What Is Short Run Injection Molding?
Short run injection molding, also known as small batch injection molding or small run injection molding, is a specialized form of plastic injection molding tailored for projects that require fewer parts – typically less than 10,000 units. Unlike traditional injection molding, which is designed for mass production and high-volume runs, short run injection molding focuses on producing a smaller quantity of parts without compromising on quality or efficiency. This method is particularly beneficial for businesses that need a limited number of parts or prototypes in a matter of days.
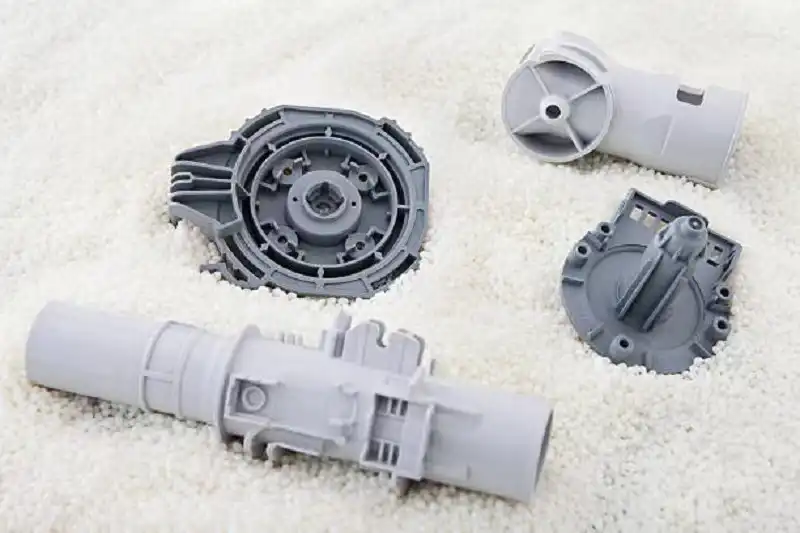
Key Components of the Short Run Injection Molding Process
- Plastic Material: Pellets of plastics such as ABS, PP, PC, and TPU are typically used. The chosen material can vary based on the specific requirements of the part being produced.
- Injection Molding Machine: This machine is responsible for melting the plastic pellets and injecting the molten plastic into the mold. Significant parts of the machine include a heated barrel with a reciprocating screw and a clamping unit.
- Mold or Die: The mold, often made from aluminum in short run injection molding, gives the plastic part its shape. Aluminum molds, despite being less expensive than steel molds used in traditional injection molding, are highly durable and capable of producing high-quality parts.
- Automation System: This system controls the entire injection molding process, ensuring each part’s accurate and consistent production. It can be programmed to control various aspects of the process, such as the temperature of the barrel, the pressure of the injection, and the cooling time.
The Role of Mold Design in Short Run Injection Molding
Mold design plays a pivotal role in short run injection molding.
- Material Selection: Given the low-volume nature of the production, molds are often made from aluminum rather than the more expensive steel used in traditional molding. Aluminum molds heat up and cool down faster, allowing for quicker turnaround times.
- Design Precision: The mold determines the shape, size, and features of the final part, so it must be designed with precision and attention to detail. In short run injection molding, the mold design process often involves the use of CAD software, which allows for precise measurements and complex designs.
- Understanding the Part: The mold design process begins with a thorough understanding of the part to be produced. This includes understanding the part’s function, the stresses it will be subjected to, and the environment in which it will be used. This information is used to determine the best design for the mold, including the number of cavities, the type of gate, and the cooling system.
- Manufacturing the Mold: Once the design is finalized, the mold is manufactured using CNC machining or 3D printing technology. These technologies allow for a high level of precision, ensuring that the mold is manufactured to the exact specifications of the design.
- Testing and Inspection: Once the mold is manufactured, it is tested and inspected to ensure that it meets the required quality standards.
- Expertise Required: The mold design process in short run injection molding is a complex and critical process. It requires a high level of expertise and attention to detail to ensure that the final part meets the required specifications.
Benefits of Adopting Short Run Injection Molding
- Cost-Effectiveness: Short run injection molding is a cost-effective solution compared to traditional injection molding. The molds, often made from less expensive materials, and less expensive machinery result in significant cost savings.
- Speed of Production: Short run injection molding allows for quicker turnaround times. As the molds heat up and cool down faster, the total time to produce each part is reduced, enabling businesses to bring their products to market more quickly.
- Design Flexibility: Short run injection molding offers greater flexibility. It’s easy to make changes to the design without incurring significant costs, due to the lower cost of molds involved in the process. This makes it more cost-effective to produce a new mold if a design change is needed.
- Reduced Waste and Inventory Costs: With short run injection molding, businesses can produce only what they need, reducing waste and inventory costs. They don’t have to produce and store more parts than necessary, which is particularly beneficial for businesses operating on a just-in-time manufacturing model, as it allows them to keep their inventory levels low.
Applications and Industries Benefiting from Short Run Molding
Medical Industry: Short run injection molding assists in producing specialized tools and equipment needed in small quantities, providing precision and customization.
Automotive Industry: Short run injection molding is used to create specific components for unique or limited-edition models, effectively meeting low quantity requirements.
Technology and Electronics: Short run injection molding is crucial in making smaller, precise components for various tech devices.
Startups and SMEs: For companies fine-tuning their market testing, short run injection molding allows high-quality, functional prototyping and small-batch production runs.
Lighting Industry: Given the demand for intricate parts in limited numbers, short run injection molding is essential for producing complex designs without compromising quality.
Consumer Goods: Products that require specific plastic parts in limited quantities often turn to short run injection molding. It can include everything from toys to household appliances.
Comparing Short Run Injection Molding vs. Traditional Injection Molding
Scale of Production: Traditional injection molding is designed for large-scale production, usually over 10,000 units. In contrast, short run injection molding is geared towards smaller scale production, typically less than 10,000 units.
Costs and Lead Time: Traditional injection molding has significant upfront tooling costs and lengthy lead times. Short run injection molding, however, has lower tooling costs and faster production times, making it more cost-effective for low volume production.
Flexibility: Short Run Injection Molding provides more flexibility; it enables quicker iterations and design changes which is especially beneficial for product designers who need functional prototypes or small-batch production runs.
Unit Cost: While the unit cost for short run injection molding might be slightly higher than traditional injection molding, overall it can be more affordable for small batch manufacturing due to reduction in upfront tooling costs and quicker time to market.
Challenges and Solutions in Short Run Injection Molding
Challenges in Short Run Injection Molding | Solutions |
Ensuring consistent quality for small batches can be complex | Utilize modern quality assurance methods and precision automation to ensure consistency |
Transitioning from prototyping to large-scale production can be difficult | Implement “Bridge tooling”, an interim solution for smoother transition |
Potential wear and tear of aluminum molds over long periods | Use high-strength aluminum alloy to extend mold’s life |
Potential higher unit cost than traditional molding for smaller batches | Optimize operation and leverage benefits of quick turnaround, low tooling cost, and faster time to market |
Limited lifespan of tooling due to lower cost materials | Regular inspection and maintenance of molds to ensure optimal operation |
Managing a high mix of products or parts in low volumes requires tighter control | Implement advanced scheduling and inventory management systems |
Ensuring complete fill in parts with complex or thin wall designs | Use advanced molding machines with better control on injection speed and pressure |
Potential difficulty in sourcing materials for small quantities | Develop strategic partnerships with suppliers to ensure material availability |
Conclusion
In summary, short run injection molding is changing the manufacturing landscape. This revolutionary process provides an efficient, cost-effective solution for small and medium-sized businesses and startups looking to introduce new products to the market, conduct prototype testing, or simply manufacture on a smaller scale. With decreased lead time, lower costs, no high minimum orders, and improved flexibility, short run injection molding caters to the evolving needs of today’s market, proving itself invaluable to industries far and wide.
Contact Us
At FOWMould, we pride ourselves on being industry leaders in injection molding. With our state-of-the-art equipment, expert team, and commitment to quality, we ensure that every project, no matter how small, is executed with precision and professionalism. Whether you’re exploring small batch plastic manufacturing or seeking a reliable partner for your molding needs, FOWMould is here to assist. Contact us today to learn more about how we can bring your vision to life.