In modern logistics and supply chain systems, plastic pallets have become indispensable core tools ideal for export, pharmaceutical, medical, and food applications due to their lightweight, durability, and high adaptability.
Compared with traditional wooden and metal pallets, plastic pallets demonstrate significant advantages in moisture resistance, corrosion resistance, hygiene, safety, and recyclability, and are widely used in industries such as food, pharmaceutical industry, and e-commerce.
This article will provide an in-depth analysis of the core technologies, manufacturing processes, and future trends in plastic pallet manufacturing, offering technical insights to industry practitioners and assisting enterprises in seizing opportunities and achieving breakthroughs in a highly competitive market.
What Materials Can Be Used To Manufacture Plastic Pallets?
High Density Polyethylene (HDPE)
HDPE (High-Density Polyethylene) is a thermoplastic polyolefin produced by copolymerizing ethylene. It is a highly crystalline, non-polar thermoplastic resin. In its natural form, HDPE appears milky white and exhibits a certain degree of translucency when viewed in thin sections.
Plastic pallets made from this material not only have good impact resistance, high hardness, and excellent load-bearing capacity, but they are also easy to reprocess with minimal degradation.
They are widely used for stacking multiple layers of goods, ground circulation, forklift handling, and shelving, making them one of the most commonly circulated pallets in use today.
Polypropylene (PP)
PP is a semi-crystalline thermoplastic polymer made by polymerizing propylene monomers. It possesses high impact resistance, strong mechanical toughness, and resistance to various organic solvents as well as acid and alkali corrosion.
Plastic pallets made from this material exhibit good toughness and ductility, along with certain heat resistance and cold resistance capabilities. They are generally used for manufacturing small-sized food pallets.
Linear Low Density Polyethylene(LLDPE)
LLDPE is a copolymer formed by polymerizing ethylene with a small amount of higher α-olefins under the action of a catalyst, suitable for various thermoplastic molding processes with good processability.
Plastic pallets made from this material not only have high strength, good toughness, strong rigidity, heat resistance, cold resistance, and strong acid and alkali resistance, but also exhibit excellent resistance to environmental stress cracking, high tear strength, and resistance to acids, alkalis, and organic solvents.
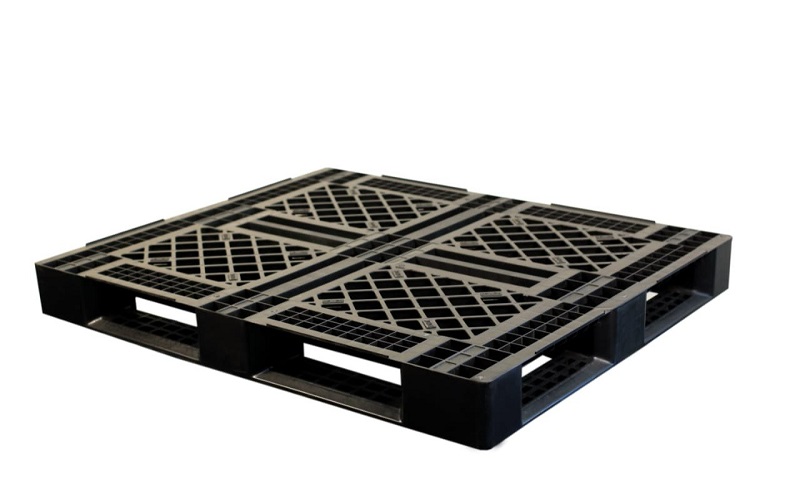
Manufacturing Processes For Plastic Pallets
The manufacturing of plastic pallets involves several key processes, each offering unique advantages. The two main methods are injection molding and blow molding.
Among these, injection molding and blow molding are the most commonly used due to their efficiency and ability to produce high-quality plastic pallets.
Injection Molding
Injection molding is the most widely used process in plastic pallet manufacturing. This method allows for precise control over the dimensions and structure of the pallet, making it ideal for producing high-precision, complex designs.
The versatility of injection molding enables the production of pallets with various surface textures and bottom structures, such as flat,grid,stringer and nine-leg designs.
For instance, injection-molded pallets are favored for heavy-duty applications in industries like automotive and construction due to their high load capacity and durability.
The drawback of injection-molded pallets is the high initial cost, as the investment in injection molds and equipment is substantial. Additionally, once the plastic pallet mold is customized, it is difficult to change the design, and the cost of iteration is high.
Blow Molding
Blow molding, also known as hollow blow molding, involves extruding molten plastic into a tubular form, which is then placed into a mold and inflated using high-pressure air to form the pallet. This process is particularly effective for creating hollow, double-sided pallets that excel in load-bearing capacity and impact resistance. Common designs include blow-molded nine-leg and double-sided pallets.
While blow-molded pallets offer excellent durability, they do have some limitations. They cannot incorporate internal steel reinforcements, which may make them less suitable for certain racking applications. Despite this, blow molding remains a popular choice for producing durable plastic pallets with impressive structural integrity and resilience.
Structural Design Principles Of Plastic Pallets
The structural design of plastic pallets is crucial for ensuring their performance and compatibility with various logistics and storage systems.
The dimensions and shapes of plastic pallets should adhere to international or domestic standards, such as 1200mm×1000mm or 1100mm×1100mm, to ensure seamless integration with automated storage and retrieval systems.
Controlling the dimensional tolerance within ±3mm is essential for stable operation and precise positioning in conveyor and racking systems.
Plastic pallets must be designed to accommodate both static and dynamic loads. Static load capacity depends on the specific application, ranging from around 1 ton for light goods storage to 5 tons or more for heavy machinery parts.
Dynamic load capacity is typically 50% to 70% of the static load capacity to ensure reliability during frequent handling operations. The structural design should balance strength and weight, with common configurations including stringer, perimeter, and nine-leg designs.
Additionally, the design must consider load stability. Features such as rims, anti-slip surfaces, and interlocking mechanisms help secure goods during transport and storage, preventing slippage and enhancing safety.
These design principles ensure plastic pallets remain durable and effective across applications like warehousing and transportation.
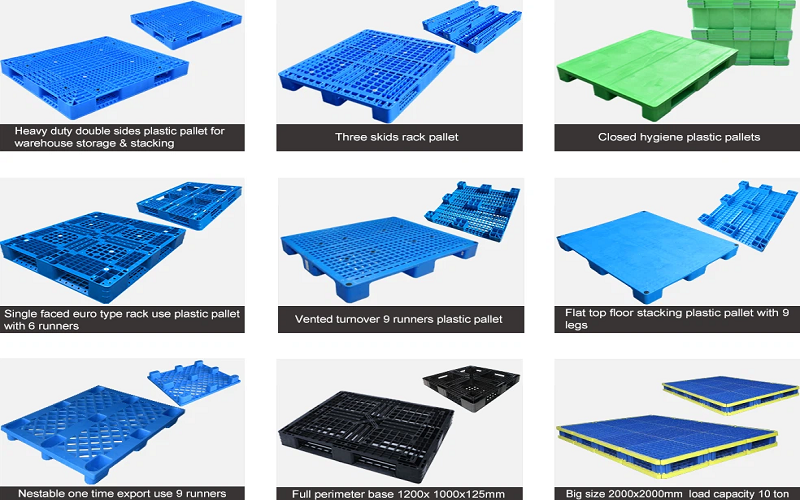
Quality Control And Equipment Requirements In Plastic Pallet Manufacturing
In the realm of plastic pallet manufacturing, advanced production equipment and technology are fundamental to maintaining market competitiveness and ensuring product quality.
High-performance injection molding machines play a central role, with their injection pressure, speed, and temperature control parameters directly impacting the flow and filling of the plastic melt.
Precise adjustment of these parameters results in uniformly structured pallets without bubbles or shrinkage, significantly enhancing overall strength and durability.
Beyond the core equipment like injection and extrusion machines, the integration of automated production lines has revolutionized plastic pallet manufacturing.
These automated lines encompass raw material pre-treatment, molding, post-processing, and quality inspection, enabling continuous and intelligent production.
Automation minimizes human error and variability, ensuring consistent product quality and stability. It also boosts production efficiency and reduces costs, with some reports indicating a 3-5 fold increase in efficiency and a 40%-50% reduction in labor costs.
Automated systems can also monitor equipment status and product quality parameters in real-time, issuing alerts and adjustments when anomalies are detected.
This proactive approach effectively prevents the production of defective products and enhances overall manufacturing reliability.
Such stringent quality control measures and state-of-the-art equipment are essential for producing high quality products, including high-quality plastic pallets that meet industry standards, specific requirements, and customer expectations.
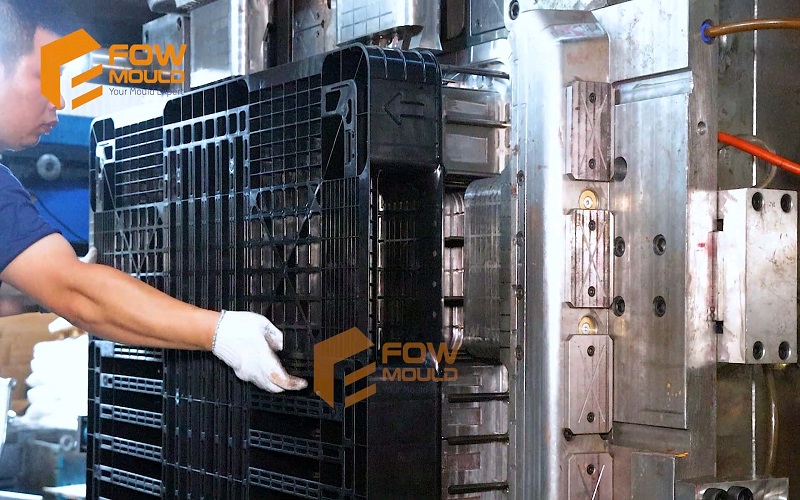
Advantages Of Using Durable Plastic Pallets
Plastic pallets offer several advantages over traditional wood pallets, making them a popular choice across various industries.
One of the primary benefits is their lightweight design, which makes them approximately 40% lighter than wooden pallets. This reduction in weight decreases labor intensity and human error risks, ultimately lowering operational costs.
Additionally, plastic pallets have a significantly longer lifespan, lasting 8-10 years, compared to the 3-5 year lifespan of wooden pallets. Although the initial purchase cost of plastic pallets is higher, the annualized cost is much lower due to their durability and longevity.
Environmental sustainability is another significant advantage. Modern plastic pallets are often made from 100% recycled materials, greatly enhancing resource utilization. Their modular design allows for a recycling rate of up to 95%, supporting the development of a circular economy.
Moreover, plastic pallets can be customized to fit various cargo sizes and shapes, providing flexibility and adaptability in complex logistics scenarios with custom sized pallets.
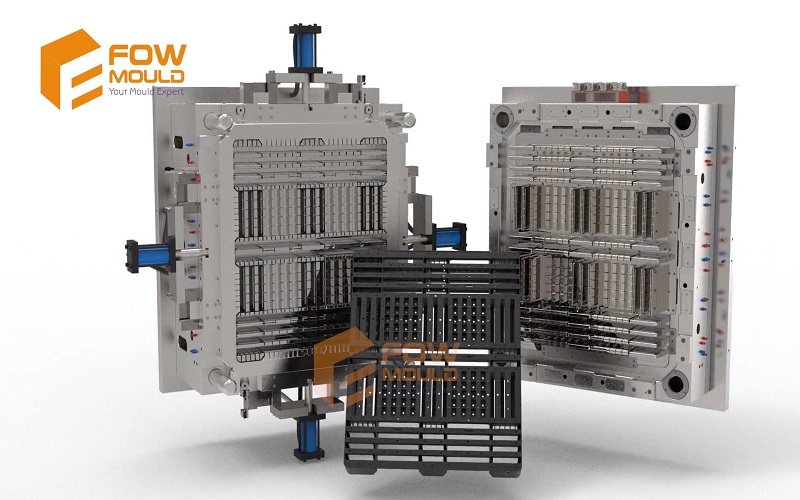
Environmental Impact and Sustainability of Plastic Pallets
Plastic pallets play a significant role in the circular economy due to their reusability, recyclability, and refurbishability, which help reduce waste and resource consumption. Their durability and compatibility with automated logistics systems extend their service life and lower environmental impact.
Recycled high-density polyethylene (rHDPE) and polypropylene (rPP) account for 30-70% of the raw materials used; for example, CHEP achieves 100% reusable plastic pallets. Using rHDPE/rPP can reduce emissions by 1.5 tons per ton of plastic and lower costs by 10-20%.
Through cleaning, sorting, and additive optimization, recycled materials can reach 90% of the performance of virgin materials. However, impurities and aging may affect quality, necessitating the use of spectroscopic analysis and automated sorting to ensure purity.
Closed-loop recycling systems collect, refurbish, or reuse pallets to minimize waste. The application of bio-based plastics and renewable energy further reduces environmental footprints.
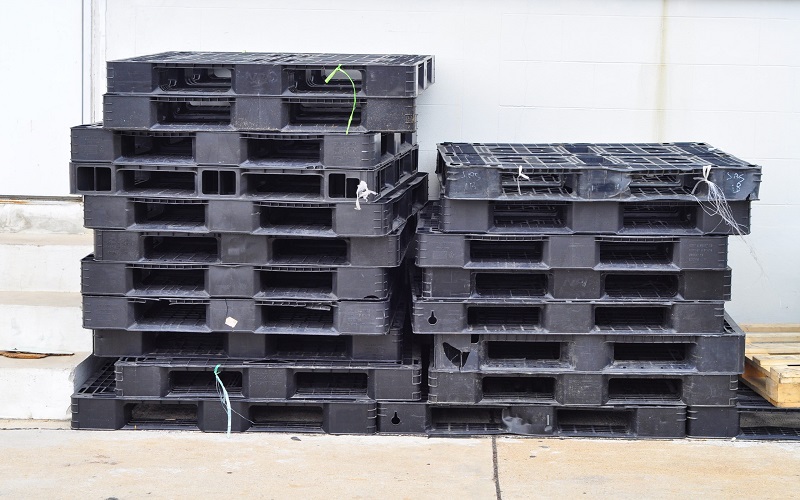
Applications of Plastic Pallets
Plastic pallets are widely used across various industries, including logistics and transportation,food industry Warehousing management
Logistics transport
In logistics and transportation, plastic pallets are preferred for their lightweight, durability, and standardized design. They significantly enhance shipping efficiency and reduce costs by optimizing space utilization and increasing vehicle load rates. The durability of plastic pallets also reduces the frequency of replacements, saving businesses money over time.
The standardization of plastic pallets ensures better space utilization during transportation, leading to more efficient loading and unloading processes. This efficiency translates into lower shipping costs and improved turnaround times, making plastic pallets an invaluable asset in the logistics sector.
Food Industry
In the food industry, plastic pallets play a crucial role in maintaining hygiene standards. Made from food-grade polypropylene (PP) and polyethylene (PE), these pallets prevent contamination and ensure food safety. Their lightweight, sturdy, and durable nature makes them ideal for food processing and storage, enhancing production efficiency and safety.
Plastic pallets are easier to clean and resist moisture and bacteria, making them superior to wooden pallets for food industry applications. This ensures that food products remain uncontaminated throughout the supply chain, from processing to storage and distribution.
Warehousing Management
Plastic pallets play a vital role in warehouse management. Their lightweight design makes handling and operation more convenient, reducing workers’ labor intensity.
The standardization and uniform dimensions of plastic pallets facilitate their use with various logistics equipment such as forklifts, shelves, and conveyor belts, greatly improving logistics operation efficiency and overall coordination.
Additionally, the high durability and impact resistance of plastic pallets enable excellent performance in warehouse environments, reducing resource waste and replacement costs.
Packaging Industry
In the packaging industry, plastic pallets are versatile and suitable for a wide range of goods, including boxed food items,consumer goods,industrial parts and chemical raw materials
Their design allows for easy handling by forklifts and other equipment, significantly improving loading and unloading efficiency while transporting and lifting.
The variety of sizes and load capacities available for plastic pallets ensures they can meet the diverse needs of the packaging industry, from lightweight goods to heavy-duty applications.
The adaptability of plastic pallets makes them a valuable asset in the packaging industry. Their resilience and ease of use translate into lower operational costs and improved logistics efficiency, making them a preferred choice for many packaging applications.
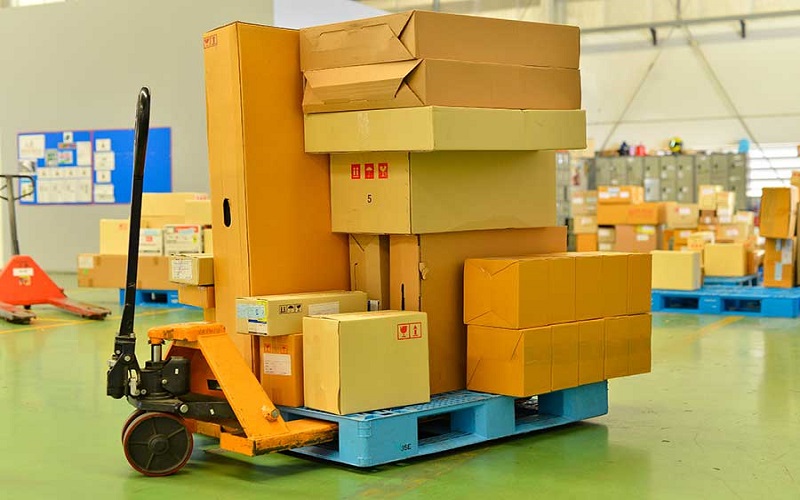
How To Choose Plastic Pallets?
Choosing the right type of plastic pallet is crucial for optimizing logistics operations, enhancing efficiency, and ensuring product safety.
By understanding the various materials, manufacturing processes, and applications of plastic pallets, businesses can make informed decisions that align with their specific needs and operational goals.
Whether for shipment, storage, or packaging, the versatility and durability of plastic pallets make them an indispensable tool in modern logistics and supply chain management. A ship can effectively transport these essential plastic pallets.
If you are looking for a reliable plastic pallet manufacturer, FOWMOULD is your ideal choice! We specialize in customized plastic pallet services, each pallet is crafted from premium materials, designed to endure heavy loads.
By choosing FOWMOULD company, you will receive high-performance, environmentally friendly, and long-lasting pallet solutions to help your supply chain operate efficiently!
Summary
Plastic pallet manufacturing, as a core component of modern logistics and supply chain management, provides efficient solutions for global warehousing and transportation through its lightweight, durability, and environmental friendliness.
Advanced processes such as injection molding and thermoforming combined with high-quality materials like HDPE and PP ensure excellent performance of pallets under heavy loads and complex environments. The use of recycled materials and bio-based plastics, along with energy-saving and emission-reduction technologies and the introduction of intelligent production lines, not only reduce environmental impact but also improve production efficiency and product quality.
In the future, with the further integration of intelligent technologies such as the Internet of Things and blockchain, as well as circular economy models, plastic pallet manufacturing will continue to lead the logistics industry toward greener and smarter development, injecting new vitality into sustainable growth.