In recent years, with the continuous progress of science and technology and the growing industrial demand, thermoplastic elastomer (TPV) has shown excellent performance in various fields due to its combination of the processing ease of thermoplastics and the elasticity of rubber.
In this paper, we will discuss in depth the material properties, process parameters and possible challenges of TPV injection molding to provide a theoretical basis and operational guidelines for practical production.
What Is TPV?
TPV, short for Thermoplastic Vulcanizate, is also known in Chinese as Thermoplastic EPDM Dynamic Vulcanized Elastomer or Thermoplastic EPDM Dynamic Vulcanized Rubber.
It is a type of blended thermoplastic elastomer material prepared using dynamic vulcanization technology.
Dynamic vulcanization involves initially blending the thermoplastic resin with rubber in a molten state, followed by the addition of a cross-linking agent.
Under the influence of intense mechanical shear and the chemical cross-linking action of the cross-linking agent, the rubber phase is sheared and broken down into a large number of micron-sized cross-linked rubber particles, which are dispersed throughout the continuous phase matrix of the thermoplastic resin.
As a result, TPV exhibits properties that are closer to those of traditional rubber, including resistance to high temperatures, low compression set, solvent resistance, and oil resistance.
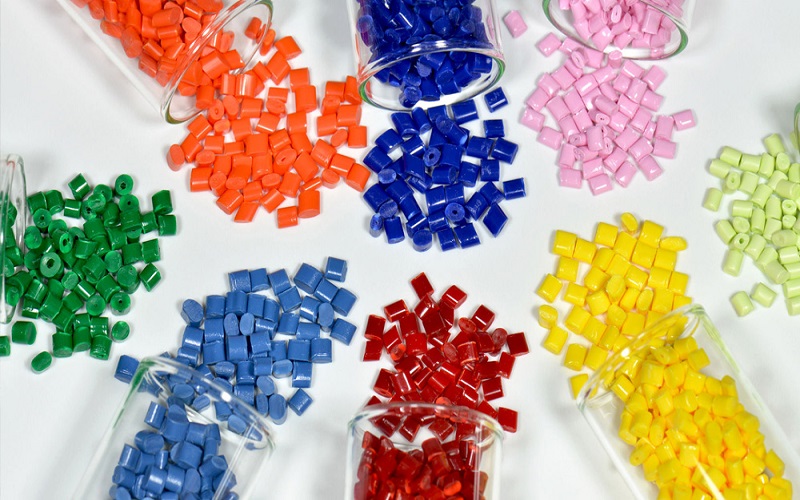
What Are The Properties Of TPV material?
In the two components of TPV, PP serves as the continuous phase, imparting thermoplasticity to the TPV material.
EPDM rubber, on the other hand, acts as the dispersed phase, bestowing rubber-like elasticity upon TPV.
Due to the saturated molecular chain structure of EPDM and its cross-linked structure, TPV possesses certain characteristics that typical thermoplastic rubbers (TPR) lack.
The main characteristics are as follows:
★TPV is lightweight (specific gravity ranging from 0.90 to 0.97), with a uniform appearance, high surface quality, and a pleasant feel.
★ TPV can function normally within a temperature range of -60℃ to +135℃; it can withstand temperatures up to +150℃ when not under load.
★ It offers a wide hardness range, from 25A to 70D.
★ TPV provides excellent resistance to ozone and weathering.
★ It has resistance to dynamic fatigue, outstanding weatherability, and good wear resistance.
★ TPV is environmentally friendly and recyclable, with no significant decrease in performance after six cycles of reuse.
★ TPV offers excellent elasticity and resistance to compression deformation, with environmental and aging resistance properties comparable to EPDM rubber.
★ TPV exhibits the heat resistance and low compression deformation properties of vulcanized rubber.
★It can be processed using thermoplastic processing methods such as injection molding and extrusion, which are efficient, straightforward, and do not require additional equipment. It also has high flowability and a low shrinkage rate.
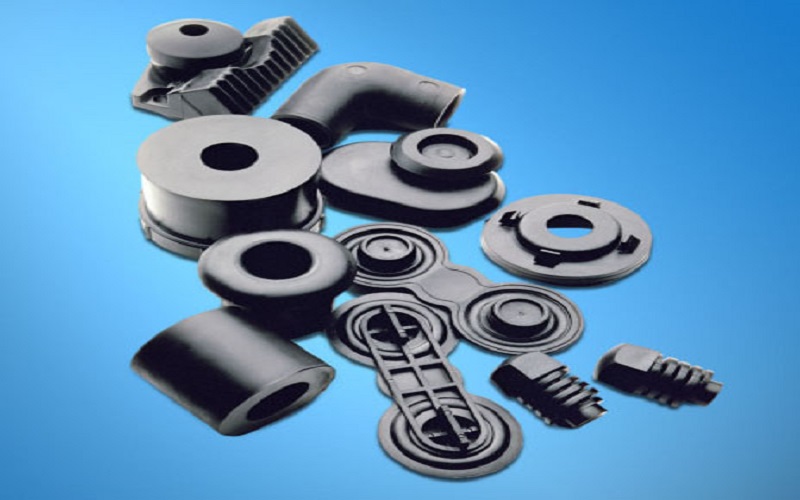
Why Choose TPV Plastic For Injection Molding?
Given these performance characteristics, TPV offers certain advantages over traditional rubber materials, other TPE elastomers (including TPR, SBS, SEBS, TPU, etc.), and plastic materials such as PVC in terms of overall performance and cost.
This provides manufacturing enterprises with new options for product innovation, adding value to their products, and enhancing competitiveness.
Aging Resistance
TPV, a blend of PP (polypropylene) and EPDM (ethylene propylene diene monomer), embodies a combination of plastic and rubber properties.
Through dynamic vulcanization, it exhibits the aging resistance characteristic of vulcanized rubber materials.
Aging resistance encompasses various performance aspects, including resistance to acids and alkalis, high temperatures, and oils, all of which contribute to the material’s longevity and durability.
Resilience
TPV material boasts excellent resilience and resistance to compressive deformation, meeting the requirements for products that necessitate high rebound and minimal compression set.
This ensures the material returns to its original form after being deformed, maintaining its functional and aesthetic properties over time.
Customizability
The surface of TPV material possesses a soft, rubbery feel, and it can be co-injection molded with a variety of materials including PP, PA, PC, ABS, PS, PBT, PET, etc.
Additionally, TPV is available in fully transparent, semi-transparent, and light color series, offering ease of coloring and processing into various forms and shapes.
This versatility enhances the material’s adaptability for diverse applications and product designs.
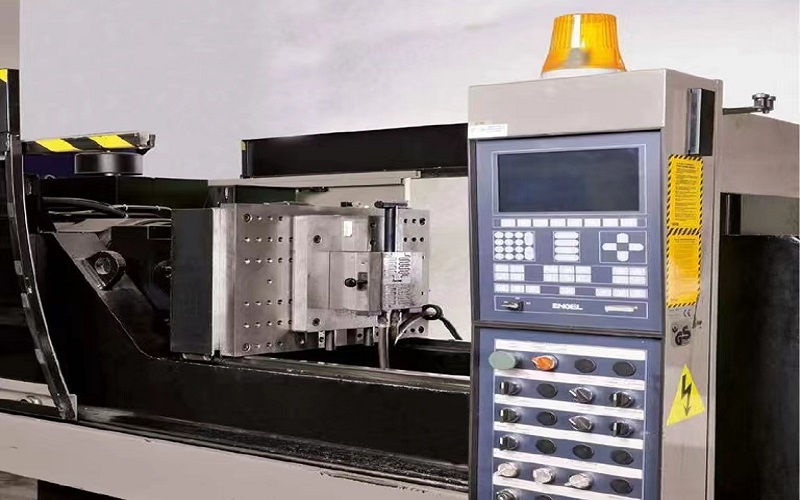
Design Principles for Injection Molded TPV Parts
In order to produce multifunctional, multi-material complex TPV (Thermoplastic Vulcanizate) parts, the TPV injection molding process has become the preferred choice.
However, before embarking on the molding process, designing a part that meets customer requirements and adheres to scientific manufacturing principles is a crucial task.
Firstly, it is essential to design the part to have a uniform wall thickness throughout. This ensures a consistent shrinkage rate across the entire part, thereby reducing warping and indentation.
In situations where variable wall thickness is necessary, it is recommended to gradually transition between thicknesses to minimize warping and indentation (with a maximum wall thickness variation of about 25%).
Secondly, incorporating draft angles facilitates part ejection from the mold. The size of the draft angle depends on the depth of the part being ejected and should take the final use conditions into account.
Generally, draft angles are applied at the mold cavity side and at the cores to ease part ejection during the TPV mold opening phase of the injection molding cycle.
In addition, sharp corners can lead to stress concentration, potentially causing damage during the part’s use. Applying appropriate fillets and chamfers helps reduce stress concentration, provides a smoother flow path for the polymer melt, and eases part release.
For TPV plastic, the recommended minimum radius for fillets and chamfers is 0.5mm, and the wall thickness between internal and external radii should be uniform.
Lastly, TPV surfaces tend to be rough, but they can become glossier as hardness increases.
To achieve a certain level of gloss on the TPV surface, treatments such as applying a slip coating or paint may be necessary, although this can alter the surface properties of the TPV.
It is advisable to add some surface texture to TPV plastic injection molded parts, which can be achieved through various mold surface treatments such as chemical etching, spark erosion, sandblasting, or conventional machining methods.
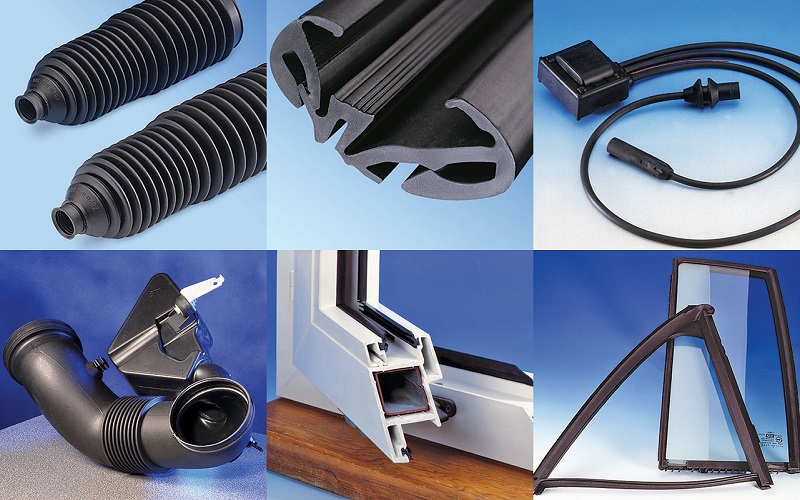
Conditions for TPV injection molding
Compared to vulcanized rubber, TPV injection molding has a shorter cycle time (as it does not require a certain holding time like vulcanized rubber).
Adhering to some of the injection molding conditions listed below will contribute to the successful of TPV molding , enhancing the yield of finished products and reducing raw material wastage.
Drying Treatment
Due to the hygroscopic nature of TPV, it is necessary to pre-dry the material before processing. It is generally recommended to use a hopper dryer at a temperature of 80-110℃ for 2 hours, or an oven dryer at 90-120℃ for 2 hours.
Barrel Temperature
In TPV plastic injection molding, it is typical to control the rear part of the barrel at a temperature range of 165-200℃, the middle and front parts at 180-220℃, while the nozzle temperature generally ranges from 185-210℃.
Injection Pressure
The injection pressure is usually controlled at 2-60 MPa and then gradually increased until the maximum pressure reaches 80-90% or a satisfactory product is obtained.
Injection Speed
The injection speed should be as fast as possible, because TPV cools quickly. A quickly injection speed helps the melt to flow smoothly and ensures the finished product has a good surface finish.
Other Parameters
Mold temperature | 20-60℃ |
Screw speed | 100-200rpm |
Back pressure | 0.4-1MPa |
Screw type | General-purpose three-stage screw |
Applications Of TPV Plastic Injection Molding
TPV (Thermoplastic Vulcanizate) possesses the performance characteristics similar to thermoset rubber while maintaining the processing speed and other advantages of thermoplastic materials.
It has found widespread applications in the automotive, electrical, and various other sectors.
Automotive Industry
- Car sealing strips and series of sealing components.
- High-voltage ignition wires for automobiles.
- Dust covers, mudguards, ventilation pipes, bumpers, corrugated tubes, and intake hoses for cars.
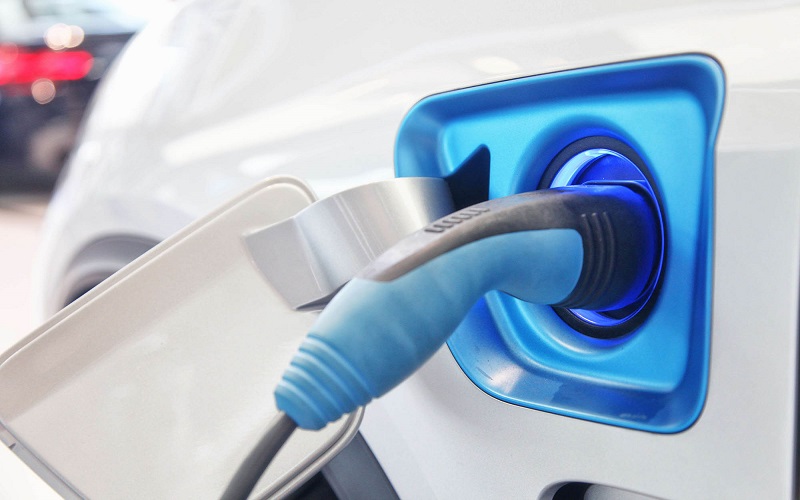
Electronics and Electrical Appliances
- Power outlets, plugs, and protective sleeves.
- Various headphone cable exteriors and headphone jack connectors.
- Battery cases, cordless phone housings, and protective sleeves for electronic transformers.
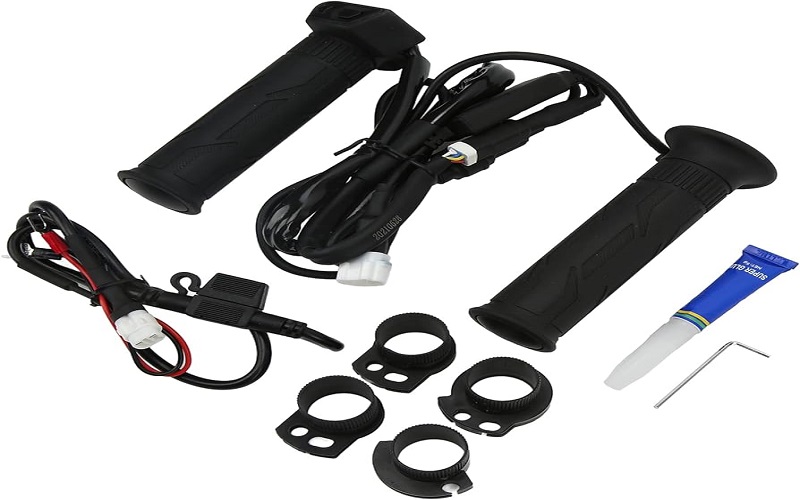
Consumer Products
- Components for manual tools, power tools, weeders, and other gardening equipment.
- Soft rubber components such as syringe plungers, bottle stoppers, straws, and tubing.
- Gaskets and components used in household appliances.
- Handles and grips for products like scissors, toothbrushes, fishing rods, sports equipment, and kitchen utensils.
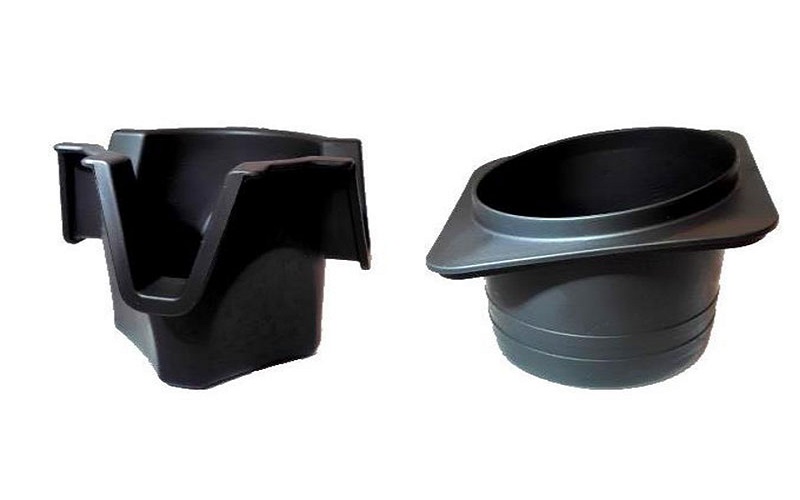
Choose FOWMOULD for Custom TPV Injection Molding Solutions
As a leading expert in injection molding in China, FOWMOULD adheres to the philosophy of innovative development and is committed to providing one-stop injection molding services.
From product design and mold manufacturing to final molding, FOWMOULD has assembled a professional design and manufacturing team to assist clients, and offers free product quotations.
In addition, FOWMOULD promises to provide high-quality raw materials, including TPE, TPU, TPV, and common plastics, offering clients a wider range of material options and the ability to customize production according to client needs.
If you are planning to start a new TPV injection molding project, FOWMOULD will be your best choice. Don’t hesitate, contact us right away!
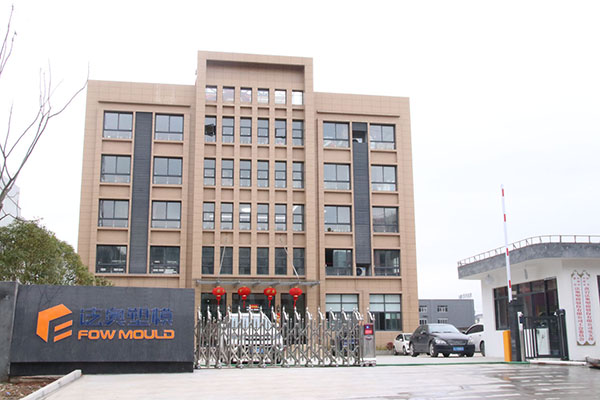
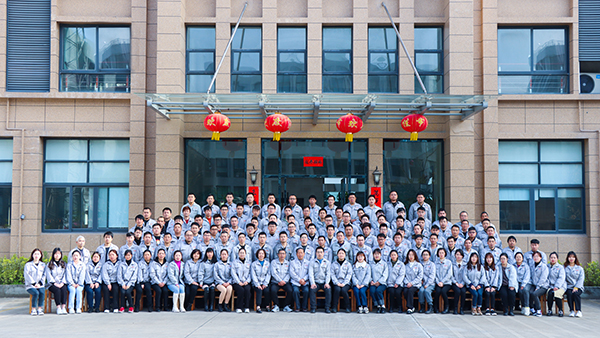