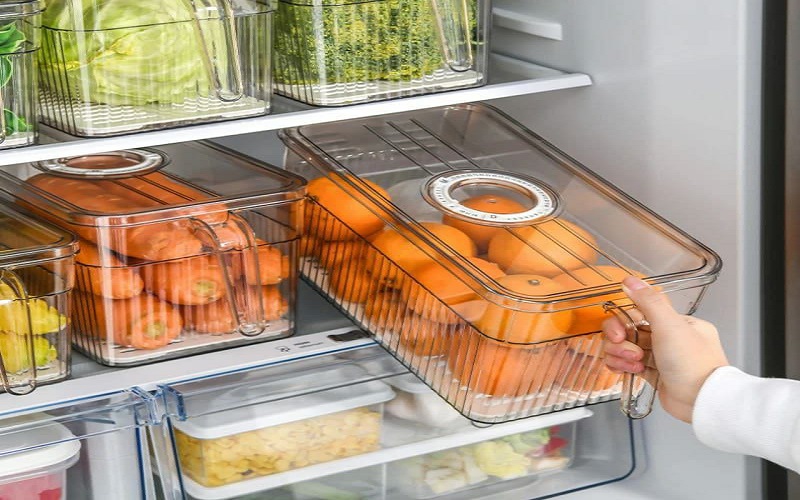
Share :
Share :
Tooling, specifically machine tooling, lays the foundation of the manufacturing and mould design. Different types of molding processes require different kinds of tooling. In order to receive properly functioning parts, it is important to choose the right type of tooling.
Urethane Molding and Injection Molding are the two common types of molding processes. In urethane molding, parts are produced using silicone, that is, soft tooling. Whereas, plastic part designs for injection molding are produced using aluminium, that is hard tooling. Understanding the difference between the two types of molding will help save both on your time and budget.
An injection mold is a customized machine tool that is used in the production of injection molding products. It is used to mold molten pieces of plastics together to form molding products. For those who provide plastic injection molding service, injection mold is indispensable.
In this article, we would briefly discuss the different (soft and hard) tooling methods. The following guide of the difference between soft tooling and complex tooling will assist you in concluding which one to use.
The first method of tooling is known as Soft tooling, which is relatively more cost-effective. This method is popularly used with cast urethane molding. It is generally used by manufacturers when a low volume of parts is required. If you ask yourself, which soft tool material suits cast urethane the best, then the answer will be silicone. Another reason why it is preferred is that it is ideal for small plastic products, such as auto molds. Furthermore, the materials needed for soft tooling are flexible, and easy to work with.
Another reason manufacturers pitch on soft tooling is its suitability for prototyping or other projects that call for a functional yet easy-to-use product with a good finish. You can even create intricate mold patterns using a soft tooling method, which otherwise would take a much longer time to come to produce if you go for other alternatives.
Not every star shines the brightest, and it does have some loopholes forbye. As for soft tooling, the method cannot be used for high volume production. Another major demerit of this method is that the structure of silicone lacks durability and wear resistance. Its durability starts to wear off with each use, making it next to impossible to continue the same silicon tool in the long run. It needs regular replacement as well, which hinders the overall process.
Hard tooling is another type of tooling method that is mostly preferred for manufacturing an injection molding product . These hard tools make use of metals like steel, aluminum, nickel alloys, and others that can withstand many production cycles. You can use these tools without having to swap them out for new ones regularly. As a result, this method allows manufacturers to produce high volumes of parts as fast as possible. All the manufacturers, who have requirements for high volume production and have tough testing requirements, prefer hard tools over soft ones.
As compared to silicone molds, the aluminium molds require less man-power. Also, the curing process takes somewhere in between a ten seconds to a ten minutes. Thus it produces parts faster than the soft tooling method. The drawback of using the hard tooling method is that it takes much more time, and a heavy amount needs to be invested into it. Manufacturers who seek tools for short production or those who wish to produce products within a stipulated time do not prefer going for this method.
There are several considerations that you need to take into account before settling on one tool. These would be talked about at length in later paragraphs.
Before choosing one tool to make your 3d mold design, you need to consider all the possible outcomes, hurdles, and other things that may come in your way. The below mentioned points will help you in selecting the tool that benefits your business and will cut back on extra costs.
It is advisable to go for cast urethanes when the part has a difficult geometry. This is because it will take much more time to get duplicated via plastic injection molding products. These cast urethanes use 3D printed master patterns and CNC molding, thus resulting in the production of complex soft tools within days.
As we stated in earlier paragraphs, soft tools don’t last for a long time. They would work efficiently up to 25-50 shots, but after that, they will soon require a replacement to make stamping mold design. In contrast to soft tools, hand tools are sustainable and could be used for thousands of shots. The reason is that it can withstand high temperatures (which makes it ideal for high-temperature products) as they are passed through extremities and several durability tests before entering the market.
Cost, beyond a doubt, plays a crucial role in deciding which method to go for. A manufacturer with a limited budget, and with a small requirement, can go for soft tools. However, the manufacturers who have sufficient budget and have a large requirement, may opt for hard tools, provided it fulfills the requirements of the manufacturers and the products in question.
Last but not the least, finishing is an important criteria to consider when deciding on the best tooling method. Cast urethanes are recommended for applications that require production of tools with smooth surfaces that do not require much post tampering.
Furthermore, a hard tool may take several weeks to complete an injection mold lifter design, whereas a finished cast urethane product can be made in 7 or fewer days.
These were a few considerations to be kept in mind and weighed upon clearly before finalizing your decision for mold design and manufacturing. Both the options have their own set of advantages and disadvantages and serve different purposes. Make sure to go through the features of both the methods before settling with one.
Before choosing any option, a mold manufacturer must have a blueprint set in his mind, and must have the required budget for the same. Depending on the budget, and the time constraints, the manufacturer can choose a method that best suits his project requirements.
Please contact us using the form below or emailing (harry@fowmould.com)