The majority of plastic pieces require further processing before being finished. Many of these procedures aim to enhance the product’s aesthetics and look. The incorporation of mold surface textures is one of those procedures.
A crucial component of the product’s appearance is its surface polish. It also affects how well the product works. As a result, it fulfills both functional and aesthetically pleasing needs. One must realize that a key element is the texture of the mold one chooses. It establishes how well the product functions and how it looks and feels.
When discussing mold textures, manufacturers utilize specific terminology. This is why we have created this blog to inform you about 6 types of mold textures and how to apply them in the injection molding process.
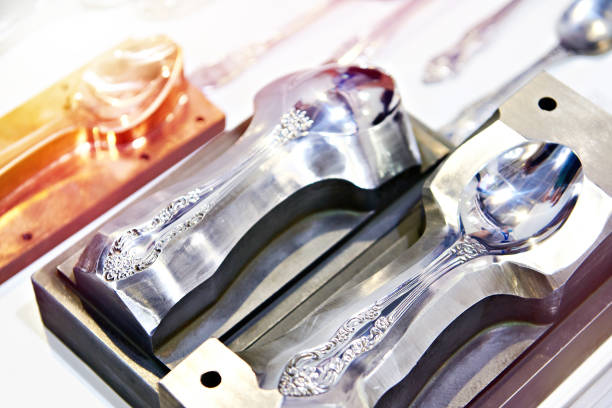
1. What are Mold Textures and Common Types of Texture?
Injection-molded components for engineering products use surface finishes for both aesthetic and functional purposes, which are essential to a successful part design. A product’s appearance and feel are enhanced by its surface finish, which also raises the product’s perceived worth and quality.
A lot of product designers concur that a product’s visual appeal is strongly influenced by how it looks and feels in the consumer’s hands. Some of them can be very unpredictable and challenging to generalize. Texturing often entails making a variety of patterns on a product’s surface.
Some of the common types of mold textures are mentioned below.
1.1 Mold Textures Made with Grit Stone
These textures are produced with the aid of grit sanding stones. These stones can also have grit sizes between 320 and 600. This resembles how sandpaper finishes look. However, surfaces with grit stone textures are far harsher.
Also, the surfaces are not as flat. This is a result of the stones’ more forceful cutting actions. One of the quickest methods for removing mold or tooling marks is this one. On plastic pieces, a matte finish is typically still present.
1.2 Mold Surface Textures Made by Blasting
Rougher finishes can be produced with the aid of abrasive blasting. Sand or glass beads are typically used for this style of texturing. This is equivalent to Category D of the SPI surface finish. Blasting and spraying are random processes that provide a non-directional, homogeneous finish. This particular injection mold texturing aids in producing flat, lifeless finishes.
1.3 Mold Textures Made by Polishing
These types fall under category A of the criteria for the surface finish of injection molding. They are the best grades and provide parts that are sleek and polished. A rotary tool is utilized to polish the surface for this kind of texture.
The polishing happens in an irregular, haphazard manner. The waviness of the surface in this instance has no particular direction. Therefore, whichever angle you observe from, the pattern appears to be the same.
1.4 Mold Textures Made by Sandpaper
The surface finish standards for injection molding fall under Category B. In this instance, the mold tech texture is applied in a back-and-forth motion. As a result, you’ll see certain linear scratches with distinct patterns.
These SPI surface treatments are categorized by manufacturers as semi-gloss. However, making it is less expensive than polishing, and it flawlessly conceals mold flaws. These coatings are sanded using grit sizes ranging from 320 to 600.
1.5 Mold Surface Textures Made with Satin
This is another quick method for making flat surfaces. Comparatively speaking, it is more durable than blasting. On rough surfaces, it is also a fantastic technique to hide weld and sink marks.
1.6 Mold Surface Textures Made with EDM
Electronic Discharge Machining is referred to as EDM. This kind of surface finish produces outcomes akin to spark erosion. Depending on the feature and kind of material you want to process, a certain strategy will be chosen.
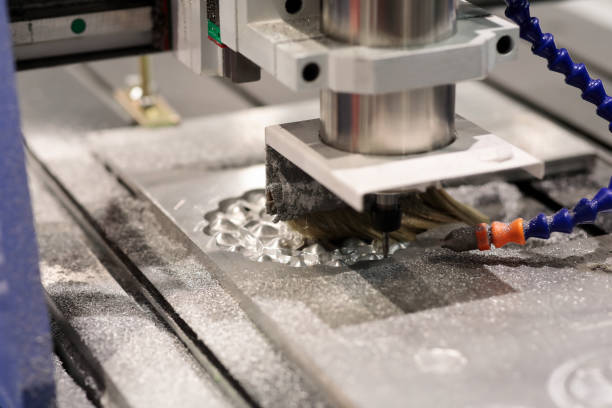
2. Benefits of Texture on Injection Mold
Plastic parts that have been molded have distinctive features and an aesthetic. Because texture offers such a wide range of functions, the designer opts for it. The following are some of the main advantages of mold texturing.
2.1 Hide Surface Imperfections
There are many benefits to adding a surface finish, including the ability to create undercuts and conceal parting lines created during the molding process. There may be several slides that move in and out to inject and release the part, depending on how the mold is made and how it was constructed. Every one of those surrounding areas creates division lines that might or might not be aesthetically pleasing to the product and the customer.
The separation lines can be masked or blended in certain areas with a thoughtful texture or finish. Beyond just adding aesthetic appeal, texture can also help with grip, paint adhesion, and allowing gases to escape the mold during the injection.
2.2 Add Strength of Injection Mold
In addition to aesthetic factors, there are significant practical factors to take into account when choosing an injection molding surface finish. Additionally, trapped gases may be helped to escape by a textured mold.
2.3 Improve Slip Resistance
The layout might require a tight grip to operate at its best. Plastic with textured finishes has better grip qualities. As a result, slip-resistant items typically use injection molding surface treatments.
2.4 Enhance Paint Adhesion
The paint may peel off on an SPI surface finish with a smooth finish. The painted object will, however, stick to the rough surface better. The strength and safety of the part are also improved with a textured SPI surface treatment.
3. Some Disadvantages of Mold Surface Texture
- A significant tooling expense and a protracted setup period.
- Smaller castings can only typically be produced using the permanent mold casting method.
- A high production volume is required in order for this technique to be an economically feasible manufacturing alternative because of the significant tooling costs involved.
- The life of the mold is shortened by the higher pouring temperature of the molten metal.
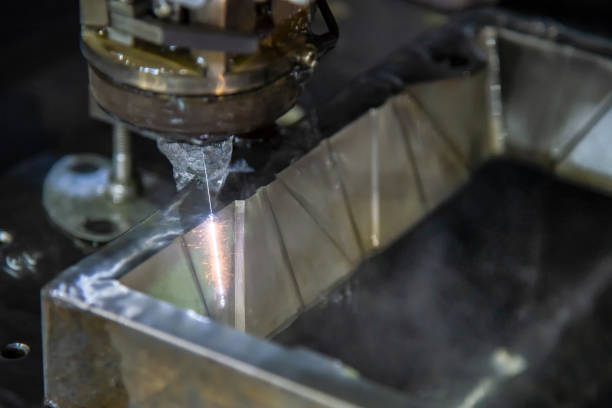
4. The Manufacturing Process of the Mold Texture
Compared with the ordinary injection mold, the injection mold with texture also requires more production steps, including cleaning the mold surface and sealing the part of the mold that does not need texture. This section describes how to create a texture based on a common mold.
- Clean Mold Cavity
This step is to clean the surface of the mold cavity, mainly to clean the surface grease and other substances remaining in the mold production process. If the cleaning measures are not in place, the dirt will affect the display effect of the lines when performing subsequent sandblasting and other processing.
- Seal Mold Against Corrosion
This step is one of the most time-consuming when making textured molds. The surface of the cavity that does not need to be marked is coated with adhesive paper or anticorrosive paint to prevent corrosion.
According to the specific situation of the mold, it is often sealed in the following three ways. Firstly, thick adhesive paper was used to seal most areas of the cavity that did not need to add textures. Then, thin adhesive paper is used to cover the details that cannot be sealed by thick adhesive paper.
Finally, if there are still areas that have not been covered, such as complex curved parts, a corrosion-resistant coating is applied. For parts coated with anti-corrosion coatings, drying treatment is also required.
- Texturing
This step is operationally different depending on the texture you want to achieve. Some textures are created by immersing the mold in a corrosive liquid, while others simply require sanding the mold using tools like sandpaper.
5. Injection Molding Experts Help You Create Textured Molds
It is important to choose an experienced plastic mold manufacturer because the process of making a textured injection mold is usually more complex than that of making a regular injection mold. If you are finding a reliable plastic injection mold manufacturer, FOW Mould is a good choice.
Our team of professionals is ready to optimize the design and provide outstanding results quickly. FOW Mould provides ideal solutions to those who need custom injection molds and offers prototype design, 3D printing, and a series of related services.
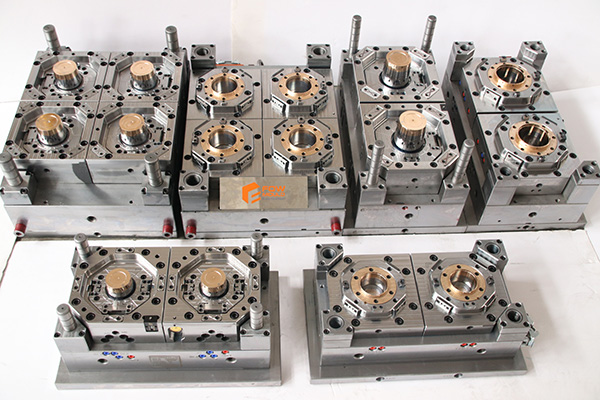
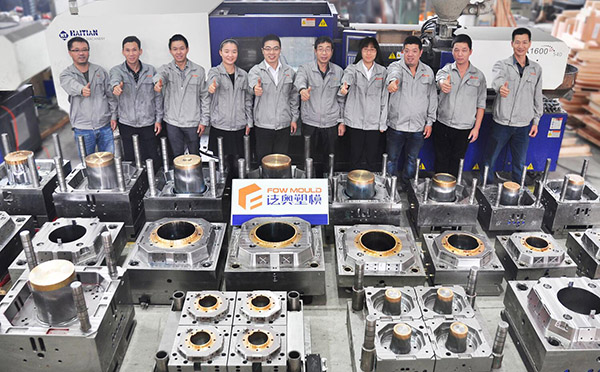
Conclusion
The aesthetics and usability of your product heavily depend on the mold surface textures. It is crucial that you comprehend the many specifics and surface finish requirements. Working with a knowledgeable injection molding firm would be beneficial. At FOW Mould, we assist you in selecting the appropriate surface treatment for your part.
A seasoned maker of plastic injection molds with 40 years of experience is FOW Mould. We are aware of how crucial surface texture is when making plastics. As a result, we are prepared to support you as you navigate this design phase and get the best results. To find out more, contact FOW Mould right away.