As a derivative of polymer injection molding, Powder Injection Molding (PIM) incorporates many of the same techniques, adding the intermittent sintered processes used in powder metallurgy and ceramic mouldings. Here are the four main stages:
In an era propelled by innovation, manufacturing techniques continuously evolve to meet the increasingly complex and diverse demands of various industries. Amidst these advancements, Powder Injection Molding (PIM) has carved a distinctive path for the production of precision components.
In this article, we will delve deep into how PIM skillfully navigates the nexus between materials and technology. Read on to explore its intricate dynamics.
What is Powder Injection Molding?
Powder Injection Molding (PIM) traces its origins totraditional metal and ceramic processing techniques and is an evolution of polymer injection molding.
By merging the strengths of powder metallurgy with plastic injection molding, PIM is frequently employed to produce components with complex geometric shapes, whether in metals (Metal Injection Molding) or ceramics ( Ceramic Injection Molding).
With its unique technological advantages, PIM continuously breaks through the constraints of component design and application.
It is the preferred method for manufacturing large volumes of intricate, functional parts, establishing its prominence in applications across diverse industries.
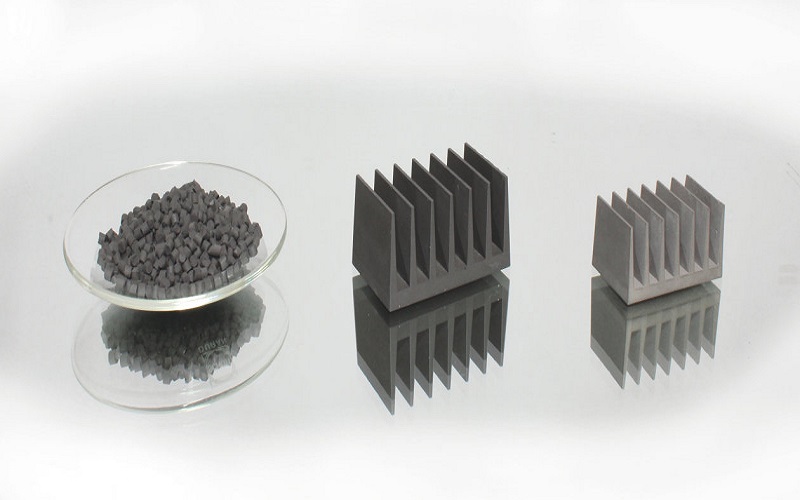
How Dose Powder Injection Molding Work?
As a derivative of polymer injection molding, Powder Injection Molding (PIM) incorporates many of the same techniques, adding the intermittent sintered processes used in powder metallurgy and ceramic mouldings. Here are the four main stages:
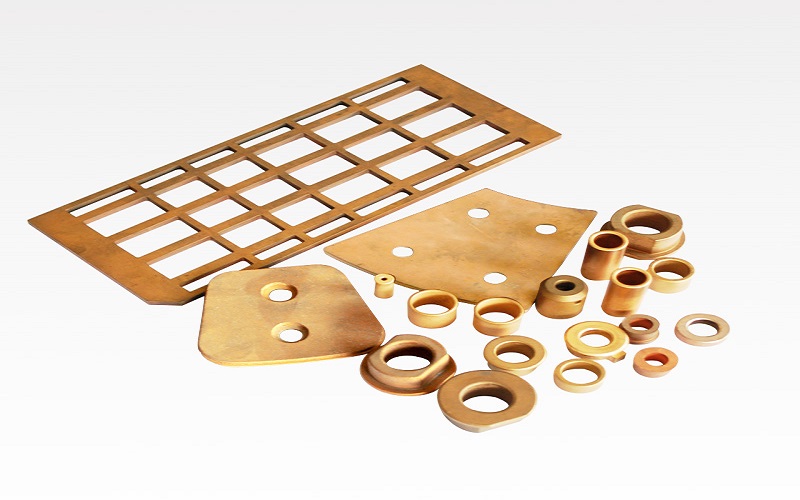
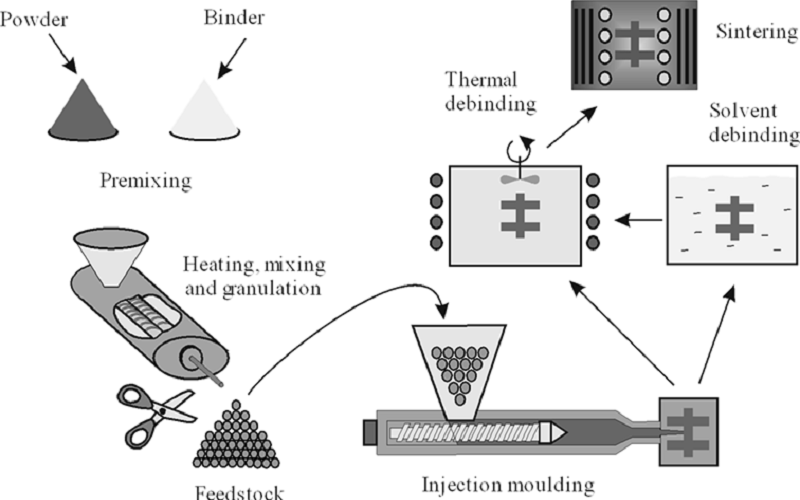
Feedstock preparation
This process starts with the creation of a mixture called “feedstock.” It typically consists of fine metal or ceramic powders combined with a thermoplastic binder. The result is a moldable plastic that retains the characteristics of the chosen metal or ceramic.
Injection Molding
The prepared mixture is poured into a helical feed barrel where it is heated and, under pressure, introduced into a mold cavity, taking on the desired final component shape. Once the feedstock cools and solidifies within the mold, it forms what is known as the “green part.”
Debinding
At this stage, the original thermoplastic binder needs to be removed from the green part. Debinding involves specific processes, which can include thermal treatments, solvent treatments, or a combination of both. The remaining component is a porous structure, termed the “brown part.”
Sintering
In the final stage, the brown part is heated under strictly controlled temperatures to just below the melting point of the metal or ceramic material. This causes the metal or ceramic particles to bond together, enhancing the part’s density and strength. The sintering process may result in a 15-20% shrinkage of the part to achieve its final dimensions.
Material Selection For Powder Injection Molding
Tracing its roots back to the history of powder injection molding, PIM is rooted in the proven technologies of powder metallurgy and ceramic processing, and has a strong inherent adaptability that ensures a wide range of material options for manufacturers and designers.
Since the process begins with a metal or ceramic in powder form, different powders can be blended to achieve specific properties such as strength, electrical conductivity, or corrosion resistance. And the binder used in the PIM process allows the powder to reach a fluidized liquid state during injection molding.
This means that many materials, even those that are not typically malleable or easy to shape, can be molded using PIM.
At the same time, these diverse material choices give a high degree of design flexibility, allowing powder injection molding to be tailored to the varying needs of various industries.
Typical Materials Used In Powder Injection Molding
Material Type | Examples | Typical Applications |
Metals | ||
Stainless Steels | 316L, 17-4 PH, 304L | Surgical instruments, automotive parts |
Tool Steels | M2, D2 | Cutting tools, wear-resistant components |
Low-alloy Steels | Fe-2%Ni, Fe-8%Ni | Structural parts, automotive components |
Soft Magnetic Alloys | Fe-Ni, Fe-Si | Electromagnetic shielding, inductors |
Titanium Alloys | Ti-6Al-4V | Aerospace components, medical implants |
Superalloys | Inconel 718, Inconel 625 | Aerospace and gas turbine components |
Tungsten Alloys | W-Ni-Fe, W-Ni-Cu | Radiation shielding, darts, counterweights |
Ceramics | ||
Alumina (Al₂O₃) | Electrical insulators, wear-resistant parts | |
Zirconia (ZrO₂) | Dental crowns, industrial knives | |
Silicon Nitride (Si₃N₄) | Engine components, cutting tools | |
Silicon Carbide (SiC) | Wear plates, seal rings |
Advantages of Powder Injection Molding
Powder Injection Molding combines the advantages of design flexibility, material versatility, and cost-effectiveness, making it an ideal choice for industries aiming to produce high-quality precision components.
Complex Geometries
In traditional manufacturing methods, producing parts with intricate shapes can often compromise the accuracy of the product. However, the Powder Injection Molding process allows for the creation of detailed components to exact specifications, offering an ideal solution.
Material Versatility
The powder injection process is highly accommodating to various materials, ranging from stainless steel to ceramic materials. This multifunctionality ensures that manufacturers can select the optimal material for a specific application, granting the final product its desired unique properties.
Cost-Effective Production
For large-scale manufacturing, PIM is typically more economical than other methods, especially when considering intricate components. The initial investment in molds can be offset by reduced costs from minimized material waste and the efficiency of mass-producing parts.
Sustainable Manufacturing
With growing attention to sustainability, PIM offers a more environmentally-friendly choice. Since PIM is a near-net-shape process, it usually generates less waste compared to machining methods. Additionally, any residual materials are typically recyclable.
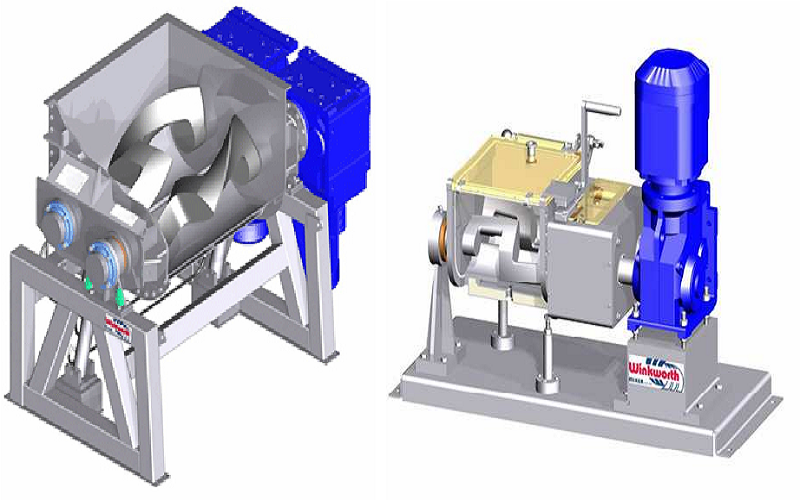
Applications of Powder Injection Molding
In modern manufacturing, powder injection molding technology, by producing lightweight and durable multifunctional products, offers unprecedented opportunities for the manufacturing sector. This technique provides excellent solutions for custom manufacturing across various industries.
Medical Instrument
With powder injection molding, we can produce orthodontic brackets and various medical tools with high precision, ensuring longevity and top-notch performance. For surgical instruments with intricate designs, this method proves particularly invaluable.
Automotive Sector
Given the complex driving environments cars operate in, automotive parts demand high strength and durability. Utilizing PIM technology, we’re able to produce complex components that meet these demands, such as engine components, transmission systems, and other structural parts.
Electronics Industry
With the rapid advancement of electronic technology and the trend toward miniaturization of devices, there’s an increasing demand for component precision and design complexity. PIM excels in producing these minute components, like various connectors, mobile device parts, etc., while also ensuring excellent conductivity.
Aerospace
Aerospace components often necessitate being lightweight yet robust. PIM precisely meets this criterion, effectively working with high-performance metals and ceramics to ensure parts conform to stringent aerospace standards. Additionally, detailed internal components of aircraft are often a product of this method.
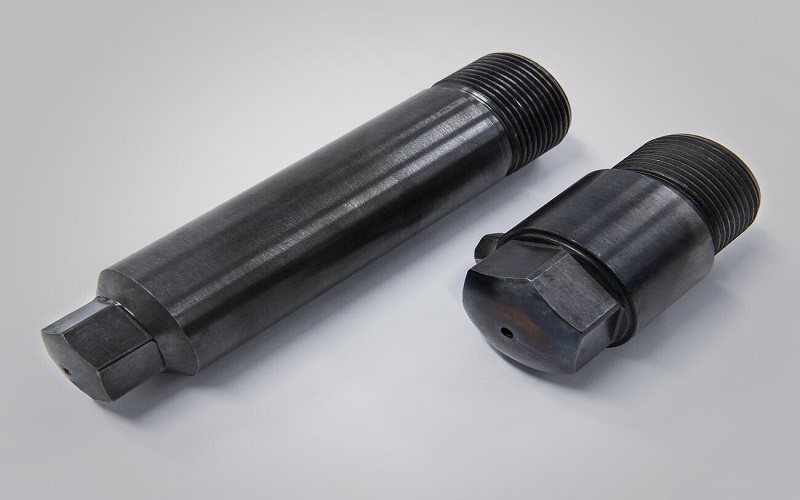
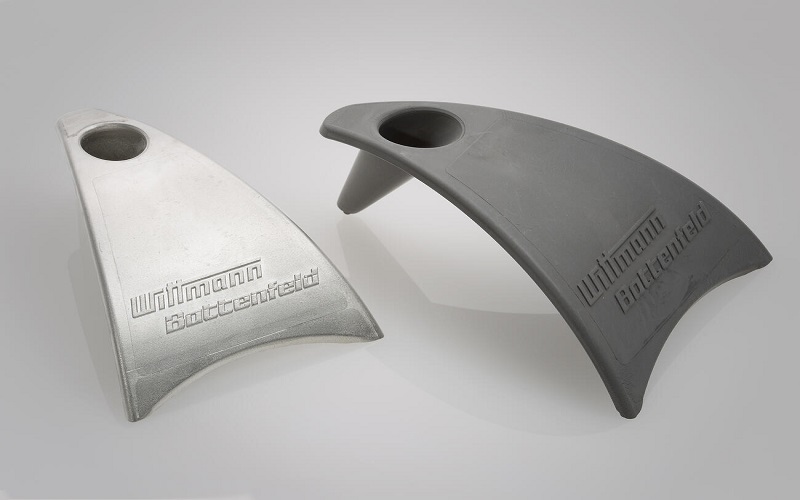
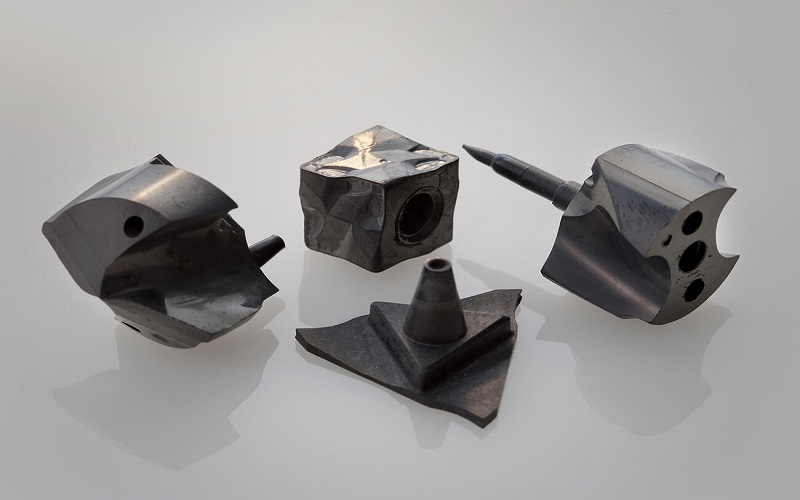
Comparison Between Powder Injection Molding And Metal Injection Molding
Powder Injection Molding (PIM) and Metal Injection Molding (MIM) are both advanced manufacturing techniques that integrate the principles of polymer injection molding with material processing.
Their shared advantage lies in their capability to efficiently produce intricate and high-precision components, making them particularly valued in industries that prioritize complex designs and scalable production levels.
However, there’s a pivotal distinction between the two. PIM merges the capabilities of polymer injection molding with either powder metallurgy or ceramics. It’s versatile in manufacturing both metal and ceramic components, catering to the diverse needs of various industries.
On the other hand, Metal Injection is a specific subset of PIM, primarily aimed at fabricating intricate metal parts. The components produced through MIM often resemble the properties of wrought metals. While PIM covers a broad range of material applications, MIM is a distinct segment within PIM’s vast domain, with its primary differentiation being its material focus.
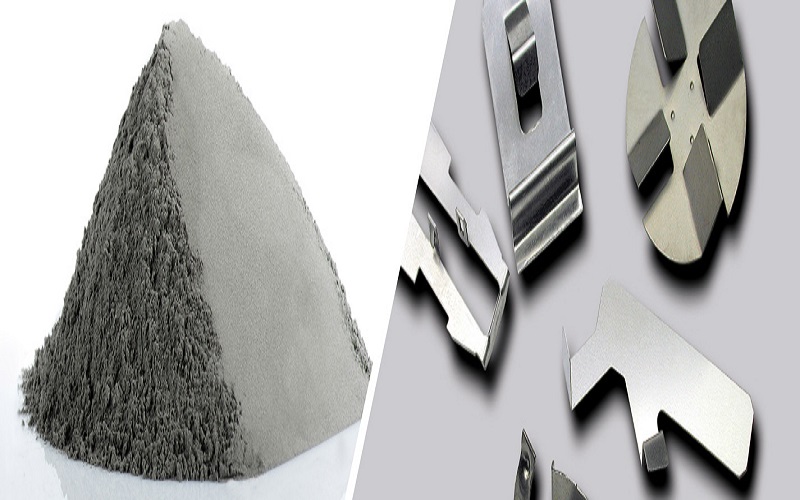
Why Choose FowMould As Powder Injection Molding Supplier in China?
Choosing FowMould as a powder injection molding service provider is a decision backed by our 40 years of rich experience and expertise in injection molding. We are adept at handling intricate designs and materials, ensuring the final products meet anticipated standards.
Moreover, FowMould boasts advanced machinery and has established confidentiality agreement procedures, offering not only high-quality products but also sincere and dedicated customer service.
Ultimately, a company’s reputation stands as a testament to its reliability and quality of service. Based on past reviews, testimonials, and case studies, FowMould has garnered widespread acclaim, forging strong collaborations with our clients.
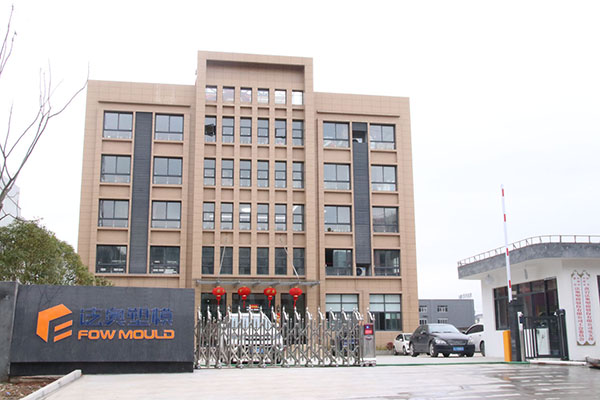
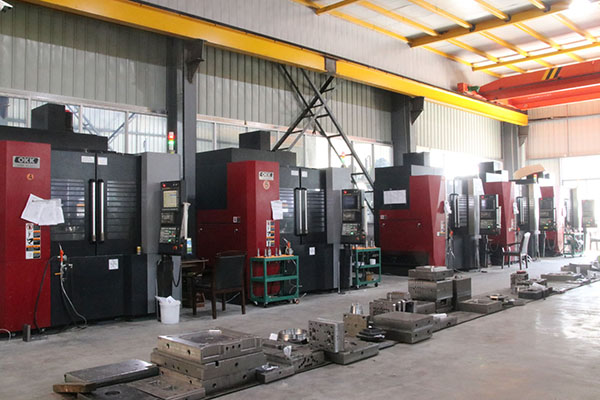
Conclusion
In summary, Powder Injection Molding stands as a cutting-edge manufacturing technique, brilliantly merging the advantages of injection molding with the unique characteristics of powdered materials across diverse fields.
As the tides of innovation continue to rise, PIM is set to ride the wave, positioning itself at the forefront of manufacturing advancements.