Acrylonitrile Butadiene Styrene (ABS) is a popular plastic widely used in the manufacturing industry, renowned for its excellent mechanical properties, chemical resistance, and processing flexibility.
From industrial applications to household appliance enclosures and 3D printing materials, ABS has become an indispensable material in many industries due to its high strength, toughness, and ease of molding.
In the following content, we will delve into the composition, performance, advantages, application areas, and safety factors of ABS material to provide readers with a comprehensive understanding of this plastic materials.
What Is ABS Plastic?
ABS stands for Acrylonitrile Butadiene Styrene, is a thermoplastic polymer material made from the copolymerization of three monomers: acrylonitrile, butadiene, and styrene.
Each monomer imparts unique properties to ABS:
Acrylonitrile: The acrylonitrile in ABS adds to chemical resistance, fatigue resistance, hardness, and rigidity, increasing the heat deflection temperature.
Butadiene: Imparts excellent toughness and impact resistance to ABS, particularly in low-temperature environments. The rubber phase structure of butadiene enhances the material’s flexibility.
Styrene: Contributes a smooth surface, good processing fluidity, and rigidity, making ABS easy to injection molding and providing high dimensional stability.
By altering the proportions, polymerization methods, and particle size, a range of abs polymer varieties with different impact strengths and flow characteristics can be produced.
ABS initially developed from the modification of PS,it can also be created by using a patented process known as continuous mass polymerization.
ABS was initially classified as an engineering plastic, but with its rapid development, its production volume quickly approached its parent PS. Since 2000, it has been classified as a general-purpose plastic, becoming the fifth-largest general-purpose plastic variety.
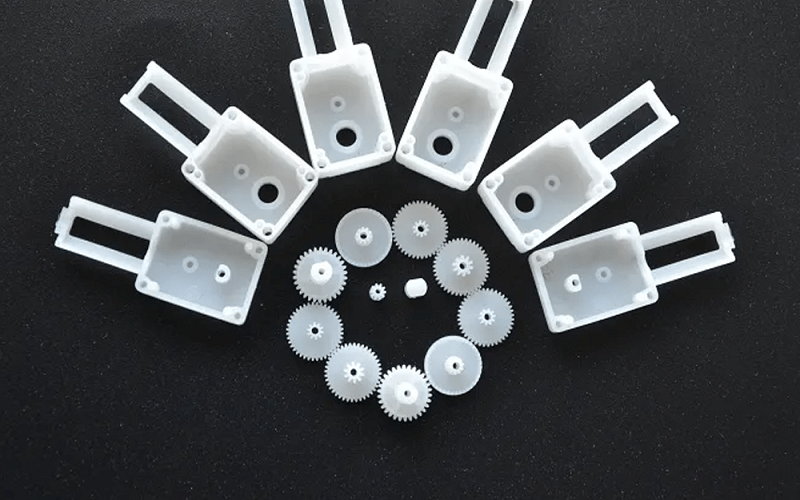
Properties Of ABS Material
Acrylonitrile butadiene styrene is the most widely produced and applied polymer, organically unifying the various properties of PB, PAN, and PS. It exhibits a balanced combination of toughness, hardness, and rigidity, offering excellent mechanical properties.
Mechanical Properties
ABS plastic exhibits good mechanical properties, with good impact strength, allowing it to be used at extremely low temperatures.
It also has excellent abrasion resistance and dimensional stability, along with oil resistance, making it suitable for bearings under moderate loads and low speeds. The creep resistance of ABS is greater than that of PSF and PC, but smaller than PA and POM.
Chemical Resistance
The material similarly provides good resistance to numerous chemicals.ABS resin is resistant to water, inorganic salts, alkalis, and acids. It is insoluble in most alcohols and hydrocarbon solvents but dissolves easily in aldehydes, ketones, esters, and certain chlorinated hydrocarbons.
Thermal Stability
ABS maintains structural integrity within a temperature range of approximately -40°C to100°C. While it offers moderate heat resistance, prolonged exposure to temperatures above 100°C can lead to deformation unless modified with heat-resistant additives.
Electrical Properties
ABS has good electrical insulating properties and is minimally affected by temperature, humidity, and frequency, making it suitable for use in most environments. The dielectric constant and dielectric loss factor of ABS increase with frequency, but the variation is small. ABS has a high volume resistivity, though it is significantly influenced by humidity.
Environmental Properties
ABS as well since the versatile thermoplastic can stand up well to rain, storms and winds. However, to prolong its life outdoors, it must be adequately protected from UV rays and exposure to more.
ABS Properties Table | |
Properties | Reference Value |
Density(g/cm³) | 1.05-1.18 |
Melting Temperature(°C) | 217-237 |
Thermal Decomposition Temperature(°C) | 2>250 |
Modulus Of Elasticity(GPa) | 2 |
Water Absorption(%) | <1 |
Shrinkage(%) | 0.4-0.9 |
Types Of ABS
ABS is most commonly polymerised through the emulsification process or the expert art of combining multiple products that don’t typically combine into a single product.
ABS can be classified into the following main types based on performance and application:
General Purpose ABS: Balances strength, rigidity, and processability, suitable for household appliance enclosures, toys (such as LEGO), and electronic products.
High Impact ABS: Contains a high butadiene content, offering strong toughness and impact resistance, used in automotive components (such as bumpers) and protective gear.
Heat Resistant ABS: Enhanced heat resistance (up to over 110°C), used for automotive interiors and appliance housings.
Flame Retardant ABS: Contains flame retardants to meet fire safety standards, used in electronic products (such as TV casings) and electrical equipment.
Electroplating Grade ABS: Suitable for metal plating, used in decorative automotive parts and bathroom fittings.
Transparent ABS: Offers optical transparency, used for lenses, lampshades, and medical device enclosures.
High Flow ABS: Features good flowability, suitable for complex or thin-walled parts, such as precision electronic enclosures.
Reinforced ABS: Contains reinforcements like glass fibers to enhance strength, suitable for structural parts, such as mechanical supports.
Weather Resistant ABS: Includes UV stabilizers to resist yellowing, suitable for outdoor products, such as gardening tools.
Bio-based/Recycled ABS: Eco-friendly with performance close to standard ABS, used for sustainable consumer goods.
Plus, you can enhance acrylonitrile butadiene styrene’s excellent mechanical properties by adding heat stabilizers and other additives, or by combining it with another plastic.
Each type of ABS plastic is engineered to meet the demands of particular industries and applications, making it one of the most adaptable thermoplastics available.
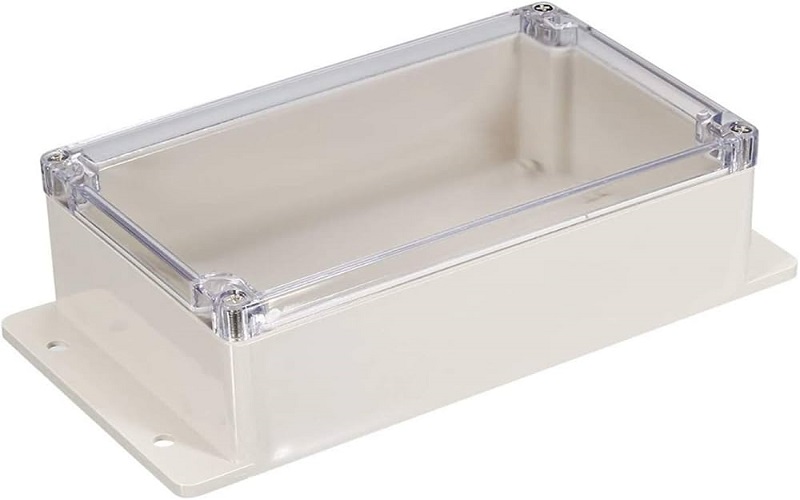
Manufacturing Processes Of ABS Parts
Acrylonitrile butadiene styrene has excellent processing capabilities and can be molded using plastic forming equipment such as injection molding machines, extruders, etc.
It can undergo processes like injection molding, extrusion, blow molding, calendering, laminating, foaming, thermoforming, as well as welding, coating, electroplating, and machining.
Injection Molding
ABS is an amorphous polymer with no distinct melting point. Due to the wide variety of grades, appropriate process parameters should be established during the injection molding process according to the different grades, typically forming at temperatures above 160°C and below 240°C.
In China, ABS injection molding products account for more than 88% of the total plastic products used in refrigerators.
Extrusion
Extruding ABS plastic can produce pipes, sheets, plates, and profiles. The screw of the extruder usually has a high length-to-diameter ratio, typically between 18-22, with a compression ratio of 2.5-3.0. A gradual change type screw with a torpedo head is recommended.
The barrel temperatures are as follows: hopper section 150-160°C, front section 180-190°C, die head temperature 185-195°C, and mold temperature 180-200°C.
CNC machining
CNC machining is suitable for producing low-volume or customized ABS parts with tight tolerances.ABS is easily machined, allowing for clean cuts, smooth surfaces, and intricate detailing without cracking or excessive tool wear.
Applicantions Of ABS
When it comes to ABS plastic parts, the uses are endless. Common uses for the ABS thermoplastic polymer include printers, vacuum cleaners, kitchen utensils, faxes, musical instruments (recorders and plastic clarinets, to name just two) and plastic toys.
Automotive Industry
Various automotive parts that look for weight reduction factors use ABS thermoplastic.It is common material used for parts that include dashboard components, seat backs, seat belt components, handles, door loners, pillar trim, and instrument panels.
Medical Applications
ABS plastic medical applications include manufacturing nebulizers, drug delivery systems, compressors, and medical equipment housings.
Its low melting point renders it inappropriate for high-temperature applications and medical implants.
Consumer Products
ABS is a ideal material for consumer electronics like vacuum cleaners, refrigerator liners, computer keyboards
ABS plastic works well for the large vacuum case designs and housings where an economical, lightweight, and rugged material is required.
3D Printing Material
ABS is a popular filament material in Fused Deposition Modeling (FDM) 3D printing for creating prototypes, functional parts, and custom tools.
Its suitability as a 3D printing filament is determined by its properties, including heat resistance, impact resistance, low-temperature resistance, chemical resistance, excellent electrical properties, and dimensional stability. ABS plastic is considered one of the most stable materials in 3D printing.
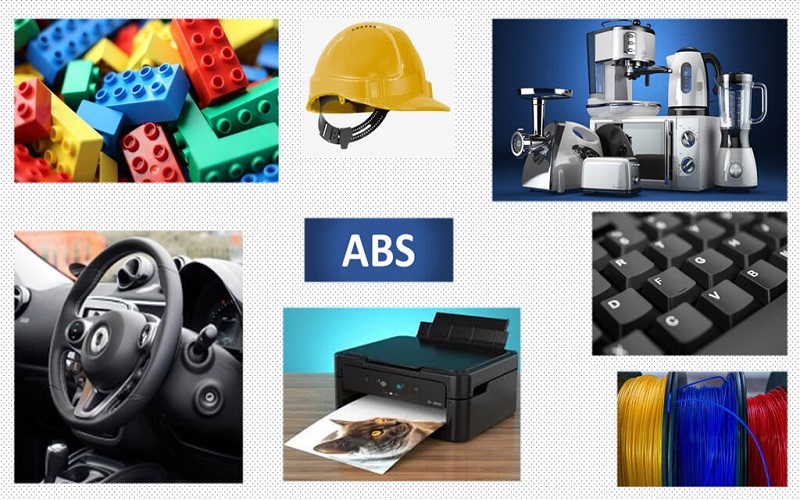
Is ABS Plastic Safe?
When considering “is abs plastic safe”, it is important to note that ABS is generally regarded as a safe and non-toxic plastic for a wide range of applications.
This thermoplastic polymer does not contain harmful substances like BPA or phthalates, making it suitable for use in consumer products, including toys and household items.
ABS plastic is FDA approved for use in food contact applications, which further underscores its safety for everyday use. It is also resistant to chemical leaching, ensuring that it does not release harmful chemicals under normal conditions.
In the context of manufacturing processes, ABS can be safely injection molded, extruded, and machined without releasing toxic fumes when processed correctly. However, it is always advisable to follow proper safety guidelines and use adequate ventilation during processing to minimize any potential risks.
For applications involving children, such as plastic toys, ABS is an ideal material due to its durability and non-toxic nature. It is also a first-choice material for plastic toys as it is rugged and colorful,such as LEGO bricks, which are known for their safety and quality.
Overall, ABS material’s safety profile makes it a preferred choice in many industries, offering peace of mind to manufacturers and consumers alike.
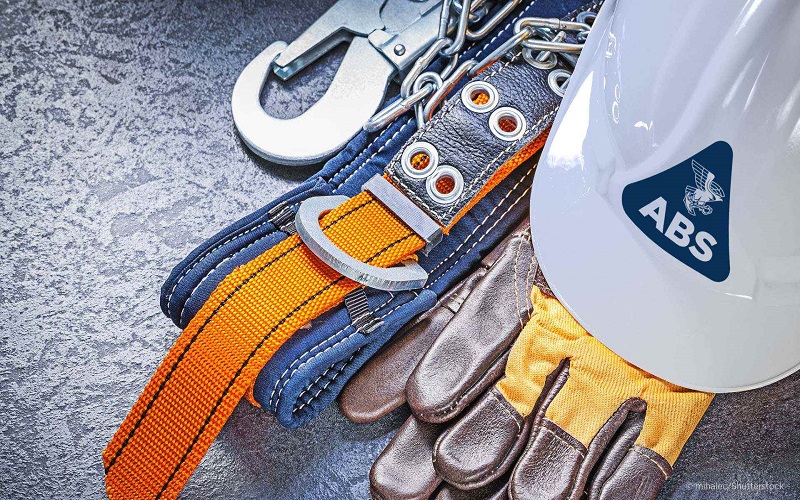
Recyclability Of ABS Plastic
ABS plastic is entirely recyclable and mostly biocompatible. ABS plastic can easily be merged with other materials to create different commercial products that are of high quality yet cost-effective.
Recycled ABS can be blended with virgin ABS to produce high-quality products at a lower cost. The blend maintains desirable properties like toughness, dimensional stability, and surface finish, making it suitable for commercial applications.
While ABS is generally safe for non-invasive applications (e.g., medical device housings), it is not inherently biocompatible for implantable or direct bodily contact uses due to potential leaching of residual monomers or additives.
Specialized medical-grade ABS, certified under standards like ISO 10993, may be used in specific healthcare applications, but these are not typically recycled for such purposes.
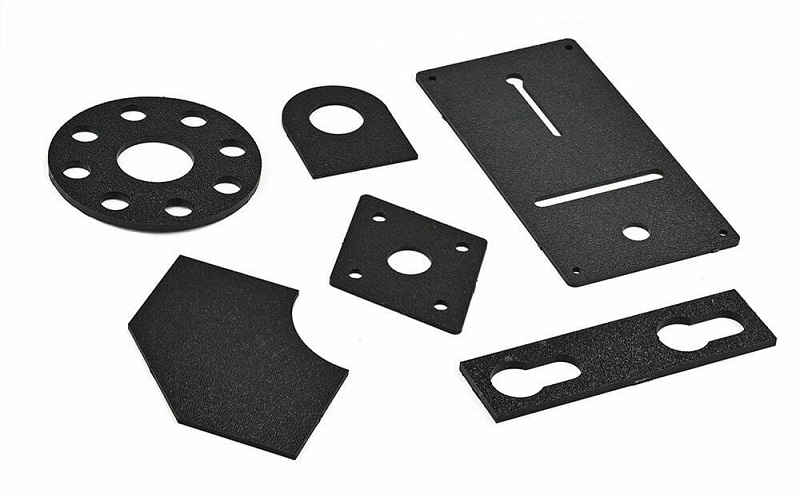
What Are The Disadvantages Of ABS Plastic?
ABS has several limitations that may affect its suitability for certain applications. Below are the key disadvantages of ABS plastic:
Heat Resistance Limitation: ABS does not have the high heat resistance of PP. The heat resistance temperature of standard ABS plastic is about 80°C. While high heat-resistant ABS can reach up to 97°C, prolonged exposure to high temperatures may still lead to deformation.
Poor Weather Resistance: ABS materials tend to age and deform easily when exposed to outdoor or high-temperature environments. Long-term exposure to UV rays can cause the surface to yellow, become brittle, and even crack.
Flammability: ABS is a flammable material with an oxygen index of only 18.5, meaning it can easily catch fire in the event of a blaze. Although adding flame retardants can improve its fire resistance, this increases both cost and complexity.
Conclusion
ABS (Acrylonitrile Butadiene Styrene) is a high-performance thermoplastic renowned for its excellent impact strength, good processing capabilities, and wide range of applications, making it a cornerstone material in modern manufacturing.
Its unique chemical composition and dual-phase structure provide outstanding mechanical properties, chemical resistance, and surface treatment capabilities, leading to its extensive use in automotive, home appliances, 3D printing, toys, and medical equipment.
Although ABS has limitations such as limited heat resistance, UV degradation, and non-biodegradability, its drawbacks are gradually being overcome through additive modification, recycling, and the development of bio-based ABS.
With its cost-effectiveness, processing flexibility, and sustainability potential, ABS will continue to play a significant role in applications that require both functionality and aesthetics, offering reliable material solutions across various industries.