Polyethylene terephthalate (PET) is a widely used thermoplastic polyester known for its lightweight, toughness, and excellent recyclability, playing an irreplaceable role in modern industry.
From beverage bottles to textile fibers, PET plastic is everywhere, profoundly impacting our daily lives. So, what is PET plastic?
In the following content, we will explore the chemical properties, processing techniques, application fields of PET plastic, as well as its environmental and safety impacts in depth.
What Is PET Plastic?
Polyethylene terephthalate (PET) is a type of thermoplastic polymer resin belonging to the polyester family. It is synthesized through a polycondensation reaction between terephthalic acid (or its dimethyl ester, dimethyl terephthalate) and ethylene glycol.
The resulting polymer consists of repeating units linked by ester bonds, giving PET its characteristic properties.Polyethylene terephthalate has beneficial properties such as light weight, high tensile strength, transparency and gas barrier.
These properties make it highly suitable for a wide range of applications, including food and beverage packaging, such as pet bottles and pet containers, textile fibers (commonly called pet fibers), and engineering plastics.
When used as a fabric or a fiber, PET is generally called “polyester”, and when it is in more solid forms, like for packaging or containers, it’s referred to as “PET” or “PET resin.”
The melting peak temperature of PET typically ranges between 225 °C and 255 °C, depending on its molecular weight and crystallinity. PET can exist in both amorphous and semi-crystalline forms, which influence its transparency and barrier properties.
Amorphous PET, for example, is transparent and widely used in packaging material to protect food and beverages by providing better barrier properties against gases like oxygen and carbon dioxide.
Moreover, PET is the most widely recycled plastic, with recycled PET (rPET) being increasingly used to produce new bottles, fibers, and films, contributing to reducing plastic pollution and the carbon footprint associated with virgin pet production.
The raw materials for PET production, such as ethylene glycol and terephthalic acid, are typically derived from crude oil or natural gas, underscoring the importance of recycling to conserve resources and minimize environmental impact.
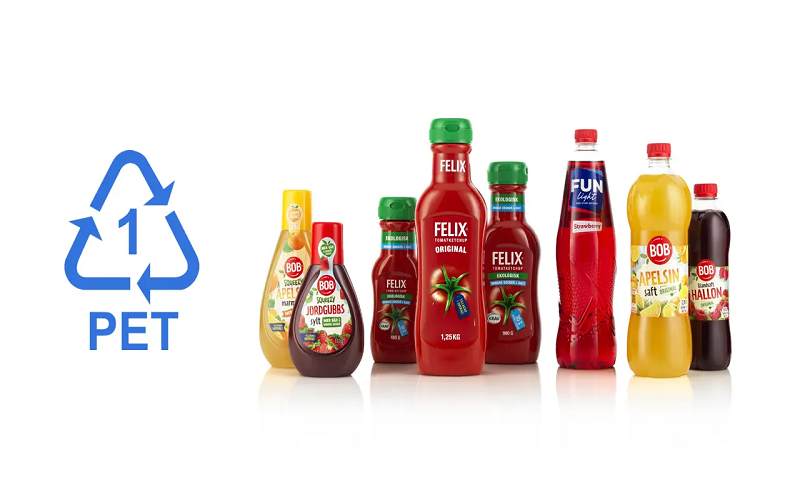
Properties Of PET Plastic Materials
PET is generally known for its light weight, high strength, and excellent chemical resistance.
The polymer chains in PET consist of repeating linked units of ethylene terephthalate, contributing to its robust mechanical and chemical resistance.
Physical Properties
PET is a white or pale yellow highly crystalline polymer with a smooth and glossy surface. It possesses excellent physical properties such as high tensile strength, good dimensional stability, and resistance to impact and abrasion.
The flexural strength of PET plastic is 200 MPa, with an elastic modulus of 4000 MPa. It also demonstrates excellent resistance to creep and fatigue, a high surface hardness, and mechanical properties comparable to thermosetting plastics.
Chemical Properties
PET has good chemical resistance. It is soluble in phenol, concentrated sulfuric acid, nitrobenzene, trichloroacetic acid, and chlorophenol, but insoluble in methanol, ethanol, acetone, and alkanes.
Additionally, PET has low permeability to gases and water vapor, providing excellent barrier properties against gases, water, oil, and odors.
Thermal Properties
PET plastic has the highest heat distortion temperature and long-term service temperature among thermoplastic general engineering plastics.
Reinforced PET shows almost no deformation or discoloration after immersion in a 250°C solder bath for 10 seconds, making it particularly suitable for manufacturing soldered electronic and electrical components.
PET Plastic Properties Data Table | |
Property | Value/Description |
Density(g/cm³) | 1.38–1.40 g/cm³ (amorphous); 1.45 g/cm³ (crystalline) |
Melting Point(°C) | 225-255 |
Tensile Strength(MPa) | 50–80 |
Elongation at Break(%) | 50–300(depending on processing and crystallinity) |
Heat Deflection Temperature(°C) | 65–70°C (amorphous); up to 115°C (crystalline, at 0.46 MPa) |
Electrical Resistivity(Ω·cm) | 10¹⁴–10¹⁶ |
How To Process PET?
PET plastic molding methods are diverse and commonly include injection molding, blow molding, extrusion molding, and thermoforming.
PET injection molding is suitable for manufacturing complex-shaped parts, featuring short molding cycles and high precision.
Blow molding is mainly used to produce PET bottles, such as drinking water bottles and carbonated beverage bottles, enabling lightweight and high-strength bottle structures.
Extrusion molding is often used to manufacture PET films and fibers, which are important raw materials for food packaging materials and the textile industry.
Thermoforming is typically employed to produce PET trays and containers by shaping heated and softened PET sheets, suitable for mass production.
During the molding process, the crystallinity and melt flow index of PET affect the final product’s performance and appearance.
For example, rapid cooling can yield transparent amorphous PET, while slow cooling forms semi-crystalline PET, enhancing mechanical strength and heat resistance. Controlling molding temperature and cooling rate is crucial to obtaining ideal PET products.
Moreover, PET has a relatively high moisture absorption; therefore, drying treatment is usually required before molding to prevent hydrolytic degradation caused by moisture and to ensure product quality.
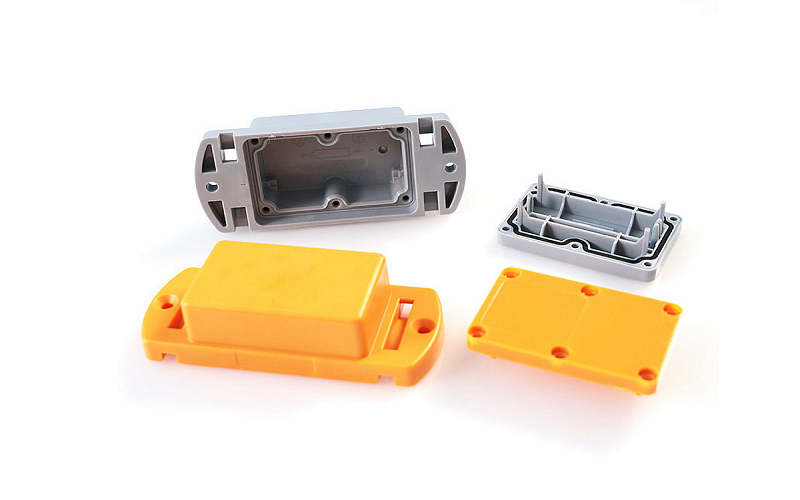
What Is The Environmental Impact Of PET Plastic?
It is estimated that it takes hundreds of years to completely degrade PET plastics by microorganisms in the environment.
As PET is extremely resistant to hydrolytic and enzymatic degradation, it makes PET very hard to be decomposed and therefore the majority of PET polymers manufactured today will persist for a considerable time, at least decades and probably for centuries.
This persistence leads to the accumulation of pet waste in landfills, oceans, and natural habitats, contributing significantly to plastic pollution and plastic litter problems worldwide.
The durability and widespread use of PET, especially in plastic bottles and pet packaging, mean that discarded PET often enters the food chain, posing potential risks to human health and ecosystems.
Additionally, the production and disposal of PET contribute to environmental concerns such as the emission of greenhouse gases and the consumption of non-renewable resources like crude oil and natural gas.
Efforts such as chemical recycling, enzymatic recycling, and improved waste management practices are critical to mitigating the environmental footprint of PET and promoting a more sustainable life cycle for this widely used polymeric material.
Is PET Plastic Safe?
PET water bottles are ubiquitous in our lives, from bottled water to fruit juices and soft drinks. Their lightweight, durability, and transparency make them the preferred packaging material. However, the question “Is PET plastic safe?” often raises concerns.
Generally, PET plastic produced and used according to established standards is considered safe for food and beverage packaging.
Regulatory agencies such as the U.S. Food and Drug Administration (FDA) and the European Food Safety Authority (EFSA) have approved PET for direct contact with consumer products because PET is inert and poses a low risk of leaching harmful substances under normal conditions.
However, there are concerns about the potential migration of certain compounds, such as antimony used as a catalyst in PET production and other trace harmful substances.
Studies have shown that under typical storage conditions, the levels of these substances released from PET bottles are far below safety limits and do not pose significant health risks.
If bottles are exposed to high temperatures (above 70°C), reused beyond the recommended period (generally not exceeding 10 months), or used to store acidic or fatty foods and beverages, the safety of PET may be compromised, as these conditions can increase the likelihood of chemical migration.
To minimize potential risks, it is recommended to use PET containers according to their intended purpose, primarily for single-use or as specified by the manufacturer, and to avoid exposure to extreme conditions.
The widespread use of PET in bottled water, fruit juices, and other beverages reflects its reliability as a safe packaging material in the food industry.
By following usage guidelines and supporting recycling, PET plastic is not only safe but also contributes to sustainability by reducing resource consumption and environmental pollution.
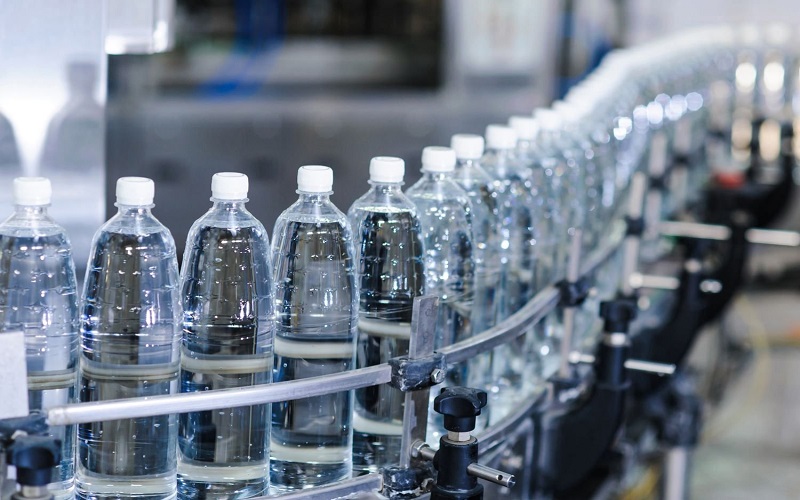
Applications Of PET Plastic
Polyethylene terephthalate is widely used in various fields due to its excellent performance, including packaging, electronics, medical, and automotive industrial applications.
Packaging Material
PET plastic is extensively used in the packaging industry, primarily for manufacturing beverage bottles, food packaging, and daily chemical product packaging.
Due to its lightweight, transparency, impact resistance, and leak-proof characteristics, PET bottles are commonly used for packaging mineral water, carbonated drinks, juices, and more.
In addition, PET plastic is also used to manufacture food containers such as cooking oil bottles and condiment bottles. Its excellent sealing and antibacterial properties effectively extend the shelf life of food products.
Medical Industry
In the medical field, PET plastic is used to produce medical device packaging and disposable medical instruments. Thanks to its outstanding chemical stability and mechanical strength, PET shows significant advantages in these applications.
Automotive Parts
PET plastic is widely applied in the manufacturing of automotive parts, such as distribution panel covers, ignition coils, various valves, and exhaust components.
Moreover, its excellent paintability, surface gloss, and rigidity make it an ideal choice for manufacturing automotive exterior parts.
Electronics and Electrical Appliances
PET plastic plays a key role in the electronics and electrical manufacturing industry. It is used to produce connectors, coil winding tubes, integrated circuit housings, capacitor casings, and other components.
Additionally, PET is widely applied in the production of television parts, tuners, switches, and timer housings.
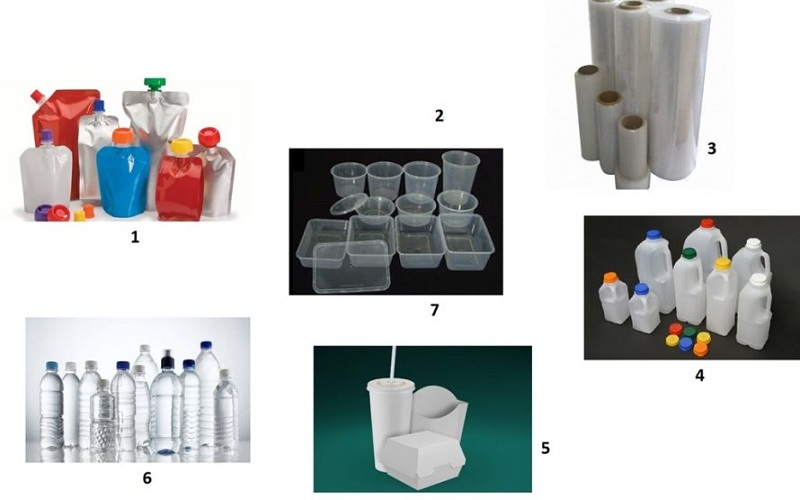
Advantage Of Polyethylene Terephthalate
Polyethylene terephthalate offers numerous advantages that make it an ideal material for various applications:
High Transparency and Aesthetic Appeal
PET exhibits glass-like clarity, allowing clear visibility of packaged contents such as beverages and food. Its smooth and glossy surface enhances product presentation, making it a popular choice for mineral water bottles, cosmetic containers, and more.
Excellent Mechanical Properties
PET boasts high tensile strength, excellent abrasion resistance, and dimensional stability, making it well-suited for transportation and storage without deformation or damage.
Outstanding Barrier Properties
PET provides effective barriers against gases like oxygen and carbon dioxide, as well as moisture vapor. This capability helps extend the shelf life of food products by preventing spoilage and contamination from external odors.
Safety and Environmental Friendliness
PET is non-toxic, odorless, and complies with food-grade standards. It contains no bisphenol A (BPA) and is widely recyclable. Recycled PET (rPET) is extensively used in fibers, packaging, and other industries, contributing to resource conservation and reducing environmental impact.
Light Weight and Cost Efficiency
Compared to glass and other packaging materials, PET is significantly lighter, reducing transportation costs and carbon footprint. Its cost-effectiveness combined with performance makes it a preferred choice in large-scale manufacturing.
Thermal and Chemical Resistance
PET maintains stability under a broad temperature range and exhibits resistance to many chemicals, making it suitable for various industrial applications including food packaging and electronics.
Versatility in Processing
PET can be processed through multiple methods such as injection molding, blow molding, extrusion, and thermoforming, allowing the production of diverse products from bottles and films to fibers and engineering plastics.
These advantages collectively contribute to PET’s widespread adoption in industries ranging from food and beverage packaging to textiles and automotive components.
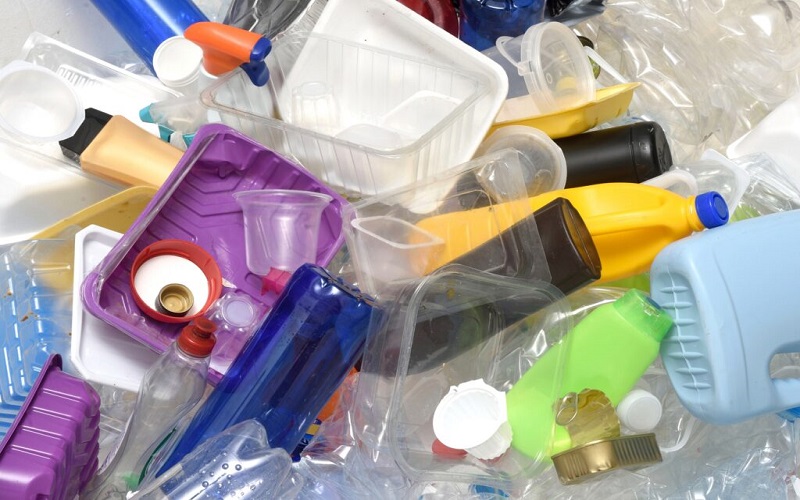
Disadvantages Of Polyethylene Terephthalate
The main disadvantages of polyethylene terephthalate PET include:
Poor high-temperature resistance: PET plastic easily deforms at high temperatures and may even release harmful substances. Its heat resistance is approximately 65°C; beyond this temperature, deformation occurs and harmful substances may migrate.
Susceptibility to chemical damage: Although PET has relative resistance to many chemicals, it may undergo hydrolysis or degradation reactions under conditions of high temperature and high concentrations of strong acids or bases.
Surface vulnerability: The surface of PET plastic is prone to scratches and abrasion, especially during daily use when it may come into contact with sharp objects or experience friction.
PET vs PETG
PET and PETG are two common transparent materials that are often confused due to their similar names, but they differ significantly in chemical structure, performance characteristics, and application fields.
PET is polymerized from purified terephthalic acid (PTA) and ethylene glycol (EG), with an orderly arranged molecular chain. It is a crystalline polymer that can form amorphous or semi-crystalline structures. Its rigid molecular structure gives it high strength but relatively low toughness, making it commonly used in packaging applications such as beverage bottles.
PETG, on the other hand, is a type of polyester new material, fully named polyethylene terephthalate glycol-modified (polyethylene terephthalate-co-1,4-cyclohexanedimethanol).
Compared to PET, PETG incorporates 1,4-cyclohexanedimethanol as a key copolymer monomer in its chemical structure. It offers superior transparency (>90%) and toughness (impact strength 2–3 times that of PET) but has poorer barrier properties. PETG is widely used in medical devices and cosmetic packaging.
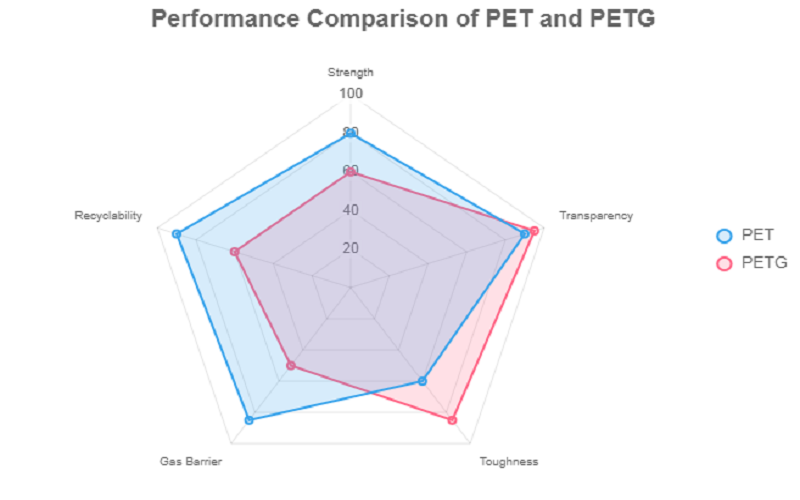
Conclusion
In summary, polyethylene terephthalate is a lightweight, high-strength, transparent, and recyclable thermoplastic polyester widely used in beverage bottles, food packaging, textile fibers, medical devices, and industrial products.
Its excellent chemical stability, gas barrier properties, and food safety certifications (such as FDA and EFSA) make it the preferred material in the packaging and textile industries.
Although PET plastic is sensitive to high temperatures (above 70°C), has a relatively high production carbon footprint (2.2–3.0 kg CO₂/kg), and poses risks of plastic pollution, the adoption of bio-based PET, lightweight design, and advanced recycling technologies enable PET to meet performance requirements while promoting sustainability, providing a balanced solution for modern industry and environmental goals.