ASA is a unique thermoplastic material that, since its inception, has established its position in a variety of applications due to its excellent weather resistance and mechanical properties similar to ABS.
As the mainstream process for manufacturing ASA plastic components, ASA injection molding technology has garnered significant attention and has been widely adopted across various sectors.
This article will delve into this process, unveiling the mystery behind plastic mold manufacturing.
What is ASA material?
Acrylonitrile Styrene Acrylate, also known as ASA, is renowned for its high impact strength and excellent chemical resistance.
ASA plastic is copolymerized from styrene, acrylonitrile, and acrylate rubbery bodies.
Technically speaking, ASA not only retains the primary characteristics of ABS but also combines the weather resistance advantages of PMMA, allowing for its extended application in outdoor settings.
Unlike ABS, ASA replaces the butadiene (B) in ABS with a unique acrylate (A) (a type of rubber material). As a result, ASA possesses exceptional UV resistance and anti-oxidative degradation capabilities, making it one of the top choices for outdoor plastic applications.
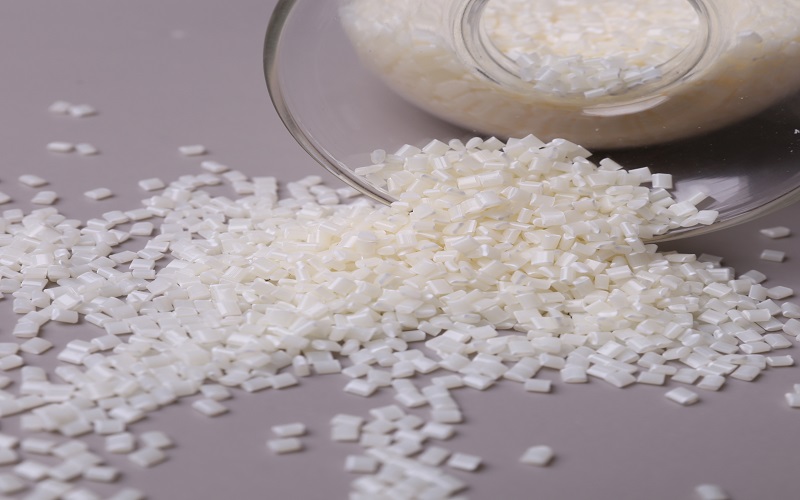
The Properties Of ASA Plastic
ASA is an opaque yellow amorphous polymer, odorless and non-toxic. Its inherent flame retardancy can reach UL94HB level, burns slowly, and emits the smell of benzene and rubber.
The relative density of ASA is 1.05-1.09g/cm3, the notched impact strength is 480-580J/m, tensile strength is 44.2 MPa, the heat distortion temperature under a 1.86MPa load is 85-105°C, and it can operate long-term in the range of -20-75°C, demonstrating relatively good high-temperature resistance.
Chemically, ASA’s stability is similar to ABS. It is resistant to oil, hydrochloric acid solutions, dilute acids, and alkalis. However, it is susceptible to the erosion of esters, ketones, aromatics, halogenated compounds, and alcohols.
Compared to ABS, ASA lacks double bonds. This not only provides resistance against degradation, aging, and discoloration from UV radiation but also resists the effects of thermal oxidation during processing, preventing decomposition and color change.
Due to these characteristics, ASA stands out as one of the plastics with superior weather resistance, with an aging resistance that’s over 10 times higher than ABS.
Homologues of ASA include ABS and AES, with their respective rubber phases being polybutyl acrylate, butadiene/styrene copolymer, and ethylene/propylene copolymer.
Research indicates that the lower the acrylate content in the rubber phase, the higher the impact strength of the resin.
Furthermore, ASA’s excellent co-extrusion properties make it suitable for co-extrusion with PVC and PC.
ASA can be used as a base material for dye modification or as a weather-resistant additive for PVC.
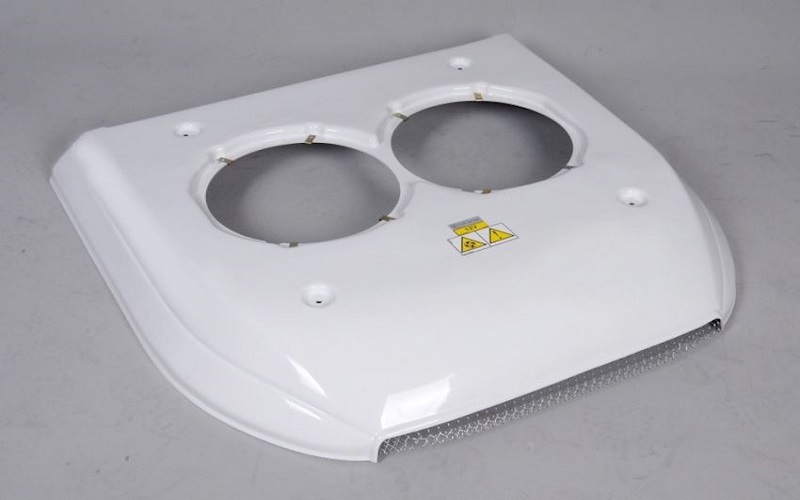
What Are The Advantages Of ASA?
Based on the aforementioned properties, ASA plastic manifests the following advantages during its processing:
ASA is an anti-static material, reducing surface dust adsorption. This endows ASA synthetic resin tiles with a “lotus leaf effect.”
After a rainfall, they appear rejuvenated and as good as new.
Furthermore, ASA possesses robust weather resistance. It not only resists degradation, aging, and discoloration caused by UV radiation ,but also provides solid protection against decomposition or color changes induced by high temperatures during the atmospheric oxidation process.
This enhances the material’s anti-aging and weather-resistant attributes.
Lastly, even after prolonged exposure to wind erosion, ASA material does not gradually turn gray, unlike specially treated aging-resistant ABS.
A Few Disadvantages Of ASA
While ASA demonstrates superior performance in many applications, it also has some significant drawbacks.
ASA plastic is relatively brittle, making it prone to fracture under impact or bending.
If continually exposed to high temperatures, it can deform, losing its original shape and structural stability.
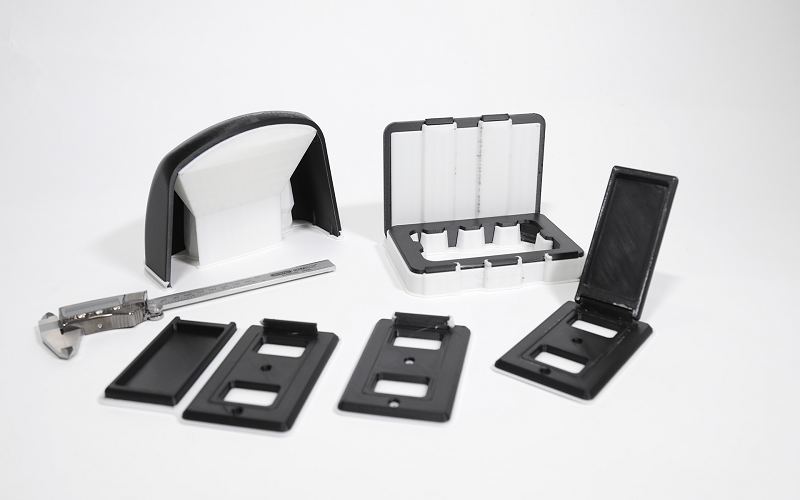
What Are The Processing Options For ASA
Just like ABS, ASA can be easily processed through various techniques such as injection molding, thermoforming, and blow molding.
It is also frequently co-extruded with ABS and PC to enhance its outdoor corrosion resistance.
Another point worth mentioning is that it’s one of the ideal materials for 3D printing nowadays.
(To understand the differences between these techniques, please click to jump to the article “3D Printing vs Injection Molding: A Comparsion“).
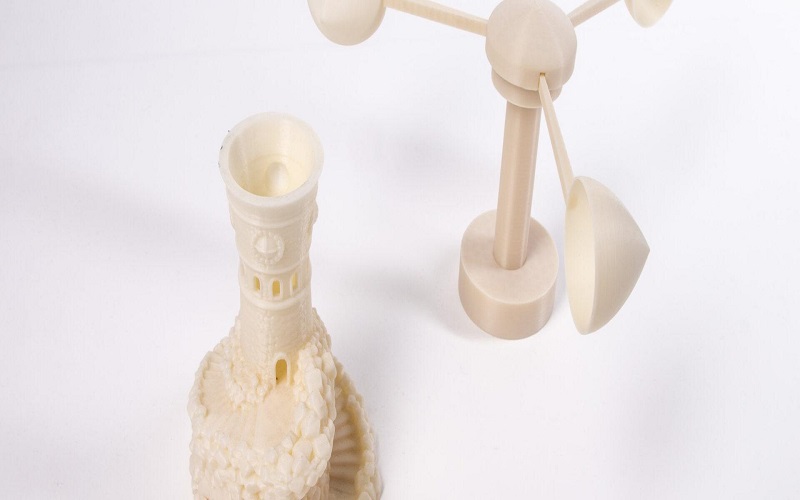
ASA Injection Molding Conditions
In the process of injection molding ASA, strict compliance with the processing conditions is an important guarantee of successful injection molding.
You can refer to the following ASA plastic injection molding parameters to adjust.
ASA Injection Molding Parameters | |||
Drying Temperature(℃) | 80 | Drying Time (hr) | 3-4 |
Mold Temperature(℃) | 40~80 | Residual Material (mm) | 3~10 |
Melt Temperature(℃) | 220~270 | Back Pressure (MPa) | 5~15 |
Injection Pressure(MPa) | 70-120 | Screw Speed(rpm) | 50-90 |
Shrinkage | 0.4%-0.7% | Injection Speed | Moderate |
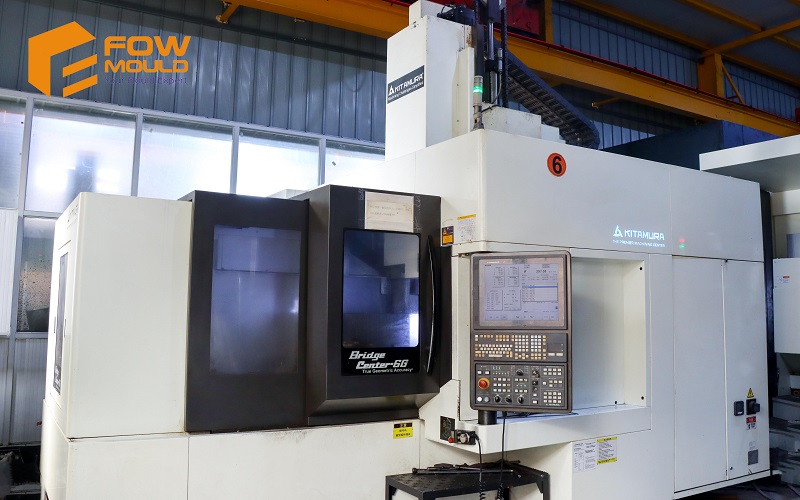
What Are The Uses of ASA Molding?
Despite its higher purchasing cost, ASA’s exceptional quality makes it an ideal material for rugged and robust applications.
Automotive Industry
Due to its excellent resistance to ultraviolet (UV) radiation, ASA has found extensive applications in the automotive sector.
It is commonly used to manufacture parts such as body components and external chrome trim, ensuring the vehicle’s longevity and maintaining its aesthetic quality.
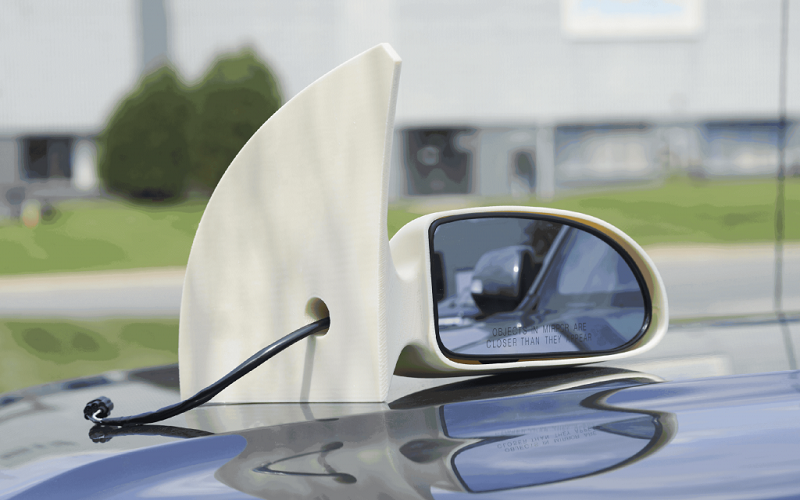
Outdoor Furniture and Equipment
Favored for its weather resistance and durability, ASA plastic, capable of withstanding various climatic conditions, has become the material of choice for manufacturers of outdoor furniture and equipment.
It is commonly used to create durable outdoor furniture, plant pots, and gardening tools.
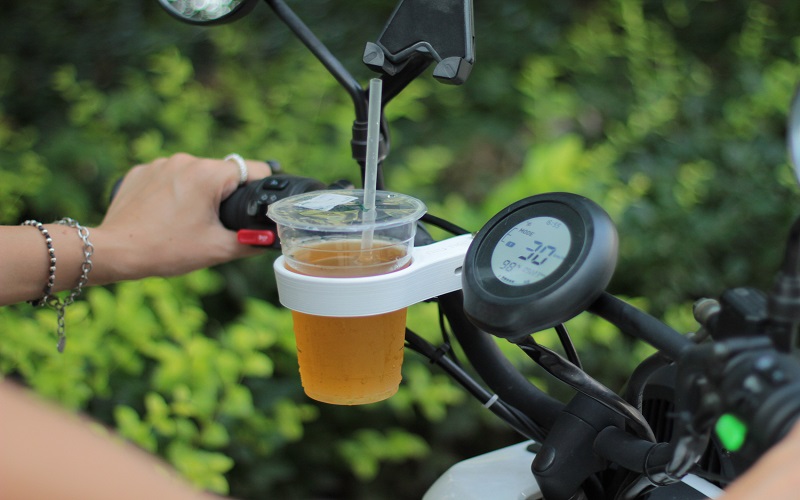
Electronics and Electricals
With its good insulation properties and stability, ASA material has carved out a niche in the electronics and electrical industries.
Especially in the manufacturing of electrical housings, connectors, and other components, ASA provides sufficient toughness and strength, ensuring the long-term performance of these parts.
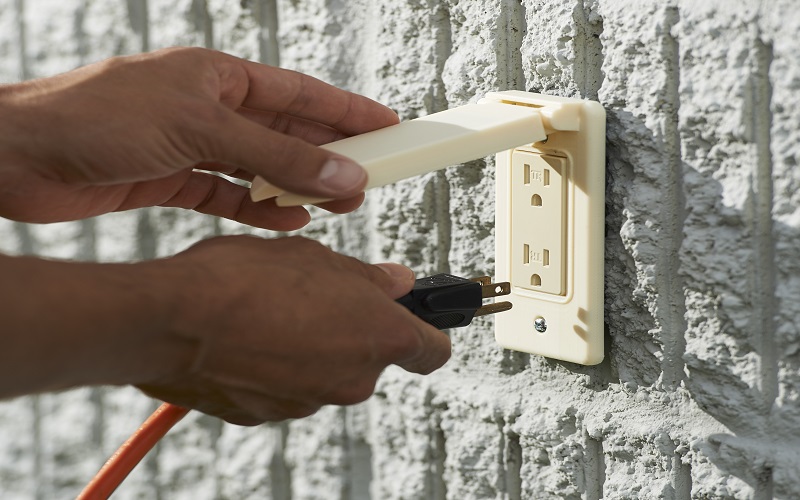
FOWMOULD—Experts in ASA Injection Molding
FOWMOULD is a comprehensive injection molding company in China, specializing in the production of plastic products.
With 40 years of injection molding experience, we are committed to providing our customers with a one-stop injection molding service, covering everything from design to molding.
Every detail is meticulously overseen by FOWMOULD’s design and production team.
Additionally, FOWMOULD promises to offer the best thermoplastic materials, including ASA, ABS, PLA, PMMA, and other popular plastics.
Clients can choose the suitable material based on their project requirements, and FOWMOULD will tailor a cost-effective injection molding solution for you.
If you have injection molding needs for new materials, feel free to contact us. FOWMOULD is always ready to serve you!
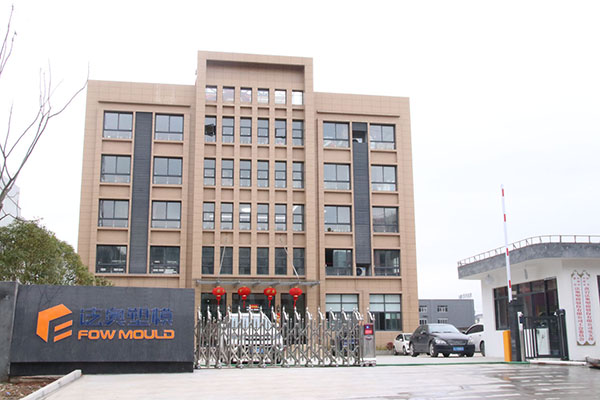