Introduction
As the market demand for plastic handles increases, plastic handle mould have become an indispensable tool for the manufacturing industry. This type of mold is specifically designed to make handles made of durable and easily machinable plastic materials that can be created in a variety of shapes, sizes and colors to give their products a unique and eye-catching appearance and are used by companies around the world to produce high-quality consumer goods.
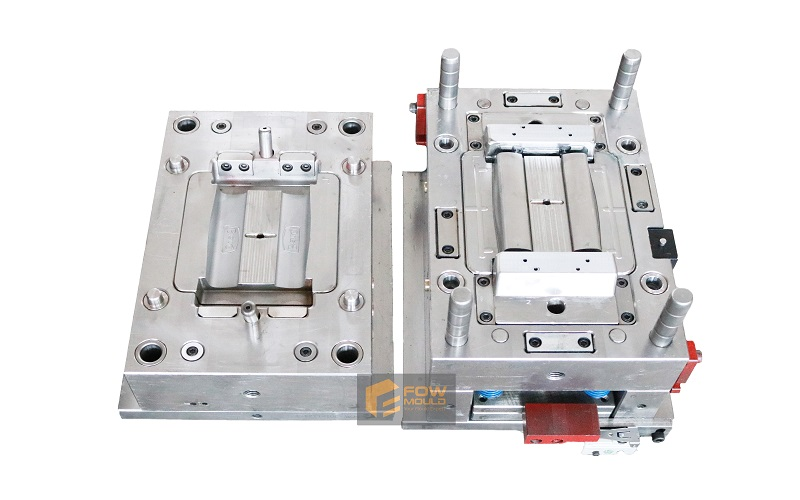
The key points of design a plastic handle mould
First and foremost, you need a clear understanding of the final product. This includes its size, shape, functionality, and any specific features it must have, such as an ergonomic grip or certain aesthetic details. This will influence the overall design of the mould.
Then, consider the precise design of the cavity and core to produce the desired handle shape. The cavity is the hollow space inside the mold that determines the shape and size of the handle. It is usually designed to be the exact opposite of the desired handle shape. And the core forms the inner surface of the handle. It is placed inside the mold cavity and the molten plastic flows around it and solidifies into the final handle shape.
In addition, The placement of gates and runners in a plastic handle mould is a crucial aspect of the mould design process. They direct the flow of the molten plastic into the mould cavity, affecting the quality of the finished handle, the moulding cycle time, and the overall efficiency of the moulding process. The gates should be positioned so that the plastic fills the mold cavity evenly and reduces runners and welds. And the runner system should be designed so that the plastic is evenly distributed in all parts of the mold.
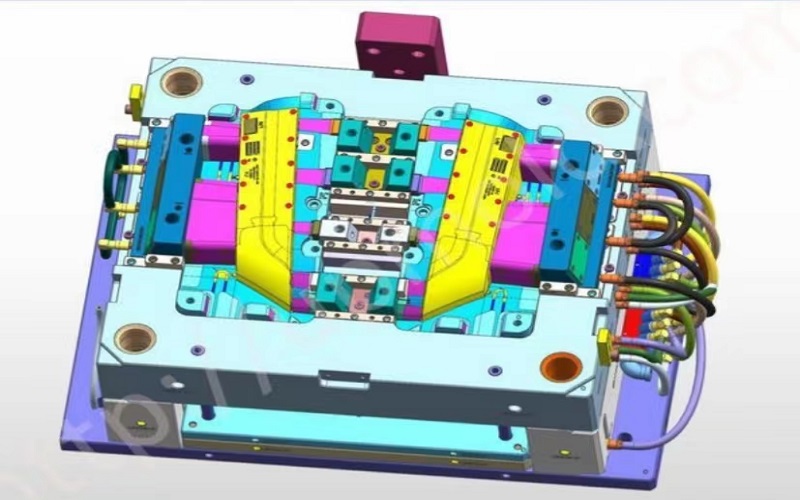
Cooling system of plastic handle mould
The purpose of the cooling system in a handle mold is to move heat away from the plastic part so that it solidifies quickly and evenly. A good cooling duct can give a mold a drying time of 4-6 seconds, which is a high requirement for the speed at which the mold can be manufactured. The cooling ducts should be as close to and evenly distributed over the mold surface as possible to ensure effective heat transfer to provide uniform cooling.
The flow rate of the coolant should be high enough to effectively remove heat but not so high that it leads to turbulent flow or pressure loss.
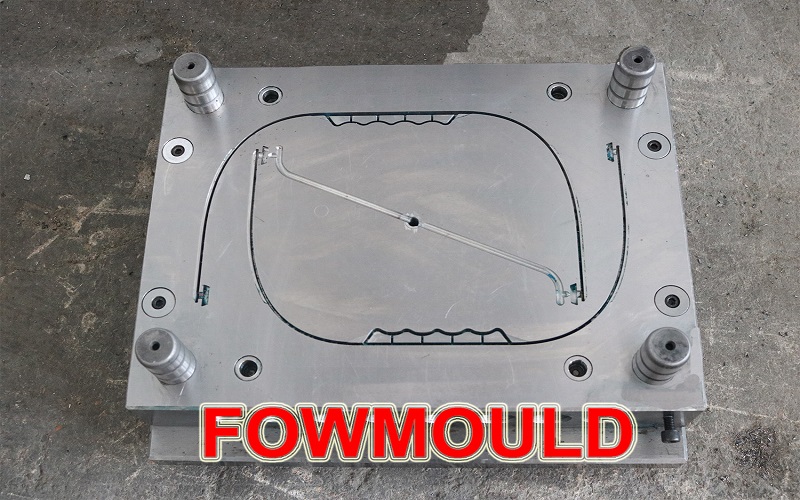
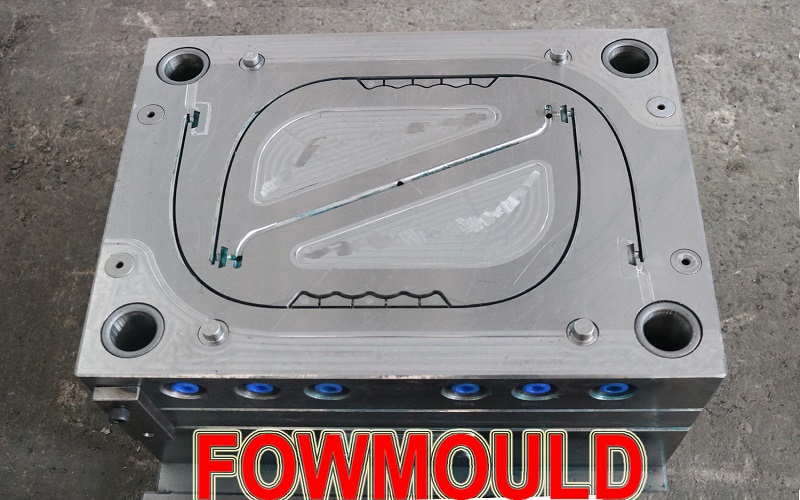
Plastic handle mould injection molding details
The injection moulding process for plastic handle molds is complex, and there are many factors to pay attention to. In order to get consistent, high-quality products, it’s important to control the following parameters precisely.
Depending on the material and the mold, the injection pressure can range from 500 to 5000 bar. After the initial injection, the holding or packing pressure is used to compensate for the shrinkage of the plastic as it cools. This is usually slightly lower than the injection pressure, about 50-60% of the initial pressure, depending on the material and part design.
The temperature of the mold can affect the cooling (and therefore cycle time) and the quality of the finished product. It can range from 20 degrees Celsius to 150 degrees Celsius, depending on the plastic material. Higher mold temperatures result in higher quality surface finishes, but increase cycle times.
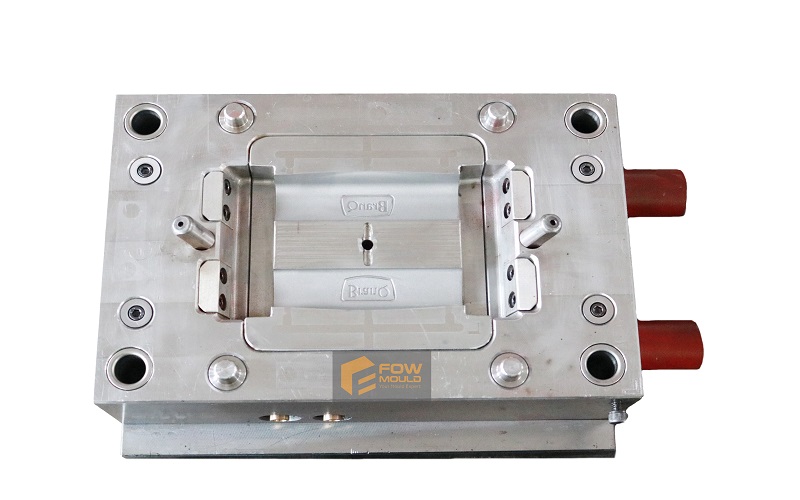
The Different Types of Plastic Handle Moulds
Plastic handle moulds can come in many shapes and sizes, depending on the specific application and design of the handle. Here are several different types of plastic handle moulds:
Single Cavity Mould
These moulds produce one handle at a time. They are simpler and cheaper to make than multi-cavity moulds, and they are often used for larger handles or for low-volume production.
Multi-Cavity Mould
These handle molds have multiple cavities, allowing for the production of multiple plastic handles in each molding cycle. They are more complex and expensive than single-cavity molds, but they can significantly improve production efficiency for large-scale manufacturing.
Hot Runner Mould
In a hot runner mold, the runners that transport the molten plastic from the injection point to the mold cavity are heated. This keeps the plastic in the runners molten and eliminates the need to remove and recycle runner material. Hot runner molds are more productive and produce less scrap than cold runner molds, but they are also more complex and expensive.
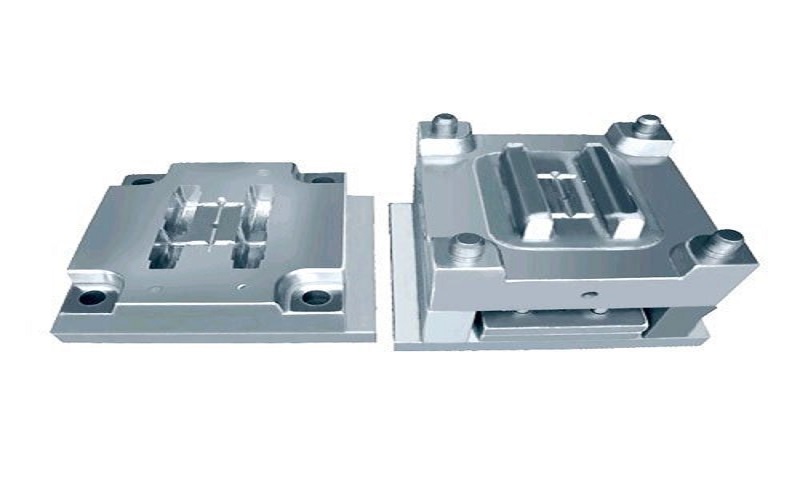
Application of plastic handle mould
As technology improves, the use of plastic handle molds permeates a wide range of industries, and these molds can be customized to the specific needs and specifications of the manufacturer to provide optimal performance and durability.
Kitchenware and Household Appliances:
Plastic handles are commonly used in kitchen appliances, cookware and small appliances such as kettles, mixers and toasters. Plastic handle molds are precisely designed to produce durable, heat-resistant plastic handles that are comfortable to hold.
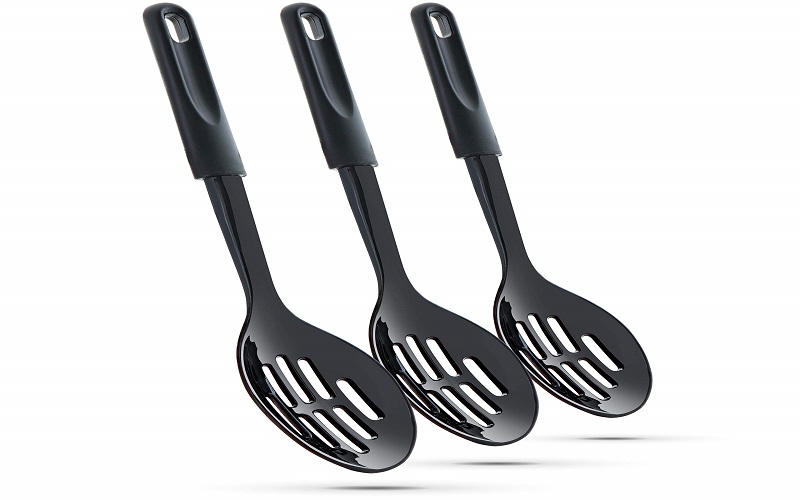
Electronics:
Many electronic devices and accessories, such as portable radios, vacuum cleaners and luggage, have plastic handles. These handles need to be strong and durable to support the weight of the device. With the help of handle molds, plastic handles can be created in different shapes and sizes to fit a variety of devices.
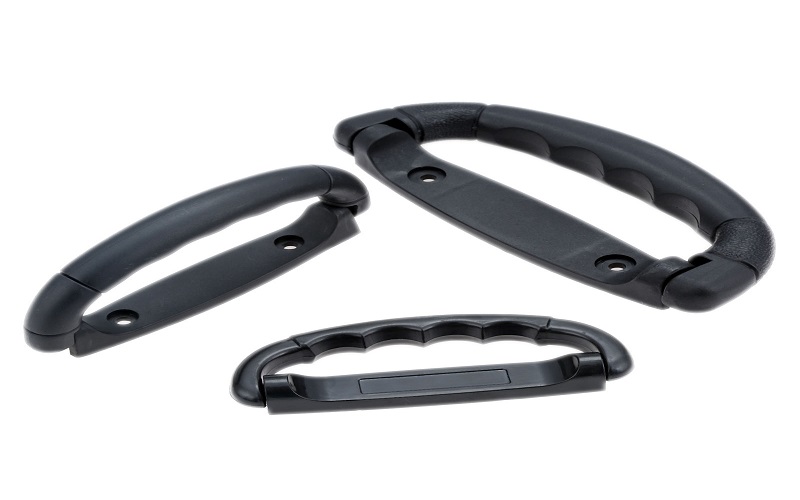
Automotive:
Inside automobiles, plastic handles are used for things like doors, glove boxes, and levers for adjusting seats or opening compartments. These small but critical components are precisely and carefully manufactured using “handle molds” to ensure that they are strong and functional enough to withstand daily wear and tear and maintain a smooth and comfortable ride.
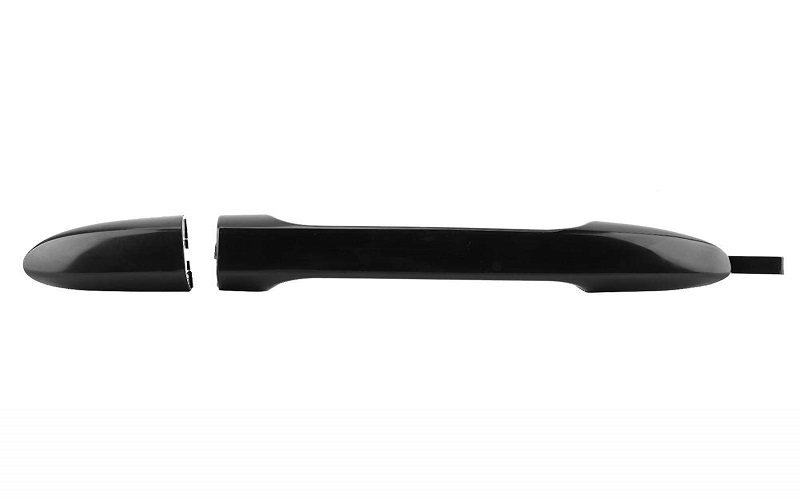
Furniture:
Many pieces of furniture, such as cabinets, drawers and doors, use plastic handles. These can be designed in a variety of styles and finishes to match furniture designs. The advantage of plastic handles is that they can be precisely molded into a variety of shapes and sizes using handle molds to match all furniture designs.
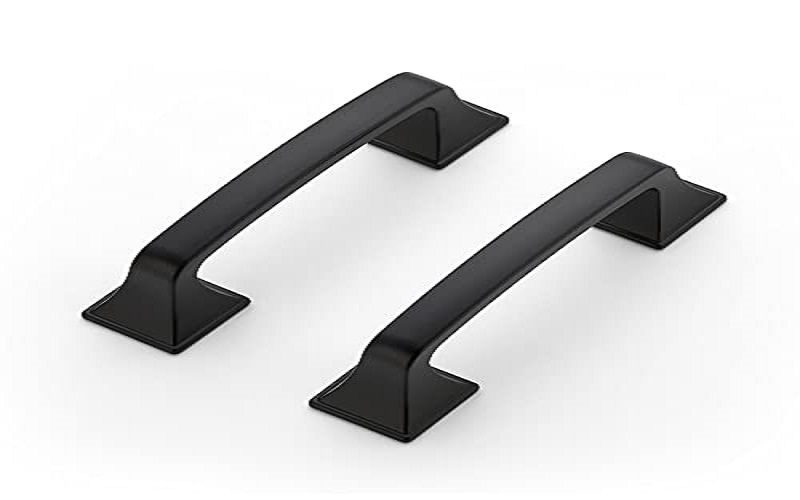
How to Choose Handle Mould Supplier in China
When looking for the right plastic handle mold supplier in China, there are several key factors to consider. First, consider the supplier’s experience and reputation in the industry. This can be done by researching the company’s online presence and customer reviews.
Second, make sure the supplier has a high level of expertise in producing plastic handle molds. This will ensure that the product you receive is of high quality and meets all your requirements. Finally, there is the promise of competitive pricing and timely delivery to ensure that the processing can be completed within the specified time frame.
FOWmould, as a leading injection molding company in China, has rich experience in manufacturing plastic handle molds, and the factory is equipped with professional machines and management team, ready to provide customized service for your handle molds.
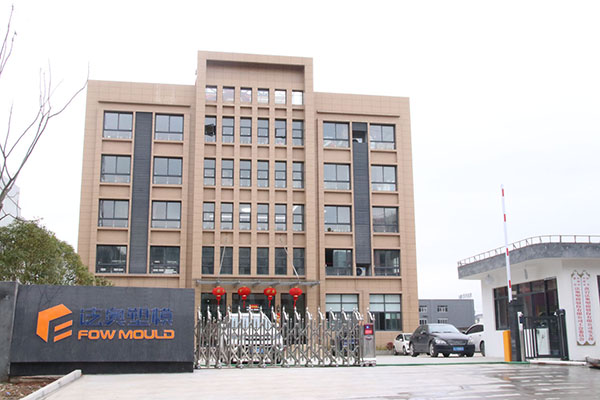
Conclusion
In conclusion, plastic handle mold is an indispensable molding tool for the manufacturing industry and the key to achieving mass production of high quality and durable products. By choosing the right plastic material, carefully designing the shape of the handle, considering the mold process to be used, and paying attention to temperature, the plastic handle molding process is ensured to be smooth and efficient.