die to form continuous pipes or complex profiles.
This method is primarily used to produce water pipes, gas pipes, cable conduits, and structural profiles. HDPE is preferred for its rigidity and durability, while LLDPE is suitable for flexible tubing.
The advantages of this method include the production of strong, seamless products with consistent cross-sections.
What Is Polyethylene Plastic Used For?
As one of the most widely used consumer plastics globally, polyethylene is employed in various applications ranging from everyday consumer goods to high-end industrial products due to its excellent properties.
Chlorinated polyethylene is a versatile and cost-effective material used in enhancing the impact and weather resistance of PVC blends, softening PVC foils, and its potential for crosslinking to create elastomers used in the cable and rubber industry. The following are the main application areas of polyethylene:
Packaging Material
Film applications :Film applications: Most PE is used for film, with LDPE or LLDPE materials being the preferred choice. HDPE film grades are generally used in applications requiring superior tensile strength and higher barrier properties. For example, HDPE films are commonly used for merchandise bags, grocery bags, and food packaging.
Food packaging:HDPE is used in several packaging applications including crates, trays, bottles for milk and fruit juices, caps for food packaging, jerry cans, drums, industrial bulk containers etc.
Pipes and Profiles
Water and Gas Pipes: HDPE is an ideal material for water and gas pipelines due to its high strength, corrosion resistance, and durability. It is widely used in municipal and industrial piping systems.
Cable Conduits: HDPE and LLDPE are used to produce cable protection pipes, offering excellent electrical insulation and mechanical protection.
Agricultural Applications
Agricultural Films: LDPE and LLDPE are used to manufacture greenhouse films, mulch films, and cover films, helping to increase crop yields, protect soil, and conserve water resources.
Fishing Nets and Ropes: HDPE is used to produce fishing nets, ropes, and agricultural tying tapes due to its high strength and weather resistance.
Consumer Goods
Household Products: HDPE and LDPE are used to make plastic containers, bottle caps, toys, garbage bins, and storage boxes through injection and blow molding.
Shopping Bags and Garbage Bags: LDPE is commonly used for producing disposable plastic bags due to its flexibility and cost-effectiveness.
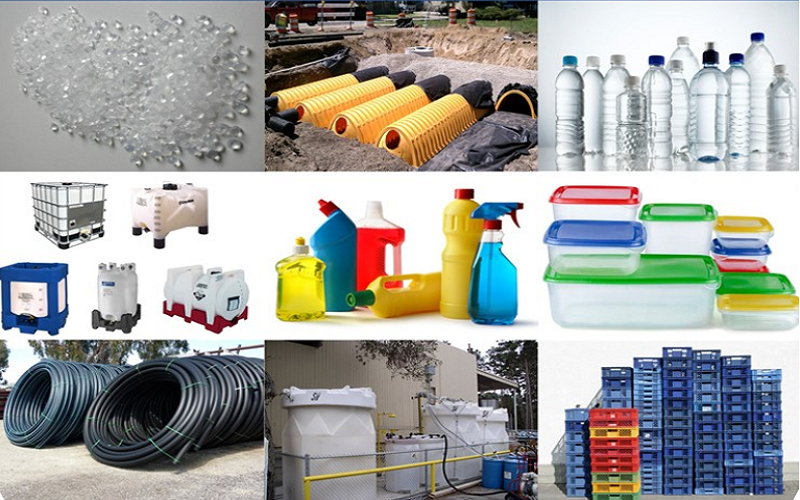
Is Polyethylene Safe?
The safety of polyethylene depends on its manufacturing process, usage environment, and application. Polymerized from ethylene monomers (CH₂=CH₂), PE contains only carbon and hydrogen, making it non-toxic, odorless, and chemically stable.
Its low water absorption rate (<0.01%) ensures no harmful substance release under normal conditions (e.g., refrigeration or room temperature), ideal for food packaging.
LDPE, with lower heat resistance (~80°C), is unsuitable for high-temperature cooking or microwaving unless labeled microwave-safe. HDPE withstands temperatures up to 121°C but should avoid prolonged high heat to prevent additive migration or degradation during the molding process or use.
PE is safe but poses risks if burned, releasing carbon monoxide (CO) and carbon dioxide (CO₂), which can cause suffocation in enclosed spaces. Waste incineration should occur in professional facilities.
Trace double bonds or ether linkages in PE’s structure may lead to aging under sunlight or rain, releasing minor degradation products. Adding antioxidants and light stabilizers during the manufacturing process mitigates this.
Typically, this material will only burn if flame or extreme temperatures are applied, so it is considered safe for its recommended applications.
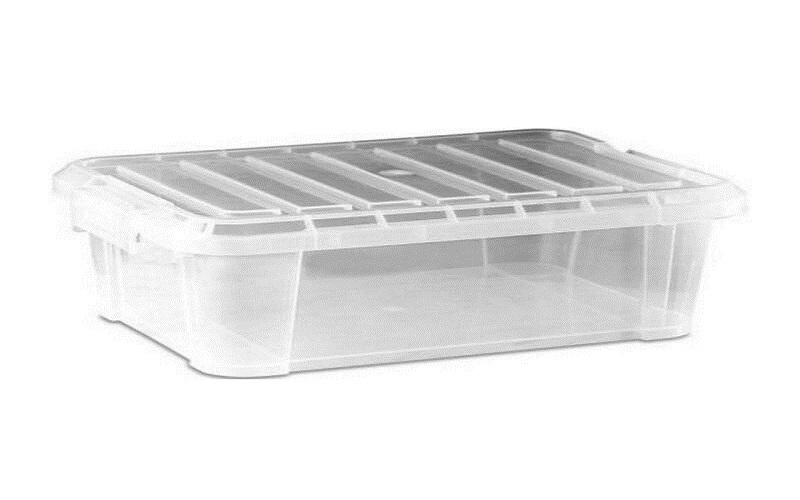
Advantage Of Polyethylene
Below are the key advantages of polyethylene, emphasizing its value in commercial production:
Diverse Mechanical Properties
Polyethylene is a durable material, which does not easily wear or weaken.LDPE and LLDPE are soft and highly extensible, ideal for films and flexible tubing.
HDPE provides high stiffness suitable for pipes and containers requiring structural strength.
UHMWPE, with its ultra-high molecular weight, offers exceptional high abrasion resistance, used in wear-resistant liners, artificial joints, and ballistic materials.
Excellent Processing Performance
PE offers good flowability, low processing temperatures (160–200°C), moderate viscosity, and high decomposition temperature (up to 300°C in inert gases), supporting injection molding, blow molding, extrusion, and rotational molding for efficient commercial production.
Superior Electrical Insulation
Non-polar PE has low dielectric loss and high dielectric strength, making it ideal for cable insulation and high-voltage materials in wires and cables.
Cost-Effectiveness
Abundant raw materials and low production costs, combined with mature processing techniques, make PE ideal for large-scale production.
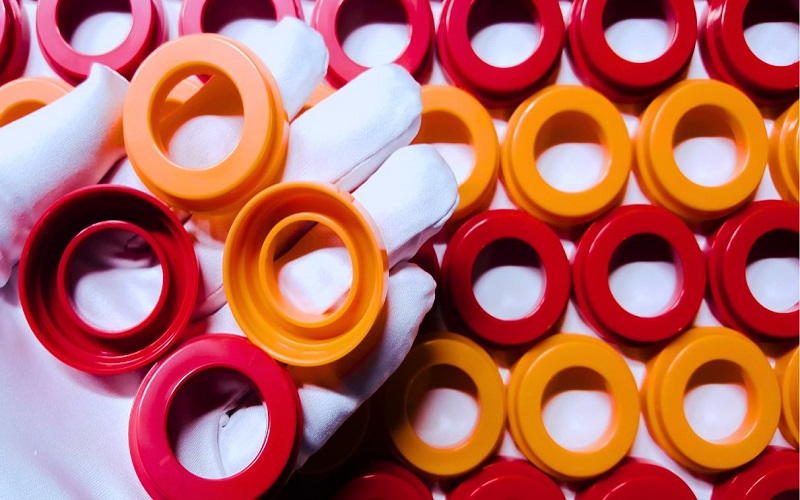
Disadvantages of Polyethylene
While polyethylene is a highly versatile and widely used plastic, it has certain limitations that can impact its suitability for specific applications. Below are the key disadvantages of polyethylene:
Limited Heat Resistance
Polyethylene has relatively low heat resistance. LDPE is limited to approximately 80°C, while HDPE can withstand long-term use up to 121°C.
This makes PE unsuitable for high-temperature applications, such as microwave cooking (unless specifically labeled) or industrial processes involving elevated temperatures.
Flammability and Combustion Risks
Polyethylene is flammable and, when burned, releases carbon monoxide (CO) and carbon dioxide (CO₂), posing suffocation risks in enclosed environments. Improper incineration of PE waste can also release toxic fumes, requiring professional disposal facilities.
Poor Barrier Properties
Polyethylene, especially LDPE, has low resistance to gas and moisture permeation, making it less effective as a barrier material compared to other materials like PET or EVOH. This limits its use in applications requiring high barrier properties, such as packaging for oxygen-sensitive products.
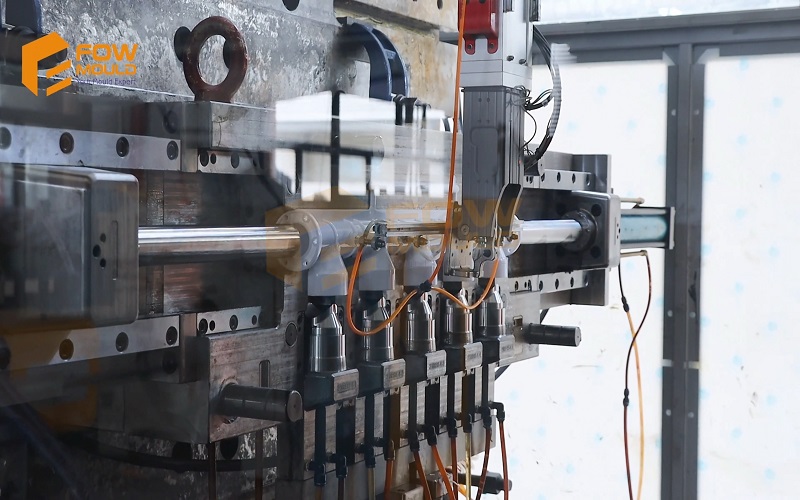
Conclusion
Overall, polyethylene is a versatile material with a range of useful variants, each offering unique properties and applications.
From HDPE known for its strength and durability, to LDPE valued for its flexibility, and UHMWPE with its exceptional abrasion resistance, PE grades cater to diverse industrial and consumer needs.
Its adaptability in manufacturing processes, coupled with cost-effectiveness, makes polyethylene a cornerstone in plastic production.
However, considerations regarding its heat resistance and environmental impact are essential for its optimal use.