What Is Short Shot Injection Molding?
Short shot injection molding is a common issue in the plastic injection molding process. It occurs when the molten plastic material does not completely fill the mold cavities during the injection process, resulting in a deficient product. This issue can lead to significant quality issues, as the incomplete parts are often unusable. The causes of short shot injection molding are numerous and can range from material viscosity to improper machine settings. Understanding these causes is the first step in preventing and troubleshooting short shot issues.
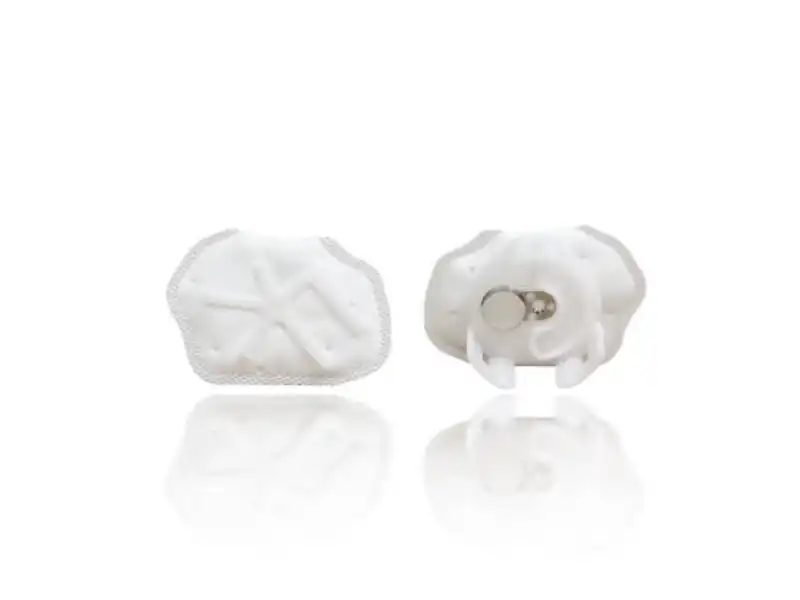
What Are the Common Signs of Short Shot Injection Molding?
The most obvious sign of short shot injection molding is the incomplete filling of the mold cavities. This can result in parts that are missing sections or have thin areas where the plastic material should have filled. These defects are often visually obvious and can be detected during the quality control process. Other signs may include an increase in the number of rejected parts, changes in the appearance or dimensions of the parts, or inconsistencies in the injection process. By identifying these signs early, manufacturers can take steps to address the root cause of the short shot and prevent further quality issues.
What Are the Key Reasons and Solutions of Short Shot Injection Molding?
There are several key reasons for short shot injection molding, each of which requires a different solution. By understanding these causes and their corresponding solutions, manufacturers can effectively prevent and troubleshoot short shot injection molding.
Reasons | Consequences | Solutions |
Material Viscosity | High viscosity can restrict flow of material. | Fine-tune materials’ melt temperature or select a material with lower viscosity suitable for the specific molding process. |
Improper Venting | Trapped air can inhibit proper filling of the mold. | Ensure mold design includes adequate vents for expulsion of air during the injection process. |
Material Variations | Inconsistencies in the properties of the material affect flow and filling. | Ensure consistent supply of material, properly stored and dried to maintain uniform properties. Regular quality checks are essential. |
Improper Machine Settings | Incorrect settings can lead to insufficient fill. | Regular calibration of the machine and training of operators to adjust settings for different molds and materials is necessary. |
Low Fill Volume | Not injecting enough material during the first stage of the process can cause short shots. | Set correct fill volume as per part’s design, and ensure machine’s feeding system’s functionality. |
Insufficient Pack and Hold Pressure | If pressure is too low, mold may not fill completely. | Adjust the pressure settings on the machine to ensure they are high enough to fully pack the mold. |
Low Melt Temperature | Low temperature can prevent proper flow of plastic. | Increase the melt temperature to improve material’s flow properties, but without degrading the plastic and affecting the part’s properties. |
Low Mold Temperature | Plastic can solidify prematurely if mold temperature is low. | Increase mold temperature to slow down cooling rate of plastic, but avoid overheating that can lead to degradation. |
Slow Injection Speed | Slow speed can lead to premature solidification of plastic. | Increase injection speed to ensure the mold is completely filled before plastic cools, taking care not to cause excessive pressure or stress on the machine. |
Inappropriate Mold Design | Complex geometries and poor venting can lead to short shots. | Redesign the mold to improve plastic flow, enhance venting, and simplify part geometry. Utilize simulation software for prediction. |
Inconsistent Production Cycle | Frequent machine stoppages and inconsistent cycles affect product quality. | Maintain a consistent production cycle with regular checks and adjustments for continuous operation of the machine. |
Foreign Material Contamination | Contamination can obstruct the flow of plastic. | Implement rigorous material handling and cleanliness procedures to avoid contamination. Regular checks of material and mold help identify and remove foreign materials. |
Material Viscosity
Material viscosity plays a vital role in short shot injection molding. Highly viscous materials can cause flow problems as it may not fill the mold cavities swiftly before the cooling phase sets in. If the raw material is very thick or viscous, it will need more force (pressure or heat) to fill the mold. Short shot defects can occur if the material’s viscosity isn’t taken into account during the process setup. The solution here lies in fine-tuning the material’s melt temperature or even choosing a material with lower viscosity, suitable for the specific molding process and part design.
Improper Venting
Improper venting poses a significant problem for successful injection molding. Without proper venting, air gets trapped in the mold cavities and impedes the plastic material flow. The result is a short shot, with voids or incomplete areas in the final part. To overcome this, you should ensure the mold design includes vents to allow air and other gases to escape from the mold cavities during the injection process—poor venting translates to poor quality products.
Material Variations
Material variations can significantly impact the injection molding process, leading to short shots. If the plastic material’s properties are inconsistent, it can affect the flow and filling of the mold. For instance, variations in the material’s moisture content, temperature, or composition can alter its behavior during the molding process. The solution is to ensure a consistent supply of material, properly dried and stored to maintain its properties. Regular checks and quality control measures can help identify and rectify any material inconsistencies.
Improper Machine Settings
Improper machine settings are a common cause of short shot injection molding. If the settings on the injection molding machine are incorrect, it can lead to incomplete filling of the mold. This includes incorrect injection pressure, speed, or temperature settings. Regular maintenance and calibration of the injection molding machine are crucial to ensure that it operates under the right conditions. It’s also important to train operators to understand the machine settings and adjust them appropriately for different materials and molds.
Low Fill Volume
Low fill volume is another factor that can lead to short shots. If there isn’t enough material injected during the first stage of the molding process, the mold may not fill completely. This can be due to an insufficient injection volume or a problem with the machine’s feed system. The solution is to ensure that the fill volume is set correctly according to the part’s size and complexity, and the machine’s feed system is functioning properly.
Insufficient Pack and Hold Pressure
Insufficient pack and hold pressure can also cause short shots. After the initial injection of plastic into the mold, additional pressure is applied to pack more material into the mold and compensate for shrinkage as the plastic cools. If the pack and hold pressure is too low, the mold may not fill completely, leading to a short shot. The solution is to adjust the pack and hold pressure settings on the injection molding machine to ensure that they are high enough to fully pack the mold.
Low Melt Temperature
Low melt temperature can prevent the plastic material from flowing properly, leading to short shots. If the melt temperature is too low, the plastic may not be fluid enough to fill the mold completely before it starts to solidify. The solution is to increase the melt temperature to improve the material’s flow properties. However, care must be taken not to set the temperature too high, as this can degrade the plastic and affect the part’s properties.
Low Mold Temperature
Similarly, if the mold temperature is too low, the plastic may start to solidify before it has fully filled the mold, leading to a short shot. The solution is to increase the mold temperature to slow down the cooling rate of the plastic, giving it more time to fill the mold. However, the mold temperature must be carefully controlled to prevent the plastic from overheating and degrading.
Slow Injection Speed
Slow injection speed can also lead to short shot injection molding. If the speed at which the molten plastic is injected into the mold is too slow, the material may begin to cool and solidify before the mold is completely filled. This can result in a short shot, where part of the mold cavity remains unfilled. To solve this issue, the injection speed should be increased to ensure that the mold is filled before the plastic has a chance to cool. However, the speed should not be so high that it causes excessive pressure or stress on the mold and machine.
Inappropriate Mold Design
Inappropriate mold design is another significant cause of short shot injection molding. If the mold design has flow restrictions, poor venting, or complex geometries that are hard to fill, it can lead to short shots. The solution to this problem often involves a redesign of the mold to improve the flow of plastic, enhance venting, and simplify the part geometry if possible. Using simulation software can help identify potential issues in the mold design before it’s manufactured.
Inconsistent Production Cycle
An inconsistent production cycle can also lead to short shot injection molding. If the machine is frequently stopped and started, or if the cycle times vary significantly, it can affect the consistency of the molded parts. This can lead to variations in the material’s temperature and flow properties, which can cause short shots. The solution is to maintain a consistent production cycle, with regular checks and adjustments to ensure that the machine is operating smoothly and consistently.
Foreign Material Contamination
Foreign material contamination is another cause of short shot injection molding. If foreign materials get into the plastic or the mold, they can block the flow of plastic and prevent the mold from filling completely. This can be caused by poor material handling practices or a lack of cleanliness in the molding area. The solution is to implement strict material handling and cleanliness procedures to prevent contamination. Regular checks of the material and the mold can also help identify and remove any foreign materials.
Conclusion
In conclusion, short shot injection molding is a common issue that can be caused by a variety of factors, from material properties and machine settings to mold design and production practices. By understanding these causes and their solutions, manufacturers can prevent short shots and ensure the production of high-quality plastic parts.
At FOWMould, we have a team of experienced professionals who can help you identify the root causes of your short shot problems and provide effective solutions. Contact us today to learn more about our services.